Доброго времени суток, уважаемые коллеги!
В сегодняшней статье я продолжу тему о необходимости проведения внутреннего аудита технического состояния оборудования с ЧПУ и об эффективности работы ремонтных служб предприятия на примере Технического центра «ТОиР оборудования с ЧПУ».
При закупке нового оборудования с ЧПУ Технический центр проводит технический аудит по следующим направлениям:
При составлении бюджета на ТОиР оборудования с ЧПУ Технический центр проводит технический аудит по следующим направлениям:
При проведении анализа эффективности осуществления закупок запчастей и материалов, а также получения услуг на ТОиР оборудования с ЧПУ, Технический центр проводит технический аудит по следующим направлениям:
По эффективности выполнения работ по ТОиР оборудования с ЧПУ Технический центр проводит технический аудит по следующим направлениям:
Здесь необходимо отметить, что если внутренний аудит хочет собственными силами протестировать фактическое выполнение ремонтных работ, то для качественного выполнения подобной процедуры критически важным является наличие специализированной компетенции сотрудников Технического центра. При этом экспертиза может быть как внутренняя, так и привлеченная со стороны. Без этого проверить или доказать собственные выводы будет гораздо сложнее.
По учету затрат на выполнения работ по ТОиР оборудования с ЧПУ Технический центр проводит технический аудит по следующим направлениям:
Здесь можно выделить два уровня организации аналитики, которая способна существенно повысить эффективность процесса.
Рассмотрим порядок проведения аудита технического состояния на примере портально-фрезерного станка модели СФП-13,1976 года выпуска, с проведенным капитальным ремонтом с глубокой модернизацией в 2014 году.
На нижерасположенном рисунке показана разработанная специалистами Технического центра математическая модель пятиосевого портально-фрезерного станка модели СФП-13.
В сегодняшней статье я продолжу тему о необходимости проведения внутреннего аудита технического состояния оборудования с ЧПУ и об эффективности работы ремонтных служб предприятия на примере Технического центра «ТОиР оборудования с ЧПУ».
Примеры аудиторских проверок, проводимых Техническим центром
«ТОиР оборудования с ЧПУ»
При закупке нового оборудования с ЧПУ Технический центр проводит технический аудит по следующим направлениям:
- Согласование и последующая проверка наличия полной технической документации оборудования;
- Согласование и последующая проверка наличия рекомендаций по проведению ТОиР;
- Согласование и последующая проверка поставки математической модели станка;
- Обязательная приемка и обучение на заводе-изготовителе станка;
- Ориентировочный расчет финансовых затрат на ТОиР станка с ЧПУ на период всего жизненного цикла;
- Анализ статистики затрат на ТОиР станка в перспективе на 2-3 года;
- Участие в разработке проекта фундамента (если это необходимо)
При составлении бюджета на ТОиР оборудования с ЧПУ Технический центр проводит технический аудит по следующим направлениям:
- анализ алгоритма формирования плановых затрат на ТОиР оборудования с ЧПУ;
- проверка наличия установления лимитов на ТОиР в разрезе единиц оборудования;
- проверка наличия актов оценки технического состояния оборудования с ЧПУ по ключевым и наиболее дорогостоящим ремонтам;
- выявление признаков формального неэффективного подхода к бюджетированию плановых затрат на ТОиР оборудования с ЧПУ (с помощью АСУ ТОиР);
- анализ соотношения бюджета на плановые и аварийные ремонты;
- сравнение плановых затрат на ремонты со стоимостью новой единицы оборудования.
При проведении анализа эффективности осуществления закупок запчастей и материалов, а также получения услуг на ТОиР оборудования с ЧПУ, Технический центр проводит технический аудит по следующим направлениям:
- проверка исполнения закупочных процедур;
- проверка наличия альтернативных поставщиков (в случае, если закупка осуществлена у единственного источника);
- анализ добропорядочности существующих поставщиков, минимизирующих риски осуществления закупки по завышенным ценам (в случае, если поставщик является единственным источником);
- анализ и проверка, а также расчет нормирования ремонтных операций, т.е. стоимости ставки ремонта за один нормо/час;
- анализ возможности осуществления ремонтных работ собственными силами.
По эффективности выполнения работ по ТОиР оборудования с ЧПУ Технический центр проводит технический аудит по следующим направлениям:
- анализ существующих порядков приемки работ по ТОиР оборудования с ЧПУ;
- анализ наличия дефектных ведомостей.
Здесь необходимо отметить, что если внутренний аудит хочет собственными силами протестировать фактическое выполнение ремонтных работ, то для качественного выполнения подобной процедуры критически важным является наличие специализированной компетенции сотрудников Технического центра. При этом экспертиза может быть как внутренняя, так и привлеченная со стороны. Без этого проверить или доказать собственные выводы будет гораздо сложнее.
По учету затрат на выполнения работ по ТОиР оборудования с ЧПУ Технический центр проводит технический аудит по следующим направлениям:
- анализ и проверку наличия по объектному учету затрат в АСУ ТОиР;
- проверка корректности отражения информации по ремонтам (период, сумма, объект, узел) в АСУ ТОиР.
Здесь можно выделить два уровня организации аналитики, которая способна существенно повысить эффективность процесса.
- Первый уровень - пообъектный учет, организация которого является ключевой задачей создания понятной и прозрачной системы учета затрат на ремонт оборудования с ЧПУ (про точность и своевременность отражения затрат не говорим, поскольку данные критерии являются обязательными для соблюдения всегда).
- Второй уровень - достоверная и детализированная пообъектная статистика, необходимая при принятии решений о том, какого производителя запчастей и оборудования выбрать в будущем , когда целесообразнее приобретать новое оборудование, а не ремонтировать старое, а также при планировании ремонтной ТОиР оборудования (результаты анализа фактической статистики могут служить основой для определения размеров бюджетных лимитов).
Технический аудит металлорежущих станков
Рассмотрим порядок проведения аудита технического состояния на примере портально-фрезерного станка модели СФП-13,1976 года выпуска, с проведенным капитальным ремонтом с глубокой модернизацией в 2014 году.
На нижерасположенном рисунке показана разработанная специалистами Технического центра математическая модель пятиосевого портально-фрезерного станка модели СФП-13.
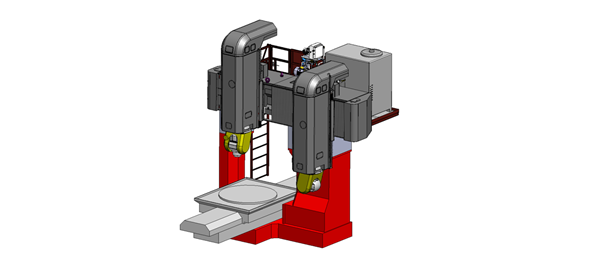
До начала проведения аудита работниками Технического центра в обязательном порядке разрабатывается задание/отчет о проведении аудита технического состояния пятиосевого портально-фрезерного станка модели СФП-13, включающего нижеперечисленные пункты:
При проведении аудита технического состояния продольно-фрезерного станка модели СФП-13 выявлено, что станок:
Выверку станка производим электронными брусковыми уровнями с ценой деления 0,001мм/м.
В результате проведенной выверки станка получили следующие результаты:
-параллельность оси Х составляет 0,012 мм. /5000мм.
-параллельность оси У составляет 0,01 мм. /2500мм.
- Провести общий визуальный осмотр станка с дополнительным оборудованием.
- Провести выверку станка перед испытанием его на технологическую точность.
- Провести осмотр системы безопасности станка.
- Провести проверку работоспособности всех узлов станка и вспомогательного оборудования.
- Проверить состояние электрического шкафа.
- Проверить состояние гидравлической системы.
- Проверить состояние пневматической системы.
- Проверить состояние холодильного агрегата.
- Проверить состояние станции смазки.
- Проверить состояние станции очистки СОЖ.
- Провести проверку геометрических параметров станка, включая техническое состояние фундамента и степень затяжки станины станка к фундаменту.
- Провести измерения точностных параметров станка при помощи лазерного интерферометра модели Renishaw XL-80.
- Если вводили корректировки таблиц компенсации, то необходимо провести контрольные проверки точности параметров станка по координатам X,Y, Z.
- Провести измерения объемной геометрической точности станка при помощи лазерного трекера модели.
- Провести проверку пространственной точности станка системой BalBar QC20-W производства фирмы Renishaw.
- Провести проверку плоскостей: XY, XZ, YZ.
- Провести проверку качества питания электрической сети прибором типа FUKT-435.
- Проверить полную мощность питающего трансформатора электрической сети на соответствие требованиям (составляет-500 kVa).
- Проверить нестабильность напряжения питания, которое не должно превышать +/-10% от номинального значения, что соответствует паспорту.
- Проверить уход по частоте напряжения линии электропитания, которое не превышает +/- 1% от номинального значения частоты, что соответствует паспорту.
- Проверить время прерывания подачи электропитания, которое составляет 2мс, а временной интервал между двумя последовательными прерываниями подачи электропитания - 0,5 сек., что соответствует паспорту.
- Линия электропитания станка не испытывает возмущения, вызванные потребителями высокой мощности, линиями высокого напряжения, сварочными аппаратами, станками лазерной резки.
- Сопротивление контура заземления составляет 3,5 Ом, что соответствует паспорту станка.
- Рабочее давление пневматической сети составляет 7,6 бар, что соответствует паспорту станка.
- Нагрузка на фундамент составляет 3000 кГ/кв. м., что соответствует паспорту станка.
При проведении аудита технического состояния продольно-фрезерного станка модели СФП-13 выявлено, что станок:
- находится в хорошем работоспособном состоянии,
- аварийные сообщения УЧПУ отсутствуют,
- основные параметры вспомогательных питающих систем станка соответствуют требованиям производителя.
Работы по выверке станка перед испытанием на технологическую точность
обработки заготовок
Выверку станка производим электронными брусковыми уровнями с ценой деления 0,001мм/м.
В результате проведенной выверки станка получили следующие результаты:
-параллельность оси Х составляет 0,012 мм. /5000мм.
-параллельность оси У составляет 0,01 мм. /2500мм.
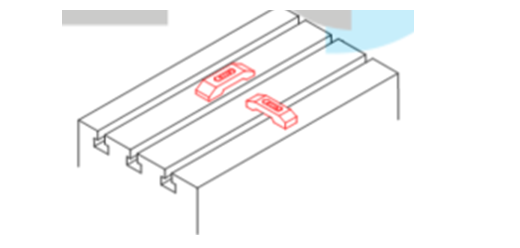
Максимально допустимое отклонение от горизонтальной плоскости для данной модели станка составляет:
-параллельность по оси Х-не более 0,03 мм. / 5000мм.
-параллельность по оси У-не более 0,03 мм. / 25000мм.
На нижерасположенном рисунке показана функциональная схема выверки станка модели СФП-13 с помощью электронного уровня.
-параллельность по оси Х-не более 0,03 мм. / 5000мм.
-параллельность по оси У-не более 0,03 мм. / 25000мм.
На нижерасположенном рисунке показана функциональная схема выверки станка модели СФП-13 с помощью электронного уровня.
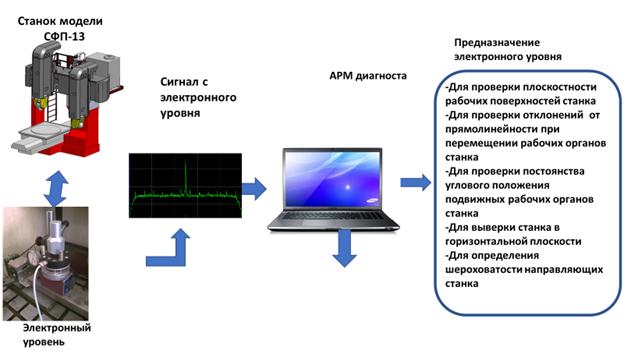
Результаты выверки станка:
Вывод:
Станок выверен в соответствии с паспортом и не требует дополнительной регулировки.
При работе по проверке геометрических параметров станка мы должны выполнить:
Вывод:
В ходе проведения проверки геометрической точности станка отклонения от паспортных значений не выявлены.
Линейные измерения являются наиболее распространенным типом измерений, выполняемых с помощью лазерного интерферометра. Лазерная интерферометрическая система позволяет определять точность линейного позиционирования и их повторяемость, путем сравнения координаты перемещения, определенной системой измерения станка, с фактическим перемещением, измеренным с помощью лазерного интерферометра.
На нижерасположенном рисунке показана функциональная схема проведения геометрических измерений станка модели СФП-13 лазерным интерферометром XL-80, с автоматическим составлением таблицы компенсации.
- Отклонение по уровню оси Х составляет 0,03мм. / 5000мм., что соответствует допустимому отклонению
- Отклонение по уровню оси У составляет 0,03мм. / 2500мм., что соответствует допустимому отклонению.
Вывод:
Станок выверен в соответствии с паспортом и не требует дополнительной регулировки.
Осмотр системы безопасности
- При проверке концевых и референтных выключателей, они находились в исправном состоянии.
- При проверке работы системы безопасности и кнопок аварийного отключения, они находились в исправном состоянии.
- При проверке состояния кабинетной защиты, она находилась в исправном состоянии.
Проверка работы всех узлов станка и агрегатов
- При проверке защитных скребков направляющих дефектных скребков не обнаружено.
- При проверке работы станка аномальных шумов и вибрации механических узлов станка не обнаружено.
- При проверке состояния кожухов направляющих станка они находились в хорошем состоянии, отклонений не имели.
- При проверке работы инструментального магазина неисправностей не обнаружено.
- При проверке ШВП и направляющих станка внешних повреждений не обнаружено.
- При проверке системы зажима/разжима инструмента в мотор-шпинделе неисправностей не обнаружено.
Проверка состояния УЧПУ и электрического шкафа
управления
- При проверке батарей ЧПУ определили их исправность, т.е. замена батарей не требуется.
- При проверке вводного напряжения определили, что вводное напряжение соответствует паспортному значению.
- При проверке состояния проводов, кабельной изоляции повреждений не обнаружено.
- При проверке состояния разъемов и контактов повреждений не обнаружено.
- При проверке температурного режима в электрическом шкафу нарушений не обнаружено, температурный режим в норме.
Работы по проверке состояния гидросистемы станка
- В результате проведенной работы по проверке герметичности гидравлической системы было выяснено ее исправное состояние.
- В результате проведенной работы по проверке состояния гидроцилиндров и гидроклапанов было выяснено их хорошее состояние.
- При проведении работ по проверке давления в гидравлической системе было выявлено их полное соответствие паспортным данным.
- При проведении работ по проверке чистоты масляных фильтров замечаний не обнаружено.
- При проведении работ по проверке состояния электромагнитных клапанов замечаний не обнаружено.
- При проведении работ по проверке состояния системы охлаждения гидравлического масла замечаний не обнаружено.
Работы при проверке пневматической системы станка
- При проверке герметичности пневматической системы станка нарушений не обнаружено.
- При проверке давления в пневматической системе станка отклонений от паспортных данных не обнаружено.
Работы по проверке геометрических параметров станка
При работе по проверке геометрических параметров станка мы должны выполнить:
- проверку параллельности перемещения по оси Х, которая находится в допуске;
- проверку параллельности перемещения по оси У, которая находится в допуске;
- проверку перпендикулярности между осями Х и У, которая находится в допуске;
- проверку перпендикулярности между осями Х и Z, которая находится в допуске;
- проверку перпендикулярности между осями Y и Z, которая находится в допуске;
- проверку параллельности Т- образного паза относительно перемещения вдоль оси Х, которая находится в допуске;
- проверку торцевого биения шпинделя, которое по результатам проверки находится в допуске;
- проверку радиального биения шпинделя, которое по результатам проверки находится в допуске;
- проверку биения шпинделя у торца шпинделя и на расстоянии 300мм., которое по результатам проверки находится в допуске;
- проверку перпендикулярности между осью шпинделя и поверхности стола, которое по результатам проверки находится в допуске;
- проверку плоскости XZ, которая по результатам проверки находится в допуске;
- проверку плоскости YZ, которая по результатам проверки находится в допуске.
Вывод:
В ходе проведения проверки геометрической точности станка отклонения от паспортных значений не выявлены.
Работы по измерению точностных параметров при помощи лазерного интерферометра типа XL-80 производства фирмы Renishaw
Линейные измерения являются наиболее распространенным типом измерений, выполняемых с помощью лазерного интерферометра. Лазерная интерферометрическая система позволяет определять точность линейного позиционирования и их повторяемость, путем сравнения координаты перемещения, определенной системой измерения станка, с фактическим перемещением, измеренным с помощью лазерного интерферометра.
На нижерасположенном рисунке показана функциональная схема проведения геометрических измерений станка модели СФП-13 лазерным интерферометром XL-80, с автоматическим составлением таблицы компенсации.
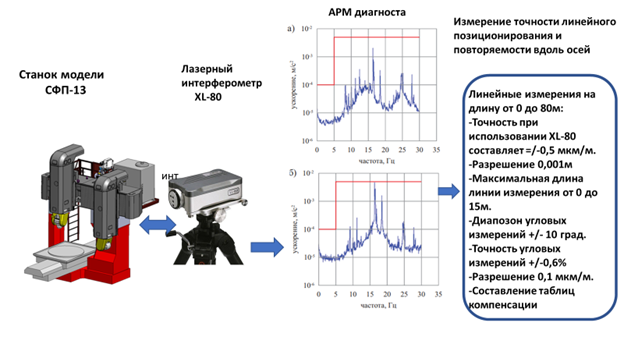
На нижерасположенном рисунке показана комплектация интерферометра модели XL-80.
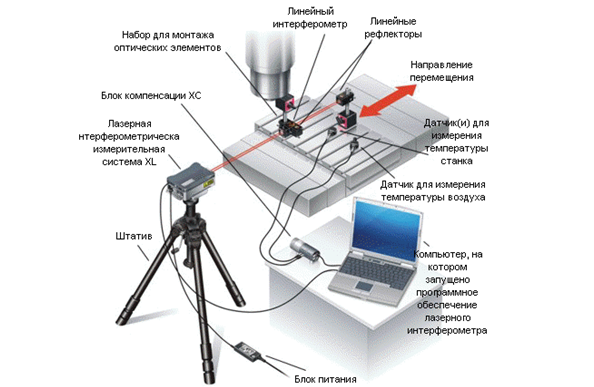
Лазерный интерферометр XL-80 оснащен системой компенсации изменения параметров, которая осуществляется при изменении:
-температуры,
-давления,
-влажности воздуха.
Затем система рассчитывает показатель преломления воздуха и длину волны лазера. После выполнения вышеуказанных задач в показания лазерного интерферометра автоматически вносятся поправки на изменение длины волны лазерного излучения.
Преимущество автоматической компенсации состоит в том, что процесс измерений в этом случае не требует вмешательства сотрудника Технического центра и происходит очень быстро.
Далее сотрудники Технического центра «ТОиР оборудования с ЧПУ» проводят работы по контрольным проверкам осей станка до и после корректировки таблиц компенсации.
Далее сотрудники Технического центра «ТОиР оборудования с ЧПУ» проводят работы по проверке объемной геометрической точности станка лазерным трекером модели API Ralbfn с автоматической компенсацией до паспортных значений объемной геометрической точности станка.
На нижерасположенном рисунке показана функциональная схема проведения измерений объемной геометрической точности станка модели СФП-13 с последующей автоматической компенсацией (при необходимости) лазерным трекером модели API Radian.
-температуры,
-давления,
-влажности воздуха.
Затем система рассчитывает показатель преломления воздуха и длину волны лазера. После выполнения вышеуказанных задач в показания лазерного интерферометра автоматически вносятся поправки на изменение длины волны лазерного излучения.
Преимущество автоматической компенсации состоит в том, что процесс измерений в этом случае не требует вмешательства сотрудника Технического центра и происходит очень быстро.
Далее сотрудники Технического центра «ТОиР оборудования с ЧПУ» проводят работы по контрольным проверкам осей станка до и после корректировки таблиц компенсации.
Далее сотрудники Технического центра «ТОиР оборудования с ЧПУ» проводят работы по проверке объемной геометрической точности станка лазерным трекером модели API Ralbfn с автоматической компенсацией до паспортных значений объемной геометрической точности станка.
На нижерасположенном рисунке показана функциональная схема проведения измерений объемной геометрической точности станка модели СФП-13 с последующей автоматической компенсацией (при необходимости) лазерным трекером модели API Radian.
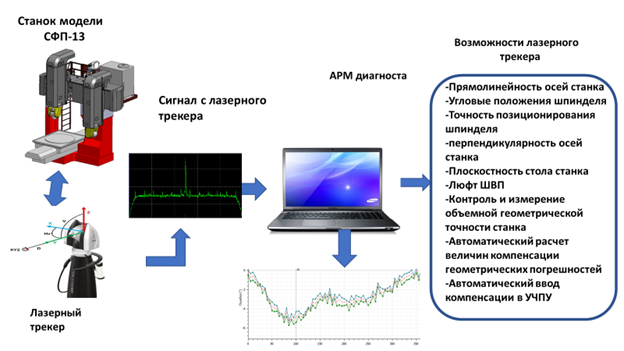
Далее сотрудники Технического центра «ТОиР оборудования с ЧПУ» переходят к проведению работы по проверке пространственной точности станка прибором QC-20 производства фирмы «Renishaw».
Для проведения измерений пространственной точности станка специалисты Технического центра использовали систему QC-20-W, в комплект которой входят:
-программное обеспечение BalBar-20,
-программа моделирования графиков BalBar,
-беспроводная система QC-20,
-шпиндель,
-держатели для выполнения тестов длиной 150 и 300 мм.,
-калибратор,
-установочный шарик.
На нижерасположенном рисунке показана функциональная схема проведения измерений пространственной точности продольно-фрезерного станка модели СФП -13 системой QC-20.
Для проведения измерений пространственной точности станка специалисты Технического центра использовали систему QC-20-W, в комплект которой входят:
-программное обеспечение BalBar-20,
-программа моделирования графиков BalBar,
-беспроводная система QC-20,
-шпиндель,
-держатели для выполнения тестов длиной 150 и 300 мм.,
-калибратор,
-установочный шарик.
На нижерасположенном рисунке показана функциональная схема проведения измерений пространственной точности продольно-фрезерного станка модели СФП -13 системой QC-20.
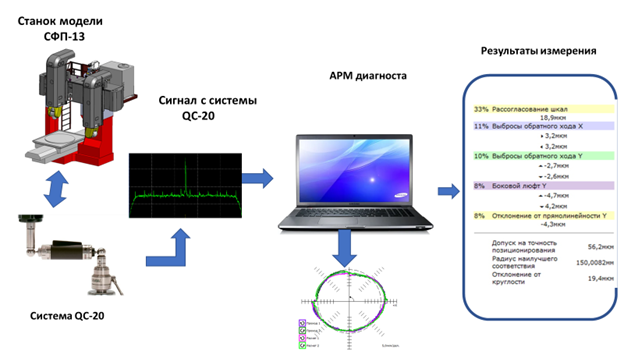
Проведенная специалистами Технического центра «ТОиР оборудования с ЧПУ» проверка геометрической точности показала, что портально-фрезерный станок модели СФП-13 соответствует всем паспортным параметрам и не требует дополнительных регулировок.
Точность позиционирования линейных осей станка имеет небольшие отклонения. Для повышения точности позиционирования была проведена корректировка таблиц компенсации. После корректировки точность позиционирования стали соответствовать паспортным данным станка.
Выполненная проверка пространственной точности станка прибором QC-20 показала хорошие результаты.
Объемная точность станка, измеренная лазерным трекером соответствует требованиям станков особо высокой точности.
По данным результатам видно, что общее состояние исполнительных механизмов станка (ШВП, направляющие, шпиндель и т.д.) находятся в отличном состоянии.
А теперь я перейду к оценке технического состояния фундамента и силы затяжки каждой опоры портально-фрезерного станка модели СФП-13 к фундаменту.
Фундаменты являются опорной частью оборудования и передают на грунт давление от его веса и сил, возникающих при работе станка. Кроме того, фундаменты придают оборудованию дополнительную жесткость и устойчивость.
Для нормальной работы оборудования фундамент должен обеспечивать:
Неправильная конструкция фундамента может привести к возникновению вибраций, преждевременному износу оборудования, неточности работы, ухудшению качества обрабатываемых поверхностей, к смещению оборудования с установленного места, к износу станины и нарушению регулировок.
Портально-фрезерный станок модели СФП-13 установлен на совмещенную конструкцию фундамента, состоящую из рамной металлической конструкции, выполненной в виде креста и бетонной конструкции, являющейся основанием фундамента.
На нижерасположенном рисунке показана схема смешанного фундамента под портально-фрезерный станок модели СФП-13.
Точность позиционирования линейных осей станка имеет небольшие отклонения. Для повышения точности позиционирования была проведена корректировка таблиц компенсации. После корректировки точность позиционирования стали соответствовать паспортным данным станка.
Выполненная проверка пространственной точности станка прибором QC-20 показала хорошие результаты.
Объемная точность станка, измеренная лазерным трекером соответствует требованиям станков особо высокой точности.
По данным результатам видно, что общее состояние исполнительных механизмов станка (ШВП, направляющие, шпиндель и т.д.) находятся в отличном состоянии.
А теперь я перейду к оценке технического состояния фундамента и силы затяжки каждой опоры портально-фрезерного станка модели СФП-13 к фундаменту.
Фундаменты являются опорной частью оборудования и передают на грунт давление от его веса и сил, возникающих при работе станка. Кроме того, фундаменты придают оборудованию дополнительную жесткость и устойчивость.
Для нормальной работы оборудования фундамент должен обеспечивать:
- распределение на грунт сил от веса оборудования в соответствии с несущей способностью грунта;
- заданное при монтаже положение оборудования при всех грунтовых условиях;
- жесткость станины оборудования путем включения фундамента в общую систему;
- необходимую устойчивость оборудования за счет понижения центра тяжести всей установки;
- увеличение массы всего агрегата, а следовательно, уменьшение возможных амплитуд смещений при вибрациях и ударном действии сил;
- благоприятное влияние грунта как фактора демпфирования вибрации;
- защиту оборудования от внешних воздействий при работе окружающих машин и механизмов.
Неправильная конструкция фундамента может привести к возникновению вибраций, преждевременному износу оборудования, неточности работы, ухудшению качества обрабатываемых поверхностей, к смещению оборудования с установленного места, к износу станины и нарушению регулировок.
Портально-фрезерный станок модели СФП-13 установлен на совмещенную конструкцию фундамента, состоящую из рамной металлической конструкции, выполненной в виде креста и бетонной конструкции, являющейся основанием фундамента.
На нижерасположенном рисунке показана схема смешанного фундамента под портально-фрезерный станок модели СФП-13.
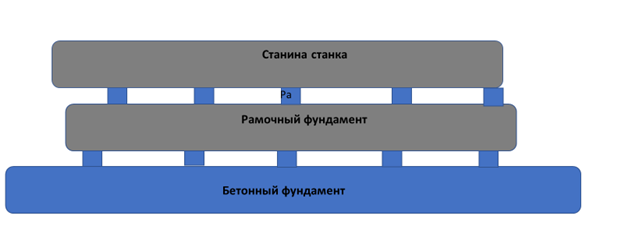
Основные параметры фундамента под станок для обработки металла, которые проверяют при выполнении работ по текущему ремонту диагносты Технического центра:
На нижерасположенном рисунке показана функциональная схема удаленного мониторинга технического состояния фундамента портально-фрезерного станка модели СФП-13.
- Грузоподъемность. Фундамент должен выдерживать вес станка и других установленных на нем компонентов. При определении грузоподъемности необходимо учитывать все нагрузки, с которыми фундамент будет сталкиваться в процессе эксплуатации.
- Уровень вибраций. Фундамент должен обеспечивать надежную амортизацию вибраций, которые возникают во время работы станка. Это поможет избежать перекосов и снижение точности обработки металла.
- Изоляция от вибраций. Фундамент должен предотвращать передачу вибраций от станка на соседнее оборудование в цехе. Для этого используются специальные материалы и технологии, которые позволяют снизить воздействие вибраций.
- Устойчивость к вертикальным и горизонтальным нагрузкам. Фундамент должен быть достаточно прочным и устойчивым, чтобы выдерживать как вертикальные нагрузки, создаваемые самим станком, так и горизонтальные нагрузки, возникающие в результате динамических процессов обработки металла.
- Величину затяжки каждой опоры, так как она влияет на общую геометрическую точность станка. Работы по выставке станка требует более квалифицированной работы слесарей-ремонтников. При правильной установке технологическое оборудование получает идеальную геометрию. В таком случае жесткость фундамента увеличивает жесткость станка, что влечет за собой прирост в точности обработки изделий на данном станке, а также уменьшает износ подвижных элементов и направляющих станка.
- Степень фиксации. Фундамент должен обеспечивать надежную фиксацию станка и его компонентов, чтобы минимизировать движение и смещение оборудования во время работы. Это улучшит точность обработки и предотвратит возможные повреждения узлов станка.
На нижерасположенном рисунке показана функциональная схема удаленного мониторинга технического состояния фундамента портально-фрезерного станка модели СФП-13.
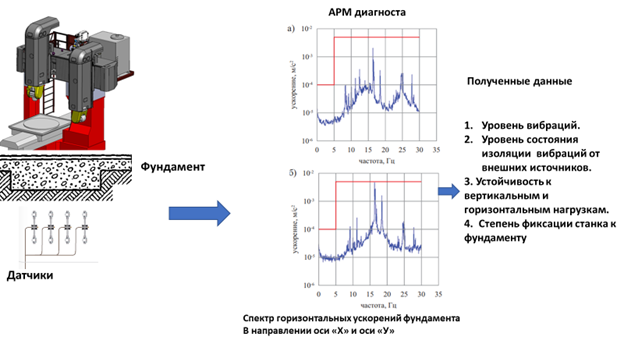
Любой дефект фундамента выражается в снижении его способности поглощать энергию вибрации.
Поиск ослабления в фундаменте производится диагностом Технического центра, в первую очередь, по принципу измерения «контурной вибрации» на станине станка, на рамном фундаменте (металлическом кресте) и на бетонном фундаменте. При этом один датчик перемещается по направляющим станка в том или ином направлении, и выполняется замер вибрации через каждые 600мм., и особенно в ее узловых и характерных точках.
Наиболее важным признаком наличия трещины в контролируемой зоне фундамента, или иного дефекта, является «скачок фазы» измеряемого вибрационного сигнала относительно фазы опорного вибрационного сигнала металлического креста и бетонного фундамента. Эти опорные точки выбираются произвольно, но являются одними и теми же для всех измерений. В этих точках постоянно установлены второй и третий датчики, показания которых регистрируются синхронно с основным измерительным датчиком, перемещаемым по направляющим станкам.
Анализ фазы контурной вибрации, регистрируемой на перемещаемом датчике, может позволить достаточно просто и точно обнаружить точку ослабления или место прохождения трещины в фундаменте. Это видно как по скачку общего уровня вибрации, так и по моменту изменения фазы основной гармоники вибросигнала скачком на 180°, которое всегда происходит в таких «пограничных» зонах.
На нижерасположенном рисунке показан график спектра вибрации станины станка с ослабленным фундаментом.
Поиск ослабления в фундаменте производится диагностом Технического центра, в первую очередь, по принципу измерения «контурной вибрации» на станине станка, на рамном фундаменте (металлическом кресте) и на бетонном фундаменте. При этом один датчик перемещается по направляющим станка в том или ином направлении, и выполняется замер вибрации через каждые 600мм., и особенно в ее узловых и характерных точках.
Наиболее важным признаком наличия трещины в контролируемой зоне фундамента, или иного дефекта, является «скачок фазы» измеряемого вибрационного сигнала относительно фазы опорного вибрационного сигнала металлического креста и бетонного фундамента. Эти опорные точки выбираются произвольно, но являются одними и теми же для всех измерений. В этих точках постоянно установлены второй и третий датчики, показания которых регистрируются синхронно с основным измерительным датчиком, перемещаемым по направляющим станкам.
Анализ фазы контурной вибрации, регистрируемой на перемещаемом датчике, может позволить достаточно просто и точно обнаружить точку ослабления или место прохождения трещины в фундаменте. Это видно как по скачку общего уровня вибрации, так и по моменту изменения фазы основной гармоники вибросигнала скачком на 180°, которое всегда происходит в таких «пограничных» зонах.
На нижерасположенном рисунке показан график спектра вибрации станины станка с ослабленным фундаментом.
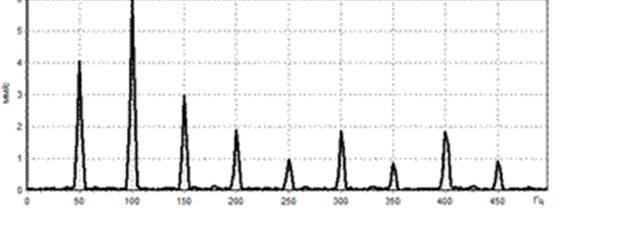
Как видно из графика, спектр вибрационного сигнала при общем механическом ослаблении фундамента достаточно прост, обычно в нем присутствует только первая гармоника вибросигнала, наведенная от небаланса вращающихся узлов станка, всегда имеющего место в практике, или иного дефекта. Амплитуда этой гармоники бывает очень значительной.
На нижерасположенном рисунке показана функциональная схема диагностики технического состояния смешанного фундамента под продольно-фрезерный станок модели СФП-13, определяемого вибро-анализатором фирмы Балтех.
На нижерасположенном рисунке показана функциональная схема диагностики технического состояния смешанного фундамента под продольно-фрезерный станок модели СФП-13, определяемого вибро-анализатором фирмы Балтех.
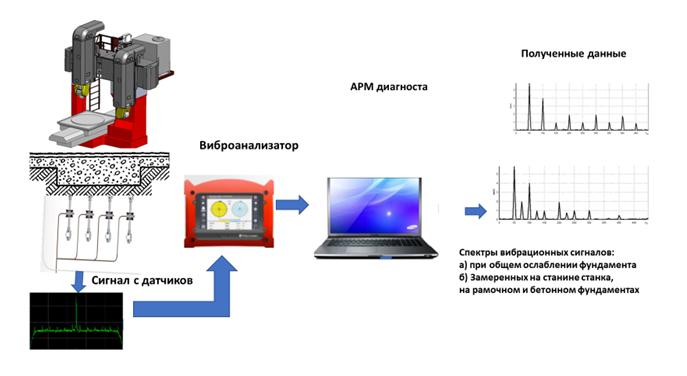
На этом я заканчиваю данную статью.
При написании данной статьи я использовал следующие материалы:
1. Материалы, опубликованные в открытой печати в интернете.
2. Материалы собственных опубликованных статей.
3. Материалы собственных докладов на научно-технических конференциях.
4. Материалы Технического центра по проверке технического состояния фундаментов под станки с ЧПУ.
При написании данной статьи я использовал следующие материалы:
1. Материалы, опубликованные в открытой печати в интернете.
2. Материалы собственных опубликованных статей.
3. Материалы собственных докладов на научно-технических конференциях.
4. Материалы Технического центра по проверке технического состояния фундаментов под станки с ЧПУ.