Доброго времени суток, уважаемые коллеги и друзья!
Поздравляю Вас с приближающимся началом работы выставки «Металлообработка-2023» и приглашаю принять участие в конференции на тему «Что выгоднее: отремонтировать металлообрабатывающий станок или купить новый? Рекомендации экспертов». Конференция состоится 23 мая 2023 года с 11 до 15 часов в павильоне №1, зал Д2. Организатор - ООО «Станки-Экспо», при поддержке АО «Экспоцентр».
В данной статье я остановлюсь на организации работ по повышению эффективности и надежности работы оборудования с ЧПУ на предприятиях ВПК в условиях продолжающейся СВО на Украине за счет правильно организованных работ по ТОиР и капитального ремонта с глубокой модернизацией.
Предприятия машиностроения заинтересованы в том, чтобы пользоваться самым современным оборудованием. Но, вместе с тем, покупка нового оборудования — это большие денежные затраты, которые не всегда оправданы. Кроме того, в настоящее время из-за санкций стало невозможно приобрести многокоординатные станки с ЧПУ. Отечественное станкостроение в настоящее время и в ближайшие 5 лет не имеет возможности его изготовить. Кроме финансовой нагрузки, покупка нового оборудования — это проблемы с транспортировкой, которая может занимать продолжительное время, а также с переобучением операторов, технологов, ремонтного персонала. Выход из создавшегося положения, конечно, есть. Это качественный инновационный капитальный ремонт с глубокой модернизацией станков с ЧПУ, на протяжении 10 лет, пока не восстановится отечественное станкостроение, если оно восстановится. При этом не только тратится значительно меньше средств, но и освоение, и сам капитальный ремонт с глубокой модернизацией проходят гораздо быстрее за счет четкого планирования и четкой организации изготовления и приобретения комплектующих изделий.
Этапы работы
Технический центр ТОиР оборудования с ЧПУ проводил капитальный ремонт с глубокой модернизацией станков с ЧПУ по следующим этапам:
За короткое время Технический центр осовременил более 150 разнообразных станков с ЧПУ.
Производство, получив вышеуказанное количество обновленных станков с ЧПУ, обновило станочный парк, который стал как более производительным,так и максимально современным с минимальными денежными и временными затратами.
Капитальный ремонт с глубокой модернизацией станков: общий обзор
Мировой рынок капитального ремонта с глубокой модернизацией станков с ЧПУ постоянно расширяется. Его объем достигает уже нескольких миллиардов долларов в год, и такая тенденция будет продолжаться.
Многие предприятия, особенно предприятия ВПК, заинтересованы в том, чтобы путем небольших инвестиций провести капитальный ремонт с глубокой модернизацией имеющегося оборудования. Эта тенденция пришла в Россию из развитых зарубежных стран. Ведь приобретение станков, особенно крупногабаритных, требует довольно больших затрат. А в условиях, когда такое оборудование,как например координатные, расточные, карусельные, шлифовальные станки, не всегда имеет постоянную загрузку, вложение в приобретение новых станков не будет оправданным. Такое оборудование выгоднее капитально ремонтировать с глубокой модернизацией.
Кроме того, следует учитывать, что приобретение нового станка несет за собой дополнительные вложения, связанные с изготовлением и поставкой. Немаловажен и тот факт, что эта процедура занимает от 6 до 9 месяцев, а в некоторых случаях и до 1,5 лет. Следует также отметить, что модернизация ранее находившегося в эксплуатации станка облегчает «привыкание» оператора, что существенно сокращает срок освоения.
Так в чем же заключается технология проведения капитального ремонте с глубокой модернизацией оборудования с ЧПУ, а также какие общие технологические этапы встречаются при выполнении этого процесса?
Очень важно сделать правильный выбор метода усовершенствования станка — капитальный ремонт с глубокой модернизацией,капитальный ремонт, модернизация станка или, наконец, ремонт с частичной модернизацией. Хотя эти процессы во многом схожи, однако существуют значительные различия.
При капитальном ремонте с глубокой модернизацией проводят полный капитальный ремонт всей механики станка с полной заменой механических элементов и установкой современных более технологических узлов. Производится полная замена систем ЧПУ, привода главного движения, приводов подач, измерительной системы, всей низковольтной аппаратуры и т.д.
При модернизации обычно устанавливают новое ЧПУ или заменяют существующее на более современное, а вместе с ним устанавливают новые современные серводвигатели, приводы главного движения и подач, электроавтоматику (пускатели, выключатели, реле), которые в модернизированных станках занимают гораздо меньше места, чем старые. И полностью перемонтируют электрическую проводку станка, что позволяет перевести его на новые правила электробезопасности.
Необходимо также иметь в виду возможность связи привязанного к станку ЧПУ с центральным сервером предприятия и технического центра ТОиР, на котором происходит централизованное написание программ для каждого конкретного, в том числе капитально отремонтированного с глубокой модернизацией станка.
Эта возможность позволяет не только сконцентрировать в одном месте написание программ, но и осуществлять высокоскоростную передачу созданного программного продукта к рабочему станку, а также одновременно с необходимой периодичностью проводить мониторинг с глубокой диагностикой технического состояния узлов станка с ЧПУ, тем самым помогая оператору, программисту и обслуживающему персоналу своевременно выявлять проблемы, связанные с инструментом, ошибками программирования или сбоями в станке по техническим причинам.
На капитально отремонтированные с глубокой модернизацией станки теперь устанавливают в основном бесщеточные двигатели переменного тока, имеющие оптимальное соотношение между мощностью, размерами и практически не требующие технического обслуживания.
В настоящее время в некоторых специализированных системах ЧПУ для повышения их уровня и производительности используют одновременно серводвигатели и приводы. Связь между приводом и ЧПУ обычно осуществляется через серийные или оптоволоконные средства коммуникации.
Стоимость модернизации станка составляет ориентировочно 20-50% от цены нового. Типовую модернизацию станка, включая его систему управления, серводвигатели и приводы главного движения, проводят за 4-8 недель. Однако, следует учесть, что необходимо закладывать в срок проведения работ дополнительно от 2 до 3 месяцев на закупку и доставку необходимых комплектующих узлов.
Разумеется, после проведения любой из вышеуказанных операций необходимо наличие полной и достоверной документации на станок , которая имеет большое значение для его успешной эксплуатации. Как минимум, она должна содержать полную принципиальную электрическую схему, схему входных и выходных соединений, схему электрического монтажа сервоприводов и главного привода (включая все контактные штыри на штепсельных вилках), чертежи и схемы станка и руководство по эксплуатации.
В контракте на проведение капитального ремонта или модернизации следует оговорить передачу заказчику модели узлов и станка в целом, перечня всех доработанных деталей, принципиальных электрической и электронных схем с описанием программного обеспечения, описания ЧПУ, в том числе системы диагностики.
Хотя количество заказов на ремонт и модернизацию станков постоянно растет, возможности их исполнения в значительной степени ограничены в первую очередь дефицитом комплектующих и квалифицированных специалистов, выполняющих ручные операции по доводке узлов, по разработке программ электроавтоматики станка и привязке их к системе ЧПУ, замене двигателей и приводов.
В целом нужно сказать, что проведение комплексного капитального ремонта с глубокой модернизацией станков, безусловно, создает оптимальные условия для дальнейшего развития инфраструктуры производства, позволяя выпускать более современную и качественную продукцию.
В свою очередь, модернизация станков направлена на расширение и улучшение функциональных свойств, на повышение эксплуатационной надежности. На практике станочный парк имеет относительно хорошую ремонтопригодную механическую часть, но имеет морально устаревшие систему ЧПУ и приводы. В этом случае необходима модернизация станка. Не редки случаи, когда модернизации подвергается исправный станок, но не удовлетворяющий требованиям точности, надежности и функциональности.
А теперь давайте перейдем непосредственно к теме статьи и рассмотрим выполненный Техническим центром ТОиР оборудования с ЧПУ капитальный ремонт с глубокой модернизацией специального продольно-фрезерно-сверлильного станка с ЧПУ модели СФП-13.
Пятиосевой специальный фрезерный станок с наклонной шпиндельной бабкой модели СФП 13, 1978 года выпуска был оснащен устаревшей цикловой системой ЧПУ «СЦП-5» с цифровой индикацией. С помощью устройства матричной логики программировалась работа вспомогательных устройств электроавтоматики. На станке было установлено четыре шкафа электроавтоматики (шкаф управления шпинделем, 2 шкафа управления приводами подач, шкаф электроавтоматики), которые занимали очень много места, а оборудование, которое было скомпоновано в них, физически и морально устарело. На станке была установлена поворотная шпиндельная бабка.
Поздравляю Вас с приближающимся началом работы выставки «Металлообработка-2023» и приглашаю принять участие в конференции на тему «Что выгоднее: отремонтировать металлообрабатывающий станок или купить новый? Рекомендации экспертов». Конференция состоится 23 мая 2023 года с 11 до 15 часов в павильоне №1, зал Д2. Организатор - ООО «Станки-Экспо», при поддержке АО «Экспоцентр».
В данной статье я остановлюсь на организации работ по повышению эффективности и надежности работы оборудования с ЧПУ на предприятиях ВПК в условиях продолжающейся СВО на Украине за счет правильно организованных работ по ТОиР и капитального ремонта с глубокой модернизацией.
Предприятия машиностроения заинтересованы в том, чтобы пользоваться самым современным оборудованием. Но, вместе с тем, покупка нового оборудования — это большие денежные затраты, которые не всегда оправданы. Кроме того, в настоящее время из-за санкций стало невозможно приобрести многокоординатные станки с ЧПУ. Отечественное станкостроение в настоящее время и в ближайшие 5 лет не имеет возможности его изготовить. Кроме финансовой нагрузки, покупка нового оборудования — это проблемы с транспортировкой, которая может занимать продолжительное время, а также с переобучением операторов, технологов, ремонтного персонала. Выход из создавшегося положения, конечно, есть. Это качественный инновационный капитальный ремонт с глубокой модернизацией станков с ЧПУ, на протяжении 10 лет, пока не восстановится отечественное станкостроение, если оно восстановится. При этом не только тратится значительно меньше средств, но и освоение, и сам капитальный ремонт с глубокой модернизацией проходят гораздо быстрее за счет четкого планирования и четкой организации изготовления и приобретения комплектующих изделий.
Этапы работы
Технический центр ТОиР оборудования с ЧПУ проводил капитальный ремонт с глубокой модернизацией станков с ЧПУ по следующим этапам:
- Разработка документации, технического задания, разработка проекта, выполнение работ, составление ведомости покупных узлов и деталей.
- Демонтаж старой системы ЧПУ, электрической проводки, двигателей и приводов, с последующей установкой новых.
- Программирование системы ЧПУ и настройка приводов.
- Подготовка тест-программ.
- Устранение недостатков.
- Сдача станка.
За короткое время Технический центр осовременил более 150 разнообразных станков с ЧПУ.
Производство, получив вышеуказанное количество обновленных станков с ЧПУ, обновило станочный парк, который стал как более производительным,так и максимально современным с минимальными денежными и временными затратами.
Капитальный ремонт с глубокой модернизацией станков: общий обзор
Мировой рынок капитального ремонта с глубокой модернизацией станков с ЧПУ постоянно расширяется. Его объем достигает уже нескольких миллиардов долларов в год, и такая тенденция будет продолжаться.
Многие предприятия, особенно предприятия ВПК, заинтересованы в том, чтобы путем небольших инвестиций провести капитальный ремонт с глубокой модернизацией имеющегося оборудования. Эта тенденция пришла в Россию из развитых зарубежных стран. Ведь приобретение станков, особенно крупногабаритных, требует довольно больших затрат. А в условиях, когда такое оборудование,как например координатные, расточные, карусельные, шлифовальные станки, не всегда имеет постоянную загрузку, вложение в приобретение новых станков не будет оправданным. Такое оборудование выгоднее капитально ремонтировать с глубокой модернизацией.
Кроме того, следует учитывать, что приобретение нового станка несет за собой дополнительные вложения, связанные с изготовлением и поставкой. Немаловажен и тот факт, что эта процедура занимает от 6 до 9 месяцев, а в некоторых случаях и до 1,5 лет. Следует также отметить, что модернизация ранее находившегося в эксплуатации станка облегчает «привыкание» оператора, что существенно сокращает срок освоения.
Так в чем же заключается технология проведения капитального ремонте с глубокой модернизацией оборудования с ЧПУ, а также какие общие технологические этапы встречаются при выполнении этого процесса?
Очень важно сделать правильный выбор метода усовершенствования станка — капитальный ремонт с глубокой модернизацией,капитальный ремонт, модернизация станка или, наконец, ремонт с частичной модернизацией. Хотя эти процессы во многом схожи, однако существуют значительные различия.
При капитальном ремонте с глубокой модернизацией проводят полный капитальный ремонт всей механики станка с полной заменой механических элементов и установкой современных более технологических узлов. Производится полная замена систем ЧПУ, привода главного движения, приводов подач, измерительной системы, всей низковольтной аппаратуры и т.д.
При модернизации обычно устанавливают новое ЧПУ или заменяют существующее на более современное, а вместе с ним устанавливают новые современные серводвигатели, приводы главного движения и подач, электроавтоматику (пускатели, выключатели, реле), которые в модернизированных станках занимают гораздо меньше места, чем старые. И полностью перемонтируют электрическую проводку станка, что позволяет перевести его на новые правила электробезопасности.
Необходимо также иметь в виду возможность связи привязанного к станку ЧПУ с центральным сервером предприятия и технического центра ТОиР, на котором происходит централизованное написание программ для каждого конкретного, в том числе капитально отремонтированного с глубокой модернизацией станка.
Эта возможность позволяет не только сконцентрировать в одном месте написание программ, но и осуществлять высокоскоростную передачу созданного программного продукта к рабочему станку, а также одновременно с необходимой периодичностью проводить мониторинг с глубокой диагностикой технического состояния узлов станка с ЧПУ, тем самым помогая оператору, программисту и обслуживающему персоналу своевременно выявлять проблемы, связанные с инструментом, ошибками программирования или сбоями в станке по техническим причинам.
На капитально отремонтированные с глубокой модернизацией станки теперь устанавливают в основном бесщеточные двигатели переменного тока, имеющие оптимальное соотношение между мощностью, размерами и практически не требующие технического обслуживания.
В настоящее время в некоторых специализированных системах ЧПУ для повышения их уровня и производительности используют одновременно серводвигатели и приводы. Связь между приводом и ЧПУ обычно осуществляется через серийные или оптоволоконные средства коммуникации.
Стоимость модернизации станка составляет ориентировочно 20-50% от цены нового. Типовую модернизацию станка, включая его систему управления, серводвигатели и приводы главного движения, проводят за 4-8 недель. Однако, следует учесть, что необходимо закладывать в срок проведения работ дополнительно от 2 до 3 месяцев на закупку и доставку необходимых комплектующих узлов.
Разумеется, после проведения любой из вышеуказанных операций необходимо наличие полной и достоверной документации на станок , которая имеет большое значение для его успешной эксплуатации. Как минимум, она должна содержать полную принципиальную электрическую схему, схему входных и выходных соединений, схему электрического монтажа сервоприводов и главного привода (включая все контактные штыри на штепсельных вилках), чертежи и схемы станка и руководство по эксплуатации.
В контракте на проведение капитального ремонта или модернизации следует оговорить передачу заказчику модели узлов и станка в целом, перечня всех доработанных деталей, принципиальных электрической и электронных схем с описанием программного обеспечения, описания ЧПУ, в том числе системы диагностики.
Хотя количество заказов на ремонт и модернизацию станков постоянно растет, возможности их исполнения в значительной степени ограничены в первую очередь дефицитом комплектующих и квалифицированных специалистов, выполняющих ручные операции по доводке узлов, по разработке программ электроавтоматики станка и привязке их к системе ЧПУ, замене двигателей и приводов.
В целом нужно сказать, что проведение комплексного капитального ремонта с глубокой модернизацией станков, безусловно, создает оптимальные условия для дальнейшего развития инфраструктуры производства, позволяя выпускать более современную и качественную продукцию.
В свою очередь, модернизация станков направлена на расширение и улучшение функциональных свойств, на повышение эксплуатационной надежности. На практике станочный парк имеет относительно хорошую ремонтопригодную механическую часть, но имеет морально устаревшие систему ЧПУ и приводы. В этом случае необходима модернизация станка. Не редки случаи, когда модернизации подвергается исправный станок, но не удовлетворяющий требованиям точности, надежности и функциональности.
А теперь давайте перейдем непосредственно к теме статьи и рассмотрим выполненный Техническим центром ТОиР оборудования с ЧПУ капитальный ремонт с глубокой модернизацией специального продольно-фрезерно-сверлильного станка с ЧПУ модели СФП-13.
Пятиосевой специальный фрезерный станок с наклонной шпиндельной бабкой модели СФП 13, 1978 года выпуска был оснащен устаревшей цикловой системой ЧПУ «СЦП-5» с цифровой индикацией. С помощью устройства матричной логики программировалась работа вспомогательных устройств электроавтоматики. На станке было установлено четыре шкафа электроавтоматики (шкаф управления шпинделем, 2 шкафа управления приводами подач, шкаф электроавтоматики), которые занимали очень много места, а оборудование, которое было скомпоновано в них, физически и морально устарело. На станке была установлена поворотная шпиндельная бабка.
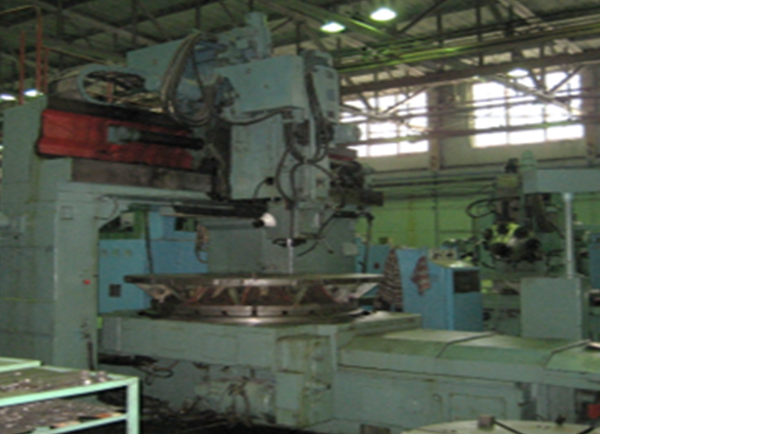
При проведении работ по капитальному ремонту с глубокой модернизацией данного станка Технический центр применил следующую последовательность работ:
1. КОНСТРУКТОРСКО-ТЕХНОЛОГИЧЕСКАЯ ЧАСТЬ ПРОЕКТА
1.1. Проработали техническое задание на капитальный ремонт с глубокой модернизацией станка с ЧПУ модели СФП-13 совместно с специалистами служб главного технолога и производства.
1.2. Разработали эскизный проект капитально отремонтированного с глубокой модернизацией станка в новом виде и с новыми возможностями в виде 3Д-модели, показанной на нижерасположенном рисунке.
1. КОНСТРУКТОРСКО-ТЕХНОЛОГИЧЕСКАЯ ЧАСТЬ ПРОЕКТА
1.1. Проработали техническое задание на капитальный ремонт с глубокой модернизацией станка с ЧПУ модели СФП-13 совместно с специалистами служб главного технолога и производства.
1.2. Разработали эскизный проект капитально отремонтированного с глубокой модернизацией станка в новом виде и с новыми возможностями в виде 3Д-модели, показанной на нижерасположенном рисунке.
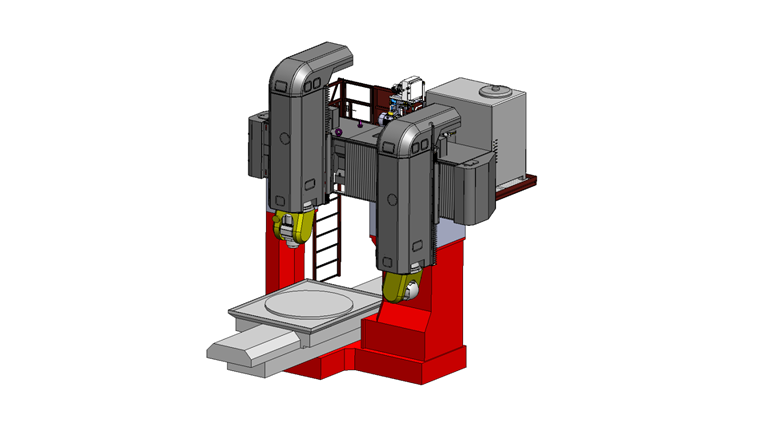
1.3. На основе эскизного проекта и технического задания были разработаны конструкторская документация и проект капитального ремонта с глубокой модернизацией станка модели СФП-13. Модель будущего станка показана на нижерасположенном рисунке.
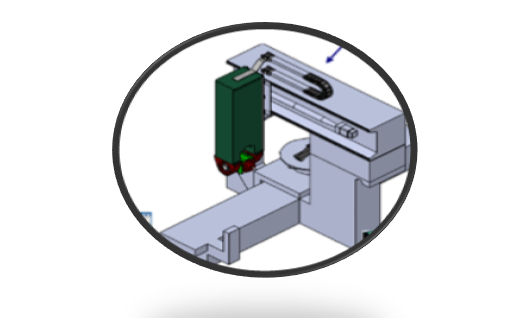
1.4. На основании технического задания фирма Hage (Австрия) разработала проект траверсы со шпиндельной бабкой, оснащенной мотор-шпинделем производства фирмы Ibag c 2-осевой фрезерной головкой.
1.4.1. Траверса Y
-Стабильная, рассчитанная с применением метода конечных элементов сварная конструкция , из закалённой стали и соответствующим образом обработанная, с минимальными остаточными напряжениями, лакированная. Конструкция траверсы предусматривает компенсацию разницы высоты колонн станка (около 500 мм).
Чертеж сварной конструкции траверсы показан на нижерасположенном рисунке.
1.4.1. Траверса Y
-Стабильная, рассчитанная с применением метода конечных элементов сварная конструкция , из закалённой стали и соответствующим образом обработанная, с минимальными остаточными напряжениями, лакированная. Конструкция траверсы предусматривает компенсацию разницы высоты колонн станка (около 500 мм).
Чертеж сварной конструкции траверсы показан на нижерасположенном рисунке.
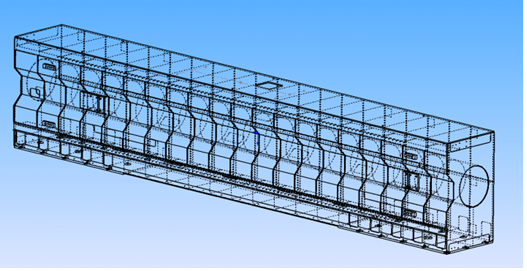
На траверсе установлены:
Для установки шпиндельной бабки была изготовлена стабильная фланцевая плита, рассчитанная с применением метода конечных элементов сварная конструкция, из закалённой стали и соответствующим образом обработанная, с минимальными остаточными напряжениями, лакированная. Чертеж плиты показан на нижерасположенном рисунке.
- направляющие с монтажным профилем из закалённой стали с интегрированной системой измерения перемещений,
- сам привод (сервомотор с планетарной передачей и ШВП),
- направляющая плита для установки шпиндельной бабки (ось Z),
- в качестве внешней измерительной системы была применена стеклянная масштабная линейка производства фирмы Heidenhain,
- конечные и аварийные выключатели,
- кабелеукладчик,
- разводка кабелей, соединенная в шинной коробке.
Для установки шпиндельной бабки была изготовлена стабильная фланцевая плита, рассчитанная с применением метода конечных элементов сварная конструкция, из закалённой стали и соответствующим образом обработанная, с минимальными остаточными напряжениями, лакированная. Чертеж плиты показан на нижерасположенном рисунке.
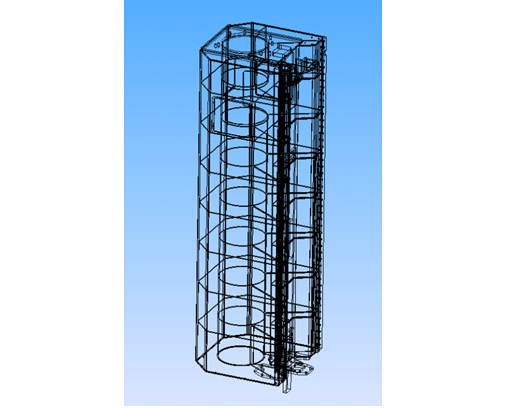
1.4.2. Шпиндельная бабка.
-Стабильная, рассчитанная с применением метода конечных элементов конструкция c монтажными плоскостями с крепёжной резьбой, соответствующим образом обработанная, с минимальными остаточными напряжениями, лакированная.
-Привод - циклоидная передача с зубчатым ремнём и сервомотором Siemens.
-Прецизионные перекрёстно-роликовые подшипники с преднатягом.
-Интегрированные кабелеукладчики.
-Защитный чехол.
-Все кабели и шланги к шпинделю съёмные, длина 15 м.
-Мотор-шпиндель типа HF260 производства фирмы IBAG.
-Система охлаждения шпинделя производства фирмы Etscheid.
-Стабильная, рассчитанная с применением метода конечных элементов конструкция c монтажными плоскостями с крепёжной резьбой, соответствующим образом обработанная, с минимальными остаточными напряжениями, лакированная.
-Привод - циклоидная передача с зубчатым ремнём и сервомотором Siemens.
-Прецизионные перекрёстно-роликовые подшипники с преднатягом.
-Интегрированные кабелеукладчики.
-Защитный чехол.
-Все кабели и шланги к шпинделю съёмные, длина 15 м.
-Мотор-шпиндель типа HF260 производства фирмы IBAG.
-Система охлаждения шпинделя производства фирмы Etscheid.
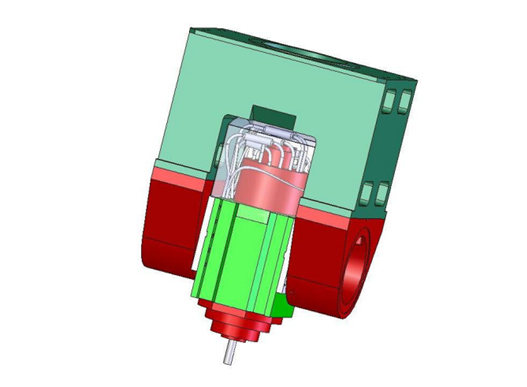
1.4.3. Центральная система смазки
- Центральная смазка каретки, зубчатых передач и гайки ходового винта.
- Распределитель смазки и дозирующие элементы.
- Считывание величины давления (мин. – макс.).
- Насос с запасным резервуаром около 4 л..
1.4.4. Гидравлика
-Гидравлический агрегат для разжима инструмента в шпинделе и поворотного стола.
-Наблюдение уровня наполнения.
-Наблюдение температуры.
-Наблюдение за чистотой фильтров.
1.4.5. Пневматика
-Пневматический шкаф.
-Клапан для обдува конуса шпинделя.
-Прецизионный регулирующий клапан для запирающего воздуха (воздушного уплотнения) внешней измерительной системы.
-Пневмоблок.
-Комбинация фильтров для запирающего воздуха.
1.5. На основании разработанного проекта составили ведомости покупных изделий, узлов, агрегатов и комплектующих.
1.6. На основании разработанного проекта изготовили техническую документацию на изготовление в цехах основного производства деталей и узлов.
1.7. Разработали технологический процесс проведения капитального ремонта с глубокой модернизацией станка модели СФП-13.
- Центральная смазка каретки, зубчатых передач и гайки ходового винта.
- Распределитель смазки и дозирующие элементы.
- Считывание величины давления (мин. – макс.).
- Насос с запасным резервуаром около 4 л..
1.4.4. Гидравлика
-Гидравлический агрегат для разжима инструмента в шпинделе и поворотного стола.
-Наблюдение уровня наполнения.
-Наблюдение температуры.
-Наблюдение за чистотой фильтров.
1.4.5. Пневматика
-Пневматический шкаф.
-Клапан для обдува конуса шпинделя.
-Прецизионный регулирующий клапан для запирающего воздуха (воздушного уплотнения) внешней измерительной системы.
-Пневмоблок.
-Комбинация фильтров для запирающего воздуха.
1.5. На основании разработанного проекта составили ведомости покупных изделий, узлов, агрегатов и комплектующих.
1.6. На основании разработанного проекта изготовили техническую документацию на изготовление в цехах основного производства деталей и узлов.
1.7. Разработали технологический процесс проведения капитального ремонта с глубокой модернизацией станка модели СФП-13.
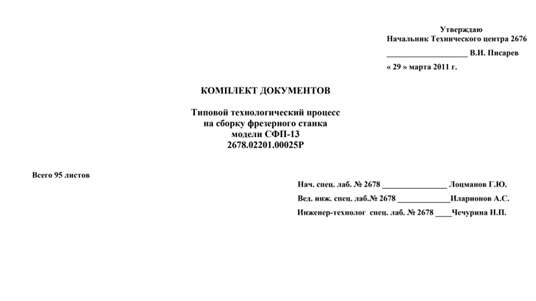
1.8. Определились с фирмой-изготовителем траверсы с шпиндельной бабкой и мотор-шпинделем по предоставленным ими проектам, согласно техническому заданию.
1.9. Разработали проект доработки металлического креста для обеспечения жесткости между станиной и стойками станка.
1.10. Определились с моделью и фирмой-изготовителем магазина инструментов на 60 мест.
2.Выполнение работ по капитальному ремонту продольно кругового стола станка модели СФП-13:
2.1. Произвели диагностику технического состояния узлов и деталей продольно-кругового стола станка.
2.2. Произвели демонтаж узлов и деталей стола станка.
2..3. Произвели дефектацию узлов и деталей кругового и продольного столов станка.
2.4. Произвели доработку металлического креста для обеспечения жесткости между станиной и стойками станка, согласно чертежу,показанному на нижерасположенной картинке.
1.9. Разработали проект доработки металлического креста для обеспечения жесткости между станиной и стойками станка.
1.10. Определились с моделью и фирмой-изготовителем магазина инструментов на 60 мест.
2.Выполнение работ по капитальному ремонту продольно кругового стола станка модели СФП-13:
2.1. Произвели диагностику технического состояния узлов и деталей продольно-кругового стола станка.
2.2. Произвели демонтаж узлов и деталей стола станка.
2..3. Произвели дефектацию узлов и деталей кругового и продольного столов станка.
2.4. Произвели доработку металлического креста для обеспечения жесткости между станиной и стойками станка, согласно чертежу,показанному на нижерасположенной картинке.
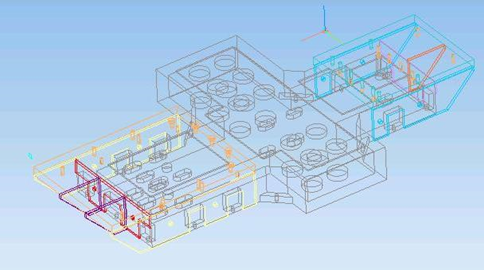
2.5. Механические узлы и детали очистили от грязи и ржавчины, промыли, проверили их функциональное состояние и затем собрали вновь, используя новые или старые, повторно обработанные детали.
2.6. Направляющие скольжения очистили от ржавчины, тщательно осмотрели на предмет обнаружения задиров и проверили твердость. Твердость составила 50 HRC на глубину 0,23-3,2 мм. Глубина задиров и
царапин превышала 1,25 мм).
2.7. Данные направляющие были перешлифованы на плоскошлифовальном станке Coburg с получением плоскостности 5 мкм и шероховатости Ra = 0,8 мкм.
2.8. Для повышения коэффициента скольжения наклеили тефлоновые пластины с последующим их шабрением ручным или механическим способами.
2.9. Провели замену шарико-винтовых передач (ШВП), по координатам «Х, Y, Z», определяющим точность перемещений узлов по осям координат. ШВП по координатам «Y и Z» были установлены на фирме-изготовителе траверсы. Новую ШВП установили в станину станка с новыми упорными подшипниками, после чего проверили на точность, т.е. измерили правильность установки винта по высоте, параллельность и биение.
Примечание:
При необходимости большинство таких передач можно все-таки восстановить один раз (иногда два) в зависимости от степени износа или вида подлежащих исправлению повреждений.
Этим обычно занимаются высокотехнологические специализированные предприятия, имеющие оборудование для финишной обработки. Технология восстановления таких передач следующая: винт и гайку разбирают, проверяют износ, твердость и наличие ржавчины, после чего выносят вердикт о возможности или невозможности ремонта. Перешлифованный винт отремонтированной передачи возвращают вместе с новой гайкой. Его опорные шейки проверяют на биение и при необходимости перешлифовывают. Винт устанавливают в станок с новыми упорными подшипниками, после чего проверяют на точность, т.е. измеряют правильность установки винта по высоте, параллельность и биение.
2.10. В станке заменили все подшипники,гидравлические, пневматические и электрические системы. Проверили все зубчатые колеса на износ и наличие трещин, определили контактные пятна, а валы — на прямолинейность. На части валов произвели ремонт опорных шеек. Большую часть валов изготовили вновь.
2.11. Произвели работы по ремонту гидросистемы: гидробак был очищен от грязи и осмотрен на наличие вмятин, трещин и было проверено состояние резьбы. Насос был заменен на новый, а старый был отправлен на участок ремонта гидроаппаратуры для ремонта. В электроцехе предприятия был проведен ремонт электродвигателя, после чего он был установлен на гидробак. Все фильтры были заменены на новые. Техническое состояние всех дросселей было проверено на специализированном стенде. После проверки часть дросселей была повторно установлена на станок, так как у соленоидных клапанов гидравлической системы механических повреждений обычно не бывает, чаще всего сгорает обмотка. Поэтому решение об их повторном применении было принято по результатам их проверки на стенде.
Резиновые шланги были все заменены на новые.
2.12. В централизованной системе смазки заменили насос, гибкие шланги и часть металлических магистралей. Все металлические магистрали были промыты и проверены на возможность утечек.
2.13. Была установлена более современная система с масловоздушным насосом высокого давления (до 210 МПа), которая содержит снабженные золотниками индивидуальные блоки подачи масла. Всякий раз, когда срабатывает поршень насоса, золотники в этих блоках смещаются на определенную величину, точно отмеряя количество масла, поступающего в каждую точку смазки. Если золотник не сместился, аварийный сигнал от блока поступает в ЧПУ.
2.14. Проведены работы по ручному и механическому шабрению всех направляющих (стола, станины траверсы и шпиндельной бабки), так как при шабрении получаем более точный результат, чем при шлифовании.
3. Работы по сборке станка
3.1. Сборку станка начинаем с установки на фундамент доработанного металлического креста и крепления его к фундаменту, с последующей выверкой с помощью электронных уровней. Металлический крест для обеспечения жесткости соединения стоек со станиной показан на нижерасположенном рисунке.
2.6. Направляющие скольжения очистили от ржавчины, тщательно осмотрели на предмет обнаружения задиров и проверили твердость. Твердость составила 50 HRC на глубину 0,23-3,2 мм. Глубина задиров и
царапин превышала 1,25 мм).
2.7. Данные направляющие были перешлифованы на плоскошлифовальном станке Coburg с получением плоскостности 5 мкм и шероховатости Ra = 0,8 мкм.
2.8. Для повышения коэффициента скольжения наклеили тефлоновые пластины с последующим их шабрением ручным или механическим способами.
2.9. Провели замену шарико-винтовых передач (ШВП), по координатам «Х, Y, Z», определяющим точность перемещений узлов по осям координат. ШВП по координатам «Y и Z» были установлены на фирме-изготовителе траверсы. Новую ШВП установили в станину станка с новыми упорными подшипниками, после чего проверили на точность, т.е. измерили правильность установки винта по высоте, параллельность и биение.
Примечание:
При необходимости большинство таких передач можно все-таки восстановить один раз (иногда два) в зависимости от степени износа или вида подлежащих исправлению повреждений.
Этим обычно занимаются высокотехнологические специализированные предприятия, имеющие оборудование для финишной обработки. Технология восстановления таких передач следующая: винт и гайку разбирают, проверяют износ, твердость и наличие ржавчины, после чего выносят вердикт о возможности или невозможности ремонта. Перешлифованный винт отремонтированной передачи возвращают вместе с новой гайкой. Его опорные шейки проверяют на биение и при необходимости перешлифовывают. Винт устанавливают в станок с новыми упорными подшипниками, после чего проверяют на точность, т.е. измеряют правильность установки винта по высоте, параллельность и биение.
2.10. В станке заменили все подшипники,гидравлические, пневматические и электрические системы. Проверили все зубчатые колеса на износ и наличие трещин, определили контактные пятна, а валы — на прямолинейность. На части валов произвели ремонт опорных шеек. Большую часть валов изготовили вновь.
2.11. Произвели работы по ремонту гидросистемы: гидробак был очищен от грязи и осмотрен на наличие вмятин, трещин и было проверено состояние резьбы. Насос был заменен на новый, а старый был отправлен на участок ремонта гидроаппаратуры для ремонта. В электроцехе предприятия был проведен ремонт электродвигателя, после чего он был установлен на гидробак. Все фильтры были заменены на новые. Техническое состояние всех дросселей было проверено на специализированном стенде. После проверки часть дросселей была повторно установлена на станок, так как у соленоидных клапанов гидравлической системы механических повреждений обычно не бывает, чаще всего сгорает обмотка. Поэтому решение об их повторном применении было принято по результатам их проверки на стенде.
Резиновые шланги были все заменены на новые.
2.12. В централизованной системе смазки заменили насос, гибкие шланги и часть металлических магистралей. Все металлические магистрали были промыты и проверены на возможность утечек.
2.13. Была установлена более современная система с масловоздушным насосом высокого давления (до 210 МПа), которая содержит снабженные золотниками индивидуальные блоки подачи масла. Всякий раз, когда срабатывает поршень насоса, золотники в этих блоках смещаются на определенную величину, точно отмеряя количество масла, поступающего в каждую точку смазки. Если золотник не сместился, аварийный сигнал от блока поступает в ЧПУ.
2.14. Проведены работы по ручному и механическому шабрению всех направляющих (стола, станины траверсы и шпиндельной бабки), так как при шабрении получаем более точный результат, чем при шлифовании.
3. Работы по сборке станка
3.1. Сборку станка начинаем с установки на фундамент доработанного металлического креста и крепления его к фундаменту, с последующей выверкой с помощью электронных уровней. Металлический крест для обеспечения жесткости соединения стоек со станиной показан на нижерасположенном рисунке.
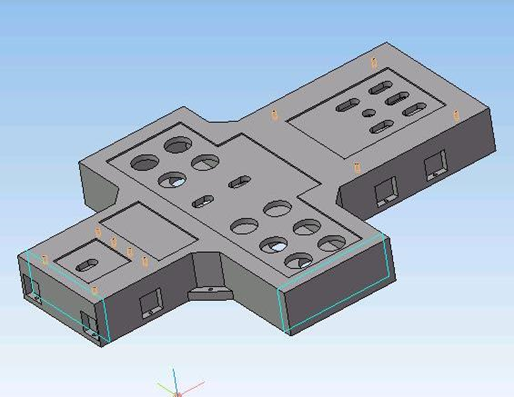
3.2. После приведения в соответствие с техническими требованиями всех узлов и комплектующих компонентов станка приступают к его сборке. Монтируем станину на специальный металлический крест, установленный на фундамент, с последующей выверкой по электронному уровню станины.
Чертеж станины показан на нижерасположенном рисунке.
Чертеж станины показан на нижерасположенном рисунке.
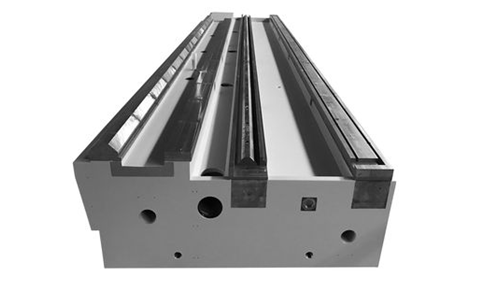
3.3. На станину станка устанавливаем продольно круговой стол.
При установке на станину продольно-поворотного стола возникают определенные точностные погрешности, поэтому мы производим повторную выверку станины вместе с установленным на него продольно-поворотным столом.
3.4. Устанавливаем на металлический крест две стойки слева и справа от станины.
Чертеж станины с продольно-круговым столом и стойками показан на нижерасположенном рисунке.
При установке на станину продольно-поворотного стола возникают определенные точностные погрешности, поэтому мы производим повторную выверку станины вместе с установленным на него продольно-поворотным столом.
3.4. Устанавливаем на металлический крест две стойки слева и справа от станины.
Чертеж станины с продольно-круговым столом и стойками показан на нижерасположенном рисунке.
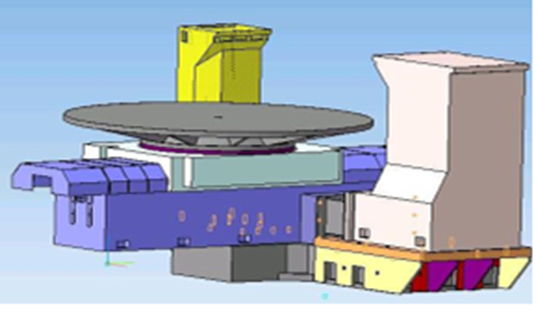
3.5. Устанавливаем на стойки вновь изготовленную траверсу, которая показана на нижерасположенном рисунке.
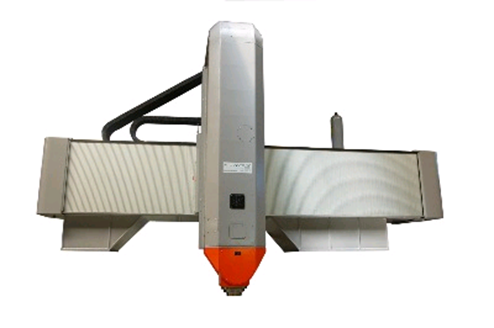
3.6. Выставляем параллельность траверсы относительно станины.
3.7. Установили шпиндельную бабку на траверсу.
3.8. Выставляем геометрию шпиндельной бабки относительно станины и траверсы.
3.9. Выполняем работы по установке станции очистки и подачи СОЖ высокого давления модели SCK3-10 производства фирмы ALUP.
3.7. Установили шпиндельную бабку на траверсу.
3.8. Выставляем геометрию шпиндельной бабки относительно станины и траверсы.
3.9. Выполняем работы по установке станции очистки и подачи СОЖ высокого давления модели SCK3-10 производства фирмы ALUP.
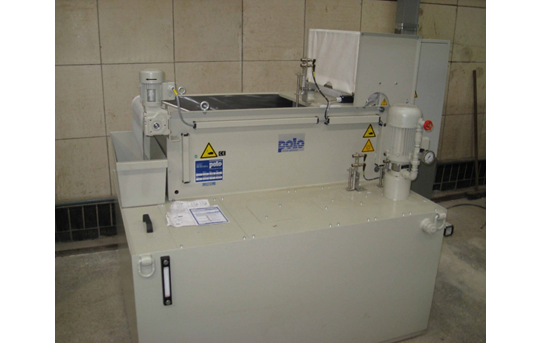
3.10. Выполняем работы по установке компрессора производства фирмы ALUP.
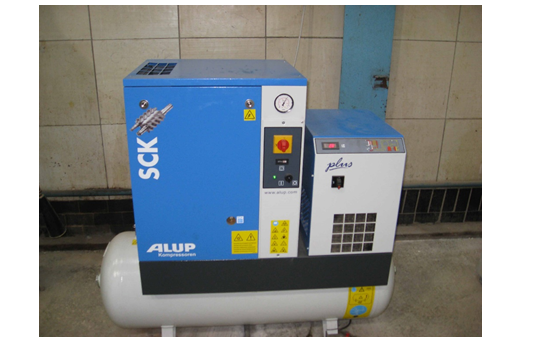
3.11. Выполняем работы по установке станции смазки и охлаждения шпинделя модели IK-V.
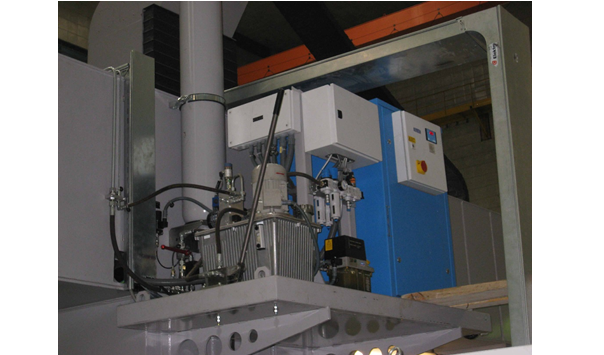
3.12. После сборки станка производим его статическую (с помощью гранитного угольника и электронных уровней) и динамическую (путем компьютерного анализа точности станка при холостых перемещениях его узлов) проверку.
3.13. С помощью измерительной системы Renishaw проверяем точность позиционирования узлов станка по всем осям и правильное соотношение между ними при перемещении.
3.14. Выполняем работы по установке компрессора, станции смазки и охлаждения шпинделя, станции очистки СОЖ.
3.15. По периметру станка устанавливаем кабинетную защиту, изготовленную собственными силами, с использованием производства пластиковых окон и перегородок.
Примечание:
При ремонте станков (с их частичной переделкой) осуществляются не только операции, характерные для модернизации и капремонта, но и производятся конструктивные изменения, улучшающие функциональные характеристики станка, в частности повышающие частоты вращения шпинделя, скорости рабочих и быстрых перемещений и при необходимости удлиняющие эти перемещения.
Обычно все работы по капитальному ремонту станков проводятся на одном заводе. Для капитального ремонта крупногабаритного станка требуется от 22 до 48 недель. Стоимость восстановленного станка составляет примерно 50-60% от цены нового. Однако производительность такого станка практически не уступает новому.
4. Электромонтажные работы
4.1 Заменена система ЧПУ типа СЦП-5 на систему ЧПУ Sinumerik 840 D sl с аксессуарами, пультом оператора, выносным станочным пультом.
3.13. С помощью измерительной системы Renishaw проверяем точность позиционирования узлов станка по всем осям и правильное соотношение между ними при перемещении.
3.14. Выполняем работы по установке компрессора, станции смазки и охлаждения шпинделя, станции очистки СОЖ.
3.15. По периметру станка устанавливаем кабинетную защиту, изготовленную собственными силами, с использованием производства пластиковых окон и перегородок.
Примечание:
При ремонте станков (с их частичной переделкой) осуществляются не только операции, характерные для модернизации и капремонта, но и производятся конструктивные изменения, улучшающие функциональные характеристики станка, в частности повышающие частоты вращения шпинделя, скорости рабочих и быстрых перемещений и при необходимости удлиняющие эти перемещения.
Обычно все работы по капитальному ремонту станков проводятся на одном заводе. Для капитального ремонта крупногабаритного станка требуется от 22 до 48 недель. Стоимость восстановленного станка составляет примерно 50-60% от цены нового. Однако производительность такого станка практически не уступает новому.
4. Электромонтажные работы
4.1 Заменена система ЧПУ типа СЦП-5 на систему ЧПУ Sinumerik 840 D sl с аксессуарами, пультом оператора, выносным станочным пультом.
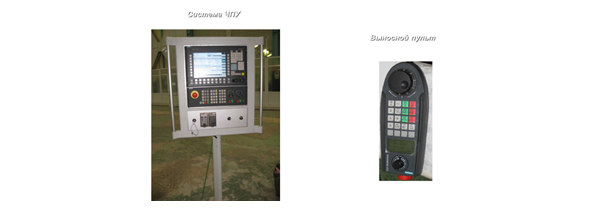
4.2. Заменены преобразователи приводов подач типа ЭТ3 на частотные преобразователи типа Sinamics по всем четырем координатам станка (3 линейные и одна круговая).
4.3. Для управления приводом главного движения с мотор-шпинделем был установлен частотный преобразователь Sinamics.
4.4. Собран электрический шкаф с новой низковольтной аппаратурой и системой охлаждения.
4.5. Установлена измерительная система позиционирования на базе измерительных линеек производства фирмы Ханденхайн.
4.6. Произведено программирование ЧПУ и настройка приводов.
4.7. Разработана программа электроавтоматики станка.
4.8. Произведена проверка управляемости систем станка от системы ЧПУ.
4.9. Разработана тестовая программа на все движения и обкатка на холостом ходу в течение 24 часов.
5. Выявление и устранение недостатков в выполненном проекте капитального ремонта с глубокой модернизацией специального фрезерного станка модели СФП-13.
5.1. Устранение замечаний, выявленных при сдаче станка контролерам и отраженных в протоколе.
5.2. Устранение замечаний, выявленных при работе станка на холостых ходах и под нагрузкой.
6.Сдача станка в эксплуатацию
6.1. Проверка точностных паспортных характеристик станка с составлением протокола.
6.2. Проверка точности позиционирования и повторяемости.
6.3. Мониторинг с глубокой диагностикой всех узлов станка при обработке тестовой детали в течении 24 часов.
6.4. Демонстрация новых возможностей станка.
6.5. Сдача станка в эксплуатацию по акту.
На нижерасположенной таблице показаны сравнительные технические характеристики специального фрезерного станка модели СФП-13 до и после капитального ремонта с глубокой модернизацией.
4.3. Для управления приводом главного движения с мотор-шпинделем был установлен частотный преобразователь Sinamics.
4.4. Собран электрический шкаф с новой низковольтной аппаратурой и системой охлаждения.
4.5. Установлена измерительная система позиционирования на базе измерительных линеек производства фирмы Ханденхайн.
4.6. Произведено программирование ЧПУ и настройка приводов.
4.7. Разработана программа электроавтоматики станка.
4.8. Произведена проверка управляемости систем станка от системы ЧПУ.
4.9. Разработана тестовая программа на все движения и обкатка на холостом ходу в течение 24 часов.
5. Выявление и устранение недостатков в выполненном проекте капитального ремонта с глубокой модернизацией специального фрезерного станка модели СФП-13.
5.1. Устранение замечаний, выявленных при сдаче станка контролерам и отраженных в протоколе.
5.2. Устранение замечаний, выявленных при работе станка на холостых ходах и под нагрузкой.
6.Сдача станка в эксплуатацию
6.1. Проверка точностных паспортных характеристик станка с составлением протокола.
6.2. Проверка точности позиционирования и повторяемости.
6.3. Мониторинг с глубокой диагностикой всех узлов станка при обработке тестовой детали в течении 24 часов.
6.4. Демонстрация новых возможностей станка.
6.5. Сдача станка в эксплуатацию по акту.
На нижерасположенной таблице показаны сравнительные технические характеристики специального фрезерного станка модели СФП-13 до и после капитального ремонта с глубокой модернизацией.
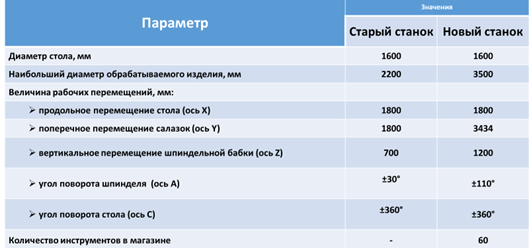
На нижерасположенной таблице показаны основные технические характеристики специального фрезерного станка модели СФП-13 после капитального ремонта с глубокой
модернизацией.
модернизацией.
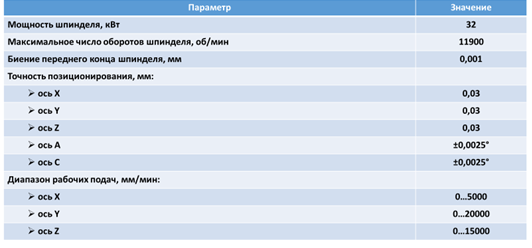
На нижерасположенном рисунке показан общий вид специального фрезерного станка модели СФП-13 после капитального ремонта с глубокой модернизацией.
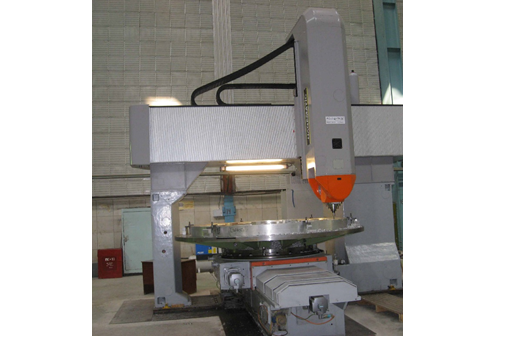
Заключение
Использование агрегатирования позволило в процессе капитального ремонта с глубокой модернизацией создать технологическое оборудование под конкретную группу изделий с реализацией оптимального технологического процесса. А оснащение станка современной системой управления, а также узлами и оборудованием для САМ-технологий и НSМ-технологий позволило получить качественно новый станок c:
Результатами контрольных испытаний было подтверждено, что гарантированная точность линейного размера при чистовой обработке на круговом контуре 500 мм составляет не более 0,02–0,03 мм. При этом скорость рабочей подачи доходит до 2 м/мин. Для повышения качества обработки карманов и вафельного фона была применена технология HSM – с использованием высокоскоростного мотор-шпинделя производства фирмы IBAG.
После проведения капитального ремонта с глубокой модернизацией специального фрезерного станка модели СФП 13 по модульному принципу мы значительно расширили технологические возможности станка.
Сочетание различных компоновок модулей и сквозная CAD/CAM-технология по 3D-моделям позволили последовательно обрабатывать практически любые сложные детали за одну-две установки без непосредственного участия станочника. Отсутствует субъективный фактор, качество определяется только технологией и возможностью оборудования.
В зависимости от текущего задания на одном станке осуществляются различные варианты современной многоосевой обработки с элементами технологии HSM, такие как технологии обработки вафельного фона на плоских и цилиндрических деталях. Данная технология позволила вести обработку наружного и внутреннего контуров крупногабаритных цилиндрических и конусообразных деталей из алюминиевых сплавов в сочетании с высокопроизводительной высокоскоростной обработки в 5-осевом режиме (благодаря высокой жесткости станка и современным приводам главного движения, приводов подачи и системы ЧПУ, производства фирмы Siemens).
Оптимально подобранные режимы резания (обороты шпинделя от 50 до 12000 об/мин, глубина резания – 4 мм, подача до 6 м/мин) при использовании фрез диаметром 50 мм обеспечивают скорость съема металла до 1,2*106 мм3/мин, что является одним из основных факторов, определяющих эффективность металлообработки на данном станке.
Стоит отметить, что фрезерование алюминиевых сплавов осложняется их способностью налипать на инструмент при нагреве заготовки от процесса резания. Нами была отработана технология кольцевого обдува инструмента воздухом, при котором процесс резания находился в температурном режиме, исключающем налипание стружки, а поверхность обработки всегда была чистой. Использование воздуха для охлаждения инструмента особенно важно при фрезеровании глубоких карманов, когда затруднено применение традиционных смазочно-охлаждающих жидкостей (СОЖ).
Для пятиосевой обработки деталей, а также пространственного сверления точных отверстий в крупных цилиндрических и сферических деталях критичными параметрами деталей с вафельным фоном и шпангоутов является точное позиционирование отверстий, карманов и ячеек и шаг между отверстиями и ячейками. При попытке изготовления данных деталей на старом станке был большой процент брака и низкая производительность. Данная головка значительно расширяет технологические возможности станка, поскольку она позволяет установку на столе с горизонтальным закреплением деталей вращения диаметром до 3,5 м.
В этом случае мы получили оборудование, способное реализовывать токарные и фрезерные, сверлильные и расточные операции на одном станке без переустановки. Разработанная технология капитального ремонта с глубокой модернизацией по модульному принципу позволяет перейти на более высокий уровень проведения работ. Кроме того, капитально отремонтированный с глубокой модернизацией станок модели СФП 13 ведет работу в CAD/CAM-системе напрямую с 3D-моделями с сетевой поддержкой на всех уровнях и тем самым снижает издержки производства в 3 раза. Технология практически полностью исключает человеческий фактор при производстве изделий и не требует обслуживающего персонала высокой квалификации.
Итак, подведем итог.
Проведен капитальный ремонт с глубокой модернизацией под конкретные технологические задачи по модульному принципу, в результате получен станок с новыми техническими возможностями:
– во-первых, он совмещает токарные, сверлильные и фрезерные операции на одном станке. При этом, проводя обработку за одну установку, мы не только повышаем общую производительность и качество обработки, но и значительно уменьшаем общие затраты;
– во-вторых, учитывая, что используем CAD/CAM-систему напрямую с 3D-моделями и со сквозной сетевой поддержкой, это позволяет исключить субъективный фактор, что также повышает качество обработки;
– в-третьих, используя современные комплектующие, мы получили технические характеристики капитально отремонтированного с глубокой модернизацией станка, значительно превосходящие характеристики старого станка.
В частности, после капитального ремонта с глубокой модернизацией станка модели СФП-13, точность его обработки показала:
Исходя из вышесказанного можно сделать вывод, что при правильном подходе к обновлению станочного парка предприятий машиностроения капитальный ремонт с глубокой модернизацией является наиболее рациональным и единственно правильным решением.
В настоящее время я уже более 3 лет живу воспоминаниями о своей трудовой деятельности на АО «РКЦ «ПРОГРЕСС», связанной с интересной работой по ТОиР наукоемкого оборудования с ЧПУ и особенно в организации и внедрению в жизнь инновационных проектов по созданию АСУ ТОиР оборудования с ЧПУ, АСУ Мониторинга с глубокой диагностикой технического состояния узлов станков с ЧПУ с элементами технологии дополненной реальности, организации и проведению капитальных ремонтов с глубокой модернизацией станков с ЧПУ.
Особое удовлетворение я получил от реализации трех проектов по капитальному ремонту с глубокой модернизацией. Это проекты по специальному фрезерному станку модели СФП-13, Forest и созданному на базе станины станка модели СТП-320 ПР многоцелевому токарно-фрезерно-сверлильному станку.
Реализованный проект по капитальному ремонту с глубокой модернизацией специального фрезерного станка модели СФП-13 позволил коллективу поверить в себя и в свои возможности и сплотить сотрудников для выполнения других сложных, но необходимых предприятию проектов. И сегодня, используя данную статью, я благодарю Вас всех, уважаемые сотрудники и друзья, за Ваше отношение к выбранному делу по возвращению в жизнь более 150 станков с ЧПУ различной сложности.
Использование агрегатирования позволило в процессе капитального ремонта с глубокой модернизацией создать технологическое оборудование под конкретную группу изделий с реализацией оптимального технологического процесса. А оснащение станка современной системой управления, а также узлами и оборудованием для САМ-технологий и НSМ-технологий позволило получить качественно новый станок c:
- высокой степенью автоматизации,
- высокой производительностью (производительность повысилась в 3-4 раза по отношению к старому показателю),
- возможностью проводить 5-осевую обработку,
- возможностью проводить высокоскоростную обработку,
- возможностью мониторить техническое состояние станка,
- возможностью отключения станка в следствии нарушения технологии обработки, при вероятности столкновения шпинделя с деталью в случае выхода за допустимые пределы технического состояния узлов,
- возможностью применять адаптивное управление процессом резания,
- возможностью проводить измерения детали непосредственно на станке
- возможностью проводить автоматические измерения объемной геометрической точности с последующей автоматической коррекцией.
Результатами контрольных испытаний было подтверждено, что гарантированная точность линейного размера при чистовой обработке на круговом контуре 500 мм составляет не более 0,02–0,03 мм. При этом скорость рабочей подачи доходит до 2 м/мин. Для повышения качества обработки карманов и вафельного фона была применена технология HSM – с использованием высокоскоростного мотор-шпинделя производства фирмы IBAG.
После проведения капитального ремонта с глубокой модернизацией специального фрезерного станка модели СФП 13 по модульному принципу мы значительно расширили технологические возможности станка.
Сочетание различных компоновок модулей и сквозная CAD/CAM-технология по 3D-моделям позволили последовательно обрабатывать практически любые сложные детали за одну-две установки без непосредственного участия станочника. Отсутствует субъективный фактор, качество определяется только технологией и возможностью оборудования.
В зависимости от текущего задания на одном станке осуществляются различные варианты современной многоосевой обработки с элементами технологии HSM, такие как технологии обработки вафельного фона на плоских и цилиндрических деталях. Данная технология позволила вести обработку наружного и внутреннего контуров крупногабаритных цилиндрических и конусообразных деталей из алюминиевых сплавов в сочетании с высокопроизводительной высокоскоростной обработки в 5-осевом режиме (благодаря высокой жесткости станка и современным приводам главного движения, приводов подачи и системы ЧПУ, производства фирмы Siemens).
Оптимально подобранные режимы резания (обороты шпинделя от 50 до 12000 об/мин, глубина резания – 4 мм, подача до 6 м/мин) при использовании фрез диаметром 50 мм обеспечивают скорость съема металла до 1,2*106 мм3/мин, что является одним из основных факторов, определяющих эффективность металлообработки на данном станке.
Стоит отметить, что фрезерование алюминиевых сплавов осложняется их способностью налипать на инструмент при нагреве заготовки от процесса резания. Нами была отработана технология кольцевого обдува инструмента воздухом, при котором процесс резания находился в температурном режиме, исключающем налипание стружки, а поверхность обработки всегда была чистой. Использование воздуха для охлаждения инструмента особенно важно при фрезеровании глубоких карманов, когда затруднено применение традиционных смазочно-охлаждающих жидкостей (СОЖ).
Для пятиосевой обработки деталей, а также пространственного сверления точных отверстий в крупных цилиндрических и сферических деталях критичными параметрами деталей с вафельным фоном и шпангоутов является точное позиционирование отверстий, карманов и ячеек и шаг между отверстиями и ячейками. При попытке изготовления данных деталей на старом станке был большой процент брака и низкая производительность. Данная головка значительно расширяет технологические возможности станка, поскольку она позволяет установку на столе с горизонтальным закреплением деталей вращения диаметром до 3,5 м.
В этом случае мы получили оборудование, способное реализовывать токарные и фрезерные, сверлильные и расточные операции на одном станке без переустановки. Разработанная технология капитального ремонта с глубокой модернизацией по модульному принципу позволяет перейти на более высокий уровень проведения работ. Кроме того, капитально отремонтированный с глубокой модернизацией станок модели СФП 13 ведет работу в CAD/CAM-системе напрямую с 3D-моделями с сетевой поддержкой на всех уровнях и тем самым снижает издержки производства в 3 раза. Технология практически полностью исключает человеческий фактор при производстве изделий и не требует обслуживающего персонала высокой квалификации.
Итак, подведем итог.
Проведен капитальный ремонт с глубокой модернизацией под конкретные технологические задачи по модульному принципу, в результате получен станок с новыми техническими возможностями:
– во-первых, он совмещает токарные, сверлильные и фрезерные операции на одном станке. При этом, проводя обработку за одну установку, мы не только повышаем общую производительность и качество обработки, но и значительно уменьшаем общие затраты;
– во-вторых, учитывая, что используем CAD/CAM-систему напрямую с 3D-моделями и со сквозной сетевой поддержкой, это позволяет исключить субъективный фактор, что также повышает качество обработки;
– в-третьих, используя современные комплектующие, мы получили технические характеристики капитально отремонтированного с глубокой модернизацией станка, значительно превосходящие характеристики старого станка.
В частности, после капитального ремонта с глубокой модернизацией станка модели СФП-13, точность его обработки показала:
- ошибку измерительной системы 0,01 мм на метр длины против 0,1 мм на метр длины в обычном исполнении (паспорт станка СФП-13),
- погрешность позиционирования реальная по осям Y и Z не больше 0,01 мм, по оси X не больше 0,03 мм.
- Станок отработал в круглосуточном режиме уже более 10 лет, показывая высокую технологичность обработки, высокую производительность, надежность и качество.
Исходя из вышесказанного можно сделать вывод, что при правильном подходе к обновлению станочного парка предприятий машиностроения капитальный ремонт с глубокой модернизацией является наиболее рациональным и единственно правильным решением.
В настоящее время я уже более 3 лет живу воспоминаниями о своей трудовой деятельности на АО «РКЦ «ПРОГРЕСС», связанной с интересной работой по ТОиР наукоемкого оборудования с ЧПУ и особенно в организации и внедрению в жизнь инновационных проектов по созданию АСУ ТОиР оборудования с ЧПУ, АСУ Мониторинга с глубокой диагностикой технического состояния узлов станков с ЧПУ с элементами технологии дополненной реальности, организации и проведению капитальных ремонтов с глубокой модернизацией станков с ЧПУ.
Особое удовлетворение я получил от реализации трех проектов по капитальному ремонту с глубокой модернизацией. Это проекты по специальному фрезерному станку модели СФП-13, Forest и созданному на базе станины станка модели СТП-320 ПР многоцелевому токарно-фрезерно-сверлильному станку.
Реализованный проект по капитальному ремонту с глубокой модернизацией специального фрезерного станка модели СФП-13 позволил коллективу поверить в себя и в свои возможности и сплотить сотрудников для выполнения других сложных, но необходимых предприятию проектов. И сегодня, используя данную статью, я благодарю Вас всех, уважаемые сотрудники и друзья, за Ваше отношение к выбранному делу по возвращению в жизнь более 150 станков с ЧПУ различной сложности.