Поговорим о системе технического обслуживания и ремонта (ТОиР) станков с ЧПУ на нашем предприятии.
В связи с повышением эффективности работы оборудования с ЧПУ, его техническое обслуживание за последнее время резко изменилось. Возникла необходимость в выборе такой стратегии и схемы управления ТОиР оборудования с ЧПУ, которая давала повышение эффективности работы оборудования за счет повышения эффективности работы ремонтной службы. В области управления ТОиР – стратегия означает комбинацию организационных и технических решений к определению сроков, объемов проведения работ по ТОиР на оборудовании, сроков его замены и позволяет оптимизировать использование ограниченных ресурсов и добиться снижение простоев станков за счет более фокусированного их использования.
Сегодня для предприятий отрасли важнее всего техническое перевооружение производства, а также совершенствование организационной структуры предприятия, а организация управления службами ТОиР на многих предприятиях остается без изменения. Поэтому необходима новая самостоятельная структура управления службы ТОиР оборудования с ЧПУ. Мы на предприятии ее изменили 17 лет назад, что позволило резко поднять эффективность ТОиР. В настоящее время структура управления ТОиР предприятия выглядит следующим образом.
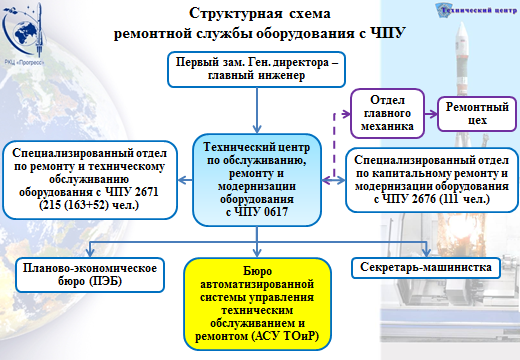
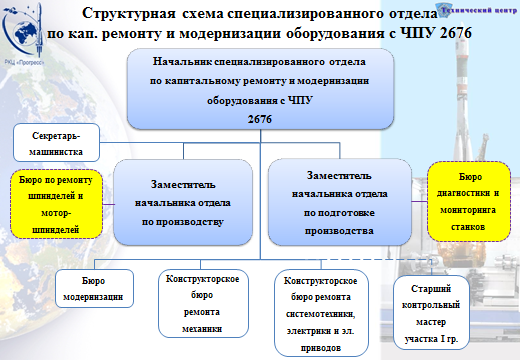
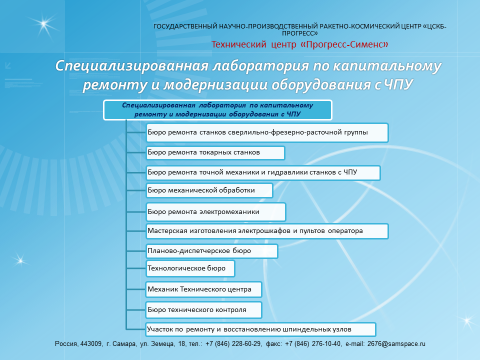
Как видно из схемы, мы стали самостоятельной службой ТОиР станков с ЧПУ, подчиненной главному инженеру.
Возрастающая актуальность повышения эффективности управление процессами ТОиР оборудования с ЧПУ поставила перед Техническим центром задачу – совершенствовать её за счёт создания АСУ ТОиР, интегрированную в АСУ-Ремонт, от решения которой напрямую зависит стабильность и эффективность работы станков с ЧПУ.
АСУ ТОиР предназначена для организации управления процессами ТОиР и создания информационной системы управления ТОиР станков с ЧПУ на предприятии.
Применение информационных систем АСУ ТОиР позволит получить принципиально новое качество управления процессами ТОиР по техническому состоянию станков с ЧПУ.
Получаемое новое качество состоит не только в безбумажных технологиях, повышении прозрачности процесса проведения ТОиР, точности, качества и сокращении времени на планирование и учёт выполненных работ, но появляются ранее отсутствующие возможности по анализу и прогнозированию результатов ТоиР технического состояния станков.
Система АСУ «ТОиР», которая в настоящее время разрабатывается и внедряется на предприятии
В структурной схеме управления техническим центром мы организовали бюро АСУ ТОиР, на которое возложили задачи проектирования и внедрения автоматической системы управления ТОиР.
Для эффективного использования станков с ЧПУ необходимо внедрить АСУ ТОиР с элементами диагностики, мониторинга и планирования ТОиР технического состояния предиктивной аналитики и планирования работ по ТОиР, что позволит устранить организационные потери, планировать ТОиР по фактическому состоянию узлов без разборки станка, предварительно заказывать комплектующие. Наибольший эффект от АСУ ТОиР получается при автоматизированном мониторинге, так как только АСУ ТОиР в современных условиях способна повысить эффективность работы ремонтной службы предприятия, за счет оперативной подачи информации о техническом состоянии станка,о загруженности ремонтников, о наличии запасных частей и технической документации и многое другое. С помощью АСУ ТОиР большой поток внеплановых отказов можно свести к минимуму, предупреждая критические ситуации. Эта система позволит ремонтной службе быстро анализировать и прогнозировать работу оборудования, обосновывать необходимые затраты, производить расчет численности работников для выполнения ТОиР, обеспечить достижение целей предприятия в области повышения эффективности работы. Для крупных машиностроительных предприятий, эксплуатирующих большое количество оборудования с ЧПУ, очень важно добиться управляемости и видимости процессов эксплуатации ТОиР. Решение этих задач заключается в разработке и внедрении единой информационной (интеллектуальной) АСУ ТОиР.
Необходимость разработки и внедрения интеллектуальной АСУ ТОиР диктует время. Кроме информационных модулей должны быть и работать модули мониторинга, диагностики, фактического состояния станка и модуль адаптивного управления узлами станка. Для реализации данного проекта на предприятии было создано бюро АСУ ТОиР, на которое возложена задача по разработке и внедрению поэтапно разрабатываемых модулей.
Разработку и внедрение АСУ ТОиР станков с ЧПУ проводила специально созданная рабочая группа. Ход работы ежемесячно обсуждали на технических совещаниях центра.
Автоматизация системы АСУ ТОиР ведется не для того, чтобы работать меньше, а для того, чтобы работать эффективнее.
Основная функция производственного процесса ремонта – обеспечение ресурса времени работоспособности узлов станка, а не станка как отдельной единицы. Базой АСУ ТОиР должна быть диагностика технического состояния узлов станка, и только на этой базе должны работать информационные модули планирования, снабжения, кадры и т. д. Сущность стратегии ТОиР по техническому состоянию с прогнозированием надежности заключается в том, что контроль технического состояния станка выполняется либо постоянно, либо с периодичностью, а момент начала ремонта планируется по техническому состоянию станка и наличия запасных частей.У себя на предприятии мы применяем смешанную стратегию ТОиР, т.е. эксплуатация до отказа, ремонт согласно ППр по фактическому состоянию оборудования- он является основным.
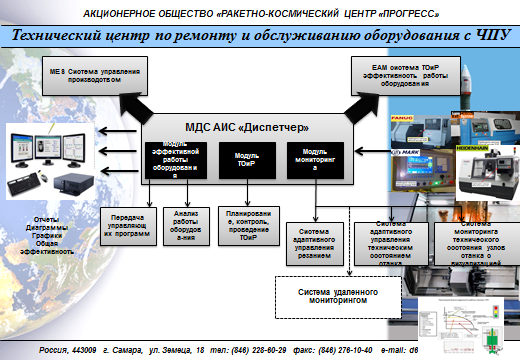
В настоящее время на предприятии внедряется система ТОиР по фактическому техническому состоянию оборудования, которая основана на том, что отказы станков возникают не из-за срока его эксплуатации, а из-за определенных дефектов, большинство из которых имеют свои характерные параметры. Контроль над изменением этих характерных параметров позволяет прогнозировать техническую неисправность и правильно планировать работы по техническому обслуживанию и ремонту.
Для реализации вышеуказанной задачи было создано бюро диагностики и мониторинга. Основной целью внедрения системы диагностики и мониторинга технического состояния узлов оборудовании, как неотъемлемой части АСУ ТОиР, является предотвращение внезапных отказов, снижение простоев станков с ЧПУ по техническим неисправностям, сокращение времени выполнения плановых работ по ТО и повышение качества ремонтных работ.
Один из самых распространенных методов безразборной диагностики, применяемый в АО «РКЦ Прогресс» на практике, - это метод вибродиагностики. Практически любая неисправность в станке выдает себя повышенной вибрацией. Метод вибродиагностики позволяет улавливать момент начала проблем с техническим состоянием узла, а не ориентироваться на календарь планово-предупредительных ремонтов, сопровождаемый разборкой станка независимо от реальной степени состояния деталей и узлов. Мы сумели на основе метода вибродиагностики создать и внедрить на предприятии современную и эффективную автоматизированную систему ТОиР по фактическому техническому состоянию оборудования.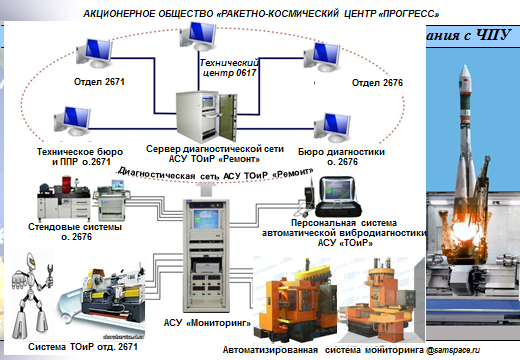
Начальник отделения отраслевой диагностики технологического оборудования НПО “Техномаш” назвал АО «РКЦ Прогресс» единственным предприятием ракетно- космической отрасли, на котором в таком масштабе на системной основе реализована идея комплексной диагностики и особенно вибродиагностики станочного парка с ЧПУ. Судя по тому, что предприятием было проведено более двадцати научно-практических тематических конференций по проблемам ТОиР оборудования, опыт предприятия и актуален, и востребован. Проблемы, о которых говорили на конференциях, - это проблемы не отдельно взятого предприятия или отдельно взятой отрасли, а системные, для всего машиностроительного комплекса. По моему мнению, внедрение системы комплексной диагностики, и особенно мониторинга по предупреждению дефектов, гарантировано дает большой экономический эффект. Да, в это сначала нужно вложиться, но через три года она даст отдачу и прибыль.
В зоне ответственности технического центра АО «РКЦ Прогресс» более 500 единиц оборудования с ЧПУ. Все оборудование разбито на 3 группы по критерию приоритетности. В 1-ю входит особо ответственное оборудование – все обрабатывающие центры, работающие в три смены и выполняющие почти половину заводской программы, и уникальное оборудование производства Mecof, WFL, Forest и др, которое просто нечем заменить, если оно остановится. Оборудование 1-ой группы (около 150 единиц) оснащается стационарными системами диагностики для непрерывного мониторинга. Во 2-ю группу – около 150 единиц – входят новые станки с ЧПУ и ответственное оборудование, которое не попало в 1-ю группу. Их с помощью переносных приборов по графику диагностируют специалисты группы диагностики централизованного бюро диагностики и мониторинга. Для остальных станков – 3-я группа приоритетности – реализована двухуровневая структура вибродиагностики. На первом уровне специалисты периодически измеряют параметры вибрации простейшими приборами – виброметрами. Если общий уровень виброскорости повышенный, то станок подвергается диагностике силами специалистов централизованного бюро. По результатам диагностики станков всех трех групп приоритетности выдается протокол с заключением о техническом состоянии узлов и деталей станка и рекомендациями для планирования работ. При выполнении комплексной диагностики мы используем следующие приборы:
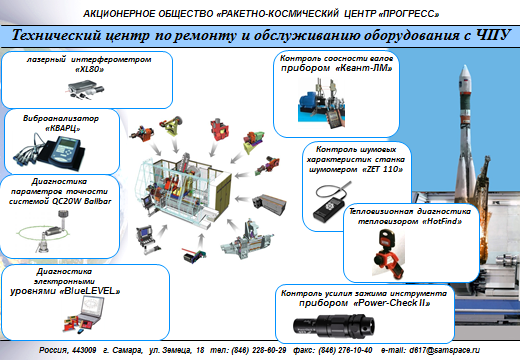
Параллельно с проведением комплексной диагностики работниками бюро диагностики и мониторинга отдела 2676 внедряется система автоматизированного мониторинга технического состояния с использованием средств измерений диагностических параметров, стационарно установленных на станке с ЧПУ. Предпосылкой к автоматизации процесса диагностики технического состояния станочного оборудования служит тот фактор, что при проведении плановой периодической диагностики переносными диагностическими приборами появляется риск внезапного отказа в период между плановыми проверками по причине внешних факторов (например, столкновение вследствие ошибки оператора). Внедряемая система позволяет не только выявлять дефекты узлов и деталей станка, но и предотвращать выход из строя дорогостоящих узлов путем отключения станка при столкновениях, а так же контролировать технологический процесс обработки.
Комплекс мероприятий по внедрению системы автоматизированного мониторинга включает в себя:
- монтаж аппаратной части системы;
- настройку программного обеспечения для сбора, обработки и удаленной передачи измеряемых значений диагностических параметров для объектов диагностики;
- разработку и настройку системы визуализации технического состояния объектов диагностики.
Система автоматизированного мониторинга на сегодняшний день уже установлена и успешно функционируют на 150 станках MECOF Mecmill Plus-HPC3Ю, FOREST V4-2500R2P2. Постоянно ведутся работы по внедрению системы автоматизированного мониторинга технического состояния на новых особо ответственных станках таких моделей как DMG DMC60T, Hurco VMX42t, WFL M40-G, ИР500ПМФ. Система мониторинга технического состояния внедряется на базе диагностического модуля VSE100, интегрированного в систему ЧПУ и АСУ. Мониторинг и «АИС «Диспетчер» работает параллельно с системой эффективности работы оборудования.
Пятнадцать лет назад был образован участок ремонта шпиндельных узлов. Шпиндельный узел металлообрабатывающего станка является важнейшей его подсистемой. Доля технического состояния шпиндельного узла в балансе точности обрабатываемых на станке деталей может достигать 60%. Предпосылкой к организации собственного участка ремонта шпиндельных узлов послужил тот факт, что стоимость ремонта шпиндельного узла современного металлообрабатывающего станка с привлечением подрядных организаций может доходить до 80% от стоимости нового шпиндельного узла.
На первоначальном этапе создания участка ремонта шпиндельных узлов полностью отсутствовало его оснащение специализированным инструментом и оборудованием. Была проведена большая работа по оснащению участка и технологической подготовке процесса ремонта шпиндельного узла. Были приобретены стенд входного контроля подшипников СП-180М, балансировочный станок ВМ-300 и другое специализированное оборудование и инструмент. Завершается работа по изготовлению стенда для обкатки, испытаний и диагностики шпиндельных узлов до и после ремонта.
На сегодняшний день работниками участка ремонта шпиндельных узлов освоена технология проведения, как приводных шпиндельных узлов, так и высокоскоростных мотор-шпинделей станков таких ответственных моделей как Chiron FZ15, Hurco VMX42t, Micron HPM1150U, WFL M40-G и пр.
Из-за отсутствия необходимой документации, которую производители станков не предоставляют, идет постоянная конструкторско-технологическая подготовка ремонта шпиндельных узлов.
В настоящее время увеличивается разрыв между уровнями оснащенности основного производства и ремонтного производства .
Отсюда и возникают проблемы в области ТОиР станков с ЧПУ. Их решение – это головная боль руководителей служб ТОиР на предприятиях. Вторая проблема – старение основных фондов. До 80% общего количества станков с ЧПУ старше 20 лет. При этом темпы обновления станочного парка низкие, а несвоевременная замена старой техники новой заставляет продлевать сроки эксплуатации неэффективных станков, что влечет за собой повышение затрат на ТОиР, а в конечном счете тормозит модернизацию предприятий.
Капитальный ремонт
Капитальный ремонт металлообрабатывающих станков с ЧПУ все больше характеризуется глубокой модернизацией в сочетании с добавлением новых конструктивных элементов. Наша цель – приспособить устаревшие станки для работы с современными технологиями и инструментами.
Предприятие заинтересовано в том, чтобы путём небольших инвестиций провести приобрести почти новый станок за счёт проведения работ по кап. ремонту с глубокой модернизацией.
Ведь приобретение новых станков, особенно крупногабаритных, требует довольно больших затрат. А в условиях, когда подобные станки не всегда имеют постоянную загрузку (2А20Ф2) соответственно, и вложения в приобретение новых станков не будет оправданным. Такое оборудование выгоднее капитально отремонтировать с проведением гл. модернизацией, немаловажен и тот факт, что эта процедура занимает от 6 до 9 месяцев.
Для реновации часто выбираем станок, который эксплуатируется на предприятии более 20-25лет. В процессе эксплуатации на станке сняты остаточные напряжения и станок приобрёл оптимальную структуру и виброустойчивость. В дальнейшем это становится залогом высокой точности обработки на капитально отремонтированном модернизированном станке. Очень важно правильно выбрать метод усовершенствования станка, этим занимаются конструктора.
Капитальный ремонт с глубокой модернизацией станков с ЧПУ позволяет усовершенствовать устаревшее оборудование, сделать его современным и годным для выпуска высокоточных сложных деталей.
Технический центр выполняет все виды ТОиР станков с ЧПУ, любых производителей.
Специалисты ТЦ накопили богатый опыт по ТОиР станков с ЧПУ и произвели капитальный ремонт с глубокой модернизацией на более чем 180 станках.
Наши специалисты способны найти и устранить даже самые сложные неисправности, возникшие в процессе эксплуатации (ремонт шпинделей исправление программ в РLC.)
Что мы получаем после капитального ремонта с глубокой модернизацией станков с ЧПУ:
- полное восстановление работоспособности оборудования в соответствии паспортным характеристикам современного оборудования;- повышение точности обработки;
- повышение производительности;
- сокращение затрат на ТОиР (в 2-3раза);
- повышение удобства для эксплуатации и ТОиР;
- новые возможности в обслуживании диагностике станка (установка систем мониторинга, измерительной системы, систем);
- компенсация погрешности механики;
- увеличение объёма памяти для управляющих и сервисных программ;
- возможность передачи управляющих программ через флешку или локальную сеть;
- возможность обработки более сложных деталей.
Исходя из вышеизложенного, мы видим, что на предприятии большое внимание уделяется работам по капитальному ремонту с глубокой модернизацией станков с ЧПУ. Так, начиная с 2007 г., данные работы были проведены на более чем 180 станках моделей 16К20,16К30, 16Б16Т,1И611, РТ755, СТП220 , СТП320, EEN320, SPR, DF2, DST2, MD5S ,MS3-200, 1516, 1E516 ,6Р13, ГФ2171, ФП17, ФП27,СФП1, СФП13, МА655,СФП500, С500, FKrSRS500? 24К40, 2455, 2А620, 2А622, ИР200, ИР320, ИР500, ИР800, ИС800, ИР2637, V4-2500R2T2P, 40-15S4030/6m, КИМ Оптон. В настоящее время ежегодный объем составляет 18-20 станков. Среди наиболее впечатляющих проектов по капитальному ремонту с глубокой модернизацией станки с ЧПУ модели СФП -13, V4-2500R2T2P, СТП-320ПР.
V4-2500R2T2P
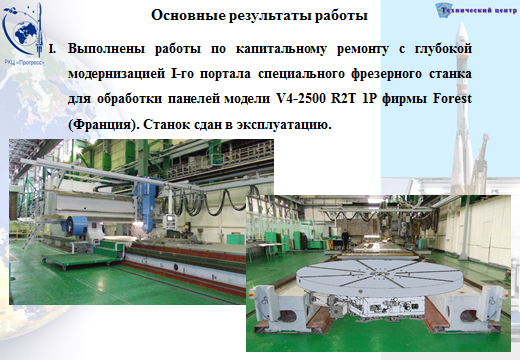
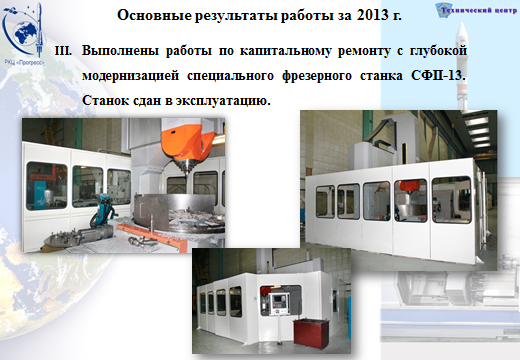
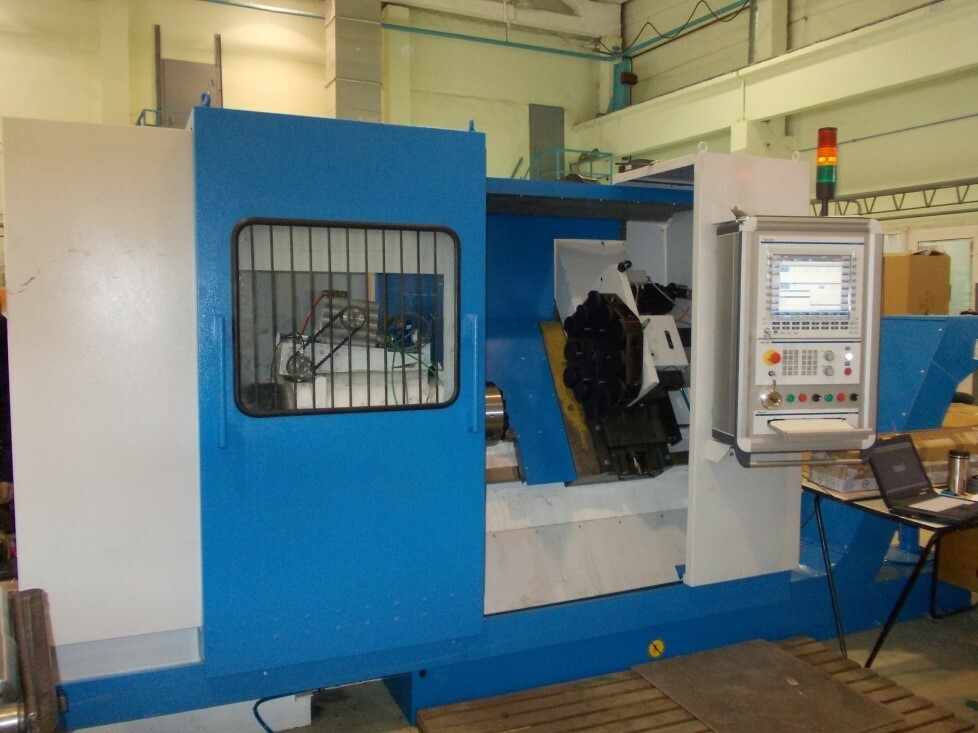
Такие работы крайне необходимы, потому что, делая капитальный ремонт с глубокой модернизацией, мы спасаем производство. Но выполнять такие работы нужно только на базе предприятий, имеющих опыт, оборудование и кадры.
Капитальный ремонт с глубокой модернизацией оборудования в подразделениях АО ”РКЦ «Прогресс», которую проводит Технический центр , даёт новую жизнь станкам. С современной системой числового программного управления и исполнительными механизмами они ещё долгие годы будут служить предприятию и приносить пользу. Вот отзывы о самых крупных выполненных проектах по модернизации и капитальному ремонту ТЦ , выполненных в 2014-2015 годах.
Начальник цеха о универсальном фрезерном станке СФП-13:
«Я выражаю огромную благодарность Техническому центру за то, что он вовремя откликнулся на нашу просьбу и взялся за капитальный ремонт с глубокой модернизацией универсального фрезерного станка СФП-13. Это оборудование морально и физически устарело. В сжатые сроки ТЦ нашёл соисполнителей, которые изготовили для станка новую траверсу с шпиндельной бабкой, была увеличена рабочая, и станок заработал, как современный. Мы решили задачу – увеличения габаритов обрабатываемых деталей, повышения качества обработки, повышения производительности работы оборудования в 3 раза.
На модернизированном фрезерном станке СФП-13 теперь можно обработать в режиме ЧПУ сложные крупногабаритные детали с точностью до 5 микрон. Повысилось качество изготовления шпангоутов больших диаметров. Техническое восстановление данного оборудования позволило равномерно распределить нагрузку и более качественно проводить обработку деталей крупных габаритов по шести координатам.»
Заместитель начальника производства о горизонтально-расточном станке«Skoda W200»:
«На протяжении тридцати лет станок безукоризненно выполнял механообработку корпусных частей РН и КА, но в последние годы в связи с физическим износом узлов и элементной базы он стал работать ненадёжно. Решение провести капитальный ремонт электрооборудования станка с заменой электроавтоматики, электродвигателей и приводов подач было принято ещё шесть лет назад, но в связи с тем, что на данный станок возложена большая нагрузка и производство в нём нуждалось постоянно, было трудно вывести его производства в июле 2015 года. Технический центр приступил к работам по капитальному ремонту с глубокой модернизацией (замена системы управления всей электроавтоматики эл. двигателей и кабелей на продукцию фирмы «Siemens»). Специалистами выполнен капитальный ремонт шпиндельной бабки с установкой системы диагностики его работы. Надёжность станка и качество изготовления деталей после проведения ремонта повысилось в несколько раз, чего мы и ожидали».
Практика проведение капитальных ремонтов с глубокой модернизацией крупных, сложных станков в РКЦ показывает, что наиболее эффективных результатов можно достичь только тогда, когда эти работы выполняются совместно с фирмой-изготовителем это станка.»
Начальник цеха
«Специалисты Технического центра ранее запустили в эксплуатацию первый портал станка модели V4-2500R2T2P, производства фирмы Форест ,который сейчас успешно работает. При проведении работ по капитальному ремонту с глубокой модернизацией второго портала станка модели V4-2500R2T2P было увеличено рабочее пространство за счёт установки двух проставок. В том числе, установлен новый современный мотор шпиндель, выполнены электромонтажные работы в электро шкафу станка, установлена новая система с ЧПУ.
Станок оснастили:
системой измерения детали фирмы «Renishaw», которая обеспечивает высокую точность базирования деталей с минимальной затратой времени на их установку.
системой вибродиагностики и против столкновения на базе контроллера, IFM установленной стационарно в электро шкафу станка, которая предотвращает столкновение режущего инструмента и самого корпуса шпинделя с обрабатываемой деталью и контролирует техническое состояние мотор шпинделя
магазином инструментов.
Станок стал более универсальным за счёт установки дополнительных расточных головок и современного универсального инструмента. На первом портале будут изготавливаться серийные детали, а на втором портале будет изготавливается высокоточная продукция для изделия в интересах национальной безопасности. Проведённый капитальный ремонт с глубокой модернизацией второго портала станка модели V4-2500R2T2P нам понравился и в перспективе мы планируем обратится к специалистам ТЦ с просьбой провести капитальный ремонт всего станка.»
Кадры
Как и все предприятия России, самарское предприятие ощущает нехватку кадров, особенно для ремонтного производства. Ремонту и модернизации оборудования нигде не учат, тем не менее, вопрос с кадрами решается. Конечно, не так быстро, как хотелось бы, и не на системной основе.
А вообще, кадры должны приходить на то место, которое им нравится. Не квадратный метр пола на престижном предприятии, а сама работа, ее конечный результат. Если человек приходит с желанием работать и учиться, то через 5-7 лет из него получится хороший специалист. Сейчас пошел поток выпускников вузов. Если раньше они шли в супермаркеты, автосервисы и прочее, то сейчас уже на заводы стоит очередь. Но, у приходящих «специалистов» ужасающе низкая подготовка. Еще хуже то, что и преподаватели почти такой же квалификации. Старые преподаватели не продвигались вперед и не развивались, поскольку были заняты выживанием, и сегодня читают свой курс в том виде, в каком он существовал 20-30 лет назад.
Что не может система образования, то делает само предприятие и его поставщики. Кроме наставничества, действует отдел обучения с привлечением специалистов, обладающих большим опытом и знаниями передовых методов ремонта. Работе с системами ЧПУ обучают компании SIEMENS и «Балт-Систем», в договоры с производителями станков также вписывается пункт об обучении специалистов.
Руководителям отрасли необходимо обратить внимание на состояние станочного парка. Требуется рассмотреть возможность создания отраслевого или регионального центра компетенции по внедрению на производстве современной технологии ТОиР станков с ЧПУ. Чтобы центр был эффективным, его нужно создать на предприятии с наиболее развитой системой ТОиР по всем направлениям, например, на «РКЦ Прогресс». Он будет заниматься внедрением эффективный, апробированных, системных решений, всесторонней поддержкой предприятий отрасли при решении разнообразных технических задач ТОиР и реализацией методов безразборной диагностики. Мы не делаем секрета из наработанного нами за долгие годы опыта. Тем не менее, каждый должен идти по своему направлению. Его нужно выбрать самостоятельно, и никогда один в один не копировать чужое!