Доброе время суток, уважаемые коллеги!
Сегодня моя статья будет носить исключительно теоретический познавательный характер, но не расстраивайтесь - менее полезной она не станет. Дело в том, что проблемы защиты шпинделей и других механических узлов станков с ЧПУ в настоящее время стали весьма актуальными и на прямую влияют на надежность и производительность работы станков с ЧПУ и на их ресурс.
Также в этой статье я расскажу о некоторых способах реализации проектов внедрения на станках с ЧПУ систем противостолкновения шпинделя с узлами станка и приспособленьями. А также проведу краткий обзор нескольких используемых систем противостолкновения, с которыми мне приходилось встречаться на предприятиях Европы. Итак, давайте рассмотрим, что такое столкновение узлов станка в процессе обработки?
Столкновение- это контакт шпинделя или резцедержки с другим узлом станка, оснасткой или обрабатываемой деталью. Существует 2 типа столкновений: динамическое и статическое.
Динамическое столкновение происходит в основном на высокой скорости подачи.
Статическое столкновение происходит в основном на низкой скорости подачи.
На нижерасположенном рисунке представлена диаграмма анализа причин простоя и времени восстановления шпинделей в период с 2014 по 2016 годы.
Сегодня моя статья будет носить исключительно теоретический познавательный характер, но не расстраивайтесь - менее полезной она не станет. Дело в том, что проблемы защиты шпинделей и других механических узлов станков с ЧПУ в настоящее время стали весьма актуальными и на прямую влияют на надежность и производительность работы станков с ЧПУ и на их ресурс.
Также в этой статье я расскажу о некоторых способах реализации проектов внедрения на станках с ЧПУ систем противостолкновения шпинделя с узлами станка и приспособленьями. А также проведу краткий обзор нескольких используемых систем противостолкновения, с которыми мне приходилось встречаться на предприятиях Европы. Итак, давайте рассмотрим, что такое столкновение узлов станка в процессе обработки?
Столкновение- это контакт шпинделя или резцедержки с другим узлом станка, оснасткой или обрабатываемой деталью. Существует 2 типа столкновений: динамическое и статическое.
Динамическое столкновение происходит в основном на высокой скорости подачи.
Статическое столкновение происходит в основном на низкой скорости подачи.
На нижерасположенном рисунке представлена диаграмма анализа причин простоя и времени восстановления шпинделей в период с 2014 по 2016 годы.
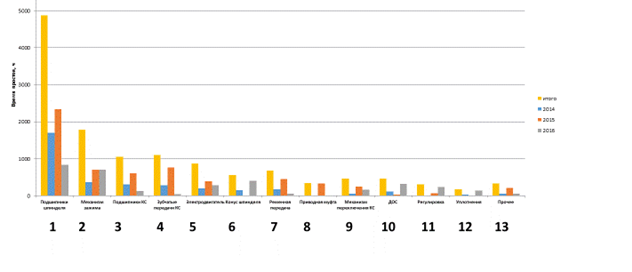
1. Подшипники шпинделя в результате столкновения.
2. Механизм зажима инструмента.
3. Подшипники шпиндельной бабки.
4. Зубчатые передачи шпиндельной бабки.
5. Электродвигатель.
6. Внутренний конус шпинделя.
7. Ременные передачи.
8. Приводные муфты.
9. Механизмы переключения скоростей шпинделя.
10. Датчики обратной связи.
11. Разрегулировка привода.
12. Выход из строя уплотнений.
13. Прочие.
2. Механизм зажима инструмента.
3. Подшипники шпиндельной бабки.
4. Зубчатые передачи шпиндельной бабки.
5. Электродвигатель.
6. Внутренний конус шпинделя.
7. Ременные передачи.
8. Приводные муфты.
9. Механизмы переключения скоростей шпинделя.
10. Датчики обратной связи.
11. Разрегулировка привода.
12. Выход из строя уплотнений.
13. Прочие.
ПОВРЕЖДЕНИЯ ИЗ-ЗА СТОЛКНОВЕНИЙ
Столкновения и аварии, которые происходят в станках, часто приводят к серьезным повреждениям шпинделей, резцедержек, приводов подач и снижению точности обработки с высокими последующими материальными издержками. В результате столкновения степень повреждения может быстро стать значительной и привести не только к непригодности многих узлов, но и к повреждению самого станка, включая электроаппаратуру. Ремонт стоит дорого, и, прежде всего, останавливается производство.
Основными причинами отказа являются износ деталей и эксплуатационные ошибки. Можно выделить две категории причин: геометрические столкновения (между движущимися компонентами внутри станка) и технологические столкновения (из-за перегрузочных ситуаций при рабочем вмешательстве режущей кромки инструмента в заготовку). Распространенными причинами являются неправильные параметры резания, износ или включения в материал, а также, как уже упоминалось ранее, эксплуатационные ошибки, такие как неправильный инструмент или ручное перемещение осей.
Из проведенного анализа выхода из строя шпинделей на предприятии было выявлено, что 70% их отказов являются результатом удара шпинделя с заготовкой, приспособлением и другими узлами станка. Из этих 70% отказов 60% приходится на человеческий фактор, включающий в себя:
1. Ошибки в управляющей программе (УП).
2. Загрузка неправильной УП.
3. Работа в другом режиме.
4. Применение неправильного инструмента.
5. Неправильный зажим детали.
6. Нахождение посторонних предметов в рабочей зоне станка.
7. Ошибка в измерении инструмента.
На нижерасположенном рисунке приведена причинно-следственная диаграмма, раскрывающая последствия столкновения шпинделя с заготовкой или узлом станка (выход из строя элементов шпинделя).
Столкновения и аварии, которые происходят в станках, часто приводят к серьезным повреждениям шпинделей, резцедержек, приводов подач и снижению точности обработки с высокими последующими материальными издержками. В результате столкновения степень повреждения может быстро стать значительной и привести не только к непригодности многих узлов, но и к повреждению самого станка, включая электроаппаратуру. Ремонт стоит дорого, и, прежде всего, останавливается производство.
Основными причинами отказа являются износ деталей и эксплуатационные ошибки. Можно выделить две категории причин: геометрические столкновения (между движущимися компонентами внутри станка) и технологические столкновения (из-за перегрузочных ситуаций при рабочем вмешательстве режущей кромки инструмента в заготовку). Распространенными причинами являются неправильные параметры резания, износ или включения в материал, а также, как уже упоминалось ранее, эксплуатационные ошибки, такие как неправильный инструмент или ручное перемещение осей.
Из проведенного анализа выхода из строя шпинделей на предприятии было выявлено, что 70% их отказов являются результатом удара шпинделя с заготовкой, приспособлением и другими узлами станка. Из этих 70% отказов 60% приходится на человеческий фактор, включающий в себя:
1. Ошибки в управляющей программе (УП).
2. Загрузка неправильной УП.
3. Работа в другом режиме.
4. Применение неправильного инструмента.
5. Неправильный зажим детали.
6. Нахождение посторонних предметов в рабочей зоне станка.
7. Ошибка в измерении инструмента.
На нижерасположенном рисунке приведена причинно-следственная диаграмма, раскрывающая последствия столкновения шпинделя с заготовкой или узлом станка (выход из строя элементов шпинделя).
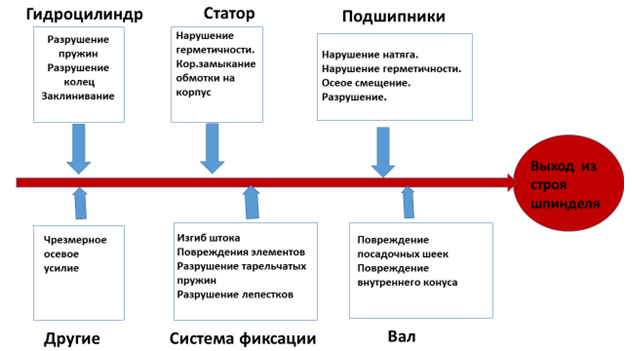
Исходя из вышесказанного можно сделать вывод, что защита шпинделя по току, наверное, самый распространённый и обязательный вид защиты, применяемый на станках для предупреждения разрушительных последствий при столкновении шпинделя с заготовкой или узлом станка. Аппаратная защита позволяет реализовать систему противостолкновения с быстродействием в пределах нескольких микросекунд, а если бюджет позволяет, то в пределах 100-200 наносекунд, что в принципе достаточно для решения защиты шпинделя и узлов станка.
Программная защита от столкновения
Системы предотвращения столкновений без использования датчиков состоят из чистого программного обеспечения. Рассматривается геометрическое пространство станка, где возможны столкновения. Описываются объекты, в пределах которых вращаются оси, перемещается инструмент и деталь.
Назначаются минимальные расстояния на границах опасных зон. В программе закладываются условия, чтобы описанные объемы не имели возможность пересекаться. Естественно, это не относится к режущей кромке инструмента. Если все геометрические объемы правильно описаны и наложены связи на их движение, то технологический процесс, управляемый такой программой, бу дет соответствовать реальности, а столкновений не будет происходить. Если, как это часто бывает, производятся изменения в программе и при этом допускаются ошибки, а также используются другие заготовки и инструменты, то все это может привести к возникновению столкновений.
Автоматическая система противостолкновения VCM
Программная защита от столкновения
Системы предотвращения столкновений без использования датчиков состоят из чистого программного обеспечения. Рассматривается геометрическое пространство станка, где возможны столкновения. Описываются объекты, в пределах которых вращаются оси, перемещается инструмент и деталь.
Назначаются минимальные расстояния на границах опасных зон. В программе закладываются условия, чтобы описанные объемы не имели возможность пересекаться. Естественно, это не относится к режущей кромке инструмента. Если все геометрические объемы правильно описаны и наложены связи на их движение, то технологический процесс, управляемый такой программой, бу дет соответствовать реальности, а столкновений не будет происходить. Если, как это часто бывает, производятся изменения в программе и при этом допускаются ошибки, а также используются другие заготовки и инструменты, то все это может привести к возникновению столкновений.
Автоматическая система противостолкновения VCM
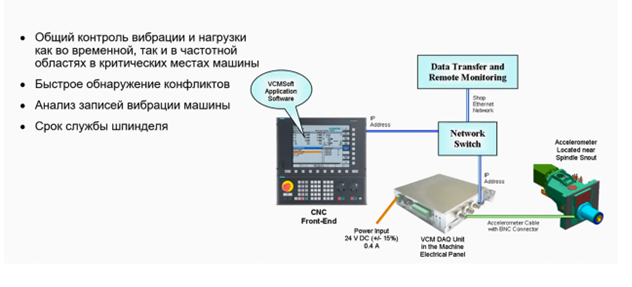
На нижерасположенном рисунке показаны возможности системы VCM по предотвращению или к сведению к минимуму повреждений шпинделя станка из-за столкновения в режиме реального времени.
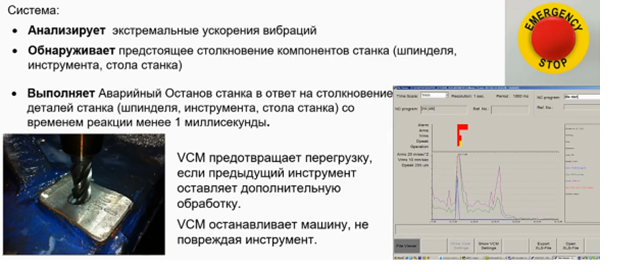
В начале 2000-х годов технологические службы предприятий, занимающиеся разработкой управляющих программ (УП) для станков с ЧПУ получили возможность при контроле разработанной управляющей программы осуществлять контроль за столкновениями, используя моделирование движения инструмента по координатам. Базовой частью таких систем стали подсистемы обнаружения столкновений. В общем случае задача данной подсистемы состоит в проверке – пересекаются ли два или три объекта в рабочем пространстве станка. Для осуществления контроля разработанных программ на столкновение узлов станков технологи начали применять программный комплекс для визуализации процесса обработки деталей на станках с ЧПУ VERICUT .
Имитация работы станка средствами системы VERICUТ позволяет обнаружить столкновения и опасные сближения с любыми компонентами оборудования, такими как направляющие, инструментальные шпиндели, револьверные головки, поворотные столы, устройства смены инструмента, крепежные приспособления, заготовки, режущий инструмент, другие определенные пользователем объекты. Вы можете задать границы зон опасного сближения с элементами, а перемещение станочных элементов можно просматривать в пошаговом режиме и в обратном направлении. Инструменты для визуализации сложных операций
Новые методы механообработки и сложные функции систем управления требуют более широких возможностей имитации. VERICUT поддерживает автоматическую передачу детали между крепежными приспособлениями, работу радиального суппорта (или программируемого выдвижного шпинделя) расточного станка, программирование синхронизации одновременной многоосевой обработки на токарно-фрезерных центрах, системы ЧПУ, которые позволяют программировать ориентацию осей инструмента.
Проверка управляющих программ
В VERICUT Verification поиск программных ошибок и проверка точности изготовления деталей осуществляются легко и просто.
Благодаря уникальным алгоритмам VERICUT обеспечиваются быстрые и точные результаты, при этом с увеличением числа проходов производительность системы не снижается. Таким образом VERICUT позволяет работать с управляющей программой, содержащей миллионы кадров обработки.
Достоверная проверка на столкновения
VERICUT гарантирует достоверность проверки управляющих программ на столкновения. Проверка траектории перемещения производится не только в узловых точках пути, но и на всем пути следования от точки к точке, учитывая различные виды интерполяций. В VERICUT можно смело увеличивать шаг проверки траектории, так как при этом все столкновения также отслеживаются.
А теперь я перейду к освещению аппаратно-программного комплекса AVCM, созданного на базе программного продукта VCM фирмы Simens и системы адаптивного управления производства фирмы Omative (аппаратная часть)
AVCM - СИСТЕМА АДАПТИВНОГО УПРАВЛЕНИЯ В СОЧЕТАНИИ С МОНИТОРИНГОМ И ГЛУБОКОЙ ДИАГНОСТИКОЙ УДЕЛЬНОЙ НАГРУЗКИ И ВИБРАЦИИ КОРПУСА ЩПИНДЕЛЯ.
Данная система состоит из двух подсистем.
1.Подсистема обнаружения и подавления вибрации
Подсистема анализирует спектр вибрации во время резания, различает аномальные модели вибрации и автоматически активирует модуляцию скорости вращения шпинделя для подавления вибрации.
2.Подсистема контроля вибрации инструмента.
Подсистема станка автоматически узнает приемлемые уровни вибрации для каждой операции обработки заготовки и для каждой текущей операции, определяется максимальный уровень вибрации (во временной и частотной областях). Решения симуляции обработки на базе G кодов.
Данное решение позволяет обнаружить потенциальные проблемы, связанные со столкновением инструмента, шпинделя с другими узлами станка на стадии отладки управляющей программы.
Итак, как можно защитить шпиндель и продлить срок его работоспособности в соответствии с паспортными характеристиками?
Приобрести портативный блок анализа вибраций, который может работать через приложение для планшетов. Приложение работает с акселерометром, который является пьезоэлектрическим измерительным устройством, используемым для измерения вибрации на определенных частотах.
Система защиты от столкновений должна по возможности учитывать все источники ошибок, которые могут привести к столкновению. Имеются два принципиально разных способа: с применением датчиков и без них.
Системы предотвращения столкновений с датчиками работают с очень разными видами датчиков. Часто используют оптические датчики формы, датчики вибрации, скорости, ускорения и камеры, сигнал от которых расшифровывается, что позволяет своевременно предотвратить столкновение. При использовании камер требуются дорогостоящие устройства переработки сигнала. Другие системы базируются на силовых датчиках, которые устанавливаются там, где возможно столкновение.
Я в своей новой статье подробно остановлюсь на системах против столкновения, использующих различные типы датчиков.
На этом я заканчиваю первую часть статьи на тему «Автоматизированные системы против столкновения шпинделя с узлами станков с ЧПУ». Надеюсь, что Вам было интересно читать данную статью и надеюсь, что она даст какие-то новые знания или освежит в памяти старые.
Имитация работы станка средствами системы VERICUТ позволяет обнаружить столкновения и опасные сближения с любыми компонентами оборудования, такими как направляющие, инструментальные шпиндели, револьверные головки, поворотные столы, устройства смены инструмента, крепежные приспособления, заготовки, режущий инструмент, другие определенные пользователем объекты. Вы можете задать границы зон опасного сближения с элементами, а перемещение станочных элементов можно просматривать в пошаговом режиме и в обратном направлении. Инструменты для визуализации сложных операций
Новые методы механообработки и сложные функции систем управления требуют более широких возможностей имитации. VERICUT поддерживает автоматическую передачу детали между крепежными приспособлениями, работу радиального суппорта (или программируемого выдвижного шпинделя) расточного станка, программирование синхронизации одновременной многоосевой обработки на токарно-фрезерных центрах, системы ЧПУ, которые позволяют программировать ориентацию осей инструмента.
Проверка управляющих программ
В VERICUT Verification поиск программных ошибок и проверка точности изготовления деталей осуществляются легко и просто.
Благодаря уникальным алгоритмам VERICUT обеспечиваются быстрые и точные результаты, при этом с увеличением числа проходов производительность системы не снижается. Таким образом VERICUT позволяет работать с управляющей программой, содержащей миллионы кадров обработки.
Достоверная проверка на столкновения
VERICUT гарантирует достоверность проверки управляющих программ на столкновения. Проверка траектории перемещения производится не только в узловых точках пути, но и на всем пути следования от точки к точке, учитывая различные виды интерполяций. В VERICUT можно смело увеличивать шаг проверки траектории, так как при этом все столкновения также отслеживаются.
А теперь я перейду к освещению аппаратно-программного комплекса AVCM, созданного на базе программного продукта VCM фирмы Simens и системы адаптивного управления производства фирмы Omative (аппаратная часть)
AVCM - СИСТЕМА АДАПТИВНОГО УПРАВЛЕНИЯ В СОЧЕТАНИИ С МОНИТОРИНГОМ И ГЛУБОКОЙ ДИАГНОСТИКОЙ УДЕЛЬНОЙ НАГРУЗКИ И ВИБРАЦИИ КОРПУСА ЩПИНДЕЛЯ.
Данная система состоит из двух подсистем.
1.Подсистема обнаружения и подавления вибрации
Подсистема анализирует спектр вибрации во время резания, различает аномальные модели вибрации и автоматически активирует модуляцию скорости вращения шпинделя для подавления вибрации.
2.Подсистема контроля вибрации инструмента.
Подсистема станка автоматически узнает приемлемые уровни вибрации для каждой операции обработки заготовки и для каждой текущей операции, определяется максимальный уровень вибрации (во временной и частотной областях). Решения симуляции обработки на базе G кодов.
Данное решение позволяет обнаружить потенциальные проблемы, связанные со столкновением инструмента, шпинделя с другими узлами станка на стадии отладки управляющей программы.
Итак, как можно защитить шпиндель и продлить срок его работоспособности в соответствии с паспортными характеристиками?
Приобрести портативный блок анализа вибраций, который может работать через приложение для планшетов. Приложение работает с акселерометром, который является пьезоэлектрическим измерительным устройством, используемым для измерения вибрации на определенных частотах.
Система защиты от столкновений должна по возможности учитывать все источники ошибок, которые могут привести к столкновению. Имеются два принципиально разных способа: с применением датчиков и без них.
Системы предотвращения столкновений с датчиками работают с очень разными видами датчиков. Часто используют оптические датчики формы, датчики вибрации, скорости, ускорения и камеры, сигнал от которых расшифровывается, что позволяет своевременно предотвратить столкновение. При использовании камер требуются дорогостоящие устройства переработки сигнала. Другие системы базируются на силовых датчиках, которые устанавливаются там, где возможно столкновение.
Я в своей новой статье подробно остановлюсь на системах против столкновения, использующих различные типы датчиков.
На этом я заканчиваю первую часть статьи на тему «Автоматизированные системы против столкновения шпинделя с узлами станков с ЧПУ». Надеюсь, что Вам было интересно читать данную статью и надеюсь, что она даст какие-то новые знания или освежит в памяти старые.