«В настоящее время вектор повышения эффективности работы предприятий машиностроения направлен на повышение надежности работы оборудования за счет применения инновационных стратегий ТОиР оборудования с ЧПУ».
В данной статье я путём систематизации отечественного опыта, а также адаптации лучших зарубежных практик раскрою сущность и содержание эволюции системы ТОиР оборудования с ЧПУ на одном крупном машиностроительном предприятии за период с 1976 года до настоящего времени за счет применения инновационных форм стратегий ТОиР оборудования с ЧПУ, которые служат основой для внедрения инновационных инструментов с целью постоянного комплексного совершенствования системы управления ТОиР оборудования с ЧПУ. Будут рассмотрены основные этапы и тенденции эволюции технического обслуживания и ремонта оборудования с ЧПУ начиная с 1976 года и до наших дней, а также выделены особенности стратегий системы ТОиР оборудования с ЧПУ.
С начала ХX века техническое обслуживание и ремонт оборудования прошли долгий путь в своем развитии. Но сегодня я подробно рассмотрю основные этапы, особенности и тенденции эволюции данной области деятельности, начиная с 1976 года и до наших дней.
Формы организации системы ТОиР
В процессе разработки системы ТОиР оборудования с ЧПУ были проработаны варианты эффективных методов управления процессом управления ТОиР оборудования с ЧПУ. На эффективность работы системы ТОиР оборудования с ЧПУ непосредственное влияние оказывает форма организации технического обслуживания и ремонта. Существовали и существуют три формы организации управления ТОиР: децентрализованная, централизованная и смешанная.
Какую форму организации ТОиР оборудования с ЧПУ применить?
Анализируя причины потерь, мы пришли к выводу, что часть из них связана с техническим состоянием оборудования, его отказами и неисправностями. Но как добиться необходимого уровня надежности техники? И как это сделать, чтобы не увеличивать затраты на техобслуживание и не останавливаться на плановое ТО для обеспечения идеального состояния? Да и нужно ли это делать для всего (очень разношерстного) парка оборудования? А как понять, в какой момент важнее всего иметь это идеальное состояние? А как успеть все привести в порядок за короткое время и с ограниченным количеством персонала?
Мы начали с теории.
Теория и практика ТОиР
Техническое обслуживание и ремонт (ТОиР) оборудования на огромном комбинате — сложный и запутанный процесс. Начнем с начала.
В процессах ТОиР выделяют три подхода:
Реактивное обслуживание.
Агрегат работает до отказа. Ремонтируют его только после аварийной остановки.
Превентивное обслуживание.
Это плановые ремонты и профилактика по регламенту.
Проактивное обслуживание.
Этот подход основан на контроле состояния и диагностики оборудования, построении трендов и предсказании выхода узлов из строя.
Это значит, при планировании ТОиР нужно учитывать множество факторов: критичность техники в момент времени, влияние на смежное оборудование, наличие резерва, экономическую целесообразность, загрузку. А еще есть требования законодательства к состоянию определенных видов механизмов!
В общем, когда начинаешь погружаться в теорию, голова идет кругом. Как же это освоить на практике?
Поиски решения привели нас к идее технического обслуживания, ориентированного на надежность (ТООН или RCM — Reliability Centered Maintenance). Эта методология позволяет выстроить управление процессами ТОиР таким образом, чтобы достигать требуемого уровня готовности оборудования с минимальными затратами. Звучит, как то, что нам надо.
В практике отечественных предприятий действуют три системы административно-технического управления ТОиР оборудования с ЧПУ:
Выглядит это так:
В данной статье я путём систематизации отечественного опыта, а также адаптации лучших зарубежных практик раскрою сущность и содержание эволюции системы ТОиР оборудования с ЧПУ на одном крупном машиностроительном предприятии за период с 1976 года до настоящего времени за счет применения инновационных форм стратегий ТОиР оборудования с ЧПУ, которые служат основой для внедрения инновационных инструментов с целью постоянного комплексного совершенствования системы управления ТОиР оборудования с ЧПУ. Будут рассмотрены основные этапы и тенденции эволюции технического обслуживания и ремонта оборудования с ЧПУ начиная с 1976 года и до наших дней, а также выделены особенности стратегий системы ТОиР оборудования с ЧПУ.
С начала ХX века техническое обслуживание и ремонт оборудования прошли долгий путь в своем развитии. Но сегодня я подробно рассмотрю основные этапы, особенности и тенденции эволюции данной области деятельности, начиная с 1976 года и до наших дней.
Формы организации системы ТОиР
В процессе разработки системы ТОиР оборудования с ЧПУ были проработаны варианты эффективных методов управления процессом управления ТОиР оборудования с ЧПУ. На эффективность работы системы ТОиР оборудования с ЧПУ непосредственное влияние оказывает форма организации технического обслуживания и ремонта. Существовали и существуют три формы организации управления ТОиР: децентрализованная, централизованная и смешанная.
Какую форму организации ТОиР оборудования с ЧПУ применить?
Анализируя причины потерь, мы пришли к выводу, что часть из них связана с техническим состоянием оборудования, его отказами и неисправностями. Но как добиться необходимого уровня надежности техники? И как это сделать, чтобы не увеличивать затраты на техобслуживание и не останавливаться на плановое ТО для обеспечения идеального состояния? Да и нужно ли это делать для всего (очень разношерстного) парка оборудования? А как понять, в какой момент важнее всего иметь это идеальное состояние? А как успеть все привести в порядок за короткое время и с ограниченным количеством персонала?
Мы начали с теории.
Теория и практика ТОиР
Техническое обслуживание и ремонт (ТОиР) оборудования на огромном комбинате — сложный и запутанный процесс. Начнем с начала.
В процессах ТОиР выделяют три подхода:
Реактивное обслуживание.
Агрегат работает до отказа. Ремонтируют его только после аварийной остановки.
- Плюсы: не останавливаемся на плановые ТО.
- Минусы: аварийный ремонт, как правило, дольше, дороже планового и срывает сроки производства продукции.
Превентивное обслуживание.
Это плановые ремонты и профилактика по регламенту.
- Плюсы: не допускаем критичного износа, минимизируем аварии, обеспечиваем план производства.
- Минусы: часто "переобслуживаем" оборудование — останавливаем агрегат и меняем запчасти, когда их состояние вполне позволяло поработать еще некоторое время.
Проактивное обслуживание.
Этот подход основан на контроле состояния и диагностики оборудования, построении трендов и предсказании выхода узлов из строя.
Это значит, при планировании ТОиР нужно учитывать множество факторов: критичность техники в момент времени, влияние на смежное оборудование, наличие резерва, экономическую целесообразность, загрузку. А еще есть требования законодательства к состоянию определенных видов механизмов!
В общем, когда начинаешь погружаться в теорию, голова идет кругом. Как же это освоить на практике?
Поиски решения привели нас к идее технического обслуживания, ориентированного на надежность (ТООН или RCM — Reliability Centered Maintenance). Эта методология позволяет выстроить управление процессами ТОиР таким образом, чтобы достигать требуемого уровня готовности оборудования с минимальными затратами. Звучит, как то, что нам надо.
В практике отечественных предприятий действуют три системы административно-технического управления ТОиР оборудования с ЧПУ:
- децентрализованная система обеспечения ТОиР оборудования.
- централизованная система обеспечения ТОиР оборудования.
- смешанная система обеспечения ТОиР оборудования.
Выглядит это так:
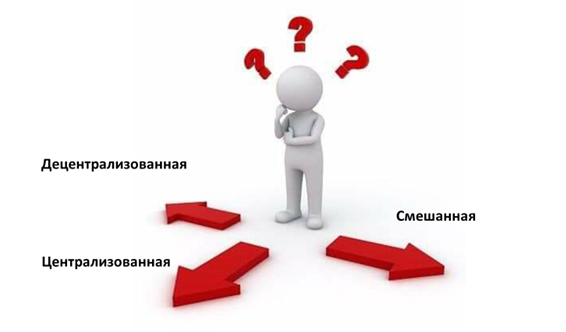
Децентрализованная форма характеризуется отсутствием специализированных ремонтных служб на предприятии. Все работы обычно выполняют сотрудники ремонтных мастерских и бригад отделов главного механика и отдела главного энергетика. Недостатком такой формы организации является не всегда рациональное использование времени работы персонала: трудности в его равномерной загрузке в соответствии с квалификацией, трудности в снабжении инструментом и в создании резервов запасных частей.
Централизованная форма подразумевает наличие специализированной структуры по ремонту оборудования в составе предприятия, несущей всю полноту ответственности за обеспечение работоспособности оборудования. Преимуществом централизованной формы является создание мощных специализированных бригад по ремонту с высокой квалификацией, что снижает общую численность ремонтного персонала, сокращаются сроки простоя, предоставляются широкие возможности для обмена опытом ремонта, внедрения новых методов, применения новейшего оборудования и инструментов. Недостатком является необходимость обеспечения для этого дополнительных ресурсов предприятия.
Смешанная форма организации ТОиР осуществляется на основе широкого диапазона децентрализованной и централизованной форм, отличающихся различной степенью детализации. Смешанная форма используется на предприятиях с небольшим штатом ремонтного персонала, который выполняет текущие и внеплановые ремонты. Для выполнения капитальных ремонтов и реконструктивных работ привлекаются сторонние предприятия, выполняющие централизованные ремонты. Смешанная форма организации ремонтных работ используется, если оказывается наиболее экономичной для конкретного предприятия по сравнению с другими формами.
Российские предприятия обычно внедряют смешанную форму управления, зарубежные предприятия чаще практикуют централизованные формы управления.
Рассмотрим хронологию развития службы ТОиР оборудования с ЧПУ на предприятии.
До 1981 года для проведения ТОиР оборудования с ЧПУ на предприятии использовалась децентрализованная форма, и ремонтные работы оборудования с ЧПУ проводили ремонтные службы предприятия по принадлежности, согласно схеме, показанной на нижерасположенном рисунке, при работе по реактивной стратегии ТОиР оборудования с ЧПУ до отказа и ППР после поломки.
Централизованная форма подразумевает наличие специализированной структуры по ремонту оборудования в составе предприятия, несущей всю полноту ответственности за обеспечение работоспособности оборудования. Преимуществом централизованной формы является создание мощных специализированных бригад по ремонту с высокой квалификацией, что снижает общую численность ремонтного персонала, сокращаются сроки простоя, предоставляются широкие возможности для обмена опытом ремонта, внедрения новых методов, применения новейшего оборудования и инструментов. Недостатком является необходимость обеспечения для этого дополнительных ресурсов предприятия.
Смешанная форма организации ТОиР осуществляется на основе широкого диапазона децентрализованной и централизованной форм, отличающихся различной степенью детализации. Смешанная форма используется на предприятиях с небольшим штатом ремонтного персонала, который выполняет текущие и внеплановые ремонты. Для выполнения капитальных ремонтов и реконструктивных работ привлекаются сторонние предприятия, выполняющие централизованные ремонты. Смешанная форма организации ремонтных работ используется, если оказывается наиболее экономичной для конкретного предприятия по сравнению с другими формами.
Российские предприятия обычно внедряют смешанную форму управления, зарубежные предприятия чаще практикуют централизованные формы управления.
Рассмотрим хронологию развития службы ТОиР оборудования с ЧПУ на предприятии.
До 1981 года для проведения ТОиР оборудования с ЧПУ на предприятии использовалась децентрализованная форма, и ремонтные работы оборудования с ЧПУ проводили ремонтные службы предприятия по принадлежности, согласно схеме, показанной на нижерасположенном рисунке, при работе по реактивной стратегии ТОиР оборудования с ЧПУ до отказа и ППР после поломки.
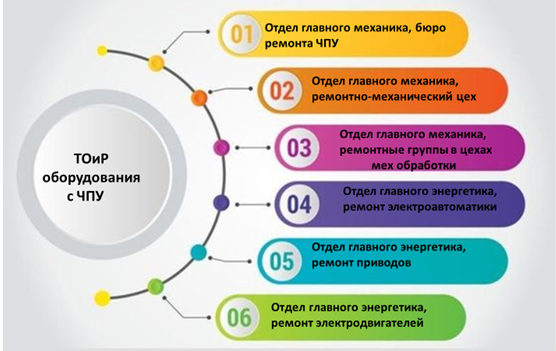
Для этого были объективные причины:
В связи с вводом в эксплуатацию оборудования с ЧПУ в середине 70-х годов для рациональной организации и проведения ТОиР потребовалась разработка новых форм организации управления ТОиР, нормативов и стандартов, регламентирующих документов. Кроме всего при организации ТОиР оборудования с ЧПУ мы столкнулись с многочисленными факторами, такими как:
1981 год - создание централизованной службы ТОиР оборудования с ЧПУ на базе бюро ремонта УЧПУ отдела главного механика.
Стратегия ТОиР оборудования с ЧПУ - ППР. Обязательные ТОиР оборудования с ЧПУ при достижении установленной наработки, с выполнением полного набора ремонтных операций. Обязательный учет простоев оборудования с ЧПУ.
Переход к системе ППР
В СССР нормативы выполнения ТОиР оборудования с ЧПУ устанавливались ведомственными министерствами и были обязательны для выполнения предприятиями, подчиненными данному ведомству. Такое положение дел обусловило необходимость разработки единой системы проведения обслуживающих и ремонтных работ, которая была разработана и обобщена как «Система планово предупредительного ремонта (ППР)», содержащая основные положения и нормативы по ремонту оборудования. Данная система представляет собой комплекс планируемых организационно-технических мероприятий по уходу, надзору, обслуживанию и ремонту оборудования. Среди основных ее особенностей мы можем выделить плановый характер и профилактическую (предупредительную) направленность. Плановый характер предполагает заблаговременное определение состава, объемов и периодичности проведения обслуживающих и ремонтных работ. Профилактическая направленность предполагает выполнение обслуживающих и ремонтных операций до наступления отказа оборудования.
Основой для разработки системы ППР являлись статистические данные, в соответствии с которыми необходимость постановки оборудования в ремонт определялась выходом из строя 5% тестируемого оборудования. Также данная система предусматривает проведение средних и малых ремонтов по специальному графику; межремонтное обслуживание, заключающееся в повседневном уходе и надзоре за оборудованием, в проведении регулировок и мелких ремонтных работ без остановки производственного процесса; периодические осмотры, промывки, испытания на точность, которые проводятся по плану через определенное число часов работы оборудования. Система ППР обладает значительными недостатками, среди которых отметим:
Но, несмотря на это, на многих предприятиях данная система используется и в настоящее время с окончательно устаревшими нормативами разработанными еще в 60-е годы.
На нижерасположенном рисунке показана сема подразделений участников ТОиР оборудования с ЧПУ в 1981 году.
- относительно несложная конструкция станков;
- длительный срок амортизации оборудования, который отрицательно влиял на скудный рынок оригинальных запасных частей;
- неоднозначность организационной структуры обеспечения ремонта.
В связи с вводом в эксплуатацию оборудования с ЧПУ в середине 70-х годов для рациональной организации и проведения ТОиР потребовалась разработка новых форм организации управления ТОиР, нормативов и стандартов, регламентирующих документов. Кроме всего при организации ТОиР оборудования с ЧПУ мы столкнулись с многочисленными факторами, такими как:
- жизненный цикл оборудования;
- ремонтная сложность оборудования по механике, гидравлике, электрике и электронике;
- трудозатраты на ТОиР оборудования с ЧПУ;
- качество и производительность ТОиР;
- материальные ресурсы, затрачиваемые для ремонта;
- трудовые ресурсы и их обучение.
1981 год - создание централизованной службы ТОиР оборудования с ЧПУ на базе бюро ремонта УЧПУ отдела главного механика.
Стратегия ТОиР оборудования с ЧПУ - ППР. Обязательные ТОиР оборудования с ЧПУ при достижении установленной наработки, с выполнением полного набора ремонтных операций. Обязательный учет простоев оборудования с ЧПУ.
Переход к системе ППР
В СССР нормативы выполнения ТОиР оборудования с ЧПУ устанавливались ведомственными министерствами и были обязательны для выполнения предприятиями, подчиненными данному ведомству. Такое положение дел обусловило необходимость разработки единой системы проведения обслуживающих и ремонтных работ, которая была разработана и обобщена как «Система планово предупредительного ремонта (ППР)», содержащая основные положения и нормативы по ремонту оборудования. Данная система представляет собой комплекс планируемых организационно-технических мероприятий по уходу, надзору, обслуживанию и ремонту оборудования. Среди основных ее особенностей мы можем выделить плановый характер и профилактическую (предупредительную) направленность. Плановый характер предполагает заблаговременное определение состава, объемов и периодичности проведения обслуживающих и ремонтных работ. Профилактическая направленность предполагает выполнение обслуживающих и ремонтных операций до наступления отказа оборудования.
Основой для разработки системы ППР являлись статистические данные, в соответствии с которыми необходимость постановки оборудования в ремонт определялась выходом из строя 5% тестируемого оборудования. Также данная система предусматривает проведение средних и малых ремонтов по специальному графику; межремонтное обслуживание, заключающееся в повседневном уходе и надзоре за оборудованием, в проведении регулировок и мелких ремонтных работ без остановки производственного процесса; периодические осмотры, промывки, испытания на точность, которые проводятся по плану через определенное число часов работы оборудования. Система ППР обладает значительными недостатками, среди которых отметим:
- неточность нормативов ремонтного, межремонтного циклов и значительные отклонения фактических данных работы оборудования от плановых.
- не учитываются фактические условия (технологические режимы) работы оборудования.
- не учитывается качество материалов и запасных частей.
- отсутствие достоверных данных о техническом состоянии оборудования.
Но, несмотря на это, на многих предприятиях данная система используется и в настоящее время с окончательно устаревшими нормативами разработанными еще в 60-е годы.
На нижерасположенном рисунке показана сема подразделений участников ТОиР оборудования с ЧПУ в 1981 году.
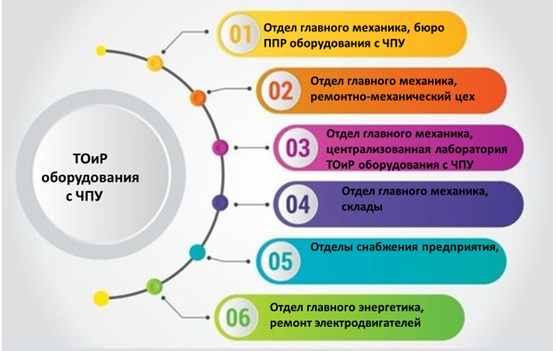
1986 год - внедрение средств диагностики технического состояния оборудования с ЧПУ.
1990 год - внедрение АСУ «Мониторинг технического состояния и диагностики механических узлов станков» и переход на стратегию ППР по техническому состоянию оборудования, такому смещению приоритетов стратегий ТОиР оборудования с ЧПУ способствовала конкурентная среда, быстрое развитие компьютерной техники и появление специальных автоматизированных систем, позволяющих хранить и обрабатывать большие объемы информации по имеющемуся на предприятиях оборудованию. Объемы работ по ТОиР оборудования с ЧПУ и время между ними заранее не фиксируются и определяются из проведенного анализа критичности оборудования, анализа типов и причин отказов. Автоматическое планирование ППР и аварийных ремонтов.
1996 год - разработка АСУ ТОиР оборудования с ЧПУ.
С последующими постоянными улучшениями и внедрением следующих аппаратно-программных средств:
- IBM Maximo – это программное обеспечение, с помощью которого в автоматическом режиме ведётся организация проведения ремонтов, учёт технических характеристик каждой единицы оборудования, история, объёмы и стоимость выполненных ремонтных работ. Перечисленную информацию в IBM Maximo вносят работники бюро диагностики и бюро АСУ ТОиР Технического центра.
- Meridium-APM – автоматизированная система для определения критичного оборудования. Meridium-APM в автоматическом режиме принимает информацию из IBM Maximo, на основе которой работники бюро диагностики Технического центра выявляют наиболее критичное оборудование. Уровень критичности определяется по 4 критериям: степени возможного причинения вреда здоровью работников, объёму возможного нанесения ущерба окружающей среде в случае аварийного выхода из строя, затратам на ремонт и финансовым потерям предприятия от простоя оборудования с ЧПУ. В зависимости от степени критичности сотрудники бюро диагностики Технического центра проводят специальные анализы процессов эксплуатации и ТОиР и технического состояния оборудования. Для обеспечения достоверности и обоснованности результатов аналитической работы осуществляется обмен данными с производством, службой главного технолога. Результаты работы передаются в отдел ТОиР оборудования с ЧПУ в виде рекомендаций по дальнейшему техническому обслуживанию.
-Система учёта простоев оборудования собственной разработки предназначена для фиксации и отправки ответственным специалистам уведомлений о наличии простоев оборудования, архивировании записей по простоям и потерям. Система разделяет простои оборудования на следующие типы:
Все вышеперечисленные автоматизированные системы нацелены на увеличение межремонтных интервалов, исключение внеплановых выходов оборудования из строя, а также снижение затрат на его ремонт и финансовых потерь производства от простоя оборудования с ЧПУ.
1998 год - разработка, внедрение и интегрирование в АСУ «ТОиР оборудования с ЧПУ» нижеперечисленных систем:
-компьютеризированной CMMS-системы управления техническим обслуживанием (CMMS), ориентированной на сокращение затрат на ТОиР оборудования с ЧПУ и повышение коэффициента технической готовности оборудования;
-ЕАМ-системы - системы комплексного управления основными фондами. Главное отличие ЕАМ-систем от CMMS-систем заключается в том, что первые позволяют управлять всем жизненным циклом оборудования, начиная с проектирования, изготовления, монтажа и сборки, работ по ТОиР, модернизации, и списания. Также ЕАМ-система включает в себя систему поддержки принятия решений, например, систему мониторинга эффективности работы оборудования. Результаты внедрений ЕАМ-систем свидетельствует об их высокой эффективности. По моему опыту, применение EAM-системы на нашем предприятии обеспечило и продолжает обеспечивать существенное снижение затрат на ТОиР оборудования с ЧПУ, повышает готовность и производительность оборудования при его использовании в производственных процессах.
В результате внедрения и совместного использования АСУ «ТОиР оборудования с ЧПУ» с системами CMMS и ЕАМ мы получили нижеперечисленные результаты:
В результате внедрения ЕАМ системы мы получили нижеописанные результаты:
2000 год - переход на проактивную стратегию ТОиР оборудования с ЧПУ, которая заключается в выполнении необходимых ремонтных воздействий, направленных на снижение скорости развития и устранения неисправностей, которые были выявлены в результате проведенной диагностики технического состояния узлов оборудования с ЧПУ.
2003 год - создание Технического центра ТОиР оборудования с ЧПУ.
На нижерасположенном рисунке показана схема участников процесса ТОиР оборудования с ЧПУ подразделениями Технического центра.
1990 год - внедрение АСУ «Мониторинг технического состояния и диагностики механических узлов станков» и переход на стратегию ППР по техническому состоянию оборудования, такому смещению приоритетов стратегий ТОиР оборудования с ЧПУ способствовала конкурентная среда, быстрое развитие компьютерной техники и появление специальных автоматизированных систем, позволяющих хранить и обрабатывать большие объемы информации по имеющемуся на предприятиях оборудованию. Объемы работ по ТОиР оборудования с ЧПУ и время между ними заранее не фиксируются и определяются из проведенного анализа критичности оборудования, анализа типов и причин отказов. Автоматическое планирование ППР и аварийных ремонтов.
1996 год - разработка АСУ ТОиР оборудования с ЧПУ.
С последующими постоянными улучшениями и внедрением следующих аппаратно-программных средств:
- IBM Maximo – это программное обеспечение, с помощью которого в автоматическом режиме ведётся организация проведения ремонтов, учёт технических характеристик каждой единицы оборудования, история, объёмы и стоимость выполненных ремонтных работ. Перечисленную информацию в IBM Maximo вносят работники бюро диагностики и бюро АСУ ТОиР Технического центра.
- Meridium-APM – автоматизированная система для определения критичного оборудования. Meridium-APM в автоматическом режиме принимает информацию из IBM Maximo, на основе которой работники бюро диагностики Технического центра выявляют наиболее критичное оборудование. Уровень критичности определяется по 4 критериям: степени возможного причинения вреда здоровью работников, объёму возможного нанесения ущерба окружающей среде в случае аварийного выхода из строя, затратам на ремонт и финансовым потерям предприятия от простоя оборудования с ЧПУ. В зависимости от степени критичности сотрудники бюро диагностики Технического центра проводят специальные анализы процессов эксплуатации и ТОиР и технического состояния оборудования. Для обеспечения достоверности и обоснованности результатов аналитической работы осуществляется обмен данными с производством, службой главного технолога. Результаты работы передаются в отдел ТОиР оборудования с ЧПУ в виде рекомендаций по дальнейшему техническому обслуживанию.
-Система учёта простоев оборудования собственной разработки предназначена для фиксации и отправки ответственным специалистам уведомлений о наличии простоев оборудования, архивировании записей по простоям и потерям. Система разделяет простои оборудования на следующие типы:
- первый - плановую остановку для выполнения работ по ТО,
- второй – внеплановый останов для выполнения аварийных работ,
- третий – внеплановый останов для выяснения причин низкого качества выпускаемой продукции.
Все вышеперечисленные автоматизированные системы нацелены на увеличение межремонтных интервалов, исключение внеплановых выходов оборудования из строя, а также снижение затрат на его ремонт и финансовых потерь производства от простоя оборудования с ЧПУ.
1998 год - разработка, внедрение и интегрирование в АСУ «ТОиР оборудования с ЧПУ» нижеперечисленных систем:
-компьютеризированной CMMS-системы управления техническим обслуживанием (CMMS), ориентированной на сокращение затрат на ТОиР оборудования с ЧПУ и повышение коэффициента технической готовности оборудования;
-ЕАМ-системы - системы комплексного управления основными фондами. Главное отличие ЕАМ-систем от CMMS-систем заключается в том, что первые позволяют управлять всем жизненным циклом оборудования, начиная с проектирования, изготовления, монтажа и сборки, работ по ТОиР, модернизации, и списания. Также ЕАМ-система включает в себя систему поддержки принятия решений, например, систему мониторинга эффективности работы оборудования. Результаты внедрений ЕАМ-систем свидетельствует об их высокой эффективности. По моему опыту, применение EAM-системы на нашем предприятии обеспечило и продолжает обеспечивать существенное снижение затрат на ТОиР оборудования с ЧПУ, повышает готовность и производительность оборудования при его использовании в производственных процессах.
В результате внедрения и совместного использования АСУ «ТОиР оборудования с ЧПУ» с системами CMMS и ЕАМ мы получили нижеперечисленные результаты:
- сокращение на 20% и более затрат на ТОиР оборудования,
- окупаемость внедрения системы за 1,5-2 года.
В результате внедрения ЕАМ системы мы получили нижеописанные результаты:
- Повышение производительности работ по ТОиР оборудования с ЧПУ на 27%.
- Повышение коэффициента готовности оборудования на 31%.
- Сокращение складских запасов на 30%.
- Уменьшение случаев нехватки запасов на 21%.
- Увеличение доли плановых ремонтов на 43%.
- Сокращение аварийных работ на 81%.
- Сокращение сверхурочных работ на 35%.
- Сокращение времени ожидания запчастей на 15%.
- Сокращение срочных закупок ТМЦ на 29%.
- Сокращение длительности ТОиР оборудования с ЧПУ на 40%.
- Уменьшение капитальных затрат (замен)на 30%.
- Сокращение страховых запасов ТМЦ на 63%.
- Сокращение затрат на эксплуатацию на 74%.
- Сокращение неплановых простоев оборудования на 44%.
2000 год - переход на проактивную стратегию ТОиР оборудования с ЧПУ, которая заключается в выполнении необходимых ремонтных воздействий, направленных на снижение скорости развития и устранения неисправностей, которые были выявлены в результате проведенной диагностики технического состояния узлов оборудования с ЧПУ.
2003 год - создание Технического центра ТОиР оборудования с ЧПУ.
На нижерасположенном рисунке показана схема участников процесса ТОиР оборудования с ЧПУ подразделениями Технического центра.
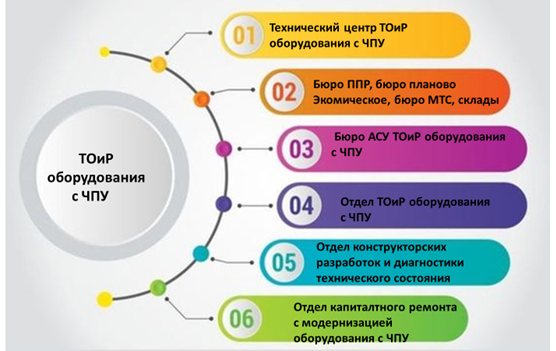
2004 год - разработка и внедрение АСУ «ТОиР оборудования с ЧПУ» с следующими функциями:
И следующими контролируемыми параметрами:
2005 год - организация в структуре Технического центра:
- Ведение нормативно справочной информации по ТОиР оборудования с ЧПУ.
- Паспортизация оборудования с ЧПУ.
- Диагностика технического состояния оборудования с ЧПУ.
- Автоматическое планирование работ по ТОиР оборудования с ЧПУ с составлением план-графика.
- Формирование бюджета на ТОиР оборудования с ЧПУ.
- Ведение контроля за расходования бюджета на ТОиР оборудования с ЧПУ.
- Автоматическое ведение и обработка план-заданий на плановые и аварийные работы.
- Организация обеспечения запчастями и материалами для проведения ТОиР оборудования с ЧПУ.
- Организация учета запчастей и материалов для ТОиР оборудования с ЧПУ.
- Организация контроля за выполнение ТОиР оборудования с ЧПУ и расходованием запчастей и материалов.
- Организация анализа фактических затрат на ТОиР оборудования с ЧПУ.
И следующими контролируемыми параметрами:
- Фактическая продолжительность выполнения плановых и аварийных ТОиР оборудования с ЧПУ.
- Фактическая трудоемкость ТОиР оборудования с ЧПУ.
- Фактическая стоимость ТОиР оборудования с ЧПУ.
- Коэффициент технической готовности оборудования с ЧПУ.
- Общая эффективность работы оборудования с ЧПУ (единицы, цеха, предприятия).
- Общая эффективность работы ремонтника, ремонтного бюро, отдела ТОиР оборудования с ЧПУ.
2005 год - организация в структуре Технического центра:
- отдела капитального ремонта станков с ЧПУ, организационная структура которого показана на нижерасположенном рисунке. Отдел капитального ремонта занимается капитальными ремонтами с глубокой модернизацией станков с ЧПУ, капитальным и восстановительными работами узлов станка.
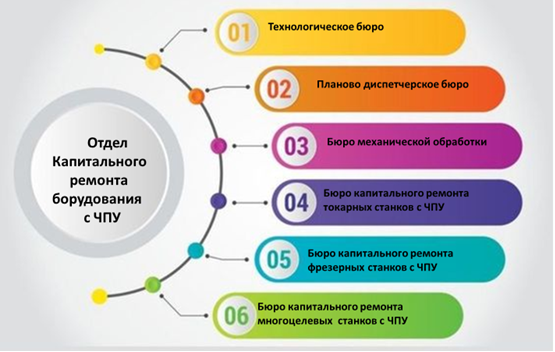
- отдела ТОиР оборудования с ЧПУ, организационная структура которого показана на нижерасположенном рисунке. Отдел ТОиР оборудования с ЧПУ занимается комплексным централизованным ТОиР оборудования с ЧПУ.
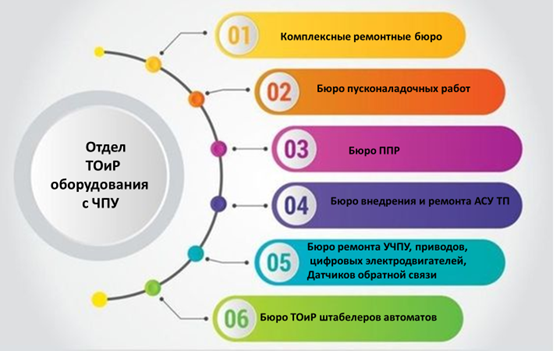
- отдела конструкторских разработок проектов капитальных ремонтов оборудования с ЧПУ, организационная структура которого показана на нижерасположенном рисунке.
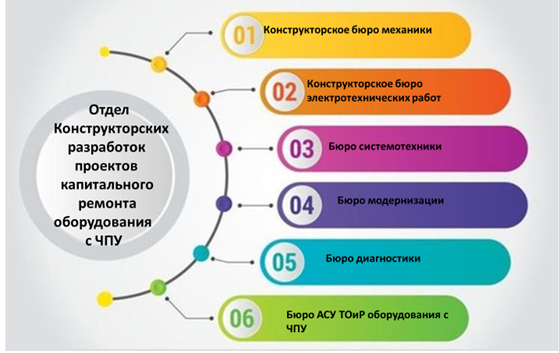
2006 год - разработка АСУ «Мониторинг с глубокой диагностикой технического состояния станков с ЧПУ».
На нижерасположенном рисунке показана блок-схема разработанной АСУ «Мониторинг с глубокой диагностикой технического состояния станков с ЧПУ».
На нижерасположенном рисунке показана блок-схема разработанной АСУ «Мониторинг с глубокой диагностикой технического состояния станков с ЧПУ».
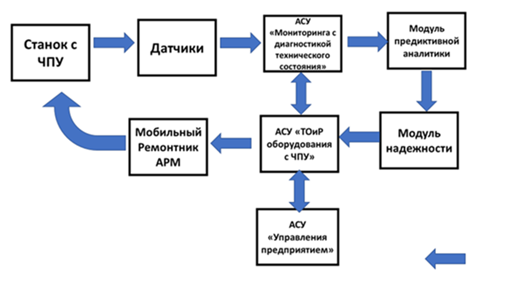
2008 год - внедрение АСУ «Мониторинг с глубокой диагностикой технического состояния станков с ЧПУ» собственной разработки. Переход на проактивную стратегию ТОиР оборудования с ЧПУ. Она позволила в online-режиме на мониторе компьютера визуально определить оборудование, работающее с отклонением от технологических регламентов соответствующих узлов станка.
АСУ «Мониторинг с глубокой диагностикой технического состояния станков с ЧПУ» стала незаменимым помощником для ремонтников Технического центра. Так же данная система стала эффективным инструментом управления процессами ТОиР оборудования с ЧПУ для руководителей процессами ТОиР оборудования предприятий. Она позволяет контролировать работу оборудования, рационально использовать ресурсы, повышать безопасность на предприятии и оптимизировать производство. Все вместе это приводит к повышению производительности и конкурентоспособности предприятия.
2010 год- внедрение интеллектуальной АСУ «Мониторинг с глубокой диагностикой технического состояния узлов станков с ЧПУ» с функциональными блоками:
2012 год - совместная работа по разработке и внедрению Автоматизированной информационной системы АИС «Диспетчер» для мониторинга оборудования с ЧПУ и персонала, которая позволяет контролировать работу любого оборудования и рабочих мест, обеспечивая объективными данные все системы управления предприятием. Данная система введена в эксплуатацию и контролирует работу более 200 станков с ЧПУ.
На нижерасположенном рисунке показана блок-схема работы АИС «Диспетчер».
АСУ «Мониторинг с глубокой диагностикой технического состояния станков с ЧПУ» стала незаменимым помощником для ремонтников Технического центра. Так же данная система стала эффективным инструментом управления процессами ТОиР оборудования с ЧПУ для руководителей процессами ТОиР оборудования предприятий. Она позволяет контролировать работу оборудования, рационально использовать ресурсы, повышать безопасность на предприятии и оптимизировать производство. Все вместе это приводит к повышению производительности и конкурентоспособности предприятия.
2010 год- внедрение интеллектуальной АСУ «Мониторинг с глубокой диагностикой технического состояния узлов станков с ЧПУ» с функциональными блоками:
- сбора данных о техническом состоянии оборудования,
- получения в реальном режиме времени и накопления актуальной информации о состоянии узлов оборудования с ЧПУ и влияющих на это состояние факторов,
- контроля за состоянием оборудования,
- непрерывного контроля в реальном режиме времени за трендами параметров режимов работы и состояния узлов оборудования с генерацией тревог по критическим событиям с оборудованием,
- оценки технического состояния оборудования,
- анализа данных о техническом состоянии оборудования, выявление неисправностей оборудования, определение причин возникновения неисправностей и отказов,
- управления тревогами,
- принятия корректирующих действий для возврата оборудования в работоспособное состояние, предотвращения отказов и снижения связанных с этим материальных издержек,
- оценки эффективности работы оборудования с ЧПУ.
2012 год - совместная работа по разработке и внедрению Автоматизированной информационной системы АИС «Диспетчер» для мониторинга оборудования с ЧПУ и персонала, которая позволяет контролировать работу любого оборудования и рабочих мест, обеспечивая объективными данные все системы управления предприятием. Данная система введена в эксплуатацию и контролирует работу более 200 станков с ЧПУ.
На нижерасположенном рисунке показана блок-схема работы АИС «Диспетчер».
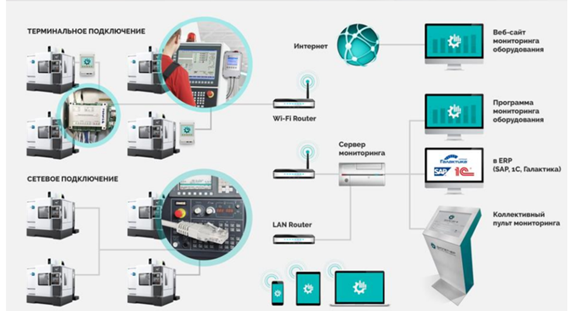
2014 год - организация централизованных участков по ремонту мотор-шпинделей, ШВП, гидроаппаратуры, создание АРМ ремонтника, интегрированных в АСУ «ТОиР».
2017 год - начало работы по созданию модуля «интеллектуальной диагностики», интегрированного в АСУ «Мониторинг».
2018 год - разработка и внедрение модуля «Геометрия станка».
2020 год - разработка и внедрение модуля «Прескриптивная аналитика», интегрированного в АСУ «ТОиР».
2021год - по настоящее время - усовершенствование АСУ ТОиР оборудования с ЧПУ для применения новой стратегии ТОиР оборудования с применением технологий искусственного интеллекта и AR технологий. Переход к стратегии всеобщего технического обслуживания оборудования с ЧПУ (ТРМ), нацеленного на оптимизацию расходов на ТОиР, вовлечение в процесс эффективного обслуживания оборудования всех соприкасающихся с ним сотрудников которая подразумевает эффективное ТОиР.
Это будет следующим этапом усовершенствования стратегии ТОиР, являющейся элементом концепции бережливого производства. Для работы по этой стратегии Техническим центром была проведена большая подготовительная работа, направленная на подготовку операторов к проведению плановых ТО по механике и гидравлике, для чего все они прошли обучение в отделе технического обучения предприятия организации проведения ТО. После этого на предприятии был выпущен приказ о переходе Технического центра «ТОиР оборудования с ЧПУ» на стратегию ТОиР «всеобщего технического обслуживания оборудования с ЧПУ», в котором были установлены зоны ответственности выполнения ТО по механике и гидравлике между операторами и ремонтниками - оператор станка выполняет работы по ТО механики и гидравлики, ремонтники выполняю текущие и аварийные работы. Плановые и аварийные работы по ТОиР систем ЧПУ и электротехнике выполняют только работники Технического центра.
На нижерасположенном рисунке показано распределение обязанностей по выполнению работ по ТОиР оборудования с ЧПУ между операторами станков с ЧПУ и сотрудниками Технического центра «ТОиР оборудования с ЧПУ».
2017 год - начало работы по созданию модуля «интеллектуальной диагностики», интегрированного в АСУ «Мониторинг».
2018 год - разработка и внедрение модуля «Геометрия станка».
2020 год - разработка и внедрение модуля «Прескриптивная аналитика», интегрированного в АСУ «ТОиР».
2021год - по настоящее время - усовершенствование АСУ ТОиР оборудования с ЧПУ для применения новой стратегии ТОиР оборудования с применением технологий искусственного интеллекта и AR технологий. Переход к стратегии всеобщего технического обслуживания оборудования с ЧПУ (ТРМ), нацеленного на оптимизацию расходов на ТОиР, вовлечение в процесс эффективного обслуживания оборудования всех соприкасающихся с ним сотрудников которая подразумевает эффективное ТОиР.
Это будет следующим этапом усовершенствования стратегии ТОиР, являющейся элементом концепции бережливого производства. Для работы по этой стратегии Техническим центром была проведена большая подготовительная работа, направленная на подготовку операторов к проведению плановых ТО по механике и гидравлике, для чего все они прошли обучение в отделе технического обучения предприятия организации проведения ТО. После этого на предприятии был выпущен приказ о переходе Технического центра «ТОиР оборудования с ЧПУ» на стратегию ТОиР «всеобщего технического обслуживания оборудования с ЧПУ», в котором были установлены зоны ответственности выполнения ТО по механике и гидравлике между операторами и ремонтниками - оператор станка выполняет работы по ТО механики и гидравлики, ремонтники выполняю текущие и аварийные работы. Плановые и аварийные работы по ТОиР систем ЧПУ и электротехнике выполняют только работники Технического центра.
На нижерасположенном рисунке показано распределение обязанностей по выполнению работ по ТОиР оборудования с ЧПУ между операторами станков с ЧПУ и сотрудниками Технического центра «ТОиР оборудования с ЧПУ».
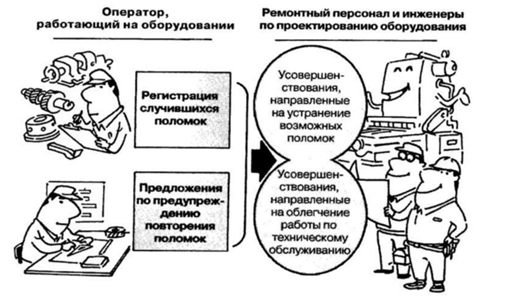
На нижерасположенном рисунке показана блок-схема возможностей современной стратегии ТОиР оборудования с ЧПУ (ТРМ).
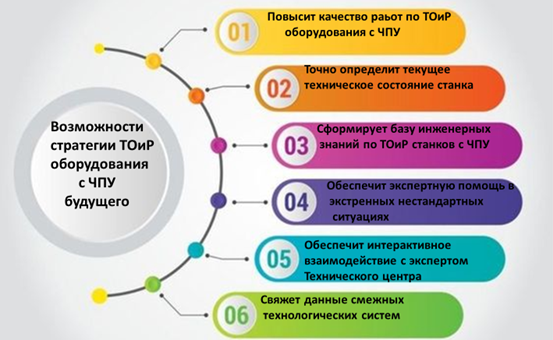
Предприятию, использующему оборудование с ЧПУ, стратегия «Всеобщего технического обслуживания оборудования с ЧПУ» позволит:
В настоящее время наибольший интерес представляет развитие производственной системы TPS, в которой одной из важнейших составляющих является система всеобщего обслуживания оборудования (ТРМ). Система ТРМ была разработана как методика повышения эффективности работы оборудования и повышения срока его службы. Данная система включает набор методов, направленных на то, чтобы каждый станок постоянно находился в работоспособном состоянии, а производство никогда не прерывалось. Таким образом система ТРМ преследовала цель создания работы всего предприятия, в принципы деятельности которого было бы заложено стремление к предельной эффективности производственной системы.
Для реализации внедрения систем TPS и ТРМ необходимо:
Система ТРМ относится к системам обслуживания оборудования по его реальному состоянию. Так, если в типовой системе ППР основанием для определения объекта, сроков и объемов работ по ТОиР оборудования с ЧПУ является наработка оборудования, то при ремонте по техническому состоянию – фактическое состояние оборудования (за исключением работ по техническому обслуживанию).
Применение системы ТРМ позволило достичь следующих результатов:
Результаты в данной области пока незначительны, что связано с большими временными затратами на успешное внедрение и необходимостью изменений в психологии работников и методах работы.
Обобщая вышесказанное и результаты начального периода внедрения систем, я предлагаю руководителям ремонтных служб предприятий рассмотреть данное развитие ТОиР оборудования с ЧПУ для возможности внедрения стратегии ТРМ в своей работе.
Для обеспечения комплексности и полноты представления развития ТОиР оборудования в пространстве и во времени, необходимо выделить нижеперечисленные определенные классификационные признаки:
На этом я заканчиваю данную статью. Желаю хорошего настроения при чтении статьи, буду рад, если материал статьи поможет Вам решить имеющиеся проблемы.
- Определить текущее техническое состояние оборудования.
- Ускорить реагирование работников Технического центра на поломки на 30%.
- Сократить время простоев до 30%.
- Своевременно планировать работы по комплексной диагностике технического состояния узлов оборудования с ЧПУ с глубиной до сборочных деталей.
- Автоматически планировать работы по ТОиР оборудования с ЧПУ, исходя из его технического состояния.
- Создать единую базу знаний и статистики оборудования с ЧПУ, которая позволяет Техническому центру ТОиР контролировать работы по ТОиР, имея оперативную информацию о техническом состоянии оборудования.
- Повысить достоверность технических осмотров, результатов диагностики, контрольных измерений и качество работ по ТОиР.
- Использовать программное обеспечение ServiceVizor для составления планов межремонтных обходов оборудования, фотоотчеты и показания контрольно-измерительных приборов в режиме AR. Работник Технического центра фиксирует результаты технических осмотров и отправляет их в Базу данных АСУ ТОиР. Результаты технических осмотров используются для проверки и расследования инцидентов. В результате время реагирования на поломки сокращается на 30-50%.
- Сформировать базу инженерных знаний по техническому обслуживанию каждого оборудования, включая вспомогательные справочники потребляемых ресурсов при выполнении операций ТОиР оборудования. При этом программное обеспечение ServiceVizor позволяет формировать и хранить историю ТОиР оборудования.
- Обеспечивать удаленную экспертную помощь сотрудникам Технического центра в сложных и нештатных ситуациях от экспертов по своим направлениям, а также интерактивное взаимодействие с работниками технических бюро ТОиР благодаря онлайн-сессиям в режиме AR. Это позволило снизить отказы оборудования по вине персонала до 20%.
- Связать данные смежных учетных и технологических систем и отправлять информацию о результатах выполненных работ ТОиР для учета.
В настоящее время наибольший интерес представляет развитие производственной системы TPS, в которой одной из важнейших составляющих является система всеобщего обслуживания оборудования (ТРМ). Система ТРМ была разработана как методика повышения эффективности работы оборудования и повышения срока его службы. Данная система включает набор методов, направленных на то, чтобы каждый станок постоянно находился в работоспособном состоянии, а производство никогда не прерывалось. Таким образом система ТРМ преследовала цель создания работы всего предприятия, в принципы деятельности которого было бы заложено стремление к предельной эффективности производственной системы.
Для реализации внедрения систем TPS и ТРМ необходимо:
- стремиться к самым высоким показателям работы оборудования;
- сформировать систему производительного технического обслуживания для всего жизненного цикла оборудования;
- развернуть общее производительное обслуживание в службах планирования, разработки нового оборудования, главного инженера, главного механика, в производственных подразделениях;
- сделать акцент на предупреждении и раннем выявлении дефектов оборудования, которые могут привести к более серьезным проблемам с помощью самостоятельного обслуживания оборудования операторами и на работу малых групп. Также обеспечивается повышение такого показателя, как «Полная Эффективность Оборудования», отражающего степень эффективности его использования.
Система ТРМ относится к системам обслуживания оборудования по его реальному состоянию. Так, если в типовой системе ППР основанием для определения объекта, сроков и объемов работ по ТОиР оборудования с ЧПУ является наработка оборудования, то при ремонте по техническому состоянию – фактическое состояние оборудования (за исключением работ по техническому обслуживанию).
Применение системы ТРМ позволило достичь следующих результатов:
- Производительность труда по добавленной стоимости - увеличение в 1,5-2 раза.
- Загруженность оборудования - увеличение в 1,5-2 раза.
- Число случайных поломок и аварий - сокращение в 10-250 раз. Текущее обслуживание оборудования операторами приобретает свою завершенность: они начинают заботиться о своем оборудовании сами, не дожидаясь указаний "сверху".
- Число случаев брака - снижение в 10 раз.
- Себестоимость продукции - снижение на 30%.
Результаты в данной области пока незначительны, что связано с большими временными затратами на успешное внедрение и необходимостью изменений в психологии работников и методах работы.
Обобщая вышесказанное и результаты начального периода внедрения систем, я предлагаю руководителям ремонтных служб предприятий рассмотреть данное развитие ТОиР оборудования с ЧПУ для возможности внедрения стратегии ТРМ в своей работе.
Для обеспечения комплексности и полноты представления развития ТОиР оборудования в пространстве и во времени, необходимо выделить нижеперечисленные определенные классификационные признаки:
- вид технического обслуживания,
- используемый подход,
- преобладающая стратегия системы ТОиР,
- влияющие концепции развития ТОиР оборудования с ЧПУ на предприятии.
На этом я заканчиваю данную статью. Желаю хорошего настроения при чтении статьи, буду рад, если материал статьи поможет Вам решить имеющиеся проблемы.