Необходимо, наконец, взять ситуацию в организации ТОиР оборудования С ЧПУ в свои руки и перестать давать деньгам предприятий утекать сквозь пальцы и получить возможность отдохнуть от постоянной нервотрёпки и забот, имея полный и прозрачный доступ ко всей телеметрии ремонтного производства. Дорогу осилит идущий, а наш путь уже подходит к концу, ведь мы уже нашли то, что искали - это уникальная в своём роде система мониторинга и глубокой диагностики технического состояния узлов станков и визуализации элементов кинематики станков. Ведь с этого момента весь инструментарий и вся информация для принятия верных и взвешенных решений - у вас перед глазами.
В данной статье я продолжу тему “Визуализация элементов кинематики при проведении мониторинга технического состояния узлов станков с ЧПУ”.
Визуализация технического состояния элементов кинематики узлов станков с ЧПУ в статике и динамике – способ представления информации и параметров о техническом состоянии оборудования на мониторе АРМа диагноста или операторской панели мобильного терминала ремонтника в системе АСУ Мониторинг.
В данной статье я продолжу тему “Визуализация элементов кинематики при проведении мониторинга технического состояния узлов станков с ЧПУ”.
Визуализация технического состояния элементов кинематики узлов станков с ЧПУ в статике и динамике – способ представления информации и параметров о техническом состоянии оборудования на мониторе АРМа диагноста или операторской панели мобильного терминала ремонтника в системе АСУ Мониторинг.
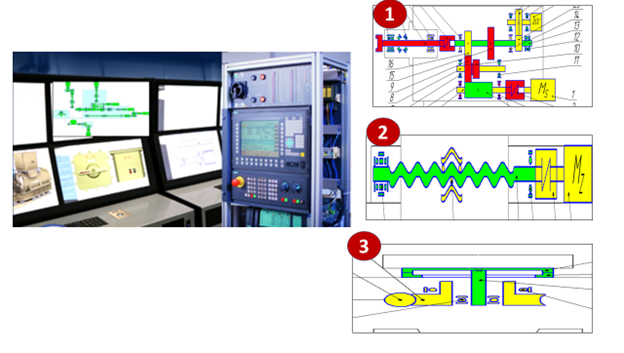
Кинематические схемы узлов станка модели ИР 500ПМФ4
1. Приводы главного движения.
2. Приводы подач.
3 Приводы поворотного стола.
Визуализация элементов кинематики станков реализуется в ряде экранов или окон, которые могут представлять собой древовидную систему. В основе системы визуализации лежит мнемосхема элементов кинематики станков в статике и динамике (состояние элементов кинематики в процессе обработки деталей). Изображения представлены в визуально простой и интуитивно понятной форме, показывающей элементы оборудования и их взаимодействие. Мнемосхемы анимируются, отображая реальное состояние элементов кинематики станка. При этом используем метод ⎯ изменения цвета элементов, зависящий от его технического состояния.
В своей статье я остановлюсь на следующих разделах, рассказывающих о создании системы визуализации технического состояния элементов кинематики станков с ЧПУ.
3. Разработка параметрических моделей кинематических схем приводов станков с ЧПУ.
В данной главе я привожу пример результатов применения теоретических изысканий в практическом их применении при создании параметрических CAD-моделей кинематики станка модели ИР 500 ПМФ4 с ЧПУ.
Желание избежать ненужной работы при выполнении ТОиР оборудования, создать другой способ проверки технического состояния узлов станков и их элементов, определить остаточный ресурс элементов кинематики станков, является главной движущей силой в создании все более совершенных систем автоматизированного анализа виртуальных моделей оборудования с ЧПУ. Для этого используются динамические параметрические модели кинематики станков, в которые CAD-системы входят как один из основных элементов. Для этого мы выполняем следующие работы:
3.1. Строим 3D-модель станка, полностью описывающую конструкцию станка (или его часть)
1. Приводы главного движения.
2. Приводы подач.
3 Приводы поворотного стола.
Визуализация элементов кинематики станков реализуется в ряде экранов или окон, которые могут представлять собой древовидную систему. В основе системы визуализации лежит мнемосхема элементов кинематики станков в статике и динамике (состояние элементов кинематики в процессе обработки деталей). Изображения представлены в визуально простой и интуитивно понятной форме, показывающей элементы оборудования и их взаимодействие. Мнемосхемы анимируются, отображая реальное состояние элементов кинематики станка. При этом используем метод ⎯ изменения цвета элементов, зависящий от его технического состояния.
В своей статье я остановлюсь на следующих разделах, рассказывающих о создании системы визуализации технического состояния элементов кинематики станков с ЧПУ.
3. Разработка параметрических моделей кинематических схем приводов станков с ЧПУ.
В данной главе я привожу пример результатов применения теоретических изысканий в практическом их применении при создании параметрических CAD-моделей кинематики станка модели ИР 500 ПМФ4 с ЧПУ.
Желание избежать ненужной работы при выполнении ТОиР оборудования, создать другой способ проверки технического состояния узлов станков и их элементов, определить остаточный ресурс элементов кинематики станков, является главной движущей силой в создании все более совершенных систем автоматизированного анализа виртуальных моделей оборудования с ЧПУ. Для этого используются динамические параметрические модели кинематики станков, в которые CAD-системы входят как один из основных элементов. Для этого мы выполняем следующие работы:
3.1. Строим 3D-модель станка, полностью описывающую конструкцию станка (или его часть)
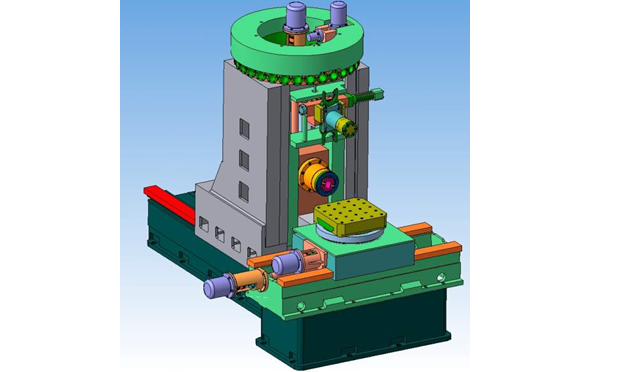
3.2. Описываем работу станка и узлов и делаем кинематический расчет, в ходе которого определяются перемещения, скорости и ускорения всех элементов модели.
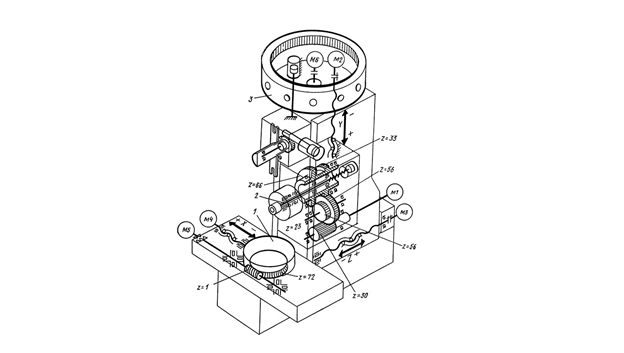
3.3. Далее модель подвергаем динамическому расчету с визуализацией состояния элементов кинематики, в ходе которого определяются силы и моменты, действующие в кинематических схемах, в том числе и реакции во всех соединениях.
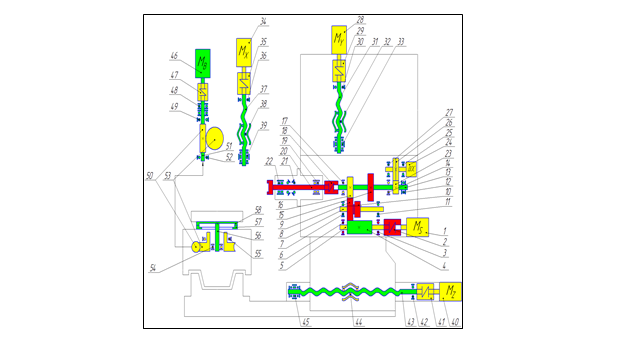
3.4. Применительно к моделированию кинематики механических узлов станков можно выделить следующие основные достоинства:
3.4.1. Интерактивность означает, что система отслеживает попытки инженера внести изменения в кинематику станка, будь то 2D или же 3D-моделирование.
3.4.2. Современные пакеты оснащены целой системой всплывающих окон, интерактивных подсказок. Часто программа предлагает выбирать несколько вариантов применения изменений, разрешается предварительно просмотреть, как будет выглядеть принятая модификация. Также существует возможность отмены нескольких предыдущих действий.
3.4.3. Информативность означает, что каждая модель способна очень многое рассказать о состоянии элементов кинематики станка. Особенно это применимо к 3D-моделям. Возможность вращать модели, увеличивать или уменьшать их, делать произвольные разрезы и сечения, просматривать информацию о массово инерционных характеристиках, видеть зазоры между деталями в сборке и так далее – все это позволяет в одном файле хранить все существенные свойства модели.
3.4.4. Возможность параметризации означает, что можно создавать базы, хранящие в себе все стандартные или широко использующиеся элементы, для которых пользователи могут задавать свои размеры. Пользователи могут и сами параметризировать свои модели, что позволяет изменением нескольких значений мгновенно преобразовать кинематику станка.
3.4.5. Легкость передачи означает, что созданная модель может легко передаваться из одной программы или с одной модели станка на другой, невзирая на различные операционные системы или расстояния. Свойство это тесно связано с универсальностью, которая означает способность использовать модель для различных целей, что предполагает целый комплекс программ. Конечно, совершенно универсальных форматов не существует, но в целом универсальность 3D-моделей во много раз выше цифровых 2D-аналогов, не говоря уже о бумажных вариантах.
4. Создание библиотеки типовых элементов кинематических схем станков
Одним из основных инструментов для параметрического моделирования в современных CAD-системах являются разнообразные библиотеки готовых компонентов. В них, в качестве компонентов могут выступать и 3D-детали. Некоторые CAD-системы позволяют создавать библиотеки не только из уже полностью готовых компонентов, но и из различных элементов.
В соответствии с важностью для производства некоторых моделей оборудования с ЧПУ, бюро мониторинга технического центра была определена фокус-группа станков с ЧПУ, состоящая из следующих моделей:
ИР320 МФ4,
ИР(ИС)500 ПМФ4,
ИР(ИС)800ПМФ,
ИР1250 ПМФ4,
ИР2637,
DMC 60T,
MS3-200,
WFL M40-G 2000,
WFL M40-G 3000,
Hurco VMX24,
Hurco VMX42,
Hurco VM
и ряда других станков, для которых были разработаны параметрические модели кинематики. Все вышеуказанные модели станков были подключены к системе непрерывного мониторинга. В результате проделанной работы была составлена библиотека типовых кинематических элементов приводов станков с ЧПУ.
Изображения кинематических элементов выполнены в САПР КОМПАС-3D V.13 с применением макросов (рис.1.Часть1). Библиотека открыта как для дальнейшего пополнения, так и для использования при составлении параметрических моделей кинематических приводов других станков.
На основании проработки технической документации были составлены кинематические схемы работы приводов станков вышеуказанных моделей в виде как представлено на рисунках ниже (рис.4.1, 4.2). При составлении кинематических схем были соблюдены обозначения кинематических элементов и правила выполнения схем в соответствии с действующими стандартами РФ. Кроме этого, была обеспечена возможность нанесения цветовой индикации на каждый отдельно взятый элемент кинематической схемы, отражающей его техническое состояние.
3.4.1. Интерактивность означает, что система отслеживает попытки инженера внести изменения в кинематику станка, будь то 2D или же 3D-моделирование.
3.4.2. Современные пакеты оснащены целой системой всплывающих окон, интерактивных подсказок. Часто программа предлагает выбирать несколько вариантов применения изменений, разрешается предварительно просмотреть, как будет выглядеть принятая модификация. Также существует возможность отмены нескольких предыдущих действий.
3.4.3. Информативность означает, что каждая модель способна очень многое рассказать о состоянии элементов кинематики станка. Особенно это применимо к 3D-моделям. Возможность вращать модели, увеличивать или уменьшать их, делать произвольные разрезы и сечения, просматривать информацию о массово инерционных характеристиках, видеть зазоры между деталями в сборке и так далее – все это позволяет в одном файле хранить все существенные свойства модели.
3.4.4. Возможность параметризации означает, что можно создавать базы, хранящие в себе все стандартные или широко использующиеся элементы, для которых пользователи могут задавать свои размеры. Пользователи могут и сами параметризировать свои модели, что позволяет изменением нескольких значений мгновенно преобразовать кинематику станка.
3.4.5. Легкость передачи означает, что созданная модель может легко передаваться из одной программы или с одной модели станка на другой, невзирая на различные операционные системы или расстояния. Свойство это тесно связано с универсальностью, которая означает способность использовать модель для различных целей, что предполагает целый комплекс программ. Конечно, совершенно универсальных форматов не существует, но в целом универсальность 3D-моделей во много раз выше цифровых 2D-аналогов, не говоря уже о бумажных вариантах.
4. Создание библиотеки типовых элементов кинематических схем станков
Одним из основных инструментов для параметрического моделирования в современных CAD-системах являются разнообразные библиотеки готовых компонентов. В них, в качестве компонентов могут выступать и 3D-детали. Некоторые CAD-системы позволяют создавать библиотеки не только из уже полностью готовых компонентов, но и из различных элементов.
В соответствии с важностью для производства некоторых моделей оборудования с ЧПУ, бюро мониторинга технического центра была определена фокус-группа станков с ЧПУ, состоящая из следующих моделей:
ИР320 МФ4,
ИР(ИС)500 ПМФ4,
ИР(ИС)800ПМФ,
ИР1250 ПМФ4,
ИР2637,
DMC 60T,
MS3-200,
WFL M40-G 2000,
WFL M40-G 3000,
Hurco VMX24,
Hurco VMX42,
Hurco VM
и ряда других станков, для которых были разработаны параметрические модели кинематики. Все вышеуказанные модели станков были подключены к системе непрерывного мониторинга. В результате проделанной работы была составлена библиотека типовых кинематических элементов приводов станков с ЧПУ.
Изображения кинематических элементов выполнены в САПР КОМПАС-3D V.13 с применением макросов (рис.1.Часть1). Библиотека открыта как для дальнейшего пополнения, так и для использования при составлении параметрических моделей кинематических приводов других станков.
На основании проработки технической документации были составлены кинематические схемы работы приводов станков вышеуказанных моделей в виде как представлено на рисунках ниже (рис.4.1, 4.2). При составлении кинематических схем были соблюдены обозначения кинематических элементов и правила выполнения схем в соответствии с действующими стандартами РФ. Кроме этого, была обеспечена возможность нанесения цветовой индикации на каждый отдельно взятый элемент кинематической схемы, отражающей его техническое состояние.
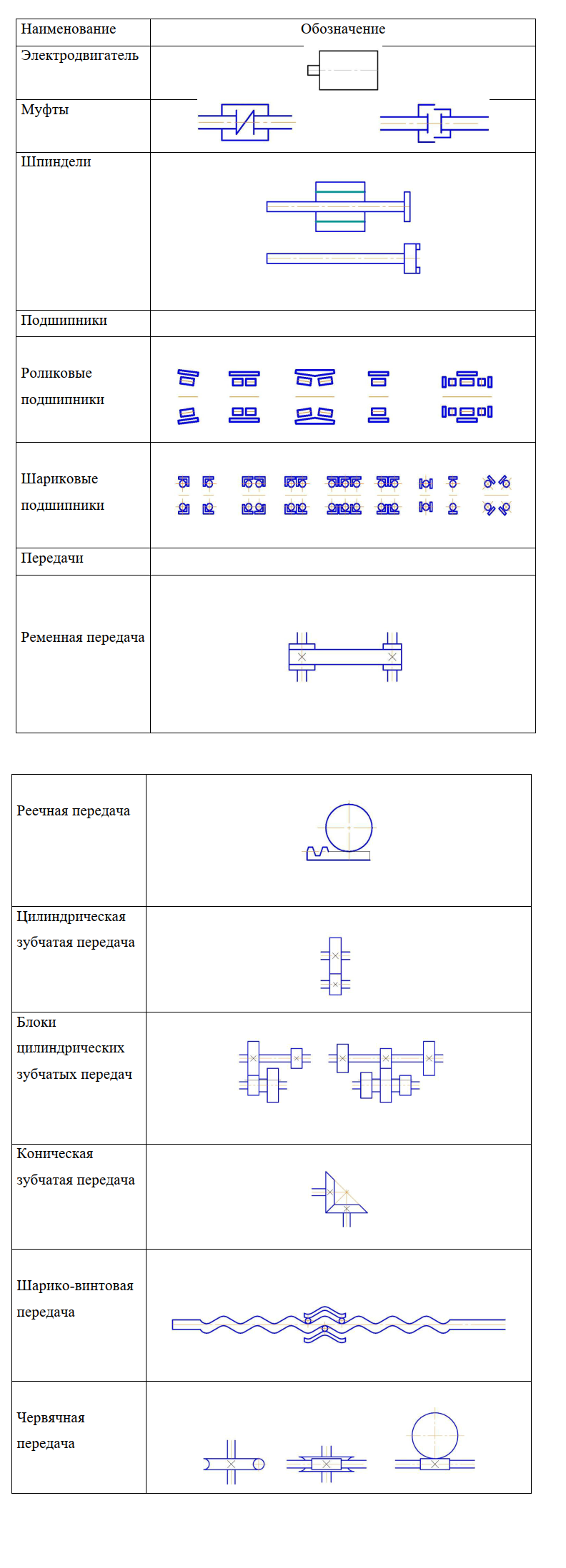
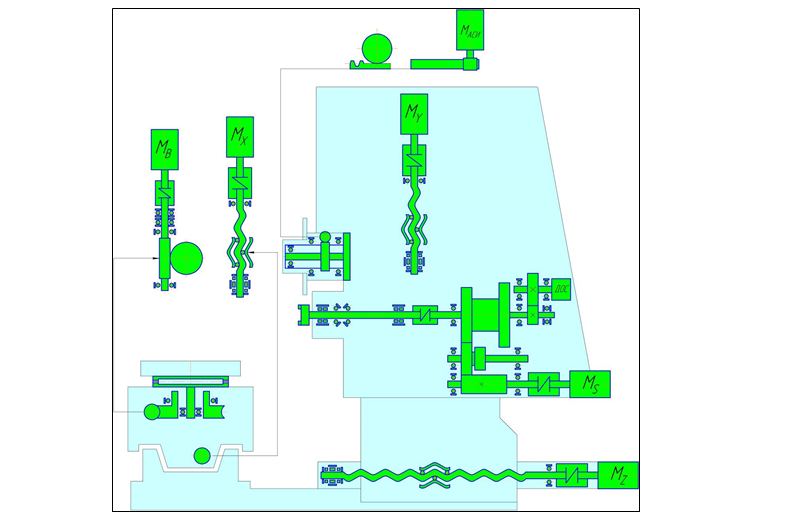
5. Применение метода визуализации кинематических схем в системах мониторинга и глубокой диагностики технического состояния узлов станков с ЧПУ.
5.1. Выбор стратегии ТОиР оборудования с ЧПУ.
Эффективность эксплуатации оборудования с ЧПУ во многом определяется совершенством стратегий технического обслуживания и ремонта.
Действовавшая многие десятилетия планово-предупредительная стратегия технического обслуживания и ремонта станочного оборудования разошлась в последние годы с рыночной системой экономики. Не рассматривая его безусловные достоинства, отметим два основных недостатка:
5.1.1. Неоправданно высокая трудоёмкость, связанная с разборкой всего станка. По результатам осмотра состояния деталей может выясниться, что некоторые узлы можно было не разбирать.
5.1.2. Возможный отказ узла станка в межремонтный период, причинами которого были нарушения в процессе сборки при предшествующем ремонте.
Исходя из вышесказанного, мы в 2008 году в Техническом центре применили стратегию ТОиР по техническому состоянию узлов оборудования и ресурсу работы элементов кинематики станка.
Такой подход существенно снизил затраты на ТОиР, повысил эффективность проведения ТОиР и работы оборудования.
Переход от жёстких сроков межремонтного ресурса к его продлению «по состоянию» без снижения надёжности оборудования с ЧПУ стал возможен, только в результате внедрения следующих мероприятий:
Система мониторинга с глубокой диагностикой текущего технического состояния оборудования с применением средств вибродиагностики была внедрена Техническим центом в 2008 году и на протяжении последующих лет постоянно совершенствовалась.
Внедрение системы мониторинга с глубокой диагностикой технического состояния узлов станков методом вибродиагностики показала очень высокую эффективность при выполнении работ по ТОиР оборудования за счет:
В настоящее время средний возраст станочного оборудования в Японии – 5 лет, в США – 7 лет. Средний возраст станочного оборудования в России – более 18 лет. Коэффициент обновления станочного парка в СССР составлял 5-6% в год, а в настоящее время в России – 0,29%.
Поэтому задача поддержания работоспособности оборудования является весьма актуальной и возможна только на основе объективной информации о текущем его состоянии.
В процессе эксплуатации оборудования ухудшаются его точностные характеристики вследствие естественного процесса износа кинематических пар механической системы, а также вследствие рассогласования работы приводов подач, управляемых системой ЧПУ.
Удобным инструментом, позволяющим руководителю подразделения службы мониторинга и ремонтникам быстро оценить состояние работоспособности узлов станка в цехе предприятия, является внедрение АСУ Мониторинга с глубокой диагностикой технического состояния узлов станков с визуализацией технического состояния элементов кинематики с помощью цветовой индикации на кинематических схемах.
Таким образом, вместо полной разборки станков, требуется лишь частичный разбор тех узлов, где имеются дефектные детали, и устранение конкретных неисправностей, то есть, реально необходимый объем работы сокращается по сравнению с затратным методом Планово-Предупредительного Ремонта (ППР). Также сокращается время ремонта, так как не требуется разбирать исправные узлы и можно заранее заказать требующиеся для замены комплектующие. В тоже время, выявляются практически все параметры, детали и комплектующие, которые требуют регулировки или замены, что служит основанием качественного выполнения ремонта оборудования.
В результате выполненной полной диагностики станка модели ИР 500 ПМФ4 были выявлены основные дефекты элементов кинематики, которые не позволяли выполнить обработку деталей с необходимой точностью. На нижерасположенном рисунке 4.3. показано реальное состояние элементов кинематики шпиндельной бабки в процессе обработки детали. Красным цветом обозначены элементы кинематики, которые необходимо заменить или отремонтировать.
5.1. Выбор стратегии ТОиР оборудования с ЧПУ.
Эффективность эксплуатации оборудования с ЧПУ во многом определяется совершенством стратегий технического обслуживания и ремонта.
Действовавшая многие десятилетия планово-предупредительная стратегия технического обслуживания и ремонта станочного оборудования разошлась в последние годы с рыночной системой экономики. Не рассматривая его безусловные достоинства, отметим два основных недостатка:
5.1.1. Неоправданно высокая трудоёмкость, связанная с разборкой всего станка. По результатам осмотра состояния деталей может выясниться, что некоторые узлы можно было не разбирать.
5.1.2. Возможный отказ узла станка в межремонтный период, причинами которого были нарушения в процессе сборки при предшествующем ремонте.
Исходя из вышесказанного, мы в 2008 году в Техническом центре применили стратегию ТОиР по техническому состоянию узлов оборудования и ресурсу работы элементов кинематики станка.
Такой подход существенно снизил затраты на ТОиР, повысил эффективность проведения ТОиР и работы оборудования.
Переход от жёстких сроков межремонтного ресурса к его продлению «по состоянию» без снижения надёжности оборудования с ЧПУ стал возможен, только в результате внедрения следующих мероприятий:
- внедрения опережающей системы планирования работ по ТОиР;
- внедрения средств и методик мониторинга и диагностирования формообразующих узлов станков;
- проведения регулярного диагностирования технического состояния узлов станков.
Система мониторинга с глубокой диагностикой текущего технического состояния оборудования с применением средств вибродиагностики была внедрена Техническим центом в 2008 году и на протяжении последующих лет постоянно совершенствовалась.
Внедрение системы мониторинга с глубокой диагностикой технического состояния узлов станков методом вибродиагностики показала очень высокую эффективность при выполнении работ по ТОиР оборудования за счет:
- сокращения неплановых и плановых остановок оборудования.
- внедрения АСУ Мониторинг.
В настоящее время средний возраст станочного оборудования в Японии – 5 лет, в США – 7 лет. Средний возраст станочного оборудования в России – более 18 лет. Коэффициент обновления станочного парка в СССР составлял 5-6% в год, а в настоящее время в России – 0,29%.
Поэтому задача поддержания работоспособности оборудования является весьма актуальной и возможна только на основе объективной информации о текущем его состоянии.
В процессе эксплуатации оборудования ухудшаются его точностные характеристики вследствие естественного процесса износа кинематических пар механической системы, а также вследствие рассогласования работы приводов подач, управляемых системой ЧПУ.
Удобным инструментом, позволяющим руководителю подразделения службы мониторинга и ремонтникам быстро оценить состояние работоспособности узлов станка в цехе предприятия, является внедрение АСУ Мониторинга с глубокой диагностикой технического состояния узлов станков с визуализацией технического состояния элементов кинематики с помощью цветовой индикации на кинематических схемах.
Таким образом, вместо полной разборки станков, требуется лишь частичный разбор тех узлов, где имеются дефектные детали, и устранение конкретных неисправностей, то есть, реально необходимый объем работы сокращается по сравнению с затратным методом Планово-Предупредительного Ремонта (ППР). Также сокращается время ремонта, так как не требуется разбирать исправные узлы и можно заранее заказать требующиеся для замены комплектующие. В тоже время, выявляются практически все параметры, детали и комплектующие, которые требуют регулировки или замены, что служит основанием качественного выполнения ремонта оборудования.
В результате выполненной полной диагностики станка модели ИР 500 ПМФ4 были выявлены основные дефекты элементов кинематики, которые не позволяли выполнить обработку деталей с необходимой точностью. На нижерасположенном рисунке 4.3. показано реальное состояние элементов кинематики шпиндельной бабки в процессе обработки детали. Красным цветом обозначены элементы кинематики, которые необходимо заменить или отремонтировать.
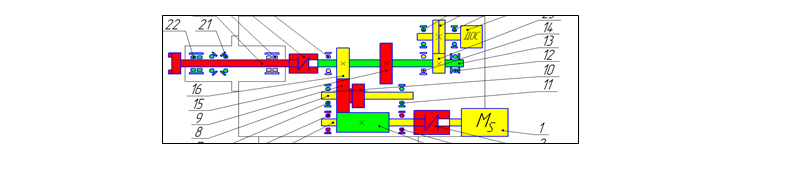
5.2 Состав и алгоритм работы АСУ Мониторинг с глубокой диагностикой
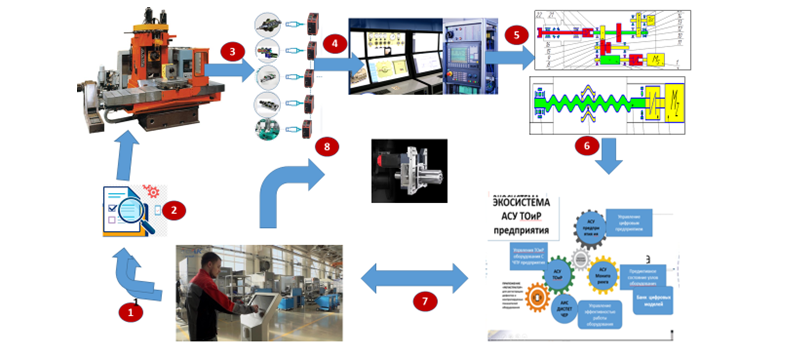
Типовой алгоритм работы АСУ Мониторинг с глубокой диагностикой и поддержания работоспособности станков с ЧПУ имеет следующий вид:
Рассмотрим алгоритм работы ремонтника по отысканию неисправных элементов шпиндельной бабки с использованием АСУ Мониторинг с глубокой диагностикой:
5.2.1. Ремонтник вызывает из архива тест программу диагностики шпиндельной бабки станка модели ИР500 ПМФ4 и устанавливает по разработанной схеме датчики вибрации на шпиндельную бабку.
5.2.2. Запускает в работу станок по Тест программе диагностики шпиндельной бабки станка модели ИР500 ПМФ4, которая предусматривает формирование специальных воздействий, стимулирующего у элементов кинематики станков ответную реакцию, которая сравнивается с эталонной. Роль стимулирующего воздействия выполняют ступенчатые импульсные, гармонические и другие сигналы, которую вводятся, как параметры кинематики (подшипников, шестерен, ШВП), числа оборотов шпинделя и скорости подач приводов подач.
В качестве диагностических показателей используются параметры динамических звеньев, коэффициенты уравнений, обобщенные параметры.
5.2.3. Станок модели ИР 500 ПМФ4 с УЧПУ типа Sinumerik 840 D sl.
- сбор информации;
- оценка информации и выявление отклонений показателей от нормы;
- определение причины отклонения:
- принятие решения и выработка корректирующего воздействия;
- ввод корректирующего воздействия в систему с целью ликвидации отклонения.
Рассмотрим алгоритм работы ремонтника по отысканию неисправных элементов шпиндельной бабки с использованием АСУ Мониторинг с глубокой диагностикой:
5.2.1. Ремонтник вызывает из архива тест программу диагностики шпиндельной бабки станка модели ИР500 ПМФ4 и устанавливает по разработанной схеме датчики вибрации на шпиндельную бабку.
5.2.2. Запускает в работу станок по Тест программе диагностики шпиндельной бабки станка модели ИР500 ПМФ4, которая предусматривает формирование специальных воздействий, стимулирующего у элементов кинематики станков ответную реакцию, которая сравнивается с эталонной. Роль стимулирующего воздействия выполняют ступенчатые импульсные, гармонические и другие сигналы, которую вводятся, как параметры кинематики (подшипников, шестерен, ШВП), числа оборотов шпинделя и скорости подач приводов подач.
В качестве диагностических показателей используются параметры динамических звеньев, коэффициенты уравнений, обобщенные параметры.
5.2.3. Станок модели ИР 500 ПМФ4 с УЧПУ типа Sinumerik 840 D sl.
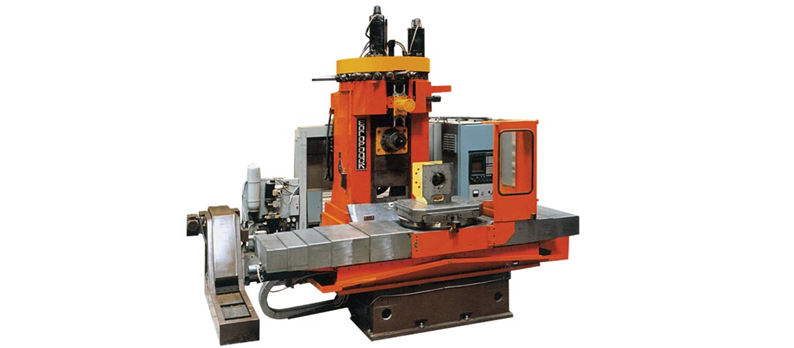
5.2.4. Вибросигнал с датчиков с датчиков поступает в контроллер и Центр обработки полученной
информации. На нижерасположенном рисунке показаны: схема Блока диагностируемых узлов и
практическое расположение датчиков вибрации на корпусе шпинделя и контроллера в электрическом
шкафу станка модели ИР500ПМФ4.
информации. На нижерасположенном рисунке показаны: схема Блока диагностируемых узлов и
практическое расположение датчиков вибрации на корпусе шпинделя и контроллера в электрическом
шкафу станка модели ИР500ПМФ4.
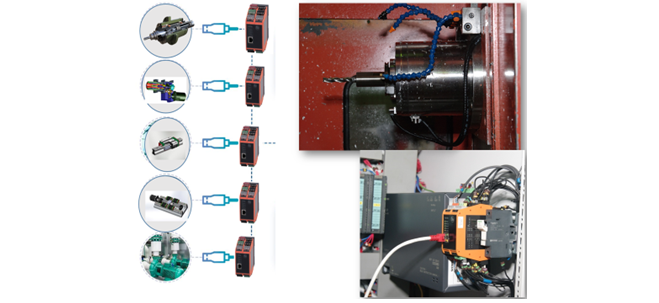
Контроллер предназначен для программирования отслеживания зон работоспособности элементов узлов станков. В процессе работы контроллер проходит два этапа это операции контроля в трех зонах и аварийное отключение при превышении порога начала аварийной зоны. (Пр = Пн (норма), Пр ≤Пн≤ Пот (предупреждение), Пр= Пот (отказ)). На нижерасположенном рисунке показаны зоны запрограммированых уставок возможного состояния элементов шпиндельной бабки, согласно паспортных значений.
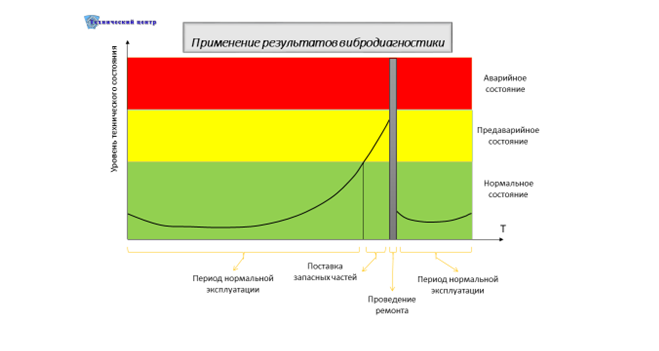
5.2.5. Также вибросигнал поступает в Центр обработки получаемых вибрационных характеристик с мест, где установлены датчики. Для получения сведений о техническом состоянии элементов кинематики используем разработанные силами Технического центра специальные программы обработки полученных вибрационных характеристик, предварительно установив частотный диапазон для их измерения и показателей, характеризующие динамику работы элементов кинематики. На нижерасположенном рисунке показан Центр обработки получаемых вибрационных характеристик. Он состоит из мониторов, подключенных сети АСУ Мониторинг, библиотеки специальных программ, системы ЧПУ и блоков диагностики технического состояния элементов узлов станка.
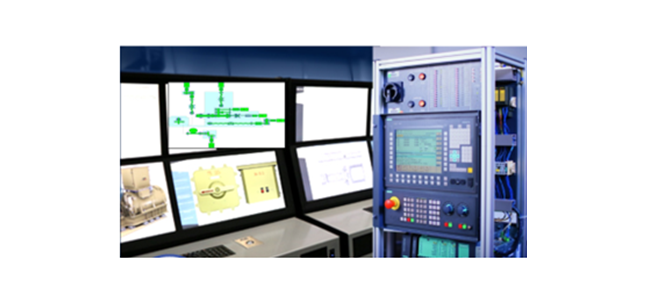
5.2.6. После обработки полученных данных мы получаем результаты диагностики шпиндельной бабки в виде:
5.2.6.1. Вуалированной кинематической схемы.
5.2.6.1. Вуалированной кинематической схемы.
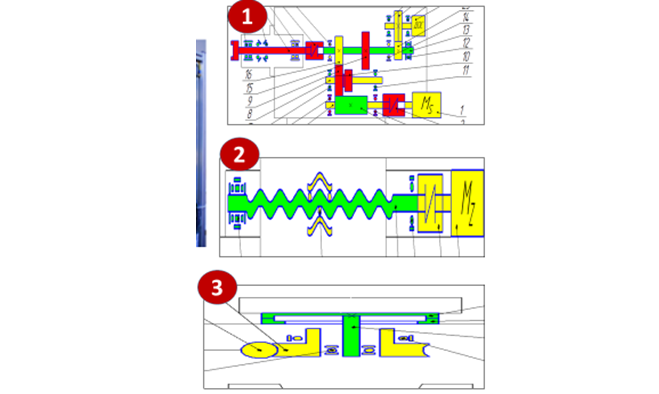
5.2.6.2. Табличной.
5.2.6.3. Протокольной.
5.2.7. Полученные результаты поступают в базу данных ЭКО системы АСУ ТОиР. ЭКО система АСУ ТОиР - это цифровая платформа, интегрировавшая в себя АСУ Мониторинг, АСУ Капитальный ремонт, модуль предиктивной аналитики и много других модулей. Сама ЭКО система интегрирована в систему управления предприятием.
5.2.6.3. Протокольной.
5.2.7. Полученные результаты поступают в базу данных ЭКО системы АСУ ТОиР. ЭКО система АСУ ТОиР - это цифровая платформа, интегрировавшая в себя АСУ Мониторинг, АСУ Капитальный ремонт, модуль предиктивной аналитики и много других модулей. Сама ЭКО система интегрирована в систему управления предприятием.
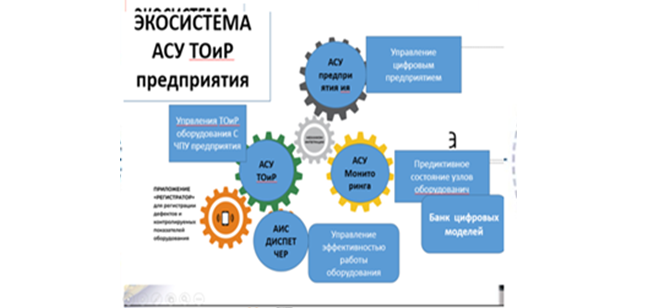
5.2.8. Выполнение работ по ремонту.
В результате проведенной вибродиагностики шпиндельной бабки станка модели ИР 500 ПМФ4 получили визуализированную модель ее кинематики, на которой видны критичные элементы кинематики (окрашенные в красный цвет).
Результаты диагностики показали дефект:
Разборка шпиндельной бабки подтвердила результаты диагностики на 100%:
На этом я заканчиваю данную статью и надеюсь, что изложенный материал поможет Вам при проведении ТОиР оборудования.
В результате проведенной вибродиагностики шпиндельной бабки станка модели ИР 500 ПМФ4 получили визуализированную модель ее кинематики, на которой видны критичные элементы кинематики (окрашенные в красный цвет).
Результаты диагностики показали дефект:
- в виде деформации тел качения двухрядного роликового подшипника.
- в устройстве зажима инструмента.
- в муфте соединения вала двигателя с валом коробки скоростей шпиндельной бабки.
Разборка шпиндельной бабки подтвердила результаты диагностики на 100%:
- В подшипнике были обнаружены деформированные тела качения и износ наружного и внутреннего колец.
- В устройстве зажима инструментальных оправок было обнаружено разрушение 9 тарельчатых пружин.
- В муфте обнаружены начальные разрушения металлического сильфона.
На этом я заканчиваю данную статью и надеюсь, что изложенный материал поможет Вам при проведении ТОиР оборудования.