Данную статью, как и все предыдущие, я использую прежде всего для передачи полученного опыта за 40 лет работы в сфере ТОиР оборудования с ЧПУ на одном из ведущих предприятий России, а также для того, чтобы поделиться с Вами подходами, применяемыми мной для решения возникающих проблем. Цель всех моих статей – это актуализировать задачи и вызовы современности в области дальнейшего развития служб ТОиР оборудования с ЧПУ на предприятиях России, как основного двигателя повышения эффективности работы оборудования.
Как я уже писал в предыдущих частях цикла статей, посвященного теме: «Автоматизированные системы против столкновения шпинделя с узлами станков с ЧПУ», в период с 2000 по 2010 годы на предприятии остро встала проблема минимизации последствий от столкновений шпинделей с узлами станков, заготовками, приспособлениями. В связи с этим, руководством предприятия перед работниками Технического центра была поставлена задача решить эту проблему. В то время на рынок России стали выходить системы против столкновения, разработанные фирмами Марпос, Montronix, Omative, IFM electronic, Prometec, Brankamp, SKF, ВИСОМ, ДИАМЕХ. При реализации проекта "АСУ мониторинг" мы решили данную проблему с использованием контроллеров IFM и разработанным по нашему техническому заданию АО ВИСОМ контролером ВС 357, систем против столкновений Montronix и Omative, ATRIS.
Проведя детальный анализ и ознакомившись с производством, мы остановились на системах Montronix, Omative, ATRIS, контроллерах IFM VSE 100, ВИСОМ ВС 357.
Любой станок с ЧПУ имеет систему защиты шпинделя от столкновения (есть возможности управлять защитой шпинделя от столкновений без применения сторонних систем контролем столкновения. Это происходит по токовому контуру). На любом станке есть 3 контура защиты:
- токовый
- позиционный
- скоростной.
По токовому контуру столкновение можно фиксировать, если вы занимаетесь мониторингом силы тока на приводе главного движения. Но беда здесь в одном: токовый контур реакцию на превышение тока выдает достаточно долго (0,6-1,0 сек). Это только по перегрузке + механическое торможение.
Специалисты вышеуказанных фирм-изготовителей систем защиты поставили перед собой задачу создать систему против столкновения шпинделя, которая по времени реакции будет опережать защиту шпинделя по токовому контуру, выдавая сигналы на аварийный останов станка быстрее, чем токовый контур. Системы данного рода только выдают сигнал на аварийную остановку станка. Но как быстро остановится станок зависит от множества факторов (оптимизации приводов, от технического состояния элементов кинематики станка).
Как видим из предоставленного графика работы существующих комплексных автоматизированных систем защиты шпинделей от столкновений и мониторинга технического состояния узлов станков с ЧПУ с элементами адаптивного управления, время реакции на возникновения столкновения и остановки станка, оснащенного системой защиты составляет до 22 мсек.
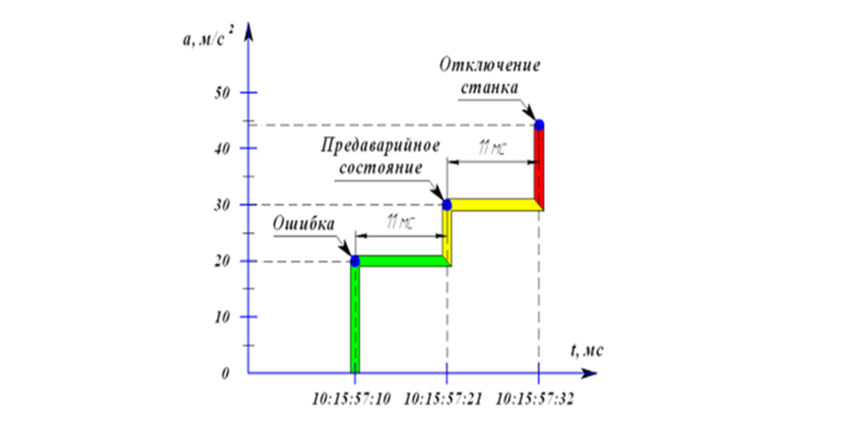
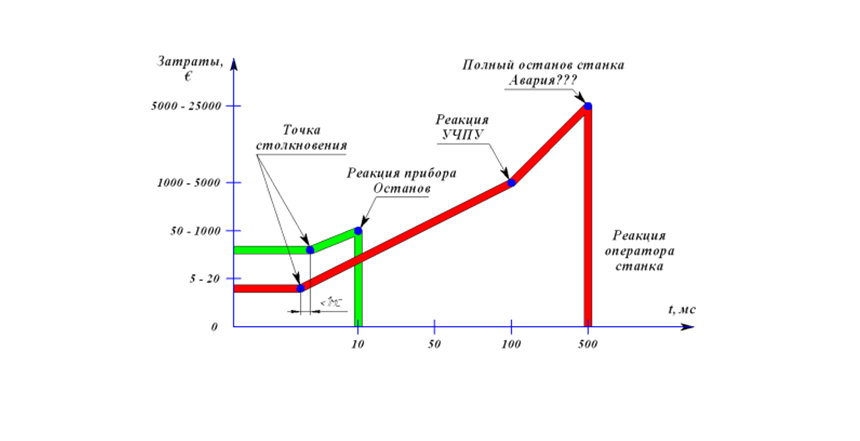
При неиспользовании системы защиты от столкновений шпинделя мы имеем максимальные финансовые потери по причине времени реакции на аварийный останов, равного 500 мсек и более.
Автоматизированные системы против столкновения шпинделя станков с ЧПУ
На нижерасположенном рисунке я привожу обзор существующих комплексных автоматизированных систем защиты шпинделей от столкновений и мониторинга технического состояния узлов станков с ЧПУ с элементами адаптивного управления.
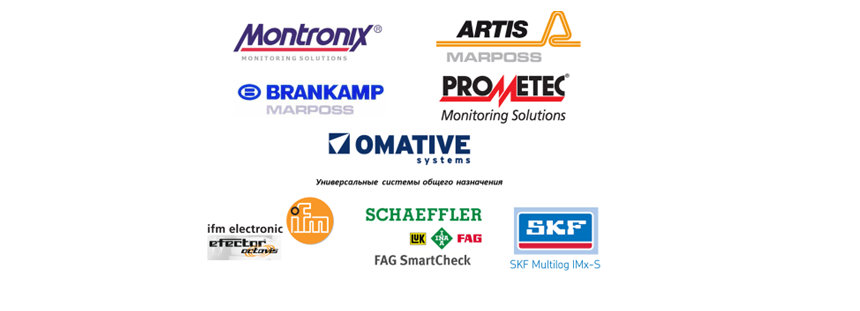
Система противоаварийной защиты и мониторинга станочного оборудования MONTRONIX
- И первой такой системой стала система защиты станка с ЧПУ от аварий и перегрузок MONTRONIX,обеспечивающая:
- защиту станочного оборудования от столкновения
- мониторинг технологического процесса и возможность его оптимизации
- диагностику состояния узлов станочного оборудования.
В комплект системы MONTRONIX входят:
-блок управления и обработки данных
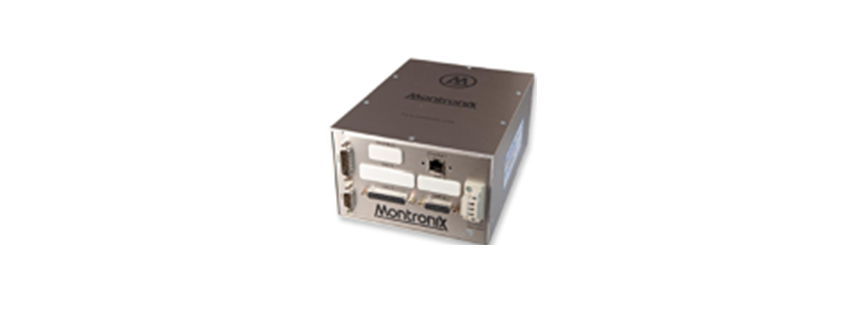
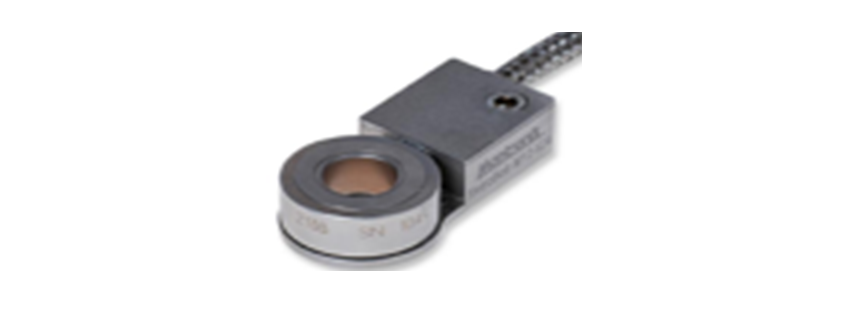
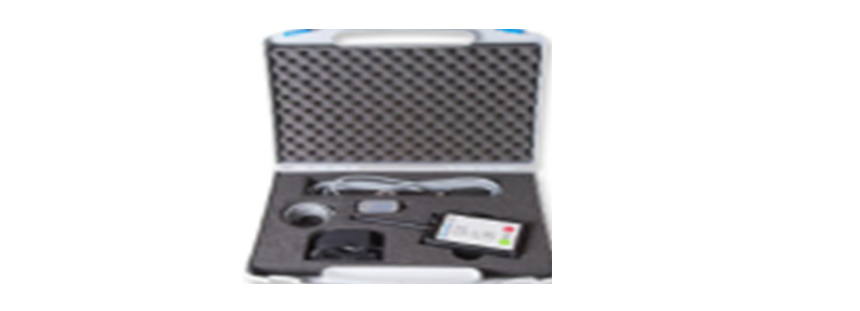
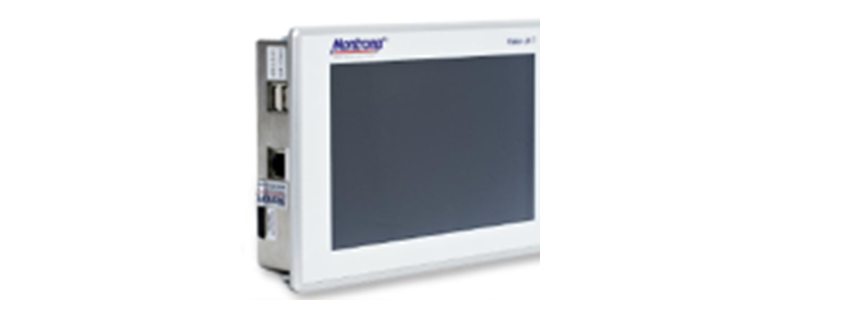
Возможности системы
В процессе эксплуатации на предприятии систем MONTRONIX на протяжении более 15 лет специалисты Технического центра с их помощью научились определять:
- техническое состояние формообразующих узлов станков, которые приведены на нижеизображенном рисунке
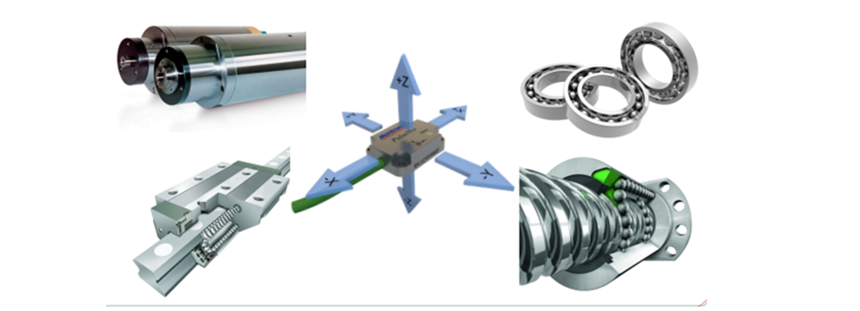
-состояние шарико-винтовых пар
-состояние смазки
-ошибки в настройке сервоприводов
-неровности станины / направляющих станка (предварительно)
-состояние кабельной цепи станка
-состояние крепления направляющих, кареток
-состояния фундамента
-повреждения станины и элементов корпуса станка
-динамические прогибы узлов станка.
В процессе эксплуатации системы MONTRONIX специалисты Технического центра минимизировали потери от столкновений шпинделя с заготовкой и узлами станков за счет применения систем защиты.
Причинами столкновений шпинделя с заготовкой и узлами станков в основном является человеческий фактор, неправильный выбор управляющей программы, неправильный выбор направления подачи, неправильная заготовка и инструмент, ошибка программирования, неправильные параметры/корректировки, ошибки заготовки или инструмента, ошибка позиционирования, ошибка установки и закрепления заготовки.
Например, в шпиндель станка установлен некорректный инструмент (торцевая фреза вместо зенкера. Тогда мы будем наблюдать следующий процесс работы системы против столкновения, показанной на нижерасположенной картинке.
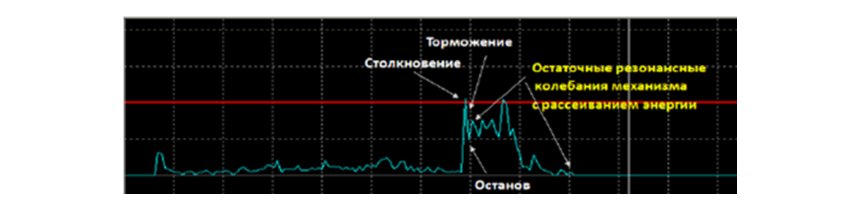
- Подвод инструмента сопровождается малой амплитудой вибрации корпуса шпинделя.
- Столкновение, начальный контакт инструмента с заготовкой сопровождается увеличением амплитуды вибрации корпуса шпинделя.
- Система реагирует на аномальный рост сил резания, сопровождающийся резким ростом амплитуды вибрации корпуса шпинделя и выдает команду на торможение подачи. При этом обнаруживается возможность статического и динамического столкновения шпинделя с заготовкой.
- Происходит полное разрушение инструмента, сопровождающегося повышенной амплитудой вибрации корпуса шпинделя из-за врезания шпинделя в заготовку.
- Происходит аварийный останов электрического двигателя подачи по току.
- Происходит движение шпинделя по инерции с остаточными колебаниями узлов станка с рассеиванием энергии.
На нижерасположенном рисунке показана блочная схема работы системы защиты шпинделя от столкновения.
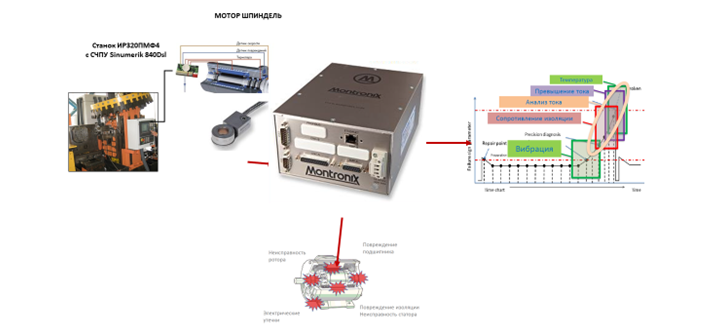
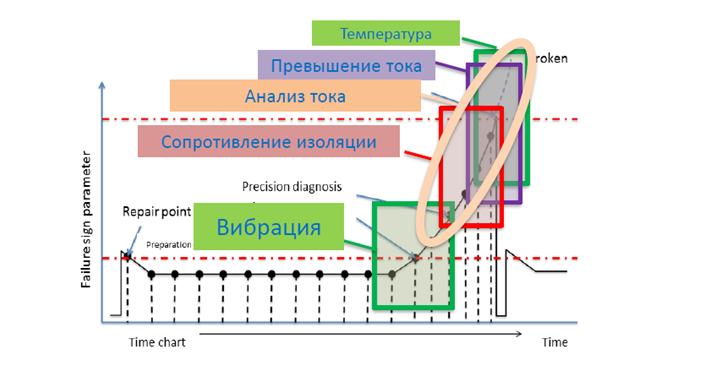
-до выхода из строя режущего инструмента и столкновения шпинделя с заготовкой,
-в момент выхода из строя инструмента,
-в момент столкновения шпинделя с заготовкой,
-в момент торможения подачи.
В процессе эксплуатации системы MONTRONIX специалисты Технического центра определяли следующие неисправности станков с ЧПУ.
Определение люфта ШВП и ослабления направляющих
На нижерасположенном рисунке я показываю виброхарактеристику перемещения одной из осей станка.
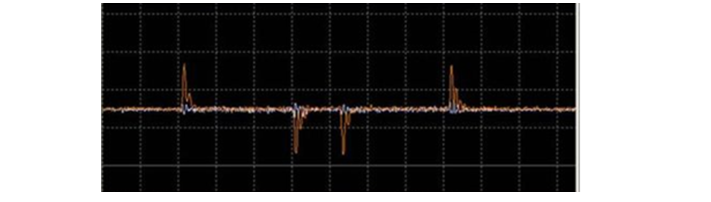
Оптимизация процесса обработки для решения проблем точности обработки
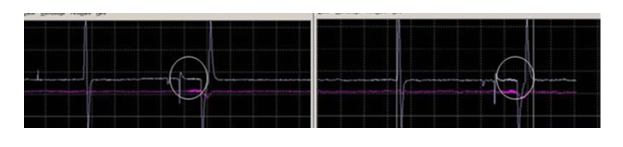
Оптимизация процесса точения
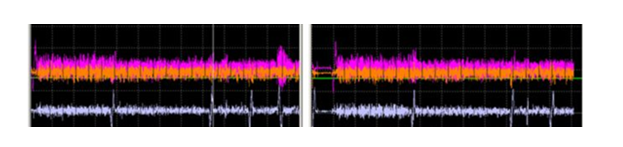
Отслеживание сбоев
Система в реальном режиме работы станка способна:
- быстро отслеживать сбои со встроенным или мобильным оборудованием для мониторинга и диагностики технического состояния узлов станка.
- для получения достоверной информации о проблемах станка устанавливать датчики в разных местах.
- исключить погрешности измерения, используя трех осевой датчик ускорения Montronix.
- пользоваться инструментарием для удаленной диагностики технического состояния узлов станка.
Определение наличия смазки
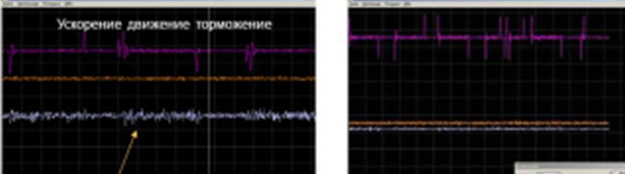
1. С наличием смазки.
2. Отсутствием смазки.
3. С выравниванием (встречается в основном после ремонта).
На картинке, расположенной справа мы наблюдем виброхарактеристики, полученные во время движения по одной из координат после смазывания направляющих станка, так как после осмотра направляющие оказались сухими.
Определение смазки шпинделя
На нижерасположенных рисунках показаны виброхарактеристики работы шпинделя станка с недостаточным количеством смазки (рисунок слева) и достаточным количеством смазки (рисунок справа).
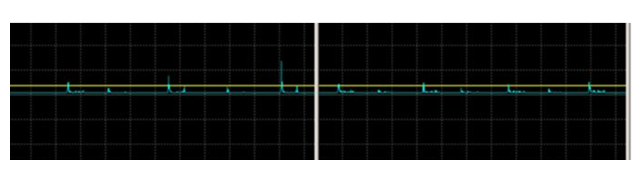
Определение состояние передачи Винт-Гайка
На нижерасположенных рисунках
-слева показаны виброхарактеристики работы передачи винт-гайка при перемещении исполнительного органа станка туда и обратно с повышенной вибрацией по одной оси. Обычно причиной такой проблемы являются неисправности в сервоприводе или отсутствия смазки направляющих. Если вибрации видны на двух осях, то это может означать рассогласованность сервоприводов.
-справа показаны виброхарактеристики работы передачи винт-гайка при перемещении исполнительного органа станка туда и обратно с повышенной вибрацией по всем трем осям. Обычно это бывает при неисправности ШВП. Если вибрации по всей длине, то проблемы с подшипниками. Если вибрации в нескольких отрезках, то проблемы в винте.
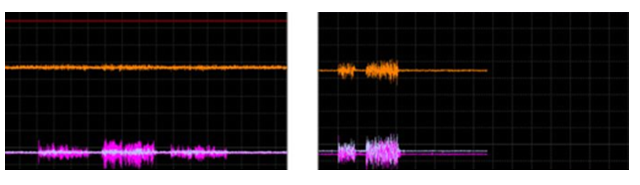
Определение состояния подшипников шпинделя
На нижерасположенных рисунках мы видим виброхарактеристики двух идентичных шпинделей.
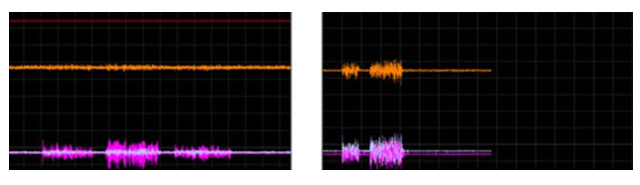
Определение плохого крепления оправок
На нижерасположенных рисунках показаны результаты тестов с балансировочной оправкой при вращении шпинделя 1500 об/мин. С хорошим креплением оправки (рисунок верхний) и со стружкой размером 30 микрометров в зоне крепления оправки (рисунок нижний).
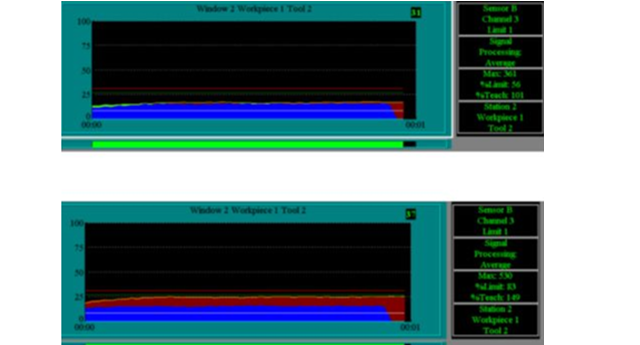
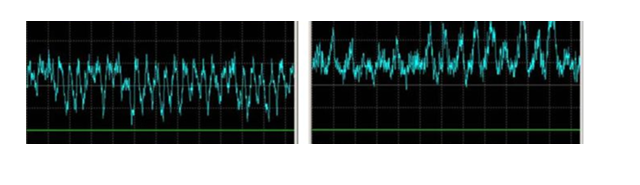
- наличия стружки на инструменте и на инструментальной оправке в зоне крепления,
- неверно установленного инструмента,
- неверно установленной заготовки.
Определение неисправностей в формообразующих узлах станков с ЧПУ при подаче 10 м/мин.
На нижерасположенном рисунке показаны виброхарактеристики, полученные в ходе эксперимента, который заключался в перемещении шпинделя по оси станка с передачей ШВП и пружинным демпфером на деревянную балку. Если пружина сжималась более чем на 1мм., происходил аварийный останов станка. Установив датчик силы, система добилась более раннего срабатывания аварийной защиты. При этом, если стандартная система защиты отключала станок после прохождения пути в 3-4 мм., то в нашем случае путь сократился до 2-3 мм.
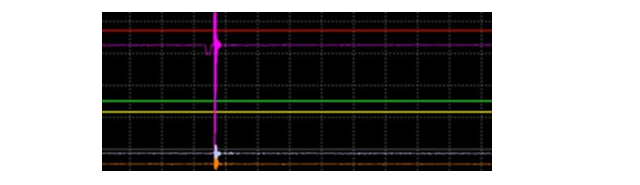
Определение неисправностей шпинделя при работе на частоте до 2000 об/мин.
На нижерасположенном рисунке показаны виброхарактеристики шпинделя (рисунок слева) и дисбаланс шпинделя (рисунок справа)
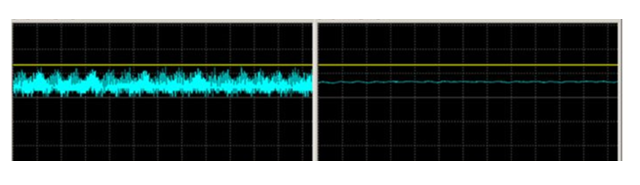
Результаты срабатывания системы защиты от столкновений шпинделя с заготовкой
На нижерасположенном рисунке показаны результаты использования системы защиты шпинделя от столкновений.
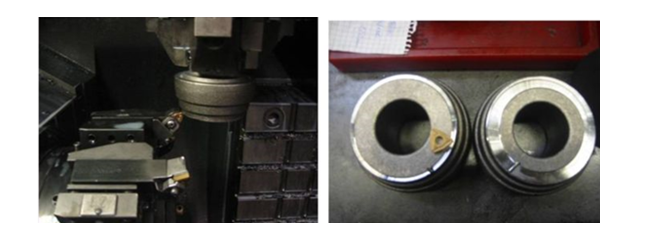
Осмотр и замеры технического состояния узлов станка, инструмента, револьверной головки и шпинделя не показали видимых дефектов. Деталь, используемая в эксперименте, прошла контроль. В прошлом, такого типа столкновения приводили к выходу из строя станка минимум на 8 часов с привлечением сервисных специалистов.
Определение неисправностей формообразующих узлов станков с ЧПУ на частоте вращения шпинделя 5000 об/мин. И подачи 50 м/мин.
На нижерасположенном рисунке показана виброхарактеристика шпинделя при работе на частоте вращения 5000 об/мин. И подачей 50 м/ мин.
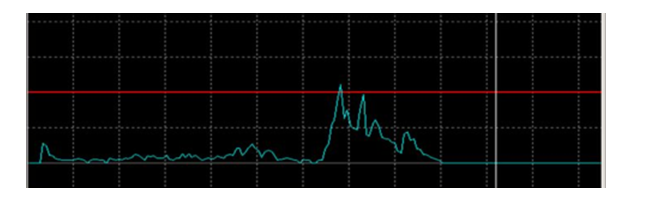
И в заключении этой части статьи я хочу показать Вам, как выглядят виброхарактеристики трех шпинделей с разными техническими состояниями и наработками.
Первый шпиндель новый с наработкой 0 часов.
Второй шпиндель с наработкой 7000 часов.
Третий шпиндель после столкновения.
На первой картинке изображены виброхарактеристики нового шпинделя, которые получены в данном случае с трех осевого датчика на нормальном уровне.
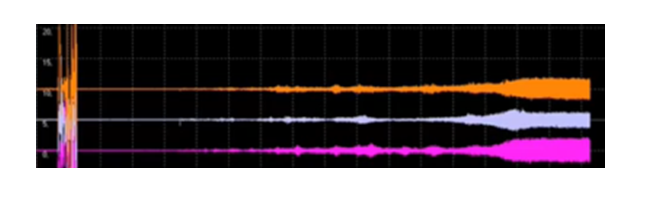
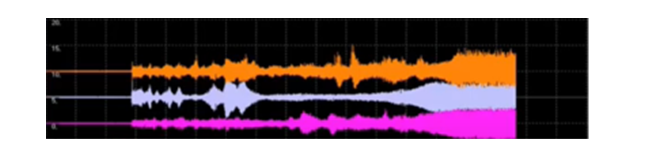
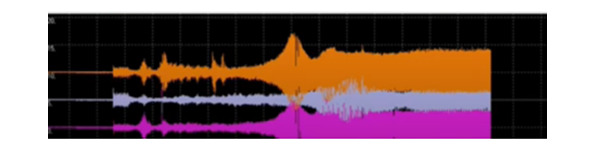
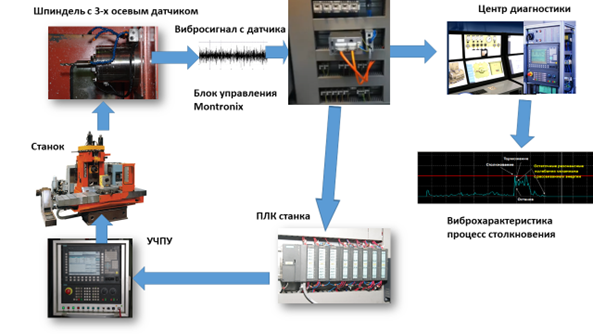
-центр диагностики для проведения глубокой диагностики технического состояния элементов шпинделя и принятия решения о ремонте.
-ПЛК станка для формирования сигналов остановки подачи и последующей аварийной остановки станка.
На этом я заканчиваю очередную часть статьи, посвященную системе против столкновения шпинделя с другими узлами станков MONTRONIX.