Стационарная система вибродиагностики и мониторинга технического состояния узлов станка — это технические, экономические, психологические аспекты в свете формулы «легче предупредить, чем лечить».
Стационарная система вибродиагностики и мониторинга технического состояния узлов станка— комплексная система непрерывного наблюдения за техническим состоянием узлов и систем станков с ЧПУ в целях постоянного контроля за их техническим состоянием, прогнозирования отказов.
Доброго времени суток, уважаемые коллеги и друзья!
В сегодняшней статье я продолжу тему методического обеспечения комплексной диагностики и мониторинга технического состояния узлов станков с ЧПУ с помощью стационарных систем. Стационарными системами диагностики и мониторинга технического состояния станков с ЧПУ я стал заниматься с 1984 г. с целью повышения уровня автоматизации ТОиР оборудования с ЧПУ, входящего в состав гибкого производственного участка, в состав которого в свою очередь входили: 4 многоцелевых станка модели ИР 500ПМФ4 со сменными столами накопителями на 8 мест, 3 многоцелевых станка модели MS 3-200 с портальными роботами и столами- накопителями, автоматизированным складом штабелёром, координатно-измерительная машина Opton и диагностическо-диспетчерский центр.
Цель выполнения проекта состояла в разработке и внедрении нового поколения систем сбора, обработки и управления потоком информации о техническом состоянии узлов станка, а также в обеспечении непрерывного электронного преобразования данных. Так как появление в узлах станков сбоев может привести не только к большим затратам, но и катастрофическим ситуациям, нужна система, способная анализировать поведение узлов станка с помощью датчиков и использовать собранные данные, чтобы предусмотреть и предотвратить потенциальные отказы.
Для выполнения вышепоставленной задачи станки модели ИР 500ПМФ4 были оснащены системами измерения деталей и инструмента производства фирмы Renishaw, системами диагностики узлов методом контроля примесей в масле в магистральных трубопроводах (разработка Куйбышевского авиационного института) и системой автоматического управления формообразованием обрабатываемых деталей на станках модели ИР500ПМФ4, с использованием результатов вибродиагностики технического состояния подшипников шпинделя. На корпус шпинделя станка устанавливались 3 датчика виброускорения (один в осевом направлении и два в радиальном направлении под углом 90 градусов). Таким образом мы определяли траекторию вращения оси шпинделя и состояние подшипников. Если траектория вращения шпинделя выходила за допустимые значения, то автоматически вводилась коррекция по двум координатам (собственная разработка).
На станках модели MS3-200 были установлены системы диагностики с элементами адаптивного управления производства фирмы Marposs. Данная система предназначалась для диагностики подшипников шпинделя и управления силой резания при обработке деталей за счет установленного в передней опоре подшипника с вмонтированным тензодатчиком.
Особое инновационное развитие это направление получило после создания в Техническом центре структуры диагностики и мониторинга технического состояния узлов станков и материально-технической базы. Была создана научно-исследовательская лаборатория для разработки и внедрения стационарных систем вибродиагостики технического состояния узлов станков с ЧПУ. Некоторые работы проводились совместно с куйбышевским политехническим и куйбышевским авиационным институтами.
Лаборатория была оснащена приборами, стендами собственной разработки и покупным оборудованием. Так, для проведения работ по вибродиагностике был создан специальный участок, оснащенный следующим оборудованием, подключенным в сеть предприятия:
- автоматизированный стенд диагностики и обкатки мотор-шпинделей (собственная разработка),
- автоматизированный стенд контроля подшипников,
- балансировочный стенд, анализатор спектра,
- приборы вибродиагностики,
- испытательный стенд на базе станков ИР320 и ИР800,
- испытательные стенды для проведения работ по приводам подач.
А теперь перейдем непосредственно к методике, используемой Техническим центром при работе со стационарными системами вибродиагностики, установленными на особо критичных станках с ЧПУ.
12. Использование стационарной системы вибродиагностики.
Целью комплексной диагностики и мониторинга технического состояния формообразующих узлов станков с ЧПУ является повышение надежности и ресурса работы оборудования в соответствии с паспортными характеристиками. В общем виде задачу комплексного диагностирования и мониторинга оборудования мы рассматривали как двойственную задачу:
-задачу построения моделей, соответствующих паспортным характеристикам и характеристикам фактического состояния,
-и задачу принятия решения о дальнейшей эксплуатации оборудования в зависимости его технического состояния.
На современных автоматизированных станках с ЧПУ, как правило, осуществляется оперативное диагностирование аппаратных и программных средств системы управления и исполнение управляющих программ методами прямого и косвенного контроля с помощью специальных датчиков. Наличие автоматической стационарной системы диагностирования технического состояния узлов оборудования с ЧПУ особенно важно для станков, работающих в составе ГПС, которые эксплуатируются в режиме ограниченности обслуживающего персонала.
На двух нижепредставленных рисунках показаны:
-Обобщенная структурная схема стационарной системы вибродиагностики технического состояния узлов станков с ЧПУ, являющейся общей для всех типов станочного оборудования.
-Функциональная схема стационарной системы вибродиагностики.
Из схемы стационарной системы вибродиагностики технического состояния узлов станков с ЧПУ мы видим, что сигналы с датчиков, установленных на формообразующих узлах станков с ЧПУ поступают в регистр данных, где они преобразуются из аналоговых сигналов в цифровые. Из блока регистратора данных данные поступают для дальнейшей обработки в персональный компьютер (ПК) и блок допустимых значений. Из блока допустимых значений данные поступают в программируемый контроллер станка, где записаны пороговые значения виброхарактеристик диагностируемых узлов. Из программируемого контроллера станка информация о техническом состоянии узлов станка в виде ошибок поступает на пульты оператора и диагноста. В случае превышения сигналов виброхаректеристики технического состояния диагностируемых узлов пороговых значений аварийных зон произойдёт отключение станка.
Используя АРМ диагноста, созданное на базе персонального компьютера и модулей мониторинга и диагностики, специалист, используя полученные данные о техническом состоянии узлов станка, программные обеспечения (ПО) настройки, анализа и данные допустимых расчетных параметров из АСУ “Мониторинг” производит проверку стационарности процессов, протекающих в диагностируемых узлах, расчеты спектра, дефектных частот и средне квадратичных значений (СКЗ) виброскорости и виброускорения для определения дефектных под узлов и просмотра тренда развития дефекта.
На основании полученных данных о техническом состоянии станка система автоматически формирует:
- протокол технического состояния станка,
- заказ на формирование комплектующих,
- план проведения ремонтных работ.
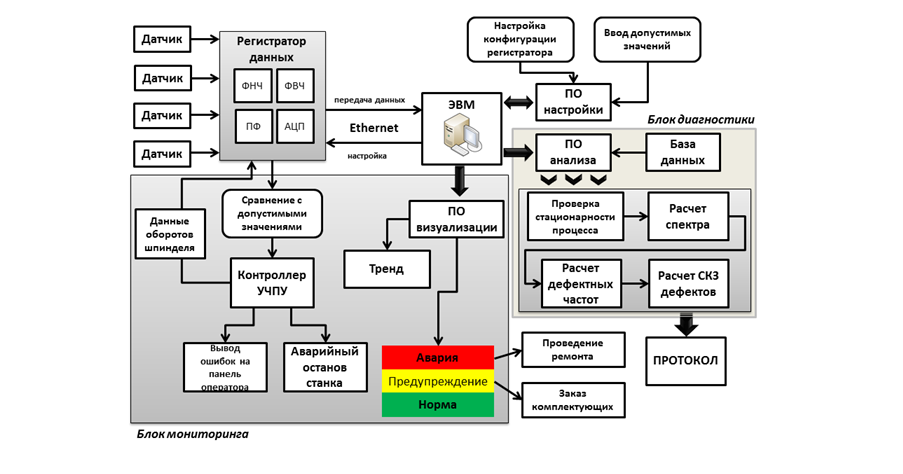
Схема организации стационарной системы вибродиагностики
На нижерасположенной функциональной схеме стационарной вибродиагностики фактического технического состояния узлов станков с ЧПУ более подробно показана работа модулей:
-диагностики
- визуализации технического состояния узла
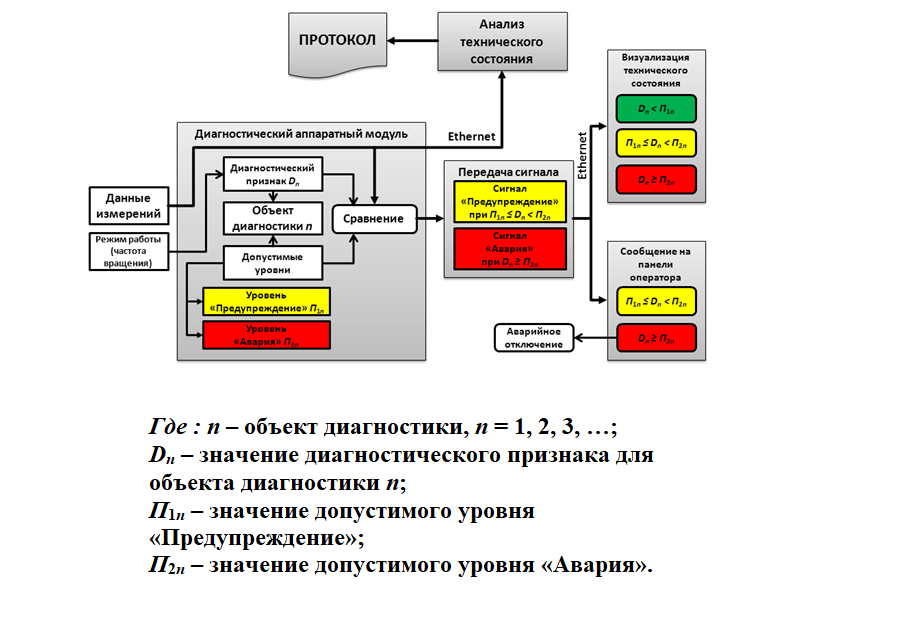
Итак, узлы станка, как объект диагностики, характеризуется набором из “j-х” физических состояний, для каждого из которых существует ”i “диагностируемый параметр. Стационарная система вибродиагностики технического состояния узлов станков выделяет информативный сигнал, наиболее полно характеризующий состояние узла диагностики, после чего блок преобразований трансформирует выделенный сигнал хi в удобный для дальнейшего использования вид. Основу библиотеки данных составляет полученная на этапе настройки системы совокупность эталонных диагностических сигналов, характеризующих возможные дефекты узлов станка. Идентификатор состояний сравнивает текущие и эталонные диагностические сигналы и принимает решение о соответствии диагностируемого параметра допустимым уровням состояний. Результатом функционирования данного блока является отчет о состоянии диагностируемого узла, выводимый на блок сигнализации и состояния. Блок формирования команд управления по результатам измерения и анализа состояния станочного оборудования формирует управляющие воздействия на УЧПУ станка для поддержания работоспособности узла до завершения расчетного периода работы станка.
На этапе эксплуатации станочного оборудования в реальных условиях стационарная система диагностики и мониторинга технического состояния узлов оборудования оперативно выявляет неисправности узлов станка путем непрерывного сопоставления текущего технического состояния объекта диагностики с перечнем наиболее вероятных, априорно установленных неработоспособных состояний и моделей с паспортными характеристиками. Результатом работы стационарной системы диагностики и мониторинга на этом этапе является формирование команд управления для аварийной остановки или отработка технологических мероприятий по поддержанию работоспособного состояния оборудования в пределах цикла функционирования.
12.1.Назначение стационарной системы вибродиагностики технического состояния узлов станков с ЧПУ.
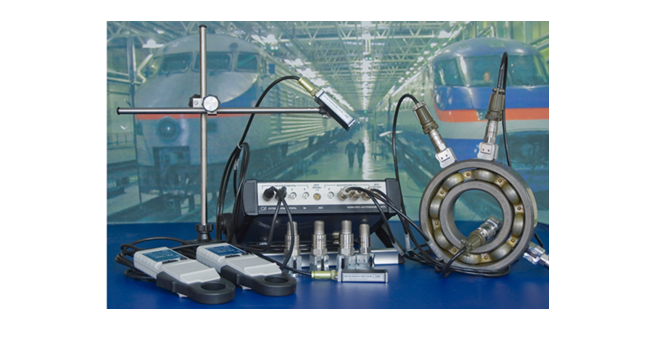
Автоматизированная стационарная система вибродиагностики технического состояния узлов станков с ЧПУ предназначена для:
12.1.1. Контроля и предотвращения столкновений подвижных узлов станка при работе по управляющей программе.
12.1.2. Сбора и удаленной передачи данных для последующего анализа в бюро диагностики и мониторинга Технического центра.
12.1.3. Оперативной диагностики технического состояния основных узлов и вывода сообщений о неисправности на панель оператора и на АРМ диагноста в Техническом центре.
2.1.4. Получения данных для визуализации технического состояния в SCADA-системе.
12.2. Оперативной диагностики технического состояния основных узлов при каждом
включении станка. При этом происходит сравнение измеряемых параметров вибрации диагностических признаков дефектов с заданными допустимыми значениями. При превышении заданных допустимых значений на панель оператора выводится сообщение о неисправности.
12.3. Контроля столкновений подвижных узлов станка осуществляется в режиме реального времени. При превышении заданных допустимых значений происходит отключение станка.
12.4. Сбора, удаленная и передачи данных для последующего анализа и получение данных для визуализации технического состояния в SCADA-системе, которая реализуется с помощью измерительно вычислительной системы (ИВС) с использованием технологии передачи данных Ethernet через набор программных технологий, которые представляют единый интерфейс (OPC-сервер).
13. Использование специального программного обеспечения
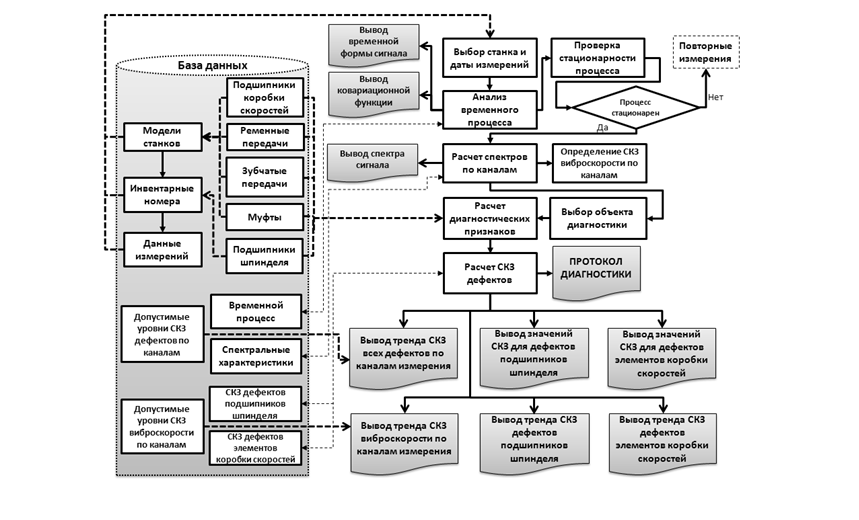
Структурная схема специального программного обеспечения для автоматизации вибродиагностики
13.1. Данное специальное программное обеспечение разработано для автоматизации анализа технического состояния узлов приводов главного движения станков с ЧПУ и подач по результатам вибродиагностики.
13.2. Оценка технического состояния объектов диагностики осуществляется по результатам мониторинга среднего квадратичного значения (СКЗ) амплитуд на дефектных частотах в спектрах сигналов.
13.3. Порядок работы с программным обеспечением.
13.3.1. Произведем загрузку экспериментальных данных замеров параметров вибрации (временной формы сигнала виброускорения) для каждой точки измерения в базу данных.
13.3.2. Выберем станок по инвентарному номеру из базы данных для проведения анализа.
13.3.3. Выберем дату проведения измерения.
13.3.4. Просмотрим общий уровень виброскорости и виброускорения в диапазоне частот 10…1000 Гц для каждой точки измерения и сравним их с допустимыми уровнями.
13.3.5. Просмотрим временные характеристики по всем каналам измерения.
13.3.6. Проверим стационарность процессов по всем каналам измерения. Если процесс не стационарен, то измерения бракуются (отклоняются).
13.3.7. Выбираем объекты диагностики (подшипники шпинделя или элементы коробки
скоростей).
13.3.8. Выводим значения СКЗ для каждого дефекта объекта диагностики по каналам
измерения. Сравнение полученные фактические данные с данными предыдущих измерений для данного узла станка.
13.3.9. Выводим и анализируем тренды СКЗ дефектов объектов диагностики по каналам
измерения.
14.Оценка технического состояния по результатам вибродиагностики
14.1. Оценка технического состояния объектов диагностики, представленных в п. 7 (п.п. 7.1 – 7.8.) осуществляется по результатам мониторинга среднего квадратичного значения
амплитуд на дефектных частотах в спектрах сигналов по результатам проведения
вибродиагностики 2-го уровня.
14.2.Оценка технического состояния по результатам вибродиагностики 1-го уровня осуществляется по общему уровню (среднему квадратическому значению) виброскорости в диапазоне частот 10…1000 Гц.
14.3.Допустимые значения общего уровня виброскорости определяются по
результатам мониторинга однотипного оборудования для каждой точки измерения.
14.3.1. Допустимые уровни вибрации привода главного движения станков фрезерного типа
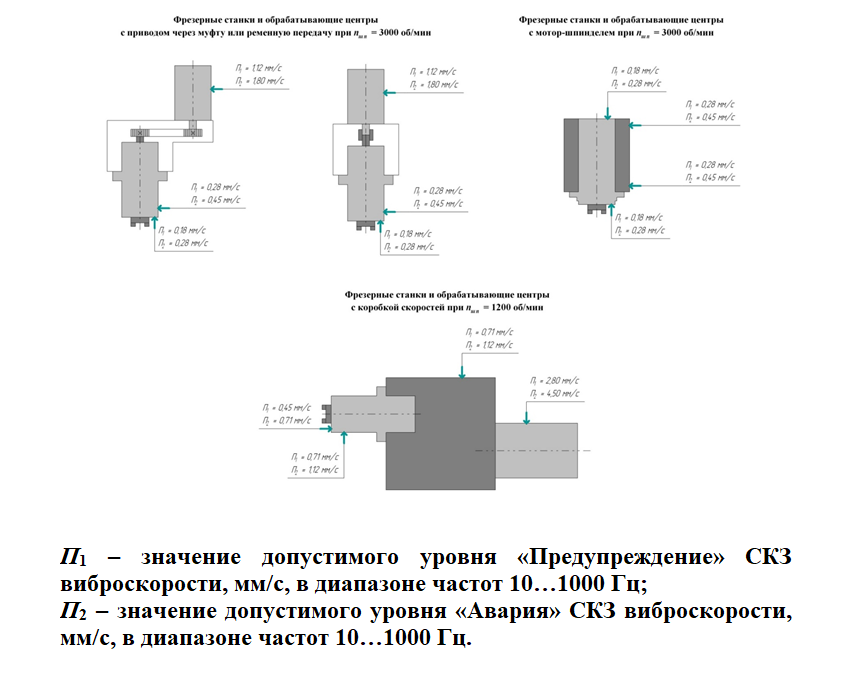
14.3.2. Допустимые уровни вибрации привода главного движения станков токарного типа
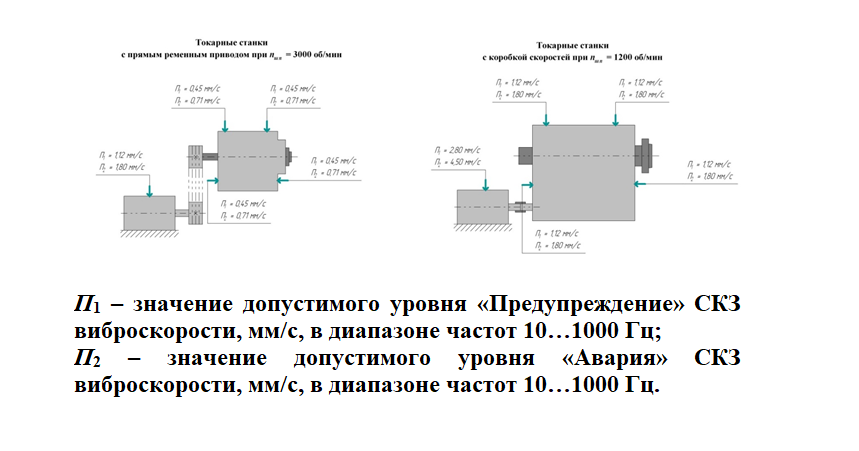
14.5. Для высокоскоростных шпинделей и мотор-шпинделей СКЗ виброскорости в диапазоне частот 10…1000 Гц при максимальной частоте вращения шпинделя не должно превышать 1,2 мм/с (в режиме холостого хода без нагрузки).
14.6. Для высокоскоростных шпинделей и мотор-шпинделей СКЗ виброскорости в
диапазоне частот 10…1000 Гц при обработке не должно превышать 6-8 мм/с.
14.7. Для высокоскоростных шпинделей и мотор-шпинделей аварийным уровнем СКЗ
виброскорости в диапазоне частот 10…1000 Гц при обработке, требующим немедленного отключения станка является уровень 10-12 мм/с.
14.8. Оценка технического состояния электродвигателей осуществляется по общему
уровню (СКЗ) виброскорости. Допустимые уровни вибрации приводятся в паспорте на
электродвигатель, либо определяются по ГОСТ 20815-93.
14.9. Оценка технического состояния редукторов общего назначения осуществляется в
соответствии с ГОСТ ИСО 8579-2-2002 (ISO 8579-2).
14.10. Пример протокола технического состояния привода главного движения станка модели TMX8MYS.
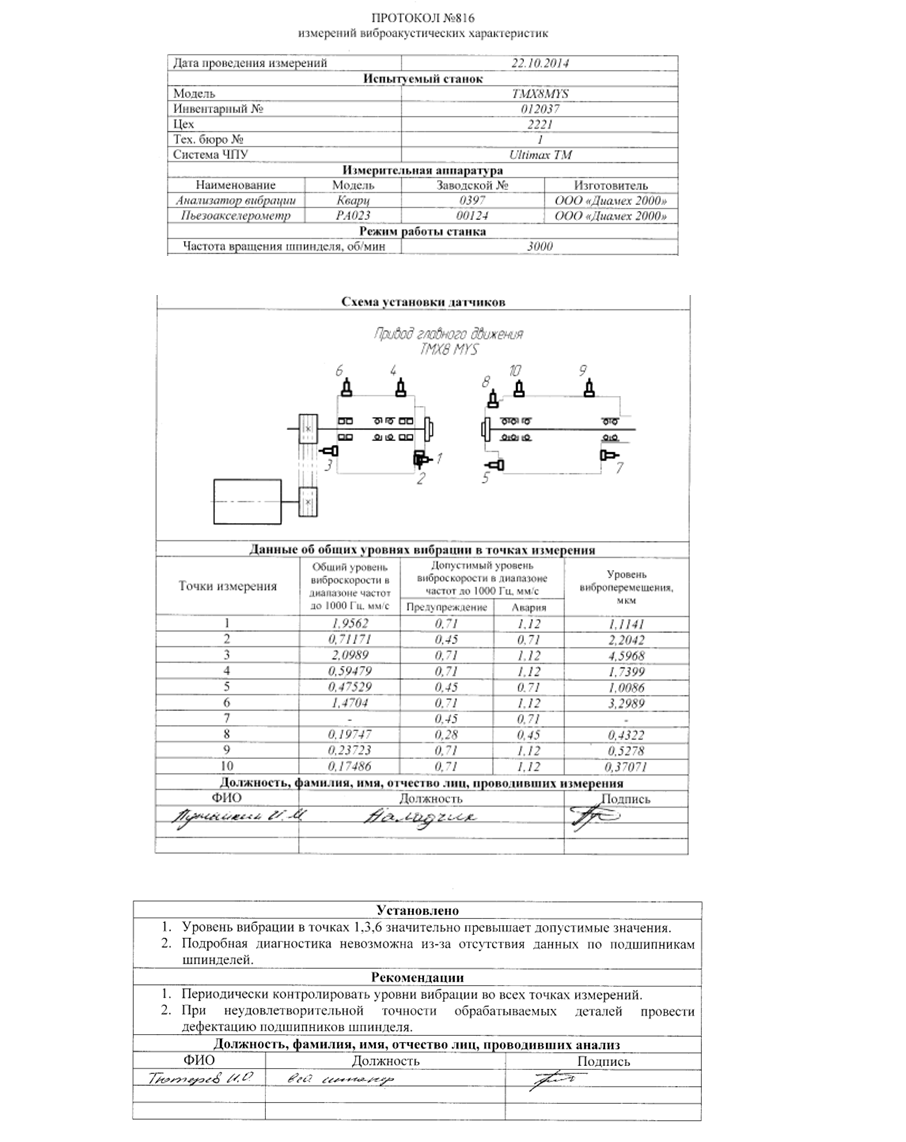
Нормативная база
1. ГОСТ Р ИСО 17359-2015. Контроль состояния и диагностика машин. Общее руководство.
2. ГОСТ Р ИСО 13372-2013. Контроль состояния и диагностика машин. Термины и определения.
3. ГОСТ Р ИСО 13373-1-2009. Контроль состояния и диагностика машин. Вибрационный контроль состояния машин. Часть 1. Общие методы.
4. ГОСТ РР ИСО 13373-2-2009. Контроль состояния и диагностика машин. Вибрационный контроль состояния машин. Часть 2. Обработка, анализ и представление результатов измерения вибраций.
5. ГОСТ Р ИСО 13374-1-2011. Контроль состояния и диагностика машин. Обработка, передача и представление данных. Часть 1. Общее руководство.
6. ГОСТ Р ИСО 13374-2-2011. Контроль состояния и диагностика машин. Обработка, передача и представление данных. Часть 2. Обработка данных.
7. ГОСТ Р ИСО 13374-3-2015. Контроль состояния и диагностика машин. Обработка, передача и представление данных. Часть 3. Передача данных.
8. ГОСТ Р ИСО 13379-2009. Контроль состояния и диагностика машин. Руководство по интерпретации данных и методов диагностирования.
9. ГОСТ Р ИСО10816-1-97. Вибрация. Контроль состояния машин по результатам.
10. ГОСТ 30848-2003 ( ИСО 13380-2002) Диагностирование машин по рабочим характеристикам. Общие положения.
11. ГОСТ Р ИСО13381-1-2011. Контроль состояния и диагностика машин. Прогнозирование технического состояния. Часть 1. Общее руководство.
В следующей статье я продолжу рассматривать тему методического обеспечения проведения диагностики и мониторинга технического состояния узлов
оборудования с ЧПУ.