Уважаемые друзья и коллеги!
От всего сердца поздравляю Вас с наступающим Новым 2024 годом и Рождеством!
Пусть наступающий новый год будет для Вас удачным и плодотворным, годом перемен и новых возможностей и достижений, наполненным яркими событиями и добрыми делами!
Искренне желаю Вам стабильности, неиссякаемой энергии, оптимизма, уверенности в своих делах и силе духа исполнения всего самого заветного.
Пусть Вам во всем сопутствует успех и удача!
Доброго здоровья Вам и Вашим близким, семейного счастья и благополучия!
Сегодняшняя статья является продолжением цикла статей, посвященных АСУ «ТОиР оборудования с ЧПУ».
Мне, проработавшему более 40 лет в сфере ТОиР оборудования с ЧПУ, из них более 20 лет начальником Технического центра ТОиР оборудования с ЧПУ крупного машиностроительного предприятия, есть, что Вам рассказать.
Начну я статью с определения, что такое техническое состояние оборудования.
Техническое состояние оборудования с ЧПУ - это состояние оборудования в определенный момент времени, при определённых условиях внешней среды, характеризующееся фактическими значениями параметров, установленных в технической документации.
В зависимости от технического состояния оборудования проводятся следующие работы по ТОиР:
Техническое обслуживание оборудования с ЧПУ
Технический обслуживание — это мероприятие, выполняемое с целью наблюдения за техническим состоянием оборудования и проведения мелкого ремонта.
Техническое освидетельствование - это наружный и внутренний осмотр оборудования, испытание и контроль технологической точности (обычно проводится 2 раза в год), проводимые в срок и объемах в соответствии с требованиями технической документации, в том числе нормативных актов и технических регламентов, с целью определения его технического состояния и возможности дальнейшей эксплуатации.
Техническое диагностирование - это комплекс операций по определению технического состояния узлов оборудования и прогнозированию их изменений, которые включают установление категории, выявление неисправностей и других отклонений, влияющих на работу узлов и оборудования в целом, а также причин их возникновения.
Диагностика технического состояния узлов оборудования
Техническая диагностика — это область знаний, охватывающая теорию, методы и средства определения технического состояния узлов оборудования.
ГОСТ 20911-89. Техническая диагностика. Термины и определения.
Среди многообразия методов, используемых для диагностирования параметров технического состояния оборудования, принято различать органолептические (субъективные) и инструментальные (объективные) методы.
Органолептические методы дают качественную оценку технического состояния; существенный недостаток этих методов – субъективизм оценки и зависимость оценки от опытности специалиста, оценивающего состояние узла. Инструментальные методы обеспечивают количественную оценку параметров технического состояния и предусматривают использование специальных приборов и инструментов, диагностических устройств и контрольных приспособлений.
Достоверный диагноз и прогноз работоспособности машин и оборудования можно получить только в результате комплексного применения различных методов диагностики. При этом следует не забывать, что в большинстве случаев наиболее целесообразно, чтобы информация о параметрах технического состояния объекта была получена без его разборки.
Существуют следующие методы диагностики технического состояния узлов оборудования:
1. Субъективные (органолептические)
1.1. Визуальный осмотр.
1.2. Анализ шумов:
1.2.1. Акустическое восприятие.
Позволяет оценить наиболее значимые неисправности, которые меняют общую акустическую картину, что весьма эффективно при определении повреждений муфт, дисбалансе, ослаблении посадки деталей узлов, взаимных ударах и так далее. При этом мы наблюдаем следующие диагностические признаки:
-изменение тональности, ритма и громкости звука.
1.3. Анализ колебаний.
Механические колебания корпусов узлов при помощи технических или электронных стетоскопов преобразуются в звуковые, что позволяет расширить возможности восприятия.
1.4. Методы осязания.
Используются для оценки шероховатости, волнистости и других параметров поверхностей деталей, а также качества смазывающего материала, его вязкости, пластичности, наличия посторонних включений и т.п.
1.5. Метод восприятия вибрации.
Основан на тактильном анализе, как реакции соприкосновения с поверхностями оборудования. Значения параметров вибрации достоверно субъективно оценить нельзя - возможен лишь сравнительный анализ, в том числе на основе ранее полученного опыта. Абсолютная оценка практически всегда содержит грубые ошибки из-за различия в ощущениях и широкого спектрального состава вибрации:
1.6. Метод контроля температуры.
Основан на оценке степени нагрева поверхности корпусов узлов оборудования и различается как:
-холодное (менее +20 град. С)
-теплое (+20…+50 град. С)
-горячее (свыше +50 град. С)
Пределом для непосредственного восприятия является температура +60 град. С, которую большинство людей может выдержать без болевых ощущений тыльной стороной ладони в течении пяти секунд. Использование брызг воды позволяет распознать более высокие значения температуры:
2. Объективные (приборные)
2.1. Механический метод.
Основан на измерении геометрических размеров, зазоров в сопряжениях, давлений и скорости взаимного перемещения узлов оборудования. Применяется при оценке износа деталей, установления люфтов и зазоров в сопряжениях, давления в гидро- и пневмосистемах, сил затяжки резьбовых соединений, скорости оборота привода главного движения, приводов подач и вспомогательных приводов. Для этого используется разнообразный мерительный инструмент и приборы:
линейки, штангенциркули, шаблоны, индикаторы перемещения часового типа, динамометрические ключи, ключи предельного момента, манометры и другие.
2.2. Методы неразрушающего контроля
Данные методы используются для определения целостности деталей и узлов оборудования с помощью магнитных, вихревых, ультразвуковых, капиллярных, радиационных, радиоволновых методов неразрушающего контроля.
На нижерасположенном рисунке показаны узлы многооперационного станка, которые диагностируются методами неразрушающего контроля.
От всего сердца поздравляю Вас с наступающим Новым 2024 годом и Рождеством!
Пусть наступающий новый год будет для Вас удачным и плодотворным, годом перемен и новых возможностей и достижений, наполненным яркими событиями и добрыми делами!
Искренне желаю Вам стабильности, неиссякаемой энергии, оптимизма, уверенности в своих делах и силе духа исполнения всего самого заветного.
Пусть Вам во всем сопутствует успех и удача!
Доброго здоровья Вам и Вашим близким, семейного счастья и благополучия!
С уважением, В.И. Писарев
Сегодняшняя статья является продолжением цикла статей, посвященных АСУ «ТОиР оборудования с ЧПУ».
Мне, проработавшему более 40 лет в сфере ТОиР оборудования с ЧПУ, из них более 20 лет начальником Технического центра ТОиР оборудования с ЧПУ крупного машиностроительного предприятия, есть, что Вам рассказать.
Начну я статью с определения, что такое техническое состояние оборудования.
Техническое состояние оборудования с ЧПУ - это состояние оборудования в определенный момент времени, при определённых условиях внешней среды, характеризующееся фактическими значениями параметров, установленных в технической документации.
ГОСТ Р27.102-2021. Надежность в технике. Надежность объекта. Термины и определения.
В зависимости от технического состояния оборудования проводятся следующие работы по ТОиР:
- при хорошем состоянии оборудования проводится техническое обслуживание по регламенту,
- при удовлетворительном состоянии оборудования проводятся работы по ТОиР в соответствии с ранее намеченным планом,
- при плохом состоянии оборудования проводятся работы по его подключению к АСУ «Мониторинг с глубокой диагностикой узлов оборудования», при необходимости проводятся внеплановые ТОиР,
- при аварийном состоянии оборудования проводятся работы по его подключению к АСУ «Мониторинг с глубокой диагностикой узлов оборудования» или немедленному останову и проведению аварийного ремонта.
Техническое обслуживание оборудования с ЧПУ
Технический обслуживание — это мероприятие, выполняемое с целью наблюдения за техническим состоянием оборудования и проведения мелкого ремонта.
Техническое освидетельствование - это наружный и внутренний осмотр оборудования, испытание и контроль технологической точности (обычно проводится 2 раза в год), проводимые в срок и объемах в соответствии с требованиями технической документации, в том числе нормативных актов и технических регламентов, с целью определения его технического состояния и возможности дальнейшей эксплуатации.
Техническое диагностирование - это комплекс операций по определению технического состояния узлов оборудования и прогнозированию их изменений, которые включают установление категории, выявление неисправностей и других отклонений, влияющих на работу узлов и оборудования в целом, а также причин их возникновения.
Диагностика технического состояния узлов оборудования
Техническая диагностика — это область знаний, охватывающая теорию, методы и средства определения технического состояния узлов оборудования.
ГОСТ 20911-89. Техническая диагностика. Термины и определения.
Среди многообразия методов, используемых для диагностирования параметров технического состояния оборудования, принято различать органолептические (субъективные) и инструментальные (объективные) методы.
Органолептические методы дают качественную оценку технического состояния; существенный недостаток этих методов – субъективизм оценки и зависимость оценки от опытности специалиста, оценивающего состояние узла. Инструментальные методы обеспечивают количественную оценку параметров технического состояния и предусматривают использование специальных приборов и инструментов, диагностических устройств и контрольных приспособлений.
Достоверный диагноз и прогноз работоспособности машин и оборудования можно получить только в результате комплексного применения различных методов диагностики. При этом следует не забывать, что в большинстве случаев наиболее целесообразно, чтобы информация о параметрах технического состояния объекта была получена без его разборки.
Существуют следующие методы диагностики технического состояния узлов оборудования:
1. Субъективные (органолептические)
1.1. Визуальный осмотр.
1.2. Анализ шумов:
1.2.1. Акустическое восприятие.
Позволяет оценить наиболее значимые неисправности, которые меняют общую акустическую картину, что весьма эффективно при определении повреждений муфт, дисбалансе, ослаблении посадки деталей узлов, взаимных ударах и так далее. При этом мы наблюдаем следующие диагностические признаки:
-изменение тональности, ритма и громкости звука.
1.3. Анализ колебаний.
Механические колебания корпусов узлов при помощи технических или электронных стетоскопов преобразуются в звуковые, что позволяет расширить возможности восприятия.
1.4. Методы осязания.
Используются для оценки шероховатости, волнистости и других параметров поверхностей деталей, а также качества смазывающего материала, его вязкости, пластичности, наличия посторонних включений и т.п.
1.5. Метод восприятия вибрации.
Основан на тактильном анализе, как реакции соприкосновения с поверхностями оборудования. Значения параметров вибрации достоверно субъективно оценить нельзя - возможен лишь сравнительный анализ, в том числе на основе ранее полученного опыта. Абсолютная оценка практически всегда содержит грубые ошибки из-за различия в ощущениях и широкого спектрального состава вибрации:
- в высокочастотном диапазоне возможности человека по восприятию вибрации крайне ограничены,
- в низкочастотном диапазоне возможности человека по восприятию вибрации существенно различаются в зависимости от индивидуальных особенностей восприятия и уровня подготовки специалиста.
1.6. Метод контроля температуры.
Основан на оценке степени нагрева поверхности корпусов узлов оборудования и различается как:
-холодное (менее +20 град. С)
-теплое (+20…+50 град. С)
-горячее (свыше +50 град. С)
Пределом для непосредственного восприятия является температура +60 град. С, которую большинство людей может выдержать без болевых ощущений тыльной стороной ладони в течении пяти секунд. Использование брызг воды позволяет распознать более высокие значения температуры:
- +70 град. С - видимое испарение пятен воды
- +100 град. С - кипение воды внутри капли.
2. Объективные (приборные)
2.1. Механический метод.
Основан на измерении геометрических размеров, зазоров в сопряжениях, давлений и скорости взаимного перемещения узлов оборудования. Применяется при оценке износа деталей, установления люфтов и зазоров в сопряжениях, давления в гидро- и пневмосистемах, сил затяжки резьбовых соединений, скорости оборота привода главного движения, приводов подач и вспомогательных приводов. Для этого используется разнообразный мерительный инструмент и приборы:
линейки, штангенциркули, шаблоны, индикаторы перемещения часового типа, динамометрические ключи, ключи предельного момента, манометры и другие.
2.2. Методы неразрушающего контроля
Данные методы используются для определения целостности деталей и узлов оборудования с помощью магнитных, вихревых, ультразвуковых, капиллярных, радиационных, радиоволновых методов неразрушающего контроля.
На нижерасположенном рисунке показаны узлы многооперационного станка, которые диагностируются методами неразрушающего контроля.
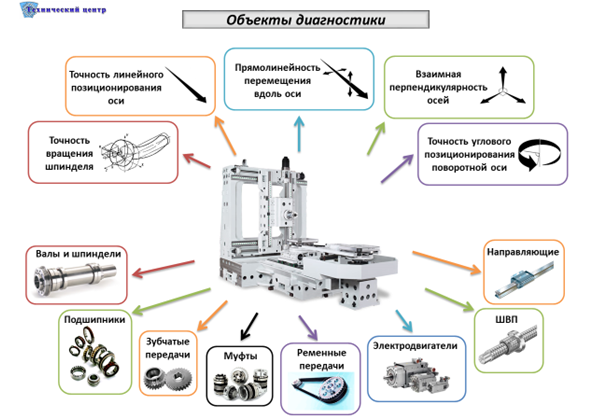
На нижерасположенном рисунке показана блок-схема классификации средств технической диагностики.
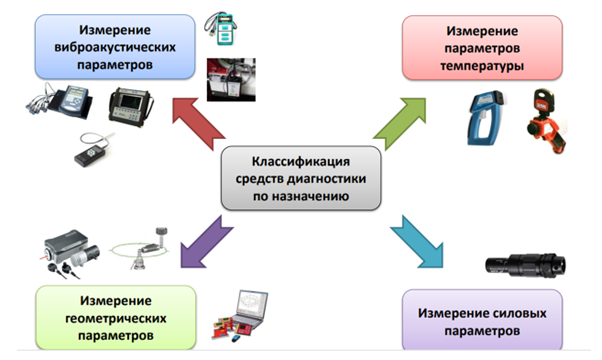
На нижерасположенном рисунке я показываю таблицу применяемых методов контроля и диагностики при отклонениях параметров станка во время его эксплуатации.
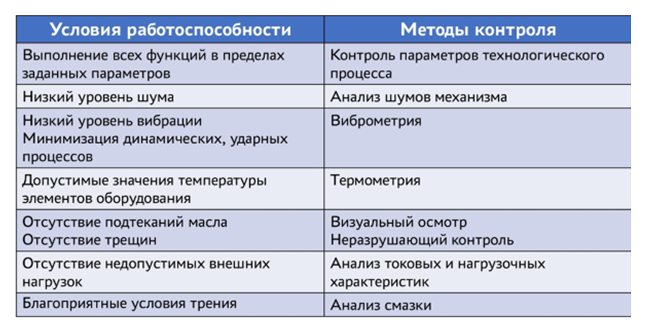
2.2.1. Виброакустические методы (виброметрия).
Базируется на измерении упругих колебаний, которые распространяются в результате соударения деталей узлов оборудования.
Область применения:
-оценка и контроль механических колебаний,
-определение, распознавание и мониторинг развития неисправностей в узлах оборудования. Для этого используются шумомеры, виброметры, спектроанализаторы параметров виброакустических сигналов.
Широкие возможности вибродиагностики позволяют использовать ее для определения технического состояния узлов оборудования, определения объема ремонтных работ и контроля качества ремонта.
На нижерасположенном рисунке показаны диагностируемые детали и узлы привода главного
движения станка методом вибродиагностики.
Базируется на измерении упругих колебаний, которые распространяются в результате соударения деталей узлов оборудования.
Область применения:
-оценка и контроль механических колебаний,
-определение, распознавание и мониторинг развития неисправностей в узлах оборудования. Для этого используются шумомеры, виброметры, спектроанализаторы параметров виброакустических сигналов.
Широкие возможности вибродиагностики позволяют использовать ее для определения технического состояния узлов оборудования, определения объема ремонтных работ и контроля качества ремонта.
Нормативная база
- ГОСТ 24346-80. Вибрация. Контроль. Термины и определения.
- ГОСТ Р ИСО 10816-1-97. Вибрация. Контроль состояния машин по результатам измерений вибрации на не вращающихся частях. Часть 1. Общие требования.
- ГОСТ Р ИСО 10816-3-2002. Вибрация. Контроль состояния машин по результатам измерений вибрации на не вращающихся частях. Часть 3. Промышленные машины номинальной мощностью более 15 кВт и номинальной скоростью от 120 до 15000 оборотов в минуту.
- ГОСТ ИСО 10817-1-2002. Вибрация. Системы измерений вибрации вращающихся валов. Часть 1. Устройства для снятия сигналов относительной и абсолютной вибрации.
- ГОСТ ИСО 7919 1-2002 Вибрация. Контроль состояния машин по результатам измерений вибрации на вращающихся валах. Общие требования.
- ГОСТ ИСО 5348-2002. Вибрация и удар. Механическое крепление акселерометров.
- ГОСТ ИСО 8579-2-2002. Вибрация. Контроль вибрационного состояния зубчатых механизмов при
- приемке.
На нижерасположенном рисунке показаны диагностируемые детали и узлы привода главного
движения станка методом вибродиагностики.
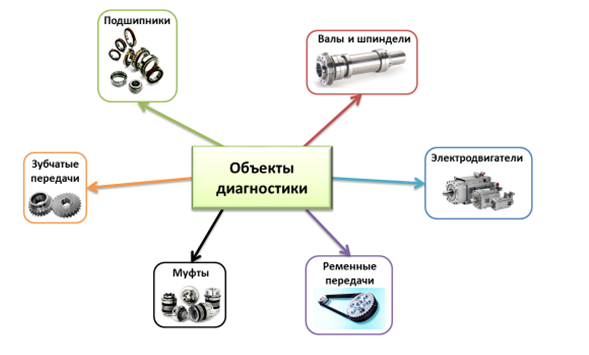
2.2.2. Тепловой метод (термометрия)
Основан на измерении температурных параметров диагностируемого узла оборудования. С помощью термометрии определяют деформации, вызываемые неравномерностью нагрева узлов оборудования, технического состояния подшипниковых узлов, смазочных систем, тормозов, муфт и т.д. Для этого используют: термосопротивления, термометры, термопары, термоиндикаторы, пирометры, тепловизоры и т.д.
Измерение температуры производится бесконтактными средствами измерения. Температура измеряется на корпусе шпиндельного узла в точках измерения, расположенных возле передней и задней опоры шпинделя. Так же, при необходимости, измеряется температура электродвигателей, насосов гидростанций. Полученные значения сравниваются с рекомендованными допустимыми значениями.
Использование тепловизионной диагностики позволяет оперативно определить локализацию дефекта как механических узлов оборудования, так и его электронных компонентов.
2.2.3. Методы анализа смазки.
Заключается в определении вида и количества продуктов износа в масле, для этого применяются следующие методы: колориметрический, полярографический, магнитно-индукционный, радиоактивный и спектрографический.
2.2.4. Электрические методы.
Подразумевают измерение силы тока, напряжения, сопротивления, мощности и других параметров электросистемы оборудования. К средствам реализации электрических методов реализации относятся: амперметры, вольтметры, измерительные мосты, датчики (перемещения, крутящего момента, давления и другие), тахогенераторы и т.п.
2.2.5. Методы измерения геометрии станка.
2.2.5.1. Метод измерения точности позиционирования узлов станка по линейным и круговым координатам с использованием лазерных интерферометров, согласно ISO 230-2 (ГОСТ 27813-2006).
Основан на измерении температурных параметров диагностируемого узла оборудования. С помощью термометрии определяют деформации, вызываемые неравномерностью нагрева узлов оборудования, технического состояния подшипниковых узлов, смазочных систем, тормозов, муфт и т.д. Для этого используют: термосопротивления, термометры, термопары, термоиндикаторы, пирометры, тепловизоры и т.д.
Измерение температуры производится бесконтактными средствами измерения. Температура измеряется на корпусе шпиндельного узла в точках измерения, расположенных возле передней и задней опоры шпинделя. Так же, при необходимости, измеряется температура электродвигателей, насосов гидростанций. Полученные значения сравниваются с рекомендованными допустимыми значениями.
- Предельная допустимая температура наружного кольца подшипника – 65°С.
- Предельная допустимая температура переднего торца шпинделя при максимальной скорости вращения – 50°С.
- Предельная допустимая температура обмотки статора электродвигателя – 130°С.
Использование тепловизионной диагностики позволяет оперативно определить локализацию дефекта как механических узлов оборудования, так и его электронных компонентов.
2.2.3. Методы анализа смазки.
Заключается в определении вида и количества продуктов износа в масле, для этого применяются следующие методы: колориметрический, полярографический, магнитно-индукционный, радиоактивный и спектрографический.
2.2.4. Электрические методы.
Подразумевают измерение силы тока, напряжения, сопротивления, мощности и других параметров электросистемы оборудования. К средствам реализации электрических методов реализации относятся: амперметры, вольтметры, измерительные мосты, датчики (перемещения, крутящего момента, давления и другие), тахогенераторы и т.п.
2.2.5. Методы измерения геометрии станка.
2.2.5.1. Метод измерения точности позиционирования узлов станка по линейным и круговым координатам с использованием лазерных интерферометров, согласно ISO 230-2 (ГОСТ 27813-2006).
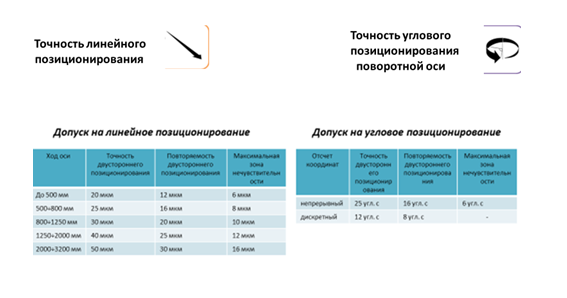
2.2.5.2. Метод диагностики по параметрам точности и постоянства отработки круговой траектории.
ISO 230-4 (ГОСТ30544-97)
ISO 230-4 (ГОСТ30544-97)

2.2.6. Метод определения уровня шума. ISO 230-5 (ГОСТ ИСО-230-5-2002).
Допустимый уровень шума приводится в паспорте станка, либо определяется по ГОСТ 12.2.107-85.
Допустимый уровень шума в зависимости от модели станка не должен превышать 84-102 ДБА.
Средства технической диагностики подразделяются на:
-портативные,
-встроенные (стационарные) системы.
Портативные средства
Виброметры
Простейший виброметр модели BALTECH VP 3410 предназначен для предварительной оперативной диагностики по общему уровню вибрации. Использование виброметра обеспечивает диагностику технического состояния оборудования на первом уровне силами работников ремонтных бюро. Сотрудники ремонтного бюро с помощью виброметров измеряют следующие параметры:
Допустимый уровень шума приводится в паспорте станка, либо определяется по ГОСТ 12.2.107-85.
Допустимый уровень шума в зависимости от модели станка не должен превышать 84-102 ДБА.
Средства технической диагностики подразделяются на:
-портативные,
-встроенные (стационарные) системы.
Портативные средства
- реализуют измерения одного или нескольких диагностических параметров,
- характеризуются малыми габаритными размерами и нередко отсутствием возможности обмена данными с компьютерными системами
- быстрота процесса измерения,
- простое управление и обслуживание,
- оперативное и наглядное получение информации,
- относительно низкая стоимость.
Виброметры
Простейший виброметр модели BALTECH VP 3410 предназначен для предварительной оперативной диагностики по общему уровню вибрации. Использование виброметра обеспечивает диагностику технического состояния оборудования на первом уровне силами работников ремонтных бюро. Сотрудники ремонтного бюро с помощью виброметров измеряют следующие параметры:
- Среднее Квадратическое Значение (СКЗ) виброскорости в диапазоне частот 10-1000 Гц,
- СКЗ виброускорения в диапазоне частот 10-1000 Гц,
- СКЗ виброперемещения в диапазоне частот 10-1000 Гц.
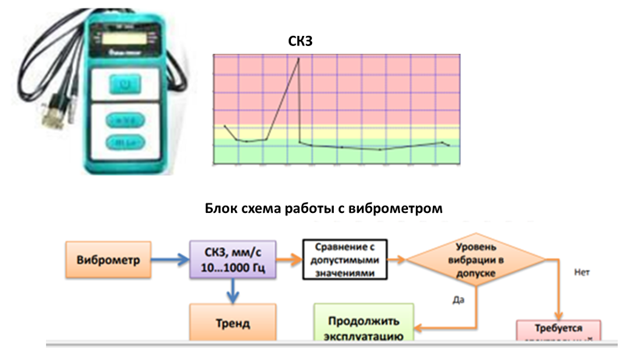
Виброанализаторы модели "КВАРЦ" и "ОНИКС"
Виброанализаторы данной модели предназначены для детальной спектральной диагностики узлов оборудования. Использование виброанализаторов обеспечивает вибродиагностику технического состояния узлов оборудования на втором уровне, проводимую силами работников бюро диагностики. Сотрудники бюро диагностики с помощью виброанализаторов измеряют следующие параметры:
-временную форму сигнала,
-прямой спектр сигнала,
-спектр огибающей,
-разбалансировку вала в собственных опорах,
-орбиты при использовании 2-х канальных анализаторов.
Виброанализаторы данной модели предназначены для детальной спектральной диагностики узлов оборудования. Использование виброанализаторов обеспечивает вибродиагностику технического состояния узлов оборудования на втором уровне, проводимую силами работников бюро диагностики. Сотрудники бюро диагностики с помощью виброанализаторов измеряют следующие параметры:
-временную форму сигнала,
-прямой спектр сигнала,
-спектр огибающей,
-разбалансировку вала в собственных опорах,
-орбиты при использовании 2-х канальных анализаторов.
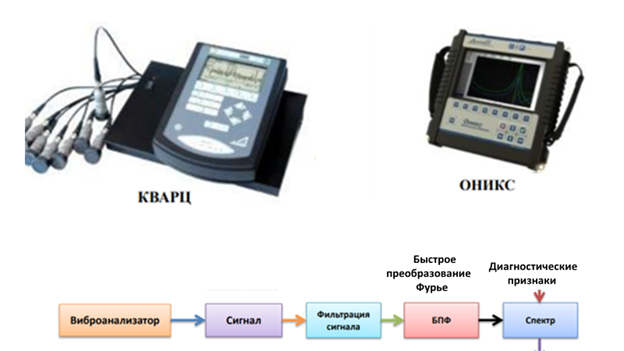
Анализаторы применяются для сбора и предварительного анализа полученных данных для последующей передачи их в компьютер. С помощью компьютера и специального программного обеспечения мы проводим глубокие исследования, анализируем тренды работы узлов оборудования, выявляем неисправности на ранней стадии их развития и т.д.
Использование анализаторов оправдано при специализации процессов оценки технического состояния узлов оборудования и наличии квалифицированных специалистов, что позволяет качественно проводить измерения и последующий анализ полученных измерений.
Совместное использование спектральных анализаторов вибрации и тепловизоров позволяет решать широкий круг задач при выполнении работ по ТОиР оборудования.
Использование анализаторов оправдано при специализации процессов оценки технического состояния узлов оборудования и наличии квалифицированных специалистов, что позволяет качественно проводить измерения и последующий анализ полученных измерений.
Совместное использование спектральных анализаторов вибрации и тепловизоров позволяет решать широкий круг задач при выполнении работ по ТОиР оборудования.
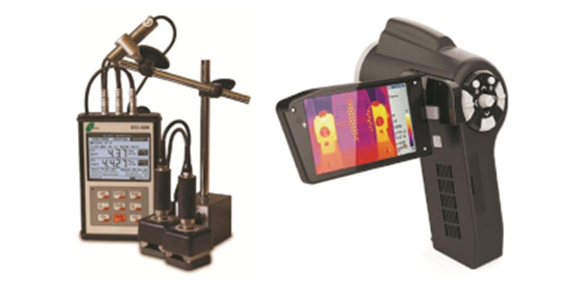
Системы мобильной диагностики технического состояния узлов оборудования модели Monotonic Spectra Pluse
Система мобильной диагностики технического состояния узлов оборудования модели Monotonic Spectra Pluse предназначена для измерения в реальном режиме времени сигналов виброускорения одновременно по трем взаимно перпендикулярным направлениям с возможностью проведения спектрального анализа.
Система мобильной диагностики технического состояния узлов оборудования модели Monotonic Spectra Pluse предназначена для измерения в реальном режиме времени сигналов виброускорения одновременно по трем взаимно перпендикулярным направлениям с возможностью проведения спектрального анализа.
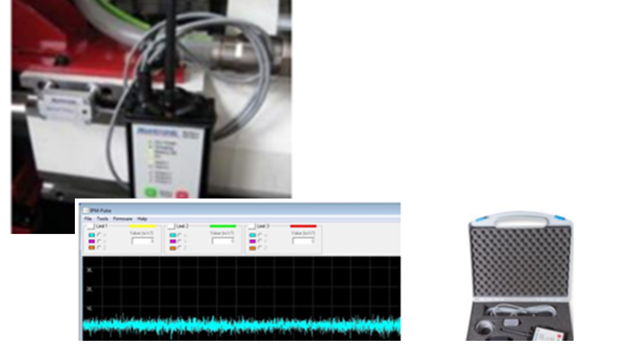
Шумомеры
Шумомер модели 110 предназначен для определения шумовых характеристик по ГОСТ ИСО 230-5-2002.
Шумомер модели 110 предназначен для определения шумовых характеристик по ГОСТ ИСО 230-5-2002.
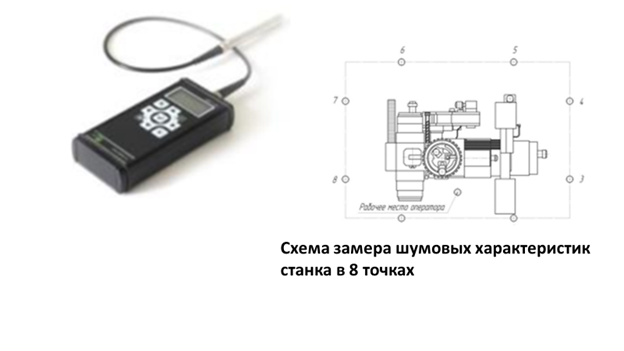
Тепловизоры
Тепловизор модели Helfand предназначен для измерения температуры поверхности корпусов узлов станков и определения источника выделения тепла путем инфракрасной съемки поверхности, с получением значений температуры сразу в нескольких точках и получением термограммы поверхности.
Тепловизор модели Helfand предназначен для измерения температуры поверхности корпусов узлов станков и определения источника выделения тепла путем инфракрасной съемки поверхности, с получением значений температуры сразу в нескольких точках и получением термограммы поверхности.
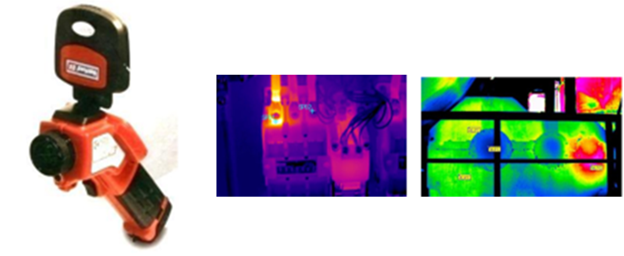
Пирометры
Пирометр модели BALTECH TI.0208 предназначен для удаленного измерения температуры поверхности узлов оборудования. Обычные термометры должны находиться непосредственно в зоне измерения температуры, а пирометр способен определить нагрев на расстоянии.
Принцип работы основан на инфракрасном излучении. Чем горячее поверхность, тем больше ИК-лучей она выделяет. Специальный датчик пирометра считывает инфракрасное излучение и передает данные на микропроцессор.
Пирометр модели BALTECH TI.0208 предназначен для удаленного измерения температуры поверхности узлов оборудования. Обычные термометры должны находиться непосредственно в зоне измерения температуры, а пирометр способен определить нагрев на расстоянии.
Принцип работы основан на инфракрасном излучении. Чем горячее поверхность, тем больше ИК-лучей она выделяет. Специальный датчик пирометра считывает инфракрасное излучение и передает данные на микропроцессор.
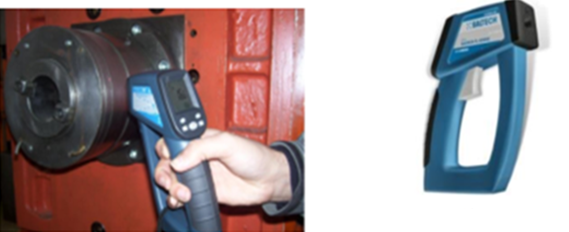
Электронные уровни
При помощи электронных уровней осуществляется экспертная проверка геометрической точности станков с ЧПУ.
На нижерасположенном рисунке показана схема измерения прямолинейности осей, взаимной перпендикулярности осей и плоскостности поверхностей станка электронным уровнем модели WYLER Blue LEVEL.
При помощи электронных уровней осуществляется экспертная проверка геометрической точности станков с ЧПУ.
На нижерасположенном рисунке показана схема измерения прямолинейности осей, взаимной перпендикулярности осей и плоскостности поверхностей станка электронным уровнем модели WYLER Blue LEVEL.
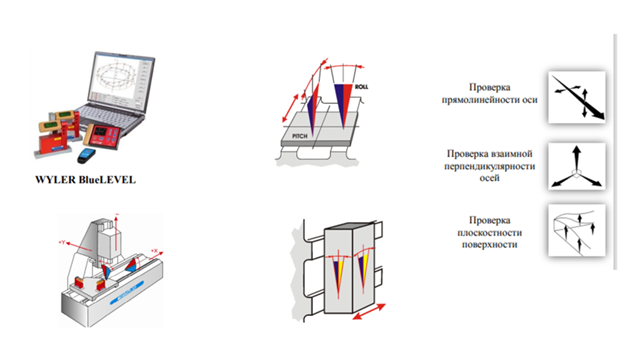
Стенд входного контроля подшипников

Системы Balbar
При помощи системы Balbar QC-10 и QC-20 производства фирмы Renishaw осуществляем оценку точности и постоянства отработки круговой траектории станка с ЧПУ при круговой интерполяции с возможностью количественного определения следующих отклонений:
-рассогласование приводов,
-определение люфтов в ШВП,
-определение люфтов в направляющих,
-определение отклонений от перпендикулярности,
-определение отклонений от прямолинейности.
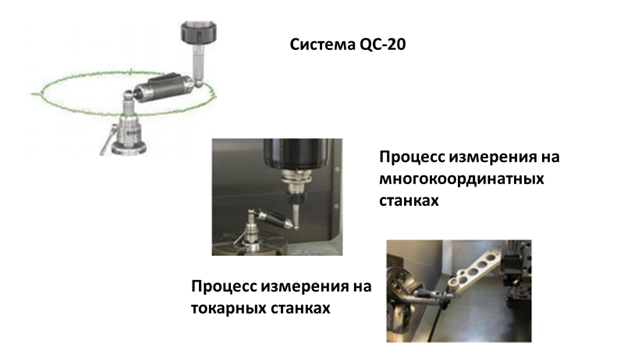
На нижерасположенном рисунке я показываю результаты работы формообразующих узлов станка с рассогласованными приводами и после их настройки.
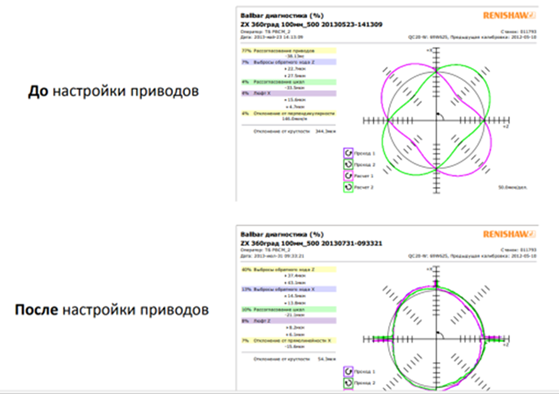
Лазерные интерферометры
Лазерный интерферометр модели XL-80 производства фирмы Renishaw.
Лазерный интерферометр модели XL-80 производства фирмы Renishaw.
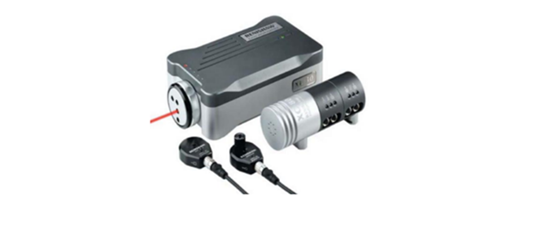
При помощи лазерного интерферометра модели XL-80 осуществляется комплексная проверка геометрической точности и точности позиционирования станков с ЧПУ и координатно-измерительных машин, с возможностью автоматического формирования параметров компенсации в УЧПУ.
На нижерасположенном рисунке показаны основные проверки геометрической точности станков, проводимых с помощью системы XL-80.
На нижерасположенном рисунке показаны основные проверки геометрической точности станков, проводимых с помощью системы XL-80.
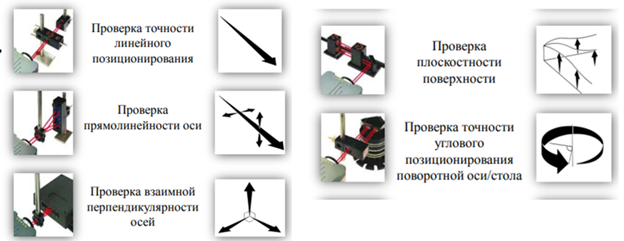
Система лазерной выверки объемной геометрической точности крупногабаритных станков с ЧПУ
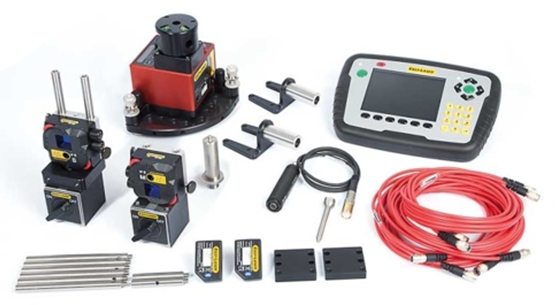
Встроенные (стационарные) системы
Встроенные системы мониторинга с глубокой диагностикой технического состояния узлов оборудования с ЧПУ обеспечивают контроль за техническим состоянием узлов оборудования и для защиты его от ненормальных режимов работы, предупреждения быстроразвивающихся де градационных процессов, раннего выявления неисправностей и решения других задач.
Недостатки: главным недостатком является высокая стоимость (аппаратная часть + программное обеспечение + техническая поддержка), что ограничивает их использование на многих предприятиях.
На нижерасположенном рисунке показана блок-схема АСУ «Мониторинг с глубокой диагностикой технического состояния узлов оборудования».
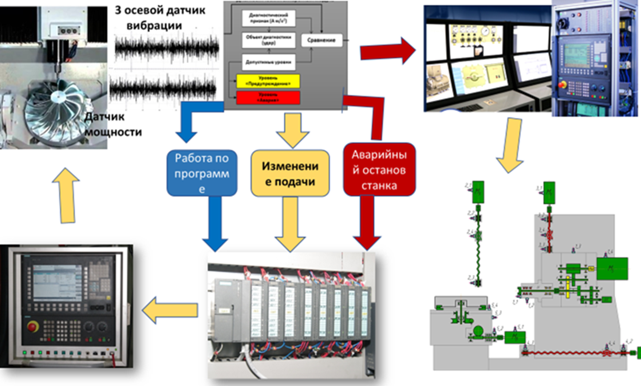
В настоящее время конвергенция современных инновационных технологий ТОиР оборудования открывает новые перспективы для более точной оценки технического состояния узлов оборудования, прогнозирования их изменений и решения задачи оптимальных сроков и объемов работ по ТОиР оборудования.
На этом я заканчиваю очередную статью из цикла АСУ «ТОиР оборудования с ЧПУ». До новых встреч.
При написании статьи использовались материалы собственных статей и презентаций, ранее опубликованных в открытой печати и интернете.
На этом я заканчиваю очередную статью из цикла АСУ «ТОиР оборудования с ЧПУ». До новых встреч.
При написании статьи использовались материалы собственных статей и презентаций, ранее опубликованных в открытой печати и интернете.