Добрый день, уважаемые коллеги!
Желаю Вам чудесного настроения и позитива при прочтении моих статей на тему ТОиР оборудования с ЧПУ! Большое Вам спасибо за ваши письма.
Целью моих ранее написанных статей было показать пример того, что в России есть промышленные предприятия, которые активно занимаются разработкой и внедрением инновационных АСУ ТОиР оборудования. Внедрение АСУ «ТОиР оборудования» для предприятия означает создание информационного взаимодействия всех вовлеченных в процесс ТОиР оборудования лиц, при котором они будут выдавать и получать достоверные, своевременные и полные данные о техническом состоянии оборудовании и о процессе ТОиР, а руководители, кроме того, будут пользоваться этими данными и основывать на них свои решения.
Сегодняшнюю статью я начну с краткого анализа отказов оборудования с ЧПУ.
Современные станки с ЧПУ представляют собой технически сложные электронно-механические устройства. И насколько бы надёжным ни было оборудование, оно периодически выходит из строя. Обработка металлов и, в особенности, твёрдых сталей связана с выделением большого количества энергии, что и влечёт за собой потерю функциональности работы станка.
В перечень основных неисправностей станка с ЧПУ входят следующие.
Специфика перечисленных выше неисправностей позволяет разделить их на два класса – механические и электронные. Такая дискретизация в свою очередь даёт Техническому центру ТОиР оборудования предприятия возможность комплексно подходить к анализу технического состояния оборудования и существенно сокращать время ремонта, за счет имеющихся специалистов по механике, гидравлике, электрике и электронике.
Данную статью я хочу начать с относительно нового подхода определения дефектов, связанного с созданием и применении модуля расчета модели отказов на базе метода энергетического состояния деталей и узлов. В процессе мониторинга технического состояния оборудования с ЧПУ методом вибрационной диагностики мы столкнулись с рядом проблем по определению зарождающих дефектов и отказов оборудования, связанных с усталостью металлов, его физического старения, результатами коррозии и многими другими факторами.
Для заблаговременного определения вышеперечисленных факторов необходим был новый взгляд на появившиеся проблемы и новые методы диагностики, так как мы считали и считаем, что улучшение и совершенствование АСУ «Мониторинг» это непрерывный путь, состоящий из маленьких шагов, которые приведут к повышению эффективности работы Технического центра ТОиР оборудования с ЧПУ и к повышению эффективности работы оборудования.
В АСУ «Мониторинг», интегрированной в АСУ «ТОиР оборудования с ЧПУ» мы включили два модуля расчета моделей отказов узлов оборудования:
Давайте рассмотрим модель отказа оборудования с точки зрения его энергетического состояния.
Для того чтобы приступить к разработке модели отказа оборудования необходимо выяснить условия возникновения отказа оборудования. При эксплуатации оборудования возникают отказы при условии:
В период эксплуатации оборудования на него действуют следующие энергетические воздействия:
Величины этих энергий, в виде сигналов, поступающих с датчиков температуры, давления, виброперемещения, виброскорости и виброускорения и информация об условиях эксплуатации оборудования и его технического состояния поступают в блок «Изменения» АСУ «Мониторинг», в котором формируются обратимые и необратимые процессы происходящих изменений в работе узлов оборудования. Необратимые изменения поступают в блок «Физическое старение». Из блока «Физическое старение» информация поступает в блок «Сравнения», который отвечает на вопрос «Функциональный параметр превысил допустимый предел?». Если предел превышен, то формируется сигнал «Отказ». Если предел не превышен, то информация направляется в блок «Физическое старение», который формирует параметры технического ухудшения оборудования и передает их в модуль «Техническое состояние оборудования». После чего бюро ППР включает в месячный план ремонта ремонтному бюро плановую замену, которая заключается в принудительном изъятии элемента оборудования из эксплуатации после выработки регламента работы и замены его новым, все технические параметры соответствуют установленным требованиям.
На нижерасположенном рисунке показана действующая модель алгоритма отказа оборудования.
Желаю Вам чудесного настроения и позитива при прочтении моих статей на тему ТОиР оборудования с ЧПУ! Большое Вам спасибо за ваши письма.
Целью моих ранее написанных статей было показать пример того, что в России есть промышленные предприятия, которые активно занимаются разработкой и внедрением инновационных АСУ ТОиР оборудования. Внедрение АСУ «ТОиР оборудования» для предприятия означает создание информационного взаимодействия всех вовлеченных в процесс ТОиР оборудования лиц, при котором они будут выдавать и получать достоверные, своевременные и полные данные о техническом состоянии оборудовании и о процессе ТОиР, а руководители, кроме того, будут пользоваться этими данными и основывать на них свои решения.
Сегодняшнюю статью я начну с краткого анализа отказов оборудования с ЧПУ.
Основные неисправности станков с ЧПУ
Современные станки с ЧПУ представляют собой технически сложные электронно-механические устройства. И насколько бы надёжным ни было оборудование, оно периодически выходит из строя. Обработка металлов и, в особенности, твёрдых сталей связана с выделением большого количества энергии, что и влечёт за собой потерю функциональности работы станка.
В перечень основных неисправностей станка с ЧПУ входят следующие.
- Поломка приводов.
- Повреждения датчиков.
- Выход и строя элементов гидравлики.
- Выход из строя элементов электрики.
- Снижение точности металлообработки.
- Выход из строя сервисных систем.
- Отказы программного обеспечения, управляющего оборудованием.
- Поломки электронной части, связанные, прежде всего, с нарушением в алгоритмах обработки информации, получаемой от датчиков.
- Выход из строя логических радиокомпонентов.
- Ухудшения обратной связи.
- Изменения кодировки ЧПУ, которые могут носить как спонтанный, так и преднамеренный характер. В последнем случае речь идёт о вирусных атаках на оборудование. Вот почему информационная защита даже на металлообрабатывающем заводе является делом необходимым и важным.
Специфика перечисленных выше неисправностей позволяет разделить их на два класса – механические и электронные. Такая дискретизация в свою очередь даёт Техническому центру ТОиР оборудования предприятия возможность комплексно подходить к анализу технического состояния оборудования и существенно сокращать время ремонта, за счет имеющихся специалистов по механике, гидравлике, электрике и электронике.
Данную статью я хочу начать с относительно нового подхода определения дефектов, связанного с созданием и применении модуля расчета модели отказов на базе метода энергетического состояния деталей и узлов. В процессе мониторинга технического состояния оборудования с ЧПУ методом вибрационной диагностики мы столкнулись с рядом проблем по определению зарождающих дефектов и отказов оборудования, связанных с усталостью металлов, его физического старения, результатами коррозии и многими другими факторами.
Для заблаговременного определения вышеперечисленных факторов необходим был новый взгляд на появившиеся проблемы и новые методы диагностики, так как мы считали и считаем, что улучшение и совершенствование АСУ «Мониторинг» это непрерывный путь, состоящий из маленьких шагов, которые приведут к повышению эффективности работы Технического центра ТОиР оборудования с ЧПУ и к повышению эффективности работы оборудования.
В АСУ «Мониторинг», интегрированной в АСУ «ТОиР оборудования с ЧПУ» мы включили два модуля расчета моделей отказов узлов оборудования:
- первый модуль расчета модели отказов на базе метода вибродигностики, который был достаточно хорошо описан в моих предыдущих статьях
- второй модуль расчета модели отказов на базе метода энергетического состояния деталей, узлов оборудования, который является относительно новым.
Давайте рассмотрим модель отказа оборудования с точки зрения его энергетического состояния.
Для того чтобы приступить к разработке модели отказа оборудования необходимо выяснить условия возникновения отказа оборудования. При эксплуатации оборудования возникают отказы при условии:
- Наличия достаточного количества энергии для изменения в узле оборудования.
- Необратимого изменения в узлах оборудования, которое приводит к изменению параметра, характеризующего способность оборудования выполнять требуемые функции.
- Изменения параметра, характеризующего способность оборудования выполнять требуемые функции, выходит за установленные пределы.
В период эксплуатации оборудования на него действуют следующие энергетические воздействия:
- энергия внешних источников
- энергия внутренних источников
- энергия рабочего процесса
Величины этих энергий, в виде сигналов, поступающих с датчиков температуры, давления, виброперемещения, виброскорости и виброускорения и информация об условиях эксплуатации оборудования и его технического состояния поступают в блок «Изменения» АСУ «Мониторинг», в котором формируются обратимые и необратимые процессы происходящих изменений в работе узлов оборудования. Необратимые изменения поступают в блок «Физическое старение». Из блока «Физическое старение» информация поступает в блок «Сравнения», который отвечает на вопрос «Функциональный параметр превысил допустимый предел?». Если предел превышен, то формируется сигнал «Отказ». Если предел не превышен, то информация направляется в блок «Физическое старение», который формирует параметры технического ухудшения оборудования и передает их в модуль «Техническое состояние оборудования». После чего бюро ППР включает в месячный план ремонта ремонтному бюро плановую замену, которая заключается в принудительном изъятии элемента оборудования из эксплуатации после выработки регламента работы и замены его новым, все технические параметры соответствуют установленным требованиям.
На нижерасположенном рисунке показана действующая модель алгоритма отказа оборудования.
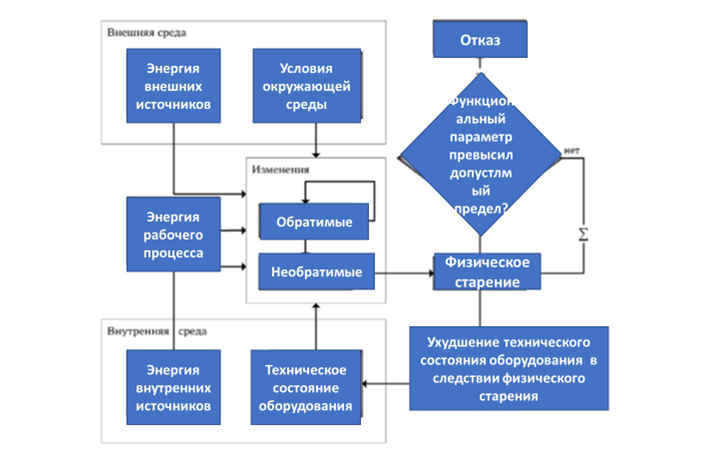
Применяемые Техническим центром методы устранения и снижения количества отказов оборудования с ЧПУ
-Проведение мониторинга с глубокой диагностикой технического состояния оборудования и его узлов.
-Проведение плановых ТОиР оборудования в целях восстановления соответствия параметров оборудования установленным требованиям паспорта.
-Проведение плановой замены, которая заключается в принудительном изъятии элемента оборудования из эксплуатации после выработки назначенного срока службы, его техническим состоянием и замене его другим, все технические параметры которого соответствуют установленным требованиям.
-Обнаружение отказов оборудования, которые заключаются в установлении способности оборудования выполнять назначенные функции.
-Отказ от проведения ТОиР оборудования по причине хорошего его технического состояния или неготовности к проведению ТОиР оборудования из-за отсутствия ресурсов.
-Использовать упреждающую (проактивную) концепцию ТОиР.
Для упреждения отказов узлов оборудования Технический центр применил следующие действия:
-выполнял все необходимые операции и мероприятия по ТОиР оборудования, направленные на снижение скорости развития неисправностей и дефектов, которые были выявлены на основе полученных сведений о фактическом техническом состоянии узлов оборудования с помощью мониторинга с глубокой диагностикой, действующей по алгоритму, представленному на нижерасположенном рисунке.
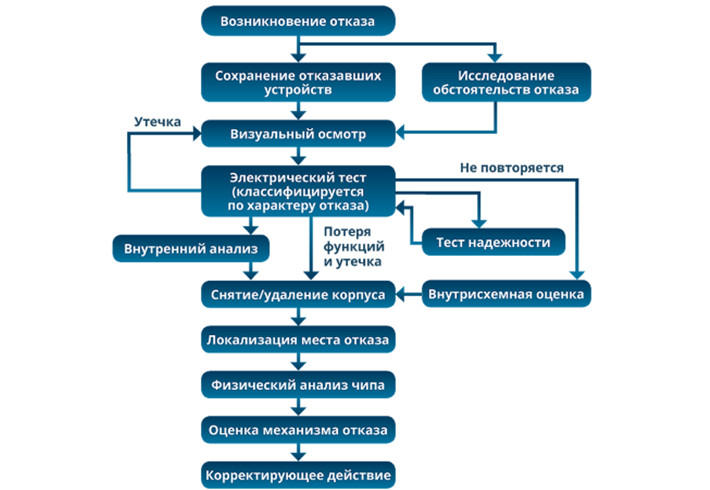
-выполнял записи характеристик поведения узлов оборудования при его вводе в эксплуатацию и после проведения капитального ремонта оборудования, так как все виды возможных неисправностей в зачаточном или явном виде потенциально присутствуют во всем оборудовании, запускаемом в эксплуатацию.
-определял детерминирующие неисправности оборудования по отношению к работоспособности конкретной единицы оборудования, так как воздействие совокупности всех факторов, сопровождающих эксплуатацию оборудования вызывает ускоренное развитие одной или нескольких неисправностей.
Для повышения эффективности и надежности работы оборудования с ЧПУ и решения вышеперечисленных проблем, Технический ТОиР оборудования с ЧПУ в 2002 году приступил к разработке и поэтапному внедрению с последующим совершенствованием АСУ «ТОиР оборудования с ЧПУ». За время существования службы ТОиР оборудования мы прошли следующие этапы применения стратегий управления ТОиР оборудования:
В общем случае по разработанному техническому заданию АСУ «ТОиР оборудования с ЧПУ» должна поддерживать решение следующих задач в области управления ТОиР:
-ведение нормативно-справочной информации по оборудованию;
-ведение эксплуатационной и ремонтной документации;
-формирование и ведение базы данных по оборудованию;
-ведение информации о персонале, участвующем в управлении ТОиР;
-оценка и прогнозирование технического состояния оборудования;
-формирование и пересмотр программ технического обслуживания;
-планирование работ по ТОиР;
-определение потребностей в материальных ресурсах;
-обеспечение материально- технических ресурсов;
-выполнение и учет внеплановых работ;
-выполнение и учет плановых работ;
-обеспечение безопасных условий выполнения работ;
-измерение и анализ показателей эффективности;
-принятие решений в отношении списания, замены и модернизации.
В современных условиях, на современных предприятиях машиностроения процессы ТОиР оборудования стали признаваться ключевыми элементами производственного процесса, целями которого являются:
-Минимизировать затраты;
-Увеличить время безотказной работы оборудования;
-Увеличить производительность;
-Работать с финансовыми потерями, так как они часто являются следствием неудовлетворительного планирования, отказа от рассмотрения новых концепций ведения работ или неспособности уделять внимание незначительным изменениям в работе оборудования;
-Развить диагностическое и профилактическое техническое обслуживание;
-Внедрять опыт успешных предприятий;
-Создать программы и проводить обучения для ремонтного персонала;
-Консультировать специалистов 24/7, используя Чат-боты со специальными программами и текстом.
Основные проблемы, которые я вижу в области технического обслуживания и ремонта оборудования на сегодняшний день следующие:
-Система мотивации в области ТОиР отсутствует или несовершенна;
-Инструментальная оснащенность низкая;
-Отсутствие программ передачи опыта;
-Компетенции ремонтного персонала в основном низкая;
-Ключевые показатели эффективности (КПЭ) ремонтной службы составлены без учета производственных служб предприятия;
-Чистое время ремонта на уровне 25% – 40%;
-Отсутствие программы развития ремонтной службы;
-Отсутствие качественного автоматизированного планирования работ по ТОиР оборудования;
-Недоверие некомпетентному руководству служб ТОиР на предприятиях;
-Отсутствие специализированных обучающих классов (для обучения и тренировок);
-Отсутствие автоматического учета наработки оборудования;
-Ремонтная документация – не ведется или плохо ведется;
-Отсутствие анализа ремонтов, ППР, ППР по техническому состоянию.
Технический центр ТОиР оборудования с ЧПУ на всем продолжении своей деятельности большое внимание уделял и уделяет инновационным новшествам, инструментам, мероприятиям по усовершенствованию в области ТОиР оборудования и особенно развитию АСУ «ТОиР оборудования с ЧПУ». Под инструментами мы понимаем доски визуализации и коэффициенты показателей эффективности (КПЭ), стенды проблем, благодарностей.
Внедрение управленческих практик:
-Выход в производство (ежедневный линейный обход оборудования), обратная связь, эффективные совещания и прочие мероприятия.
-Разработка и внедрение стендов эффективности для проведения бесед по эффективности работы.
-Конкретное описание благодарностей, проблем, КПЭ участка. Единые правила проведения бесед. Точечная работа с проблемами и последующая эскалация проблем на уровень выше (единые правила).
За последние 30 лет подход к техническому обслуживанию и ремонту оборудования изменился в корне. От аварийного ремонта мы пришли к превентивному с минимумом ремонтных воздействий, с максимумом предупредительных. Оптимизация ТОиР на сегодня требует осознания проблем и поиска решений, регулярного планирования и мониторинга с глубокой модернизацией технического состояния оборудования, системного подхода к организации ТОиР, развития управленческих практик, работы с ремонтной документацией и много другого.
На нижерасположенном рисунке, я показываю схему действующей АСУ «ТОиР оборудования с ЧПУ» в Техническом центре с реализованными основными функциями.
-определял детерминирующие неисправности оборудования по отношению к работоспособности конкретной единицы оборудования, так как воздействие совокупности всех факторов, сопровождающих эксплуатацию оборудования вызывает ускоренное развитие одной или нескольких неисправностей.
Для повышения эффективности и надежности работы оборудования с ЧПУ и решения вышеперечисленных проблем, Технический ТОиР оборудования с ЧПУ в 2002 году приступил к разработке и поэтапному внедрению с последующим совершенствованием АСУ «ТОиР оборудования с ЧПУ». За время существования службы ТОиР оборудования мы прошли следующие этапы применения стратегий управления ТОиР оборудования:
- C 1981 по 2004 годы использовали стратегию ППР.
- С 2005 по 2010 годы использовали стратегию ППР+ППР по техническому состоянию.
- С 2010 по 2013 годы использовали стратегию ППР+ППР по техническому состоянию +ППР на основе возможных рисков.
- С 2014 по настоящее время используем стратегию ППР+ППР по техническому состоянию +ППР на основе возможных рисков +ППР на основе надежности работы оборудования.
В общем случае по разработанному техническому заданию АСУ «ТОиР оборудования с ЧПУ» должна поддерживать решение следующих задач в области управления ТОиР:
-ведение нормативно-справочной информации по оборудованию;
-ведение эксплуатационной и ремонтной документации;
-формирование и ведение базы данных по оборудованию;
-ведение информации о персонале, участвующем в управлении ТОиР;
-оценка и прогнозирование технического состояния оборудования;
-формирование и пересмотр программ технического обслуживания;
-планирование работ по ТОиР;
-определение потребностей в материальных ресурсах;
-обеспечение материально- технических ресурсов;
-выполнение и учет внеплановых работ;
-выполнение и учет плановых работ;
-обеспечение безопасных условий выполнения работ;
-измерение и анализ показателей эффективности;
-принятие решений в отношении списания, замены и модернизации.
В современных условиях, на современных предприятиях машиностроения процессы ТОиР оборудования стали признаваться ключевыми элементами производственного процесса, целями которого являются:
-Минимизировать затраты;
-Увеличить время безотказной работы оборудования;
-Увеличить производительность;
-Работать с финансовыми потерями, так как они часто являются следствием неудовлетворительного планирования, отказа от рассмотрения новых концепций ведения работ или неспособности уделять внимание незначительным изменениям в работе оборудования;
-Развить диагностическое и профилактическое техническое обслуживание;
-Внедрять опыт успешных предприятий;
-Создать программы и проводить обучения для ремонтного персонала;
-Консультировать специалистов 24/7, используя Чат-боты со специальными программами и текстом.
Основные проблемы, которые я вижу в области технического обслуживания и ремонта оборудования на сегодняшний день следующие:
-Система мотивации в области ТОиР отсутствует или несовершенна;
-Инструментальная оснащенность низкая;
-Отсутствие программ передачи опыта;
-Компетенции ремонтного персонала в основном низкая;
-Ключевые показатели эффективности (КПЭ) ремонтной службы составлены без учета производственных служб предприятия;
-Чистое время ремонта на уровне 25% – 40%;
-Отсутствие программы развития ремонтной службы;
-Отсутствие качественного автоматизированного планирования работ по ТОиР оборудования;
-Недоверие некомпетентному руководству служб ТОиР на предприятиях;
-Отсутствие специализированных обучающих классов (для обучения и тренировок);
-Отсутствие автоматического учета наработки оборудования;
-Ремонтная документация – не ведется или плохо ведется;
-Отсутствие анализа ремонтов, ППР, ППР по техническому состоянию.
Технический центр ТОиР оборудования с ЧПУ на всем продолжении своей деятельности большое внимание уделял и уделяет инновационным новшествам, инструментам, мероприятиям по усовершенствованию в области ТОиР оборудования и особенно развитию АСУ «ТОиР оборудования с ЧПУ». Под инструментами мы понимаем доски визуализации и коэффициенты показателей эффективности (КПЭ), стенды проблем, благодарностей.
Внедрение управленческих практик:
-Выход в производство (ежедневный линейный обход оборудования), обратная связь, эффективные совещания и прочие мероприятия.
-Разработка и внедрение стендов эффективности для проведения бесед по эффективности работы.
-Конкретное описание благодарностей, проблем, КПЭ участка. Единые правила проведения бесед. Точечная работа с проблемами и последующая эскалация проблем на уровень выше (единые правила).
За последние 30 лет подход к техническому обслуживанию и ремонту оборудования изменился в корне. От аварийного ремонта мы пришли к превентивному с минимумом ремонтных воздействий, с максимумом предупредительных. Оптимизация ТОиР на сегодня требует осознания проблем и поиска решений, регулярного планирования и мониторинга с глубокой модернизацией технического состояния оборудования, системного подхода к организации ТОиР, развития управленческих практик, работы с ремонтной документацией и много другого.
На нижерасположенном рисунке, я показываю схему действующей АСУ «ТОиР оборудования с ЧПУ» в Техническом центре с реализованными основными функциями.
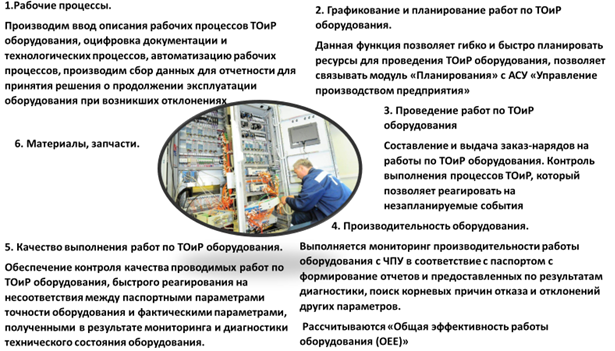
Постоянный переход к новому поколению прикладных технических решений по организации управления ТОиР оборудования стала одной из наиболее актуальной для Технического центра ТОиР и меня, как его руководителя. Технический мир, а особенно станкостроение не стоит на месте, а развивается ускоренными темпами. Технологическая состоятельность и конкурентоспособность предприятий начинает зависеть не только от новизны оборудования и квалификации станочного персонала, но и от рационально организованной службы ТОиР оборудования.
Для эффективной работы службы ТОиР оборудования необходимы АСУ «ТОиР» с прикладными решениями, являющимися главными инструментами повышения эффективности и качества работы оборудования. При проектировании АСУ «ТОиР оборудования с ЧПУ» мы заложили в основу структуры ее следующие типовые процессы ТОиР:
-учет оборудования;
-паспортизация оборудования;
-ведение нормативно-справочной информации по ТОиР;
-мониторинг с глубокой диагностикой технического состояния оборудования;
-формирование бюджета на ТОиР оборудования;
-автоматическое и ручное планирование ТОиР, формирование план-графиков;
-ведение и обработка заявок на внеплановые работы;
-управление материально-техническим обеспечением проводимых ТОиР;
-обеспечение запчастями и материалами;
-поиск поставщиков запчастей и материалов;
-оформление договоров на поставку запчастей, материалов и выполнения работ;
-учет запчастей и материалов на складах Технического центра;
-управление персоналом;
-управление наряд-заказами и работами по ТОиР;
-управление документацией;
-автоматизированный документооборот;
-применение искусственного интеллекта;
-контроль выполнения работ по ТОиР и расходования запчастей;
-анализ фактических затрат на ТОиР, привязанных к каждой единице оборудования;
- автоматизированный анализ эффективности работы службы ТОиР;
-ведение предиктивной аналитики технического состояния оборудования;
-ведение журнала «Контролируемые показатели»;
-средняя продолжительность работ по ТОиР;
-средняя трудоемкость работ по ТОиР;
-средняя стоимость ТОиР;
-коэффициент готовности оборудования;
-автоматизированное формирование отчетов;
-автоматизация процессов ТОиР, связанная с оцифровкой, упрощением и ускорением процессов ТОиР через программное обеспечение с использованием АИС «ДИСПЕТЧЕР».
Кроме вышеперечисленных показателей АСУ « ТОиР оборудования» мониторит следующие финансовые показатели:
-первоначальную стоимость оборудования;
-фактическую стоимость оборудования на данный период времени;
-фактические затраты на ТОиР оборудования;
-степень износа оборудования;
-численность работников ремонтной службы;
-фонд оплаты труда сотрудников ремонтной службы;
-долю затрат на ТОиР оборудования в себестоимости продукции;
-долю плановых и аварийных ремонтов в общем числе ремонтов;
-анализ по количеству, трудоемкости и стоимости плановых и аварийных работ;
-стоимость запасов запчастей и материалов на складах Технического центра;
-точность составления годового бюджета на ТОиР;
-контролирует расход и выполнение бюджета;
-ведет учет затрат на автоматизацию процессов ТОиР оборудования;
-ведет учет затрат на инструмент, измерительные приборы и стенды;
Все вышеуказанные типовые процессы были распределены по модулям.
На нижерасположенном рисунке показана блок-схема основных типовых процессов АСУ «ТОиР оборудования с ЧПУ.
Для эффективной работы службы ТОиР оборудования необходимы АСУ «ТОиР» с прикладными решениями, являющимися главными инструментами повышения эффективности и качества работы оборудования. При проектировании АСУ «ТОиР оборудования с ЧПУ» мы заложили в основу структуры ее следующие типовые процессы ТОиР:
-учет оборудования;
-паспортизация оборудования;
-ведение нормативно-справочной информации по ТОиР;
-мониторинг с глубокой диагностикой технического состояния оборудования;
-формирование бюджета на ТОиР оборудования;
-автоматическое и ручное планирование ТОиР, формирование план-графиков;
-ведение и обработка заявок на внеплановые работы;
-управление материально-техническим обеспечением проводимых ТОиР;
-обеспечение запчастями и материалами;
-поиск поставщиков запчастей и материалов;
-оформление договоров на поставку запчастей, материалов и выполнения работ;
-учет запчастей и материалов на складах Технического центра;
-управление персоналом;
-управление наряд-заказами и работами по ТОиР;
-управление документацией;
-автоматизированный документооборот;
-применение искусственного интеллекта;
-контроль выполнения работ по ТОиР и расходования запчастей;
-анализ фактических затрат на ТОиР, привязанных к каждой единице оборудования;
- автоматизированный анализ эффективности работы службы ТОиР;
-ведение предиктивной аналитики технического состояния оборудования;
-ведение журнала «Контролируемые показатели»;
-средняя продолжительность работ по ТОиР;
-средняя трудоемкость работ по ТОиР;
-средняя стоимость ТОиР;
-коэффициент готовности оборудования;
-автоматизированное формирование отчетов;
-автоматизация процессов ТОиР, связанная с оцифровкой, упрощением и ускорением процессов ТОиР через программное обеспечение с использованием АИС «ДИСПЕТЧЕР».
Кроме вышеперечисленных показателей АСУ « ТОиР оборудования» мониторит следующие финансовые показатели:
-первоначальную стоимость оборудования;
-фактическую стоимость оборудования на данный период времени;
-фактические затраты на ТОиР оборудования;
-степень износа оборудования;
-численность работников ремонтной службы;
-фонд оплаты труда сотрудников ремонтной службы;
-долю затрат на ТОиР оборудования в себестоимости продукции;
-долю плановых и аварийных ремонтов в общем числе ремонтов;
-анализ по количеству, трудоемкости и стоимости плановых и аварийных работ;
-стоимость запасов запчастей и материалов на складах Технического центра;
-точность составления годового бюджета на ТОиР;
-контролирует расход и выполнение бюджета;
-ведет учет затрат на автоматизацию процессов ТОиР оборудования;
-ведет учет затрат на инструмент, измерительные приборы и стенды;
Все вышеуказанные типовые процессы были распределены по модулям.
На нижерасположенном рисунке показана блок-схема основных типовых процессов АСУ «ТОиР оборудования с ЧПУ.

На нижерасположенном рисунке представлен Алгоритм реализации упреждающей концепции ТОиР оборудования:
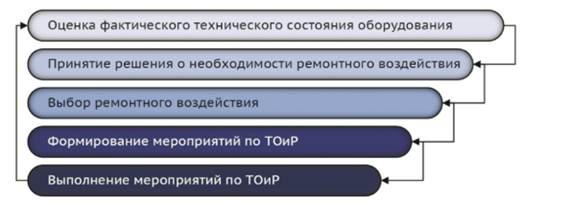
В период с 1981 по 1994 годы капитальный ремонт оборудования с ЧПУ на предприятиях машиностроения проводился через каждые 26400 часов его работы (примерно через 13 лет). При этом было замечено растущее число отказов к концу этого межремонтного периода. Поэтому мы сделали вывод, что техническое обслуживание и ремонт в период окончания ремонтного цикла нужно проводить через меньший интервал времени, не допуская массовых отказов оборудования. Время между ремонтами в конце ремонтного цикла было сокращено.
Но увеличение количества профилактических мероприятий имело три очень неожиданных результата. Результаты, которые в конечном итоге перевернули мир ТОиР с ног на голову.
Прежде всего, возникновение некоторых типов отказов, действительно, уменьшилось. Это было именно то, чего все ожидали.
Второй результат состоял в том, что большое количество сбоев происходило так же часто, как и раньше. Этого не ожидалось и немного сбило нас с толку.
Третьим результатом было то, что большинство отказов стало происходить чаще. Другими словами, увеличение мероприятий по техническому обслуживанию и ремонту привело к увеличению числа отказов. Это было нелогично, и это был шок для нас.
Оказалось, что только 23% отказов соответствует представлению, о том, что интенсивность отказов растет с наработкой оборудования. Эти отказы свойственны для относительно простого оборудования.
Что же касается технически сложного оборудования, выяснилось, что между вероятностью их отказа и сроком эксплуатации нет или почти нет взаимосвязи. А это 77% отказов. Для этого оборудования интенсивность отказа находится за пределами интервала приработки и имеет постоянную величину, не изменяющуюся с наработкой оборудования.
Но увеличение количества профилактических мероприятий имело три очень неожиданных результата. Результаты, которые в конечном итоге перевернули мир ТОиР с ног на голову.
Прежде всего, возникновение некоторых типов отказов, действительно, уменьшилось. Это было именно то, чего все ожидали.
Второй результат состоял в том, что большое количество сбоев происходило так же часто, как и раньше. Этого не ожидалось и немного сбило нас с толку.
Третьим результатом было то, что большинство отказов стало происходить чаще. Другими словами, увеличение мероприятий по техническому обслуживанию и ремонту привело к увеличению числа отказов. Это было нелогично, и это был шок для нас.
Оказалось, что только 23% отказов соответствует представлению, о том, что интенсивность отказов растет с наработкой оборудования. Эти отказы свойственны для относительно простого оборудования.
Что же касается технически сложного оборудования, выяснилось, что между вероятностью их отказа и сроком эксплуатации нет или почти нет взаимосвязи. А это 77% отказов. Для этого оборудования интенсивность отказа находится за пределами интервала приработки и имеет постоянную величину, не изменяющуюся с наработкой оборудования.
На нижерасположенном рисунке показана тактика выполнения работ по ТОиР оборудования и паттерны имеющихся отказов.
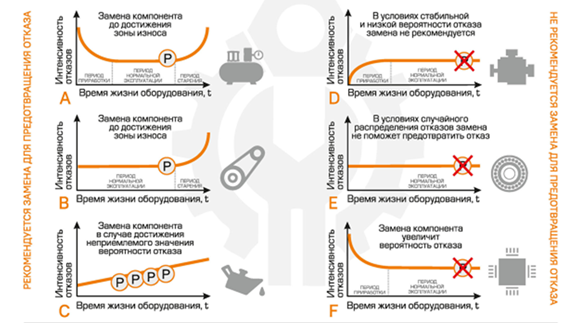
На данном рисунке показаны самые известные диаграммы, называемые U-образными кривыми интенсивности отказов. Здесь выделяется три основные зоны слева направо.
Первая — это период приработки с высокой вероятностью отказа. Кривая идёт на снижение до тех пор, пока не станет стабильной. Такой отказ называется выходом из строя в начальный период эксплуатации и означает, что каждый новый установленный компонент изначально подвержен высокому риску отказа («Синдром детской смертности»).
Вторая зона — это период нормальной эксплуатации со стабильно низкой вероятностью отказа.
Третья зона — зона износа оборудования. Исходя из информации на графике, можно сделать вывод, что замена компонента до достижения зоны износа уменьшит вероятность отказа. Однако необходимо учитывать, что несмотря ни на что, сохраняется высокий риск выхода из строя оборудования в период приработки.
Этот график похож на вариант А, но он не имеет зоны отказов в приработочном периоде. Иногда отсутствие такой зоны является характеристикой оборудования, производитель которого заранее исключил компоненты с дефектами, возникающими на начальном этапе эксплуатации. Такой процесс известен как «испытание на отказы».
Как и в графике А, замена компонента до зоны износа является лучшим способом снизить вероятность отказа, и в этом случае не учитывается возможность потенциального отказа в приработочный период.
На графике С видно, что условная вероятность отказа увеличивается прямо пропорционально сроку жизни оборудования.
Здесь нельзя идентифицировать определённую зону износа, поэтому нет оптимального срока замены компонента. Теоретически можно произвести замену, когда вероятность отказа достигнет определённого значения, не являющегося приемлемым в каждой конкретной ситуации.
На графике D присутствует низкая вероятность отказа в начале жизненного цикла оборудования, которая впоследствии увеличивается до приемлемого уровня и остаётся постоянной в течение дальнейшего срока эксплуатации. Стоит отметить, что эта зона с условно стабильной вероятностью отказа доказывает нам, что зачастую отказы происходят случайно.
В этом случае замена компонента не принесёт никакой пользы, исключая период низкой вероятности отказа в начале эксплуатации, что на самом деле незначительно в сравнении с остальным сроком службы оборудования.
На рисунке F продемонстрирована стабильная вероятность отказа в течение всего жизненного срока оборудования. В RCM такой график называется случайным распределением отказов.
Здесь замена компонента не поможет уменьшить вероятность наступления отказа.
Показывает случайные неисправности, вероятность, которых высока в зоне износа, но с течением времени она снижается.
В этом случае замена компонента не только не принесет никакой пользы, но и увеличит вероятность отказа, потому что изначально оборудование вошло в эксплуатацию с высокой вероятностью отказов на приработанном этапе.
Из вышесказанного следует, что для 70% оборудования, которое имеет постоянную вероятность выхода из строя, нет смысла выполнять основанные на времени задачи по продлению срока службы, такие как обслуживание или замена.
Нет смысла тратить ресурсы для обслуживания или замены узла или компонента, надежность которого не снизилась, или чья надежность не может быть улучшена этой задачей обслуживания.
На практике это означает, что 70% - 90% оборудования выиграют от какой-либо формы мониторинга технического состояния оборудования. И только 10% - 30% могут эффективно управляться заменой или капитальным ремонтом по времени.
На этом я заканчиваю очередную часть статьи из цикла АСУ «ТОиР оборудования с ЧПУ». Ждите продолжения.
Первая — это период приработки с высокой вероятностью отказа. Кривая идёт на снижение до тех пор, пока не станет стабильной. Такой отказ называется выходом из строя в начальный период эксплуатации и означает, что каждый новый установленный компонент изначально подвержен высокому риску отказа («Синдром детской смертности»).
Вторая зона — это период нормальной эксплуатации со стабильно низкой вероятностью отказа.
Третья зона — зона износа оборудования. Исходя из информации на графике, можно сделать вывод, что замена компонента до достижения зоны износа уменьшит вероятность отказа. Однако необходимо учитывать, что несмотря ни на что, сохраняется высокий риск выхода из строя оборудования в период приработки.
Этот график похож на вариант А, но он не имеет зоны отказов в приработочном периоде. Иногда отсутствие такой зоны является характеристикой оборудования, производитель которого заранее исключил компоненты с дефектами, возникающими на начальном этапе эксплуатации. Такой процесс известен как «испытание на отказы».
Как и в графике А, замена компонента до зоны износа является лучшим способом снизить вероятность отказа, и в этом случае не учитывается возможность потенциального отказа в приработочный период.
На графике С видно, что условная вероятность отказа увеличивается прямо пропорционально сроку жизни оборудования.
Здесь нельзя идентифицировать определённую зону износа, поэтому нет оптимального срока замены компонента. Теоретически можно произвести замену, когда вероятность отказа достигнет определённого значения, не являющегося приемлемым в каждой конкретной ситуации.
На графике D присутствует низкая вероятность отказа в начале жизненного цикла оборудования, которая впоследствии увеличивается до приемлемого уровня и остаётся постоянной в течение дальнейшего срока эксплуатации. Стоит отметить, что эта зона с условно стабильной вероятностью отказа доказывает нам, что зачастую отказы происходят случайно.
В этом случае замена компонента не принесёт никакой пользы, исключая период низкой вероятности отказа в начале эксплуатации, что на самом деле незначительно в сравнении с остальным сроком службы оборудования.
На рисунке F продемонстрирована стабильная вероятность отказа в течение всего жизненного срока оборудования. В RCM такой график называется случайным распределением отказов.
Здесь замена компонента не поможет уменьшить вероятность наступления отказа.
Показывает случайные неисправности, вероятность, которых высока в зоне износа, но с течением времени она снижается.
В этом случае замена компонента не только не принесет никакой пользы, но и увеличит вероятность отказа, потому что изначально оборудование вошло в эксплуатацию с высокой вероятностью отказов на приработанном этапе.
Из вышесказанного следует, что для 70% оборудования, которое имеет постоянную вероятность выхода из строя, нет смысла выполнять основанные на времени задачи по продлению срока службы, такие как обслуживание или замена.
Нет смысла тратить ресурсы для обслуживания или замены узла или компонента, надежность которого не снизилась, или чья надежность не может быть улучшена этой задачей обслуживания.
На практике это означает, что 70% - 90% оборудования выиграют от какой-либо формы мониторинга технического состояния оборудования. И только 10% - 30% могут эффективно управляться заменой или капитальным ремонтом по времени.
На этом я заканчиваю очередную часть статьи из цикла АСУ «ТОиР оборудования с ЧПУ». Ждите продолжения.