В сегодняшней статье я поделюсь опытом работы бюро диагностики и мониторинга Технического центра ТОиР оборудования с ЧПУ в области обеспечения геометрической точности станков с ЧПУ с помощью современных инновационных технологий и инструмента, применяемых при выполнении работ по проверке оборудования на геометрическую точность и при ее восстановлении с помощью беспроводной системы диагностики точности станка в трех плоскостях модели QC20-W ballbar компании Renishaw. Этот метод в настоящее время является основным и самым востребованным на предприятиях при проведении ТОиР.
Мое знакомство с продукцией фирмы Renishaw началось с 2002 года, когда я занимался поиском компании исполнителя по капитальному ремонту с глубокой модернизацией координатно-измерительной машины (КИМ) модели OPTON-850. В 2005 году в Техническом центре возникла потребность в инновационных решениях по измерению геометрической точности многооперационных станков с ЧПУ, с последующей коррекцией параметров, вышедших за пределы паспортных параметров. В результате проведенного анализа рынка мы остановились на приборе Ballbar QC10. И приобрели его одними из первых в России. С этого момента у нас начали складываться тесные деловые отношения. Получив хорошие результаты при эксплуатации системы, мы совместно с представителями фирмы Renishaw организовали знакомство и практическое обучение через проводимые технические конференции. В последующем мы приобрели беспроводную систему Ballbar QC20-W.
Тенденции развития технологических и производственных процессов предъявляют повышенные требования к качеству обрабатываемых поверхностей детали, реализация которых требует применения повышенных режимов обработки деталей машин, что не всегда возможно из-за отсутствия информации о точностных характеристиках используемого оборудования. Поэтому необходимо улучшать методы диагностики технического состояния приводов металлообрабатывающих станков на этапе их эксплуатации, а также разработать эффективные мероприятия по оценке и повышению точности оборудования. Итак, я перехожу к разработанной методике комплексной диагностики технического состояния узлов станков с ЧПУ в части определения геометрической точности оборудования.
Диагностика привода подач по параметрам точности и
постоянства отработки круговой траектории
Задача контроля эксплуатационных характеристик станка с ЧПУ легко решается благодаря беспроводной системе диагностики точности станка в трех плоскостях
QC20-W ballbar компании Renishaw, которая дает
возможность проводить простую оперативную проверку точности позиционирования станка с учетом применяемых международных стандартов. Диагностика станка с ЧПУ производится при помощи электронно-механического прибора модели QQC20-W точностью 0,5 мкм и программы для расшифровки и анализа полученных данных. В процессе испытаний проводится контроль круговой траектории, выполняемой согласованными действиями приводов подач станка. Метод позволяет определить неисправности станка по 17 параметрам. Среди них - люфты по каждой координате, боковые люфты, рассогласование скорости приводов, неперпендикулярность осей, не прямолинейность по каждой оси. Результаты диагностики предоставляются в форме отчёта, включающего графики, таблицы расшифровки, анализ неисправностей и рекомендации по их устранению. Время проведения испытаний одного станка, обработки информации и выдача рекомендаций - 2-3 часа.
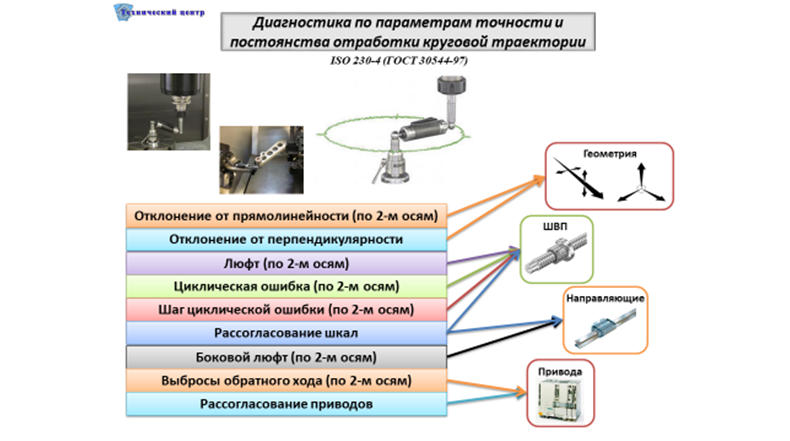
15. Средства диагностики, применяемые Техническим центром.
15.1. Система Renishaw QC10, QC20W.
15.2. Программное обеспечение Renishaw Ballbar.
15.3. Приспособление для токарных станков.
16. Рассмотрим общие сведения по проведению диагностики технического состояния привода подач по параметрам точности и постоянства отработки круговой траектории.
16.1. Диагностика по параметрам точности и постоянства отработки круговой траектории проводится в соответствии с ГОСТ 30544-97, ISO 230-4.
16.2. При проведении измерений оборудования с ЧПУ система QC20-W используется совместно с программным обеспечением «Ballbar 20», установленном на персональном компьютере.
16.3.Диагностика станков токарной группы производится при продольном перемещении станка по оси Z не менее 330 мм от патрона и поперечном перемещении станка по оси X не менее 210 мм от осевой линии.
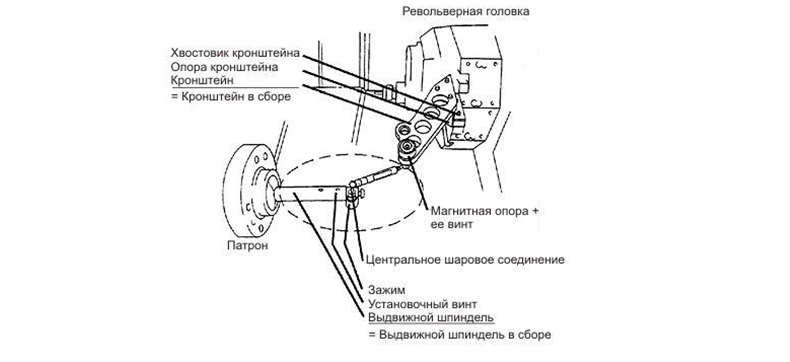
17. Параметры для оценки технического состояния привода подач
17.1. Отклонение от округлости, мкм.
17.2. Отклонение от прямолинейности (по 2-м осям), мкм/диаметр теста.
17.3. Отклонение от перпендикулярности, мкм/м.
17.4. Люфт (по 2-м осям), мкм.
17.5. Циклическая ошибка (по 2-м осям), мкм.
17.6. Шаг циклической ошибки (по 2-м осям), мм.
17.7. Рассогласование шкал, мкм.
17.8. Боковой люфт (по 2-м осям), мкм.
17.9. Выбросы обратного хода (по 2-м осям), мкм.
17.10. Рассогласование приводов, мс.
18. Порядок подготовки измерений в программном обеспечении «Renishaw Ballbar 20»
18.1. Создать в программном обеспечении «Renishaw Ballbar 20» модель станка, на котором необходимо провести измерения геометрической точности станка.
18.2. Создать в программном обеспечении «Renishaw Ballbar 20» для заданной модели станка координатные плоскости, измерения в которых необходимо провести.
18.3. Задать в программном обеспечении «Renishaw Ballbar 20» для заданных координатных плоскостей, измерения в которых необходимо провести, количество и направления проходов, радиуса измерений, скорости подачи.
19. Порядок проведения измерений параметров точности и постоянства отработки круговой траектории
19.1. Установить магнитные опоры диаметром 12 мм на шпинделе станка (для станков сверлильно-фрезерно-расточной групп) или на револьверной головке (для станков токарной групп).
19.2. Устранить центровой держатель на магнитной опоре на столе станка (для станков сверлильно-фрезерно-расточной групп) или в специальном приспособлении в патроне (для станков токарной групп), как показано на нижерасположенном рисунке.
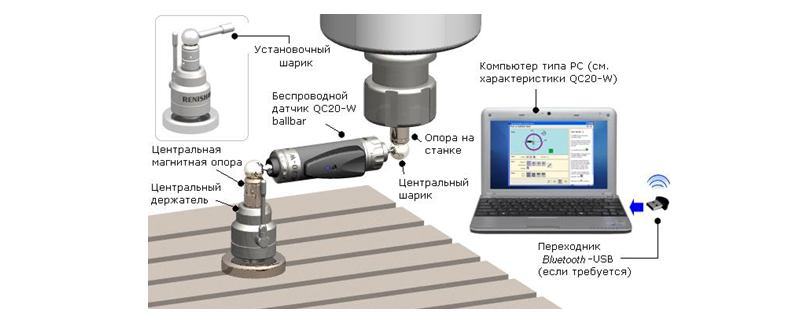
19.3. Соединить центровой держатель, посредством регулировки шарового шарнира, с магнитной опорой.
19.4. Определить нулевые точки (центра измеряемой окружности).
19.5. Выполнить отвод магнитной опоры от центрового держателя в направление точки старта на радиус измеряемой окружности.
19.6. Задать в системе ЧПУ станка управляющую программу движения системы вокруг центрового держателя.
19.7. Выполнить проверку управляющей программы по отдельным кадрам без установки измерительного датчика.
19.8. Подключить систему и выбрать в программном обеспечении «Renishaw Ballbar 20» координатную плоскость, в которой необходимо провести измерения.
19.9. Запустить управляющие программы. Произойдет движение исполнительных органов станка в позицию старта.
19.10. Установка измерительного датчика между центровым держателем и магнитной опорой.
19.11. Начать проведение измерений.
19.12. Сохранить результаты для последующей обработки и анализа, полученных данных.
19.13. Перейти при необходимости к следующей координатной плоскости.
20. Оценка технического состояния привода подач по результатам измерения параметров точности и постоянства отработки круговой траектории
20.1. Отклонение от округлости не должно превышать 0,6 % допуска округлости обрабатываемой с использованием круговой интерполяции цилиндрической поверхности изделия с учетом пересчета допусков в зависимости от размеров. Для станков класса точности «П» по ГОСТ 8-82 допуск округлости на диаметре тестовой окружности 300 мм должен быть не более 30 мкм.
20.2. Отклонение от прямолинейности на длине 300 мм не должно превышать для станков классов точности «П» – 10 мкм, «А» – 5 мкм.
20.3. Отклонение от перпендикулярности не должно превышать для станков классов точности «П» – 40 мкм/м, «А» – 20 мкм/м.
20.4. Люфт не должен превышать для станков классов точности «П» – 10 мкм, «А» – 5 мкм.
20.5. Циклическая ошибка связана с износом ШВП, эксцентричной установкой винта ШВП или датчика обратной связи, неисправностью устройства уравновешивания (для вертикальной оси). С учетом вклада циклической ошибки в общее отклонение от круглости принимается решение о регулировке или ремонте ШВП, датчика обратной связи или устройства уравновешивания.
20.6. Ошибка рассогласования шкал связана с применением неправильных параметров компенсации, растянутым при монтаже винтом ШВП, перегревом ШВП или отклонением от прямолинейности направляющих. С учетом вклада ошибки рассогласования шкал в общее отклонение от круглости после проверки правильности введенной компенсации принимается решение о регулировке или ремонте ШВП или направляющих.
20.7. Боковой люфт – люфт в системе направляющих станка. С учетом вклада бокового люфта в общее отклонение от округлости принимается решение о регулировке или ремонте направляющих станка.
20.8. Выбросы обратного хода связаны с недостаточной величиной крутящего момента для быстрого преодоления сил трения в направляющих или недостаточным временем срабатывания привода при смене направления движения. Выбросы обратного хода увеличиваются при увеличении подачи станка. С учетом вклада выбросов обратного хода в общее отклонение от округлости принимается решение о компенсации выбросов обратного хода средствами СЧПУ или подбора оптимальной величины подачи с минимальными выбросами обратного хода.
20.9. Рассогласование приводов связано с несоответствием коэффициента усиления одного привода другому. Рассогласование приводов не должно превышать 1 мс.
На нижерасположенном рисунке я показал протокол измерения.
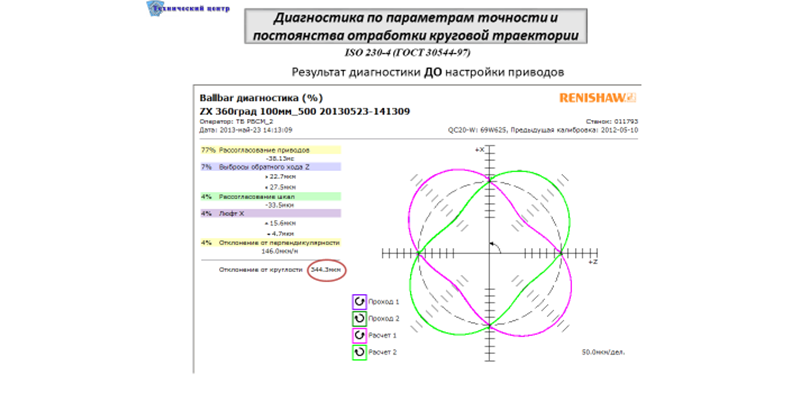
Теперь перейдем к методу определения точности позиционирования.
Контроль геометрических параметров точности позиционирования осей
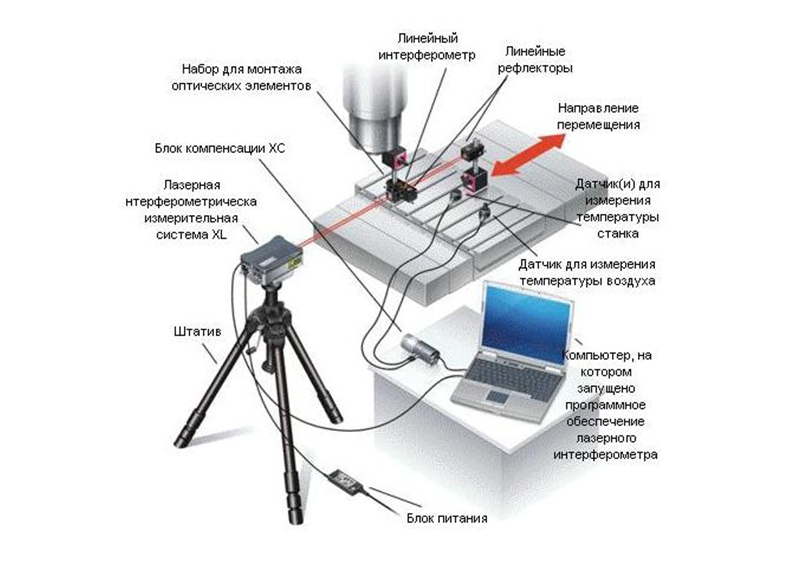
21. Средства измерения, применяемые Техническим центром при проверке точности позиционирования.
21.1. Электронные уровни (WYLER BlueLEVEL).
21.2. Лазерный интерферометр (Renishaw XL80).
21.3. Лазерные трекеры.
22. Основные параметры для оперативной оценки геометрической точности и точности позиционирования
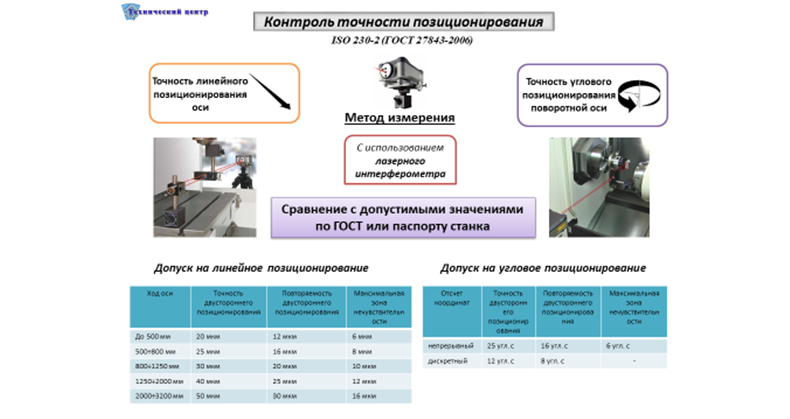
22.1. Прямолинейность перемещения вдоль оси.
22.2. Взаимная перпендикулярность осей.
22.3. Точность линейного позиционирования оси.
22.4. Точность углового позиционирования поворотной оси.
23. Общие сведения по измерению геометрических параметров и точности позиционирования
23.1. Измерение основных геометрических параметров (прямолинейности перемещения вдоль оси и взаимной перпендикулярности осей) проводится в соответствии с ГОСТ Р ИСО 230-1-2012 (ISO 230-1).
23.1. Измерение точности позиционирования проводится в соответствии с ГОСТ 27843-2006 (ISO 230-2).
23.2. В качестве средства измерения основных геометрических параметров используются электронные уровни.
23.3. При необходимости получения более высокой точности измерений, в частности для координатно-измерительных машин, используется лазерный интерферометр.
23.4. В качестве средства измерения точности линейного и углового позиционирования используется лазерный интерферометр.
23.5. Электронные уровни используются либо автономно, либо в комплекте со специальным программным обеспечением.
23.6. Лазерный интерферометр используется только в комплекте со специальным программным обеспечением.
24. Порядок измерения основных геометрических параметров
24.1. Установка электронного уровня жестко на подвижный базовый элемент станка, перемещающийся вдоль оси, прямолинейность которой необходимо измерить.
24.2. Подготовка маршрута измерений в специальном программном обеспечении.
24.3. Перемещение подвижного элемента на всю длину хода оси с равными шагами, фиксируя измеренные значения после каждого шага.
24.4. При измерении взаимной перпендикулярности двух осей последовательно измеряется прямолинейность каждой оси, при этом одна из осей берется за базу.
24.5. Формирование протокола измерений.
24.6. Сравнение с допустимыми значениями.
25. Порядок измерения точности позиционирования
25.1. Установка измерительного лазера жестко на штативе.
25.2. Монтаж оптических элементов в соответствии с руководством по эксплуатации лазерного интерферометра.
25.3. Подготовка маршрута измерений в специальном программном обеспечении.
25.4. Задание в системе ЧПУ станка управляющей программы перемещения по линейной или поворотной оси.
25.5. Проведение измерений в автоматическом режиме и запись результатов.
25.6. Сравнение полученных результатов с допустимыми значениями.
25.7. Проведение регулировки станка или компенсация погрешностей средствами СЧПУ.
25.8. Проведение повторных измерений.
25.9. Формирование протокола измерений.
26. Оценка технического состояния по результатам измерения геометрических параметров
26.1. Отклонение от прямолинейности не должно превышать:
26.1.1. На длине 300 мм для станков классов точности «П» – 10 мкм, «А» – 5 мкм.
26.1.2. На длине 500 мм для станков классов точности «П» – 12 мкм, «А» – 6 мкм.
26.1.3. На длине 500…800 мм для станков классов точности «П» – 16 мкм, «А» – 8 мкм.
26.1.4. На длине 800…1250 мм для станков классов точности «П» – 20 мкм, «А» – 10 мкм.
26.1.5. На длине 1250…2000 мм для станков классов точности «П» – 25 мкм, «А» – 12 мкм.
26.1.6. На длине 2000…3200 мм для станков классов точности «П» – 30 мкм, «А» – 16 мкм.
26.1.7. На длине 3200…5000 мм для станков класса точности «П» – 40 мкм.
26.1.8. На длине 5000…8000 мм для станков класса точности «П» – 50 мкм.
26.1.9. На длине 8000…12500 мм для станков класса точности «П» – 60 мкм.
26.2. Отклонение от перпендикулярности не должно превышать для станков классов точности «П» – 40 мкм/м, «А» – 20 мкм/м.
27. Оценка технического состояния по результатам измерения точности позиционирования
27.1. Отклонение от точности линейного двустороннего позиционирования не должно превышать:
27.1.1. На длине 500 мм для станков классов точности «П» – 20 мкм, «А» – 10 мкм.
27.1.2. На длине 500…800 мм для станков классов точности «П» – 25 мкм, «А» – 12 мкм.
27.1.3. На длине 800…1250 мм для станков классов точности «П» – 30 мкм, «А» – 16 мкм.
27.1.4. На длине 1250…2000 мм для станков классов точности «П» – 40 мкм, «А» – 20 мкм.
27.1.5. На длине 2000…3200 мм для станков классов точности «П» – 50 мкм, «А» – 25 мкм.
27.1.6. Отклонение от точности углового двустороннего позиционирования не должно превышать при непрерывном отсчете координат для станков классов точности «П» – 25 угл. с., «А» – 16 угл. с.
27.1.7. Отклонение от точности углового двустороннего позиционирования не должно превышать при механической фиксации дискретных угловых положений для станков
классов точности «П» – 12 угл. с., «А» – 8 угл.с
На нижерасположенном рисунке мы видим схему измерения точности углового позиционирования поворотного стола многооперационного станка лазерным интерферометром модели XL-80 Renishaw.
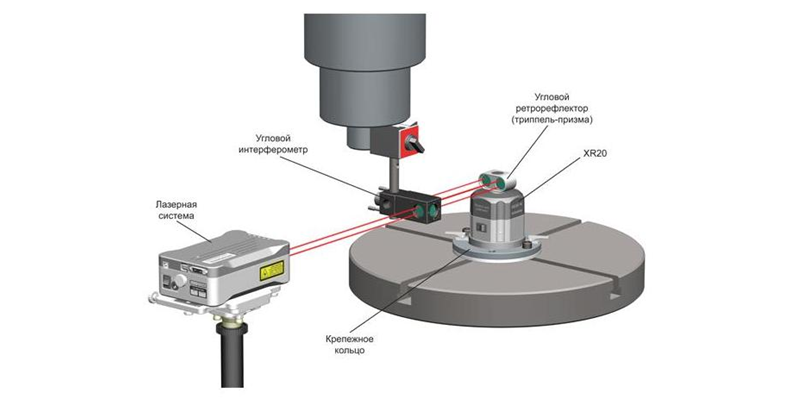
Уважаемые коллеги, на этом я заканчиваю третью часть статьи о комплексной диагностике узлов многооперационных станков с ЧПУ. Буду рад, если статья Вам понравилась и принесла практическую пользу. В других статьях я рассмотрю другие методы безразборной диагностики и метод проверки объемной геометрической точности крупногабаритных многооперационных станков с ЧПУ.