И начнем с тепловизионной диагностики.
Тепловизионная диагностика и тепловой контроль представляют собой высокотехнологичную область прикладных исследований, объединяющую достижения не только в создании аппаратуры (тепловизоров), но и в теории теплопередачи, информационных и компьютерных технологиях.
Основными преимуществами тепловизионной диагностики являются:
проведение тепловизионного контроля без специальных условий и без вывода объекта контроля из эксплуатации, без контактности, контроль объектов любых форм и размеров, высокая производительность контроля, высокая скорость обработки результатов.
Рассмотрим основы тепловизионного метода диагностики, применяемого при поиске неисправных узлов станков.
Все мы прекрасно знаем и наблюдаем, что изменение температурного режима узлов станка всегда предшествует выходу их из строя. Узлы оборудования, такие как шпиндель, шарико-винтовая пара, фрезерная головка имеют в своей конструкции подшипники, которые имеют свойство в процессе работы нагреваться за счет увеличения трения в связи с износом или недостатком смазки.
Нагрев электрического оборудования происходит, как правило, из-за повышения сопротивления контактных групп.
Нагрев гидравлического оборудования происходит из-за засорения фильтра, нарушения пропускной способности гидросистемы, низкого уровня масла в гидросистеме, потери качества масла, выхода из строя охладителя или теплообменника, поломки элементов гидросистемы (клапанов, моторов, распределителей и т.п.), ошибочной настройки элементов гидросистемы.
На нижерасположенном рисунке я представил график общего баланса тепловыделения узлами токарного станка, полученный в практических условиях при эксплуатации станков, из которого мы видим узлы участвующие в тепловыделении в процессе эксплуатации.
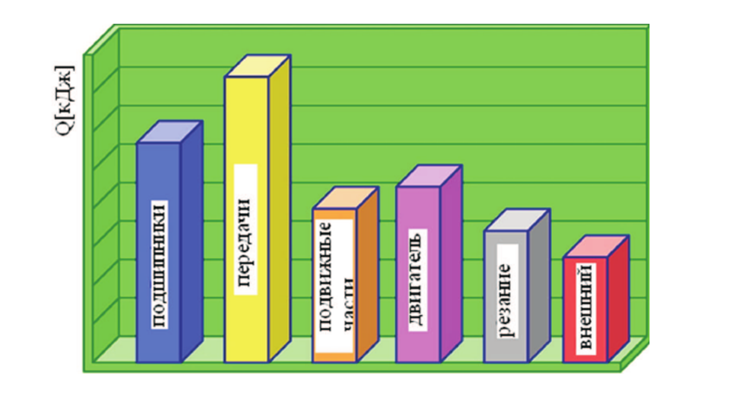
А теперь прейдем к теме сегодняшней статьи и начнем с методики.
Измерение параметров температуры
28. Средства измерения
Мы в Техническом центре измерение температур узлов оборудования осуществляли с помощью нижеперечисленных специальных устройств.
Использование в процессе ТОиР оборудования с ЧПУ тепловизионной диагностики узлов станков Технический центр начал с 2008 года, используя Пирометр BALTECH TL-0208C.
В результате проводимой тепловизионной диагностики мы очень быстро стали получать результаты в виде теплограмм, на основании анализа которых с помощью программы BALTECH Expert получали выводы о наличии тепловых аномалий и уровне развития дефекта во времени.
28.1.Пирометр (BALTECH TL-0208C)
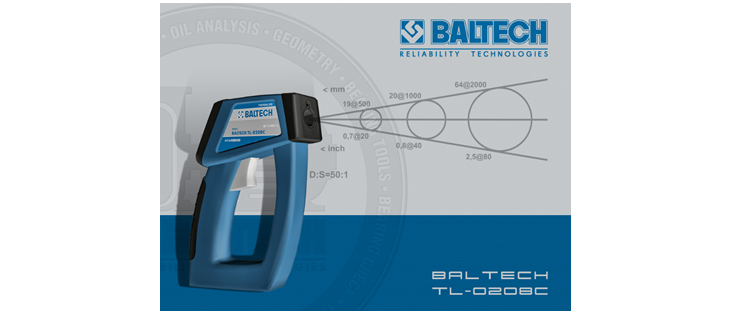
BALTECH TL-0208C – это современный пирометр инфракрасный для измерения температуры, который обеспечивает точные мгновенные измерения температуры 0°С или 0°F.
В основе работы инфракрасных термометров лежит бесконтактное измерение мощности теплового излучения узла станка в диапазоне инфракрасного излучения. Показатель визирования инфракрасного бесконтактного термометра BALTECH определяется оптической схемой объектива. Показатель визирования является отношением расстояния от объектива прибора до пятна измерения* к диаметру пятна измерения. Показатель визирования для данного инфракрасного бесконтактного термометра определяется на расстоянии 1 метр от объектива. Принцип работы приведен ниже на рисунках.
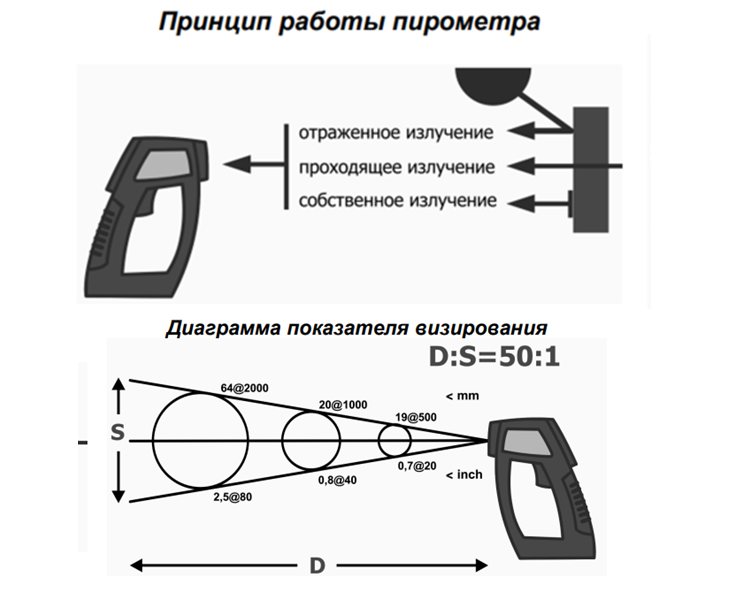
28.2. Тепловизоры (HotFind и Fluke T1300+).
На нижерасположенном рисунке изображены общий вид и состав блоков тепловизора модели Fluke 1300+.
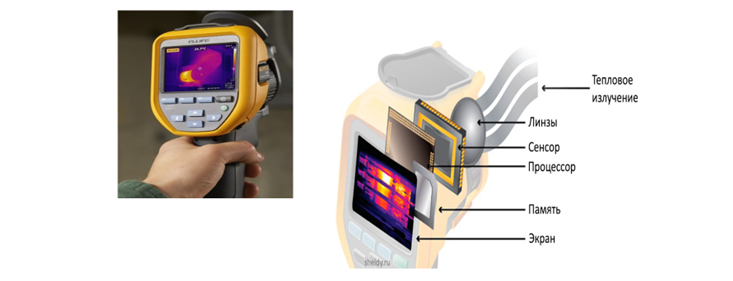
28.2.1. Объекты измерения параметров температуры узлов станка.
28.2.1.1. Электродвигатели: приводы главного движения, приводы подач, вспомогательных перемещений, приводы насоса гидростанции (при необходимости).
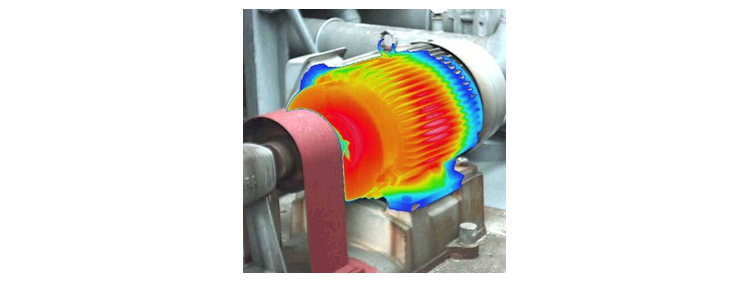
28.2.1.2. Корпуса всех разновидностей шпинделей (по необходимости).
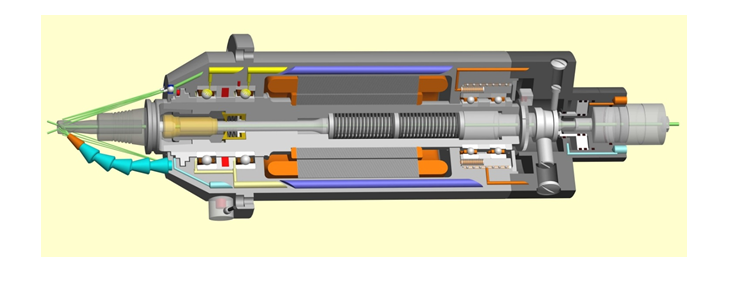
28.2.1.3. Шарико-винтовые пары (ШВП).
В системе шариковых винтов источниками тепловыделения являются гайки и 2 подшипника, а источниками теплопотерь являются жидкостное охлаждение и поверхностная конвекция.
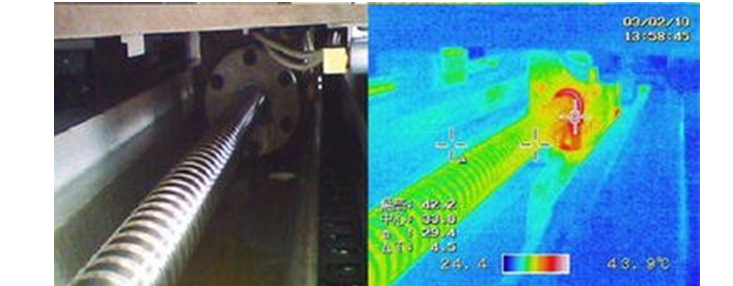
28.2.1.4. Линейные опоры качения (ЛОК).
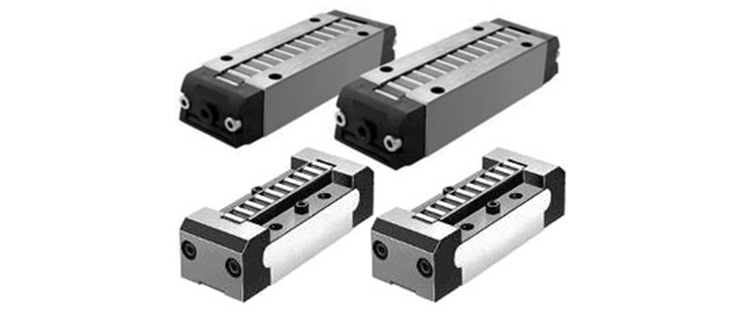
28.2.1.5. Направляющие станков:
-качения,
-скольжения,
-комбинированные.
28.2.1.6. Корпуса насосов гидростанций (по необходимости).
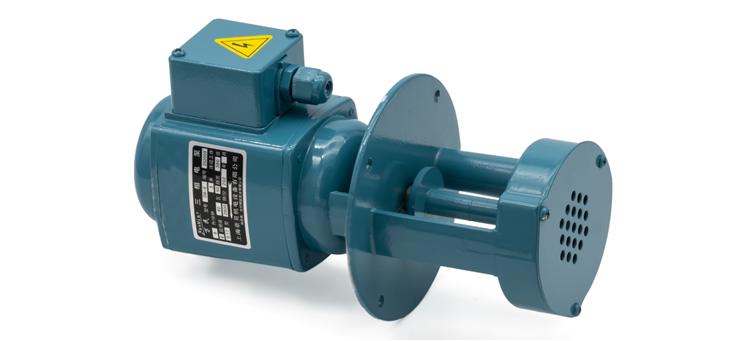
28.2.1.7. Шкаф с низковольтной аппаратурой (по необходимости).
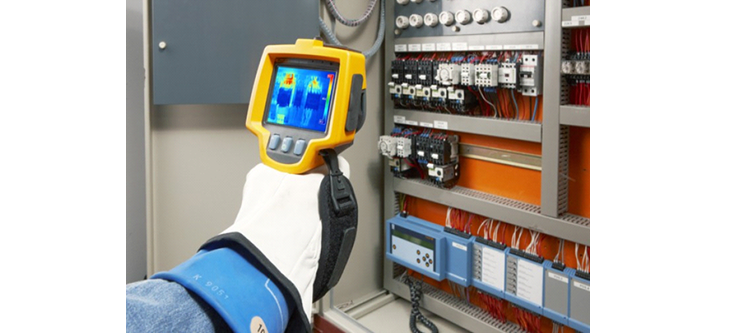
28.2.1.8. Корпуса фрезерных головок.
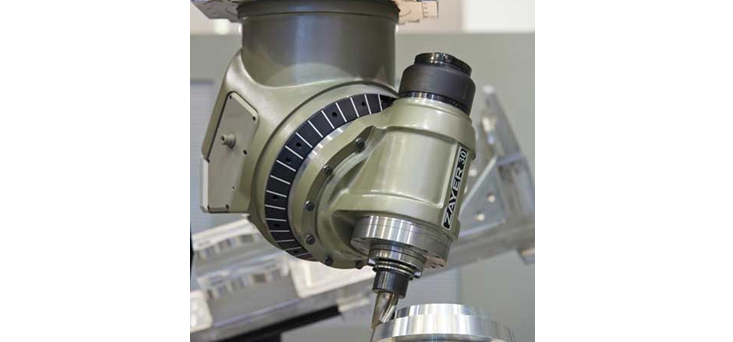
28.3 Датчики температуры, стационарно установленные на станке.
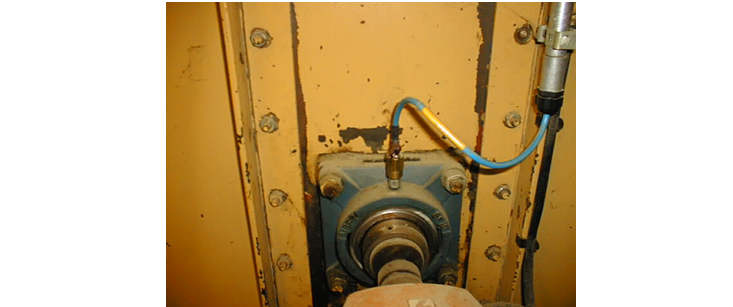
29. Порядок проведения измерений параметров температуры
29.1. Включение объекта диагностики на максимальный режим работы на время не менее 60 мин.
29.2. Измерение температуры бесконтактным средством измерения в точках с наибольшим потенциальным нагревом.
29.3 Запись измеренных значений.
29.4. Сравнение измеренных значений с рекомендованными допустимыми.
29.5. Выдача протокола измерений.
30. Оценка технического состояния по результатам измерения параметров температуры
30.1. Предельная допустимая температура наружного кольца подшипника шпинделя не должна превышать 65°С.
30.2. Предельная допустимая температура переднего торца шпинделя при максимальной скорости вращения не должна превышать 50°С.
30.3. Избыточная температура корпуса шпинделя (разница между температурой корпуса и температурой окружающей среды) не должна превышать 50°С.
30.4. Предельная допустимая температура обмотки статора электродвигателя не должна превышать 130°С.
30.5. Предельная температура электродвигателей и насоса гидростанции не должны превышать значений, указанных в руководстве по эксплуатации.
30.6. Температура подшипников должна быть не выше рекомендуемой. Увеличение ее на 10...20 °С уже свидетельствует о нарушениях в работе (плохое смазывание или механическое повреждение). Сравнивая условия нагревания подшипников с типовыми, можно выявить неисправности в работе соответствующего узла.
Повышенный уровень шума вредно действует на людей, работающих в близи станков. Для обеспечения нормальных условий работы уровни шума в производственных помещений регламентируются. В зависимости от частотной характеристики шума устанавливаются допустимые общие уровни шума в производственных цехах и около работающих станков.
Измерение шумовых характеристик
31. Средства измерения
31.1. Шумомер (ZET 110).
Виброметр, шумомер и регистратор данных ZET 110 предназначен для измерения параметров сигналов с различных датчиков, измерения уровней шума и уровней вибрации, отображения измеряемых параметров на экране и непрерывной записи сигналов во встроенную энергонезависимую память объемом до 2 Гб. ZET 110 представляет собой 1-канальный прибор с жидкокристаллическим экраном и клавиатурой.
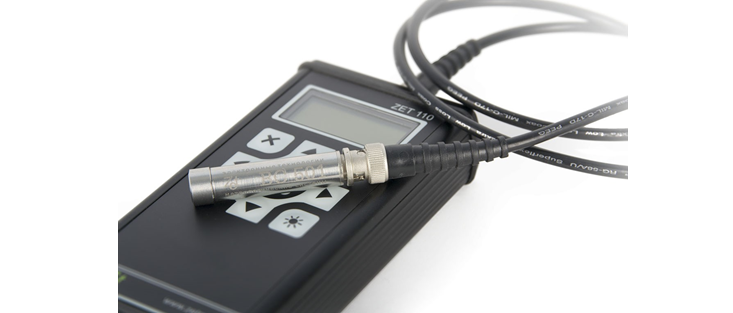
31.2. Микрофон (MPA-201).
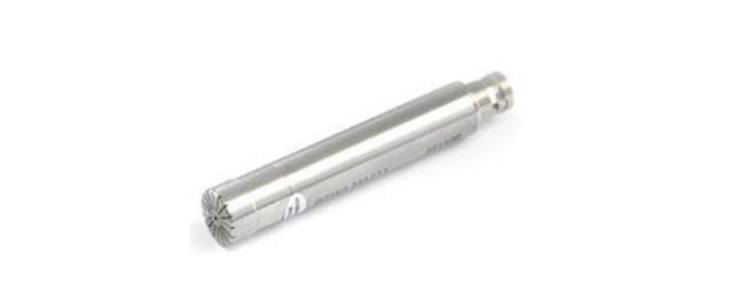
Микрофон МРА 201 поддерживает технологию опроса датчиков TEDS (Transducer Electronic Data Sheet – Электронные Таблицы Данных Датчиков), что позволяет анализатору спектра и шумомеру автоматически определять параметры микрофона. Микрофон позволяет не только измерять общий уровень шума, но проводить, при наличии программного обеспечения, спектральный анализ сигналов с равномерной или октавной (1/1, 1/3, 1/12, 1/24) разверткой по частоте, применять различные фильтры, снимать амплитудно-частотные характеристики, проводить корреляционный анализ
32. Общие сведения по измерению шумовых характеристик
32.1. Измерение шумовых характеристик проводится в соответствии с ГОСТ ИСО 230-5-2002 (ISO 230-5).
32.2. Допустимый уровень шума приводится в паспорте станка, либо определяется по ГОСТ 12.2.107-85.32.3. 32.3. 32.3. Настройка на работу с микрофоном, осуществляется в соответствии с паспортом для шумомера модели ZET 110 производства ЗАО «Электронные технологии и метрологические системы».
33. Порядок настройки прибора на работу с микрофоном
33.1. Подключение к выключенному прибору микрофона посредством кабеля с разъемом типа BNC.33.2. Включение прибора. Переход в режим шумомера.
33.3. Выбор необходимого типа датчика (Наст.>Вход>Дтч).
33.4. Выбор корректирующего фильтра А (Изм.>Сигнал>Fкорр.).
33.5. Выбор детектора вторичных параметров S (Изм.>Сигнал>ДВП).
33.6. Проверка реагирования прибора на сигнал микрофона (увеличение уровня шума в момент легких ударов микрофона по столу).
34. Порядок измерения уровней шума
34.1. Настройка прибора в соответствие с паспортными рекомендациями.34.2. Включение прибора и ожидание 30 секунд с момента включения.
34.3. Измерение фонового уровня шума в цехе в дБА с регистрацией значения в протоколе.
34.4. Измерение уровня шума в дБА возле рабочего места оператора при максимальном числе оборотов шпинделя с регистрацией значения в протоколе.
34.5. Последовательное измерение уровней шума в дБА в точках измерений согласно схеме измерений, при максимальном числе оборотов шпинделя с регистрацией значений в протоколе.
34.6. Сравнение измеренных уровней шума с допустимыми значениями по ГОСТ 12.2.107-85 или по паспортным данным.
34.7. Формирование протокола испытания станка на шум.
На нижерасположенной картинке я представил рабочий протокол результатов измерения уровня шума станка в процессе его работы на холостом ходу.
В протоколе обязательно предоставляется схема расположения точек измерения шума на каждую модель станка.
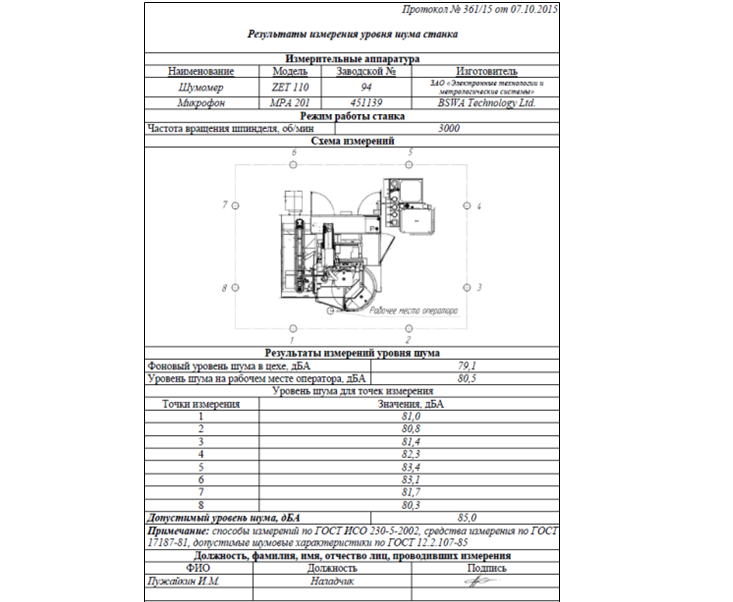
Срок службы механических узлов станков во многом определяется качеством установленных подшипников качения. Снижение качества изготавливаемых подшипников, широкое распространение контрафактной подшипниковой продукции, проведение тендерных закупок подшипников по минимальным ценам, появление восстановленных подшипников на рынке – все это потребовало организацию в Техническом центре входного контроля новых и бывших в употреблении подшипников качения. При этом функции входного контроля не могут ограничиваться анализом документов на продукцию. Требуется комплексный анализ качества поставляемых подшипников. Для этой цели мы приобрели стенд входного контроля подшипников качения модели СП-180М, позволяющий выполнить отбраковку некачественных подшипников до операций сборки подшипниковых узлов. Это дает возможность исключить внеплановые простои механического оборудования и аварийные ситуации, а также увеличить межремонтный период работы оборудования.
Диагностика подшипников качения на стенде
35. Средства диагностики
35.1. Стенд входного контроля подшипников (СП-180М).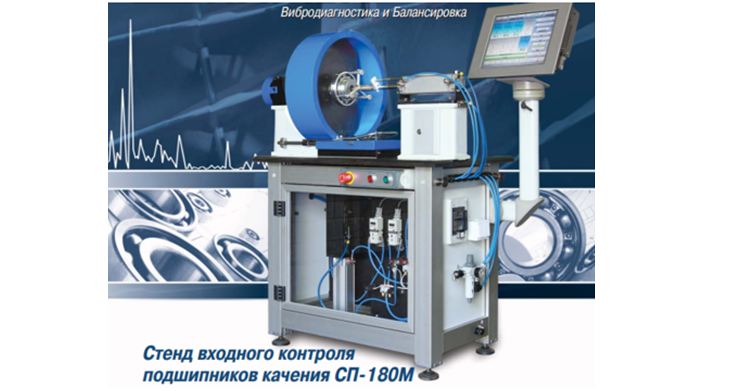
36.Общие сведения по диагностике подшипников качения на стенде
36.1. Диагностика подшипников качения на стенде проводится в соответствии с ГОСТ Р 52545.1-2006 (ИСО 15242-1:2004).
36.2.В качестве метода диагностики подшипников качения используется виброакустическая диагностика.
36.3. Измеряемым параметром вибрации является среднеквадратическое значение виброскорости.
36.4. Измерение среднеквадратического значения виброскорости производится в 3-х полосах частот в зависимости от необходимой частоты вращения внутреннего кольца подшипника.
36.4.1. При частоте вращения 900 об/мин (15 Гц):
36.4.2. Полоса низких частот (L): 25…150 Гц;
36.4.3. Полоса средних частот (M): 150…900 Гц;
36.4.4. Полоса высоких частот (H): 900…10000 Гц;
36.4.5. При частоте вращения 1800 об/мин (30 Гц):
36.4.6. Полоса низких частот (L): 50…300 Гц;
36.4.7. Полоса средних частот (M): 300…1800 Гц;
36.4.8. Полоса высоких частот (H): 1800…10000 Гц;
36.5. Диагностика шариковых радиальных и радиально-упорных подшипников осуществляется при частоте вращения внутреннего кольца 1800 об/мин (30 Гц).
36.6. Диагностика роликовых радиальных цилиндрических подшипников осуществляется при частоте вращения внутреннего кольца 1800 об/мин (30 Гц) для подшипников с наружным диаметром до 100 мм включительно и при частоте вращения внутреннего
кольца 900 об/мин (15 Гц) для подшипников с наружным диаметром более 100 мм.
36.4.9. Диагностика радиальных роликовых двухрядных сферических, радиально-упорных однорядных и двухрядных роликовых конических подшипников осуществляется при частоте вращения внутреннего кольца 900 об/мин (15 Гц).
37.Порядок диагностики подшипников качения на стенде
37.1. Промывка и просушка открытого подшипника, подлежащего диагностики.
37.2. Установка в шпиндель стенда оправки под необходимый внутренний диаметр диагностируемого подшипника.
37.3. Смазывание диагностируемого подшипника маслом типа И-12А и установка на стенд.
37.4. Задание в программном обеспечении стенда параметров диагностируемого подшипника, измерительных нагрузок, частоты вращения внутреннего кольца и допустимых уровней в соответствии с требованиями ГОСТ Р 52545.1-2006 (ИСО 15242-1:2004), МИ ИЦ ЕПК.001-11, РД ВНИИПП.038-08.
37.5. Запуск и проведение измерений.
37.6. Выдача протокола измерений.
38.Оценка технического состояния подшипников качения по результатам диагностики на стенде
38.1. Для подшипников качения шпиндельных узлов (классов точности 4 и 2 по ГОСТ 520-2002) уровни среднеквадратического значения виброскорости в 3-х полосах частот не должны превышать допустимых, представленных в МИ ИЦ ЕПК.001-11, РД ВНИИПП.038-08, для вибрационного разряда Ш3 в зависимости от типа подшипника и его внутреннего диаметра.
38.2. Для подшипников качения общего назначения (редуктора, коробки скоростей и пр.) уровни среднеквадратического значения виброскорости в 3-х полосах частот не должны превышать допустимых, представленных в МИ ИЦ ЕПК.001-11, РД ВНИИПП.038-08, для вибрационного разряда Ш1 в зависимости от типа подшипника и его внутреннего диаметра.
38.3. При наличии рекомендаций от производителя подшипников качения по допустимым уровням среднеквадратического значения виброскорости при диагностике необходимо руководствоваться этими рекомендациями.
На этом я заканчиваю четвертую часть статьи на тему “Методическое обеспечение технического диагностирования оборудования с ЧПУ”, которое
специалисты Технического центра ТОиР оборудования применяют в повседневной практике на предприятии.
В следующей части статьи я познакомлю Вас, уважаемые коллеги, с новым инновационным методом автоматического измерения объемной геометрической точности крупногабаритных многоцелевых станков с ЧПУ с последующим автоматическим вводом коррекции.