В статье я буду говорить о том, как мы у себя на предприятии организовали работы по капитальному ремонту с глубокой модернизацией станков с ЧПУ. Все, о чем я буду говорить в этой статье, — это прожито и пережито в процессе трансформации сотен процессов и ситуаций за 40 лет работы в области ТОиР оборудования с ЧПУ. И мне нет никакой необходимости что-то скрывать и доказывать, я просто хочу поделится опытом, который накопил за 20 лет работы в области организации и проведении работ по капитальному ремонту с глубокой модернизацией оборудования с ЧПУ на предприятии АО “РКЦ “ПРОГРЕСС”.
Весомый вклад в решение проблемы ускоренного обновления и повышения эффективности станочного парка машиностроения может внести организованный должным образом капитальный ремонт с глубокой модернизацией имеющегося оборудования с ЧПУ.
Под капитальным ремонтом с глубокой модернизацией в данном случае понимается доведение имеющегося оборудования до современного уровня по точности, производительности, функциональным и технологическим возможностям путем капитального ремонта и оснащения современными (преимущественно отечественными) комплектующими изделиями (системы ЧПУ, привода, электродвигатели, шарико-винтовые пары, электро-гидроаппаратура и др.).
Практика проведенных Техническим центром ТОиР оборудования капитальных ремонтов с глубокой модернизацией станков с ЧПУ для продления ресурса их работы и доведения их до современного технического уровня показала правильность выбранного решения.
К сожалению, капитальный ремонт с глубокой модернизацией имеющегося металлообрабатывающего оборудования до сих пор не воспринимается как один из важнейших ресурсов обновления технологической базы предприятий и находится вне поля зрения органов государственного управления, не находя должного отражения в принимаемых законах и госпрограммах.
Капитальный ремонт с глубокой модернизацией оборудования с ЧПУ, как правило, осуществляются маломощными, плохо оснащенными станкоремонтными фирмами, работающими в сфере малого бизнеса. Усиленно насаждается мнение, что восстановление и повышение эффективности станочного парка возможно только за счет закупки нового, желательно импортного, оборудования.
Капитальный ремонт с глубокой модернизацией имеющегося оборудования (наряду с заменой оборудования на новое) в процессе технического перевооружения промышленных предприятий имеет ряд неоспоримых преимуществ:
- рационально используется имеющееся оборудование (станок, который можно модернизировать, не сдается в металлолом);
- сокращаются сроки замены оборудования, особенно это касается тяжелых станков: изготовление нового оборудования под заказ потребует 1,5–2 года, капитальный ремонт с глубокой модернизацией имеющегося оборудования — 3–6 месяца;
- сокращаются потребности в закупках импортного оборудования (капитально отремонтированный и модернизированный отечественный станок во многих случаях может заменить новый);
- снижаются затраты на обновление станочного парка (капитальный ремонт с глубокой модернизацией имеющегося станка, как правило, стоит значительно дешевле, чем закупка нового станка, тем более импортного);
- компенсируется дефицит производственных мощностей по изготовлению отливок базовых деталей станков (большинство специализированных литейных заводов прекратили свое существование);
- к работам по модернизации станочного оборудования, в том числе к изготовлению запчастей и комплектующих изделий, можно привлечь станкостроительные и машиностроительные предприятия, что позволит увеличить их загрузку, улучшить финансовое состояние, стимулируя тем самым разработку и выпуск нового оборудования.
В настоящее время промышленные предприятия должны обладать высоко эффективным парком оборудования, что является необходимой предпосылкой повышения качества и обеспечения конкурентоспособности выпускаемой продукции. Современные условия обусловливают переориентацию инвестиционной политики от приобретения нового оборудования, в основном, на обновление действующего станочного парка.
В то же время состояние станочного парка на многих промышленных предприятиях в настоящее время следует признать неудовлетворительным. Значительная часть оборудования является физически и морально изношенным и не может способствовать решению вышеуказанных задач. Обновление производственной базы идет низкими темпами. Происходит значительное уменьшение поставок техники российскими предприятиями в связи с сокращением ее выпуска в России и зарубежных санкций. Технический уровень многих видов выпускаемого оборудования снизился и не соответствует требованиям производства.
Весомый вклад в решение проблемы обновления и модернизации станочного парка могут внести организованные на предприятиях должным образом ремонт и техническое обслуживание существующего станочного парка.
Из моего опыта, техническая политика в области эксплуатации станков с ЧПУ должна быть частью общей технической политики предприятия. И должна включать в себя:
- единую для всего предприятия политику в области капитального ремонта, модернизации парка оборудования с ЧПУ,
- постоянный мониторинг оборудования,
- корректировку существующих планов с учетом новых тенденций,
- постоянный контроль эффективности уже выполненных мероприятий по модернизации.
Особое внимание следует уделить унификации аппаратных и программных средств, так как почти все предприятия испытывают серьезные проблемы от многообразия эксплуатируемых типов УЧПУ, приводов (начиная от несовместимости УП и различных конструктивных и технических решений и заканчивая многочисленным списком комплектующих, необходимых для ремонта).
В связи с высокими ценами введенными санкциями на новые станки с ЧПУ в наши дни снова приобретает популярность капитальный ремонт с глубокой модернизацией металлообрабатывающего оборудования с ЧПУ.
Для выполнения капитальных ремонтов Технический центр ТОиР оборудования с ЧПУ располагает двумя собственными производственными площадками, оснащенными новейшими диагностическими, измерительными средствами и приборами, инструментом, испытательными стендами и квалифицированными кадрами.
При проектировании капитальных ремонтов мы учитывали основные направления развития станкостроения в мире. Особенно повышение уровня автоматизации капитально отремонтированного оборудования с ЧПУ за счет применения:
- Новых систем ЧПУ
- Систем технического зрения
- Информационных систем
- Новых цифровых приводов
- Новых шпинделей (мотор-шпиндели)
- Новых инструментальных магазинов
И повышение производительности станков с ЧПУ за счет применения прогрессивных комплектующих узлов:
- Новых направляющих
- Новой низковольтной аппаратуры
- Новых цифровых следящих приводов (линейные приводы)
- Новых приводов главного движения и приводов подач
- Быстродействующих устройств автоматической смены инструмента и заготовок
- Высокой степени концентрации технологических операций на одном станке
Основные направления при разработке проектов капитального ремонта с глубокой модернизацией станков с ЧПУ
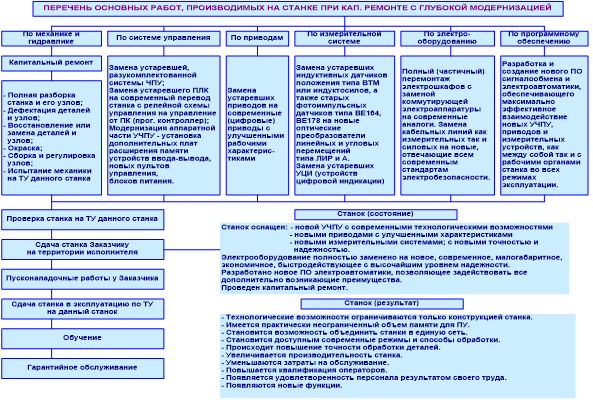
Капитальный ремонт с глубокой модернизацией представляет собой восстановление геометрической точности всех направляющих, замену всех износившихся узлов и деталей, всех подшипников и ШВП, систему ЧПУ и электроавтоматики, ремонт шпинделя, восстановление паспортных характеристик и последующую гарантию на один год.
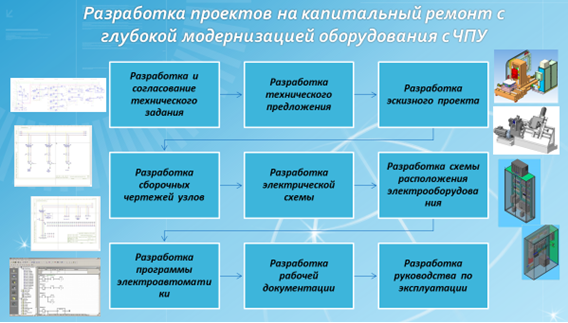
Для организации и проведения работ по капитальному ремонту были выделены два производственных корпуса площадью 1700 кв.м. и 2000 кв.м., а в структуре Технического центра ТОиР были созданы конструкторский отдел и отдел капитального ремонта.
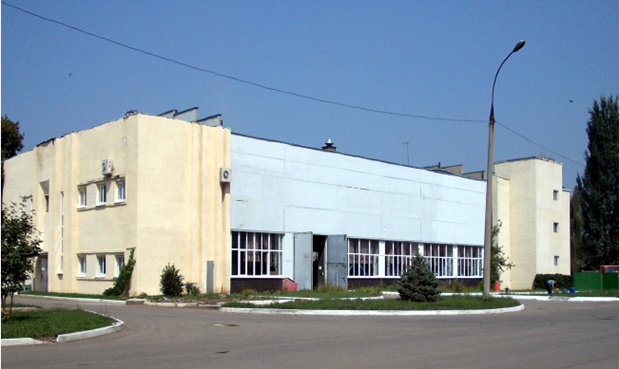
В первом корпусе площадью 1700 кв.м. были организованы 20 рабочих мест для разборки и сборки токарных, фрезерных и многооперационных станков с ЧПУ, оснащенных АРМами с интерактивными панелями, ИРК, склад, тех. бюро и бюро электро-монтажных работ.
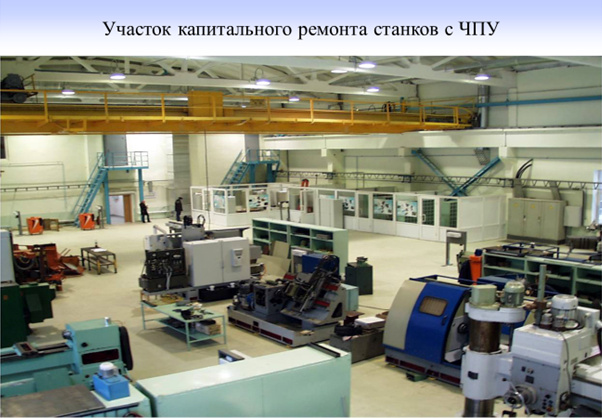
Во втором корпусе, площадью 2000 кв.м. были организованы участки ремонта шпинделей с диагностическими стендами, элементов гидравлики с диагностическими стендами, ШВП, участок экспериментальных работ по внедрению инновационных технологий по мониторингу и диагностике механических узлов.
Капитальный ремонт с глубокой модернизацией оборудования с ЧПУ начинается с разработки технического задания, в формировании которого участвуют производство, служба главного технолога и Технический центр ТОиР. На основании полученного технического задания группа перспективного проектирования разрабатывает эскизный проект будущего станка. На основании одобренного эскизного проекта выполняются проекты по механике, электрике, системотехнике. Определяется комплектация и группа МТС приступает к комплектации. Станок транспортируется на участок капитального ремонта и начинаются работы по разборке, дефектации и диагностики узлов и составлению дефектной ведомости. Проверяем состояние всех направляющих скольжения и особенно наличие закаленного слоя и местного износа для определения глубины шлифовки. После этого мы выполняем шлифовку с последующим контролем геометрической точности и параллельности.
Вот так обычно выглядят направляющие скольжения до шлифовки. Здесь мы видим борозды, сильные разрушения металла, которые возникли от отсутствия смазки и попадания стружки ввиду плохо проводимого ТО.
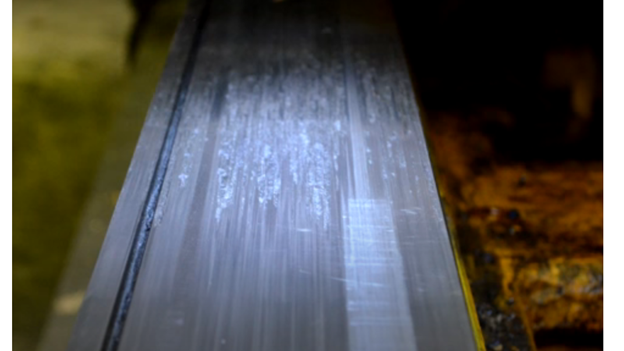
А вот направляющая после шлифовки, выполненной на нашем продольно-шлифовальном станке модели 40-15S4030/6m производства фирмы Waldrich Coburg. Такие направляющие при хорошем уходе будут служить долго.

После шлифовки направляющих наши специалисты переходят к другим узлам, согласно технологическому процессу капитального ремонта этого станка. При проведении работ по капитальному ремонту мы производили и производим 100% замену всех подшипников, гидроаппаратуры. Новые подшипники и гидроаппаратура проходят 100% входной контроль на специализированных стендах. При необходимости производим ремонт ШВП, а если ремонт не возможен, устанавливаем новую. Так как в процессе эксплуатации станков с ЧПУ в течении 30 и более лет на ШВП образовались местные износы винтов, износы дорожек и гаек и износы шариков, которые приводили к накопительной ошибке шага, что приводило к неточности позиционирования. Поэтому мы при проведении капитального ремонта станка устанавливаем новые инновационные ШВП соответствующего класса точности. За время эксплуатации станков на внутренней поверхности конусов шпинделя появляются царапины, задиры и наклепы, что влечет за собой неправильную установку инструментальной оправки. В этом случае появляется биение оправки, которое ускорит износ конуса и подшипников шпинделя. Чтобы восстановить геометрию конуса мы производим шлифовку торцевой и внутренней поверхности конуса шпинделя.
Кроме замены и ремонта механических узлов, мы меняем или ремонтируем гидравлические и пневматические узлы, заменяем всю электрику и систему ЧПУ в стандартной комплектации. На ответственное оборудование и многооперационные станки мы устанавливаем комплектную аппаратуру производства Siemens, низковольтную аппаратуру производства фирм Siemens, Schneider Electric.
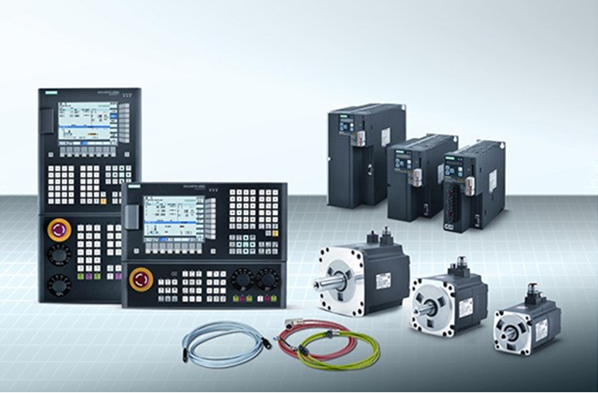
На остальное оборудование устанавливаем комплектные системы производства и комплектации ООО «Балт-Систем» и бюджетную низковольтную аппаратуру.
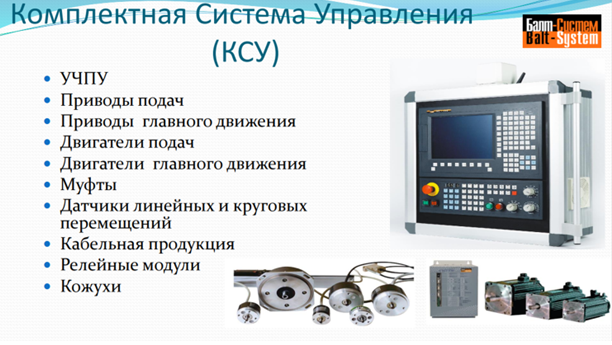
Гидравлическую аппаратуру устанавливаем производства фирм «Bosch», «Hydac», «Festo» и отечественных производителей. Так же мы устанавливаем новейшие высокоточные измерительные системы и датчики обратной связи производства фирм ООО «СКБ ИС», «Precizika», «Heidenhain», «Renishaw» и др.
Кроме того, мы восстанавливаем и улучшаем внешний вид станка. Меняем электрошкаф на новый или дорабатываем старый. Разрабатываем ПЛК для каждой модели и УЧПУ станка.
Пример проекта капитального ремонта с глубокой модернизацией специального фрезерного станка модели СФП 13
Цель проекта – рассмотреть использование капитального ремонта с глубокой модернизацией устаревшего металлорежущего оборудования с ЧПУ под современные технологические задачи с использованием агрегатирования, как одного из экономически обоснованных вариантов, альтернативных покупке нового дорогостоящего оборудования и обеспечить:
- Возможность обработки деталей диаметром до 3500 мм.
- Повышение числа оборотов шпинделя до 12000 об/мин.
- Возможность измерения детали на станке.
- Установку защитного ограждения кабинетного типа.
- Установку инструментального магазина на 60 инструментов..
- Установку отсоса пыли при обработке композитных материалов.
- Решение для увеличения надежности с целью максимально возможного исключения брака
- Аварийный отвод инструмента при всех сбоях.
- Установку датчиков вибрации для проведения мониторинга технического состояния узлов станка.
- Включение в функции контроля за состоянием вибрации.
- Включение S – образной кривой разгона осей станка.
- Установку новых измерительных систем по всем осям.
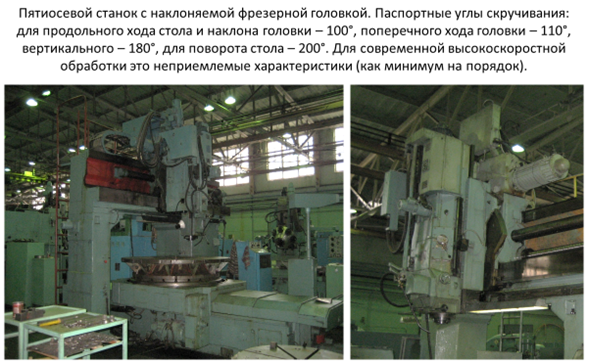
В качестве основного оборудования для проведения капитального ремонта с глубокой модернизацией был взят специальный продольно-фрезерный станок модели СФП 13, 1978 г. выпуска. Станок был оснащен устаревшей цикловой системой ЧПУ «СЦП-5» с цифровой индикацией. С помощью устройства матричной логики программировалась работа вспомогательных устройств электроавтоматики. На станке было установлено четыре шкафа электроавтоматики (шкаф управления шпинделем, 2 шкафа управления приводами подач, шкаф электроавтоматики), которые занимали очень много места, а оборудование, которое было скомпоновано в них, физически и морально устарело. На станке была установлена поворотная шпиндельная бабка.
Основой капитального ремонта с глубокой модернизацией стал модульный принцип изготовления станка. При выполнении проекта нового станка рассматривалась в качестве системы ЧПУ, УЧПУ типа Sinumerik 840D sl с комплектом привода главного движения и приводами подач. В качестве главного привода использован частотный привод с векторным управлением мотор-шпинделем производства фирмы IBAK . Для повышения точности обработки на контуре в качестве датчиков обратной связи использованы оптические линейки по всем трем осям производства фирмы Heidenhain и круговой датчик ROD 426[i]. Был разработан и изготовлен на краснодарском станкозаводе им. Седина накладной стол диаметром 3500 мм. Также была разработана и изготовлена на фирме Hage (Австрия) траверса, длиной 4500 мм. Траверса была изготовлена с проставками длиной 600 мм. для увлечения расстояния от стола до шпинделя. На приводах подач были применены современные планетарные редукторы.
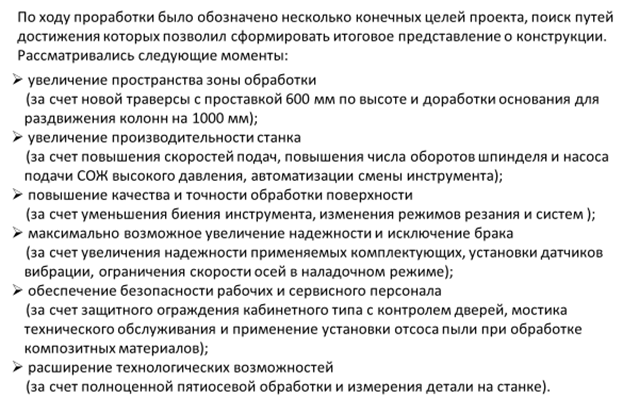
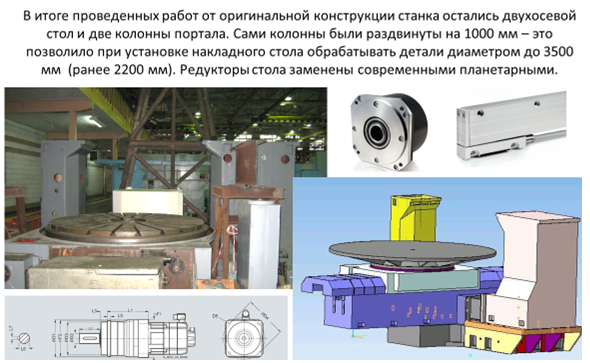
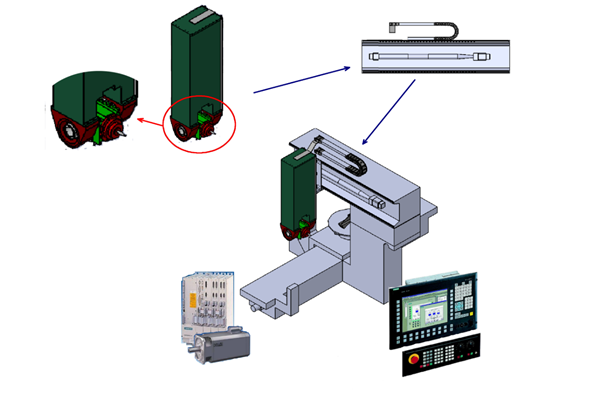
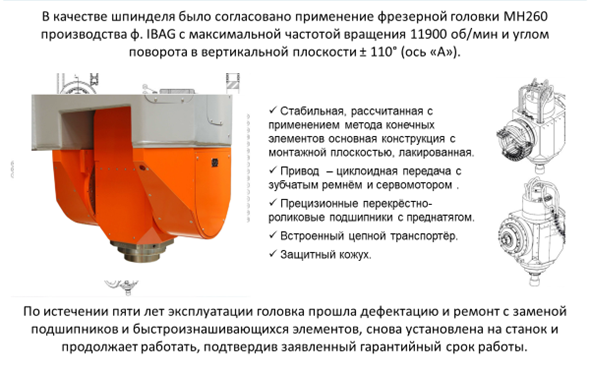
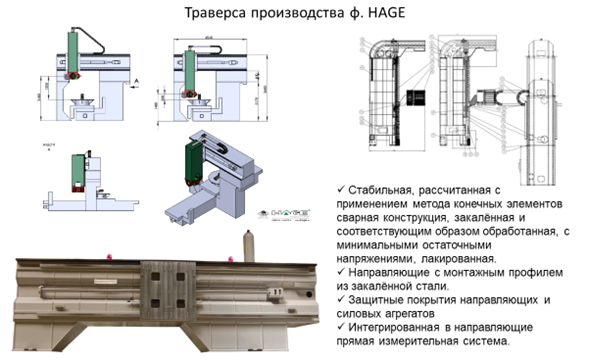
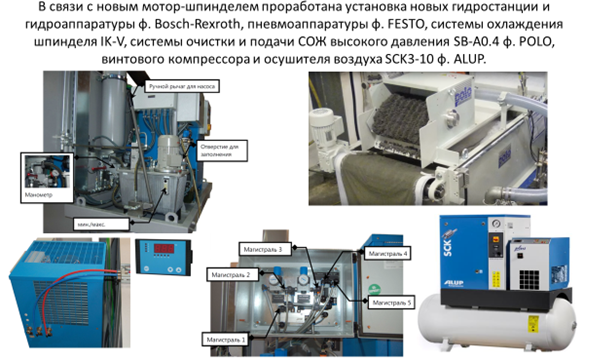
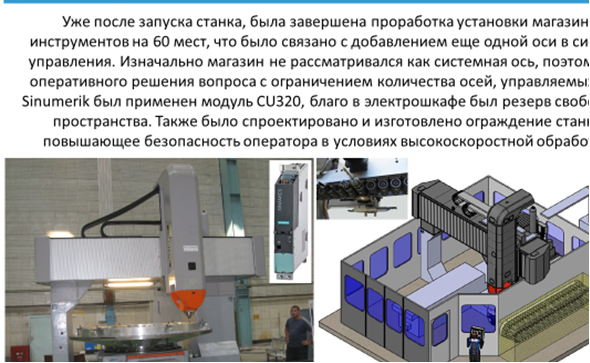
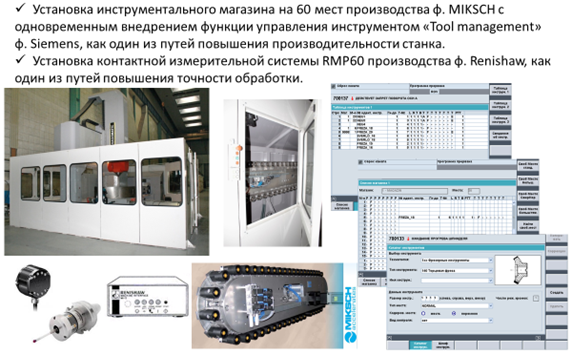
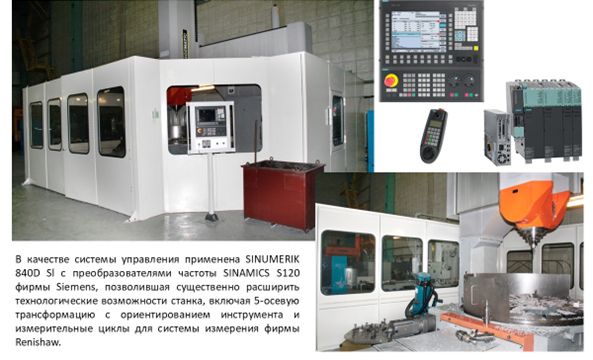
Заключение
Использование агрегатирования позволило в процессе модернизации создать технологическое оборудование под конкретную группу изделий с реализацией оптимального технологического процесса. Одновременное оснащение станка современной системой управления, а также узлами и оборудованием для САМ-технологий и НSМ-технологий позволило получить качественно новый станок c:
-высокой степенью автоматизации,
-высокой производительностью (производительность повысилась в 3-4 раза по отношению к старому),
-возможностью проводить 5-осевую обработку,
-возможность проводить высокоскоростную обработку,
-возможность мониторить техническое состояние станка,
-возможность отключения станка в следствии нарушения технологии обработки, при вероятности столкновения шпинделя с деталью в случае выхода за допустимые пределы технического состояния узлов,
-возможностью применять адаптивное управление процессом резания,
-возможностью проводить измерения детали непосредственно на станке
-возможностью проводить автоматические измерения объемной геометрической точности с последующей автоматической коррекцией.
Результатами контрольных испытаний было подтверждено, что гарантированная точность линейного размера при чистовой обработке на круговом контуре 500 мм составляет не более 0,02–0,03 мм. При этом скорость рабочей подачи доходит до 2 м/мин... Для повышения качества обработки карманов и вафельного фона была применена технология HSM – с использованием высокоскоростного мотор-шпинделя производства фирмы IBAG.
После проведения капитального ремонта с глубокой модернизацией специального фрезерного станка модели СФП 13 по модульному принципу мы значительно расширили технологические возможности станка. Сочетание различных компоновок модулей и сквозная CAD/CAM-технология по 3D-моделям позволяют последовательно обрабатывать практически любые сложные детали за одну-две установки без непосредственного участия станочника. Отсутствует субъективный фактор, качество определяется только технологией и возможностью оборудования. В зависимости от текущего задания на одном станке осуществляются различные варианты современной многоосевой обработки с элементами технологии HSM, такие как технологии обработки вафельного фона на плоских и цилиндрических деталях. Данная технология позволила вести обработку наружного и внутреннего контуров крупногабаритных цилиндрических и конусообразных деталей из алюминиевых сплавов в сочетании с высокопроизводительной высокоскоростной обработки в 5-осевом режиме (благодаря высокой жесткости станка и современным приводам главного движения, приводов подачи и системы ЧПУ, производства фирмы Siemens). Оптимально подобранные режимы резания (обороты шпинделя от50–до 12000 об/мин, глубина резания – 4 мм, подача до 6 м/мин) при использовании фрез диаметром 50 мм обеспечивают скорость съема металла до 1,2*106 мм3/мин, что является одним из основных факторов, определяющих эффективность металлообработки. Стоит отметить, что фрезерование алюминиевых сплавов осложняется их способностью налипать на инструмент при нагреве заготовки от процесса резания. Нами была отработана технология кольцевого обдува инструмента воздухом, при котором процесс резания находился в температурном режиме, исключающем налипание стружки, а поверхность обработки всегда была чистой. Использование воздуха для охлаждения инструмента особенно важно при фрезеровании глубоких карманов, когда затруднено применение традиционных смазочно-охлаждающих жидкостей (СОЖ). Для пятиосевой обработки деталей, а также пространственного сверления точных отверстий в крупных цилиндрических и сферических деталях критичными параметрами деталей с вафельным фоном и шпангоутов является точное позиционирование отверстий, карманов и ячеек и шаг между отверстиями и ячейками. При попытке изготовления данных деталей на старом станке был большой процент брака и низкая производительность. Данная головка значительно расширяет технологические возможности станка, поскольку она позволяет установку на столе с горизонтальным закреплением деталей вращения диаметром до 3,5 м.
В этом случае мы получили оборудование, способное реализовывать токарные и фрезерные, сверлильные и расточные операции на одном станке без переустановки. Разработанная технология капитального ремонта с глубокой модернизацией по модульному принципу позволяет перейти на более высокий уровень проведения работ. Кроме того, капитально отремонтированный с глубокой модернизацией станок модели СФП 13 ведет работу в CAD/CAM-системе напрямую с 3D-моделями с сетевой поддержкой на всех уровнях и тем самым снижает издержки производства в 3- 5 раза. Технология практически полностью исключает человеческий фактор при производстве изделий и не требует обслуживающего персонала высокой квалификации.
Итак, подведем итог.
Проведена модернизация под конкретные технологические задачи по модульному принципу, в результате получен станок с новыми техническими возможностями:
– во-первых, он совмещает токарные, сверлильные и фрезерные операции на одном станке. При этом, проводя обработку за одну установку, мы не только повышаем общую производительность и качество обработки, но и значительно уменьшаем общие затраты;
– во-вторых, учитывая, что используем CAD/CAM-систему напрямую с 3D-моделями и со сквозной сетевой поддержкой, это позволяет исключить субъективный фактор, что также повышает качество обработки;
– в-третьих, используя современные комплектующие, мы получили технические характеристики капитально отремонтированного с глубокой модернизацией станка, значительно превосходящие характеристики старого станка.
В частности, после капитального ремонта с глубокой модернизацией станка модели СФП-13, точность его обработки показала:
- ошибку измерительной системы 0,01 мм на метр длины против 0,1 мм на метр длины в обычном исполнении (паспорт станкаСФП-13),
- погрешность позиционирования реальная по осям Y и Z не больше 0,01 мм, по оси X не больше 0,03 мм.
Можно сделать вывод, что при правильном подходе к капитальным ремонтам, анализе выпускаемой продукции и экономическом обосновании- капитальный ремонт с глубокой модернизацией может быть рациональным решением обновления станочного парка.
Описанный выше капитальный ремонт с глубокой модернизацией станка модели СФП 13 был выполнен на базе действующего Технического центра ТОиР оборудования с ЧПУ АО”РКЦ “ПРОГРЕСС”, занимающегося ТОиР и капитальным ремонтом с глубокой модернизацией оборудования с ЧПУ.