Уважаемые коллеги и друзья!
В своих статьях я делюсь с Вами своим опытом и накопленными сокровенными знаниями в области организации ТОиР оборудования с ЧПУ на крупном машиностроительном предприятии.
В начале своей деятельности Технический центр ТОиР оборудования с ЧПУ столкнулся с рядом нижеследующих проблем:
Причины:
В последнее время на передовых предприятиях машиностроения стала активно внедряться концепция «Умное ТОиР оборудования с ЧПУ», я эту концепцию в своих статьях называл «Интеллектуальное ТОиР оборудования с ЧПУ».
Поговорим немного о Концепциях ТОиР оборудования и современных тенденциях в управлении ТОиР оборудования.
В настоящее время существуют четыре концепции для построения системы ТОиР оборудования:
3.2. планово-предупредительные ремонты оборудования;
3.3 капитальные ремонты с глубокой модернизацией;
3.4. замена изношенного оборудования на новое;
4. Концепция развивающихся систем ТОиР.
Дальше я поясню, что представляет из себя каждая концепция ТОиР оборудования в отдельности. В этой статье я опишу и оценю вышеупомянутые концепции ТОиР оборудования и покажу, насколько значим был этот подход для Технического центра и будет важен для служб ТОиР оборудования с ЧПУ предприятий ВПК.
Рано или поздно любое оборудование выходит из строя из-за:
И каждый такой отказ влечёт за собой колоссальные расходы, причём ремонт, запчасти и расходные материалы — далеко не самые крупные их статьи. К примеру, поломка конвейера на заводе может привести к полной остановке производства. Производственная линия, которая в обычные дни выпускает продукцию на миллионы рублей каждый час, простаивает, пока проблема не будет устранена. В результате компания упускает выгоду и рискует своей репутацией из-за срыва поставок.
Поэтому очень важно выявлять дефекты и проблемы на оборудовании задолго до того, как они станут причиной аварий и простоев. В этом современным предприятиям помогают системы предиктивной аналитики, интегрированные в АСУ «ТОиР оборудования».
Долгие годы машиностроительные предприятия использовали одну из двух стратегий технического обслуживания и ремонта (ТОиР) оборудования:
• «реактивную», то есть меняли детали уже после того, как они вышли из строя;
• или «превентивную», когда проводили плановые ремонты и регулярно обновляли технику.
В первом случае компании сталкивались с немалыми издержками на простоях оборудования.
Во втором случае предприятия тратили огромные средства на обслуживание оборудования, которое в этом не нуждалось.
Развитие Индустрии 4.0 и, в частности, концепции интернета умных вещей, позволило Техническому центру в 2017 году перейти к более современной стратегии (методике) ТОиР — предиктивному обслуживанию оборудования. Её основная идея заключается в том, чтобы за счёт использования передовых технологий предсказывать дефекты и поломки узлов оборудования до того, как они произойдут.
Для оптимизации расходов на ТОиР оборудования в 2014 году Технический центр ТОиР оборудования перешел на концепцию всеобщего производственного обслуживания оборудования (TPM).
Концепция TPM основана на предотвращении появления поломок путем отслеживания и изучения всех причин сбоев оборудования с привлечением персонала, который на нем работает и выполняет работы по межремонтному и техническому обслуживанию.
В основе концепции TPM заложены восемь принципов:
По концепции TPM считается, что идеально работающее оборудование — то, которое чинится еще до того, как оно сломалось. Однако поломки могут случаться по разным причинам, в том числе непредвиденным обстоятельствам или воздействиям. В некоторых отраслях промышленности требуется предусмотреть даже случайные сбои, в связи с чем появилась следующая концепция.
Концепция RCM зародилась в конце 1970-х годов в области авиации при создании самолетов нового поколения. С 1980-х годов данная концепция стала применяться в других отраслях промышленности и особенно в службах ТОиР оборудования. Главной идеей концепции обеспечения надежности (RCM) является планирование технического обслуживания и ремонтов оборудования на основе инженерного анализа возможных отказов оборудования и вариантов уменьшения последствий этих отказов.
Концепция обеспечение надежности работы оборудования (RCM) обеспечивает:
Концепция 4 ключевых процедур традиционна для российских предприятий. Данная концепция основывается на принципах планово-предупредительного обслуживания оборудования, которые предусматривают плановый вывод оборудования из эксплуатации в соответствии с ремонтным циклом.
Ремонтный цикл предполагает определенное чередование следующих видов процедур:
И, наконец, мы добрались до четвертой концепции учета ремонтов оборудования – концепции развивающихся систем. Практика применения вышеперечисленных концепций: TPM, RCM и концепции четырех процедур - показывает, что универсальных решений для построения систем ТОиР нет, так как каждая отрасль промышленности имеет свои особенности производственного процесса. Как правило, в условиях реального предприятия учет ТОиР строится не на одной концепции, а на основании всех трех.
В то же время концепция развивающихся систем ТОиР предполагает построение опорной модели, состоящей из компонентов: «как есть», «как можно» и «как нужно». Компонент «как есть» регулярно корректируется, исходя из возможностей компонента «как можно», целевых требований компонента «как нужно».
Для создания индивидуального решения по организации ТОиР оборудования необходимо:
- описать ключевые компоненты системы ТОиР предприятия «как есть»;
- проанализировать потенциальные возможности компонента «как можно»;
- сформировать политику компонента «как нужно» в плановом периоде:
Важно понимать, что самая даже продуманная и грамотно внедренная система учета ТОиР не будет эффективна при использовании на предприятии устаревшего и изношенного оборудования, которое само по себе служит источником низкой производительности предприятия и высокой себестоимости производимой продукции. Система ТОиР как раз будет указывать на необходимость произвести замену устаревшего оборудования, так как задача этой системы – обеспечивать ресурс для качественного производства.
Для этого на формообразующие узлы оборудования мы устанавливали датчики, которые непрерывно отслеживали различные параметры работы узлов и их технического состояния.
Информация, собранная с датчиков, отправляется в АСУ «Мониторинг», где система, используя алгоритмы машинного обучения, сравнивает полученную информацию о фактическом техническом состоянии узла с нормальными (базовыми) показателями, записанными при запуске оборудования в эксплуатацию и прогнозирует, что в ближайшее время те или иные детали могут выйти из строя.
К примеру, система предиктивной аналитики может определить, что при текущем уровне шума, нагрузке и вибрации, росте температуры, росте тренда развития дефекта, электродвигатель привода главного движения может выйти из строя через 40 дней. Благодаря такому подходу инженеры по ремонту могут заблаговременно просчитывать риски и предпринимать меры по приобретению запчастей и спланировать сроки начала ТОиР оборудования. Причём именно там, где это действительно требуется.
Как известно, задача управления техобслуживанием и ремонтом оборудования возникает на разных уровнях управления промышленным предприятием. В последнее время для распределения работ, связанных с проведением технического обслуживания и ремонта (ТОиР), используются исполнительные производственные системы MES (Manufacturing Execution Systems).
В контуре управления предприятием также бывают задействованы системы класса APS (Advanced Planning Systems).
Это программное обеспечение включает в состав своей функциональности задачу «Управление техобслуживанием и ремонтом». Эта же задача сформулирована в блоке 10 модели стандарта ГОСТ Р МЭК 62264–1-2014 и рассматривается также на уровне ERP-систем. Правила проведения технического обслуживания и ремонта оборудования (ТОиР) регламентируются также международными стандартами серии ISO 55000:2014 и национальными стандартами ГОСТ 18322–2016 и ГОСТ 57329–2016 «Система технического обслуживания и ремонта техники».
В состав АСУ «ТОиР оборудования с ЧПУ» входит современное программное обеспечение для формирования графиков ТОиР.
Для формирования графиков проведения ТОиР мы использовали специализированное программное обеспечение, предназначенное для информационной поддержки процедур технического обслуживания и ремонта.
При выборе программных решений в области ТОиР оборудования с ЧПУ мы рассмотрели три класса программных решений, различающихся по функциональным возможностям и полноте предоставляемого сервиса:
Работы по техническому обслуживанию и ремонту (ТОиР) включают в себя:
Уже в 30 е годы прошлого столетия возникло понимание того, что работы ТОиР по принципу RFT, т. е. «сломается — починим», может привести предприятие к значительным убыткам как в результате возникновения брака, так и нарушения обязательств перед заказчиками. В эти годы стала интенсивно развиваться концепция планово предупредительного ремонта как на Западе, так и в СССР.
Окончательно же новые методы планирования предупредительных ремонтов сформировались в послевоенные годы. Но от обслуживания станков «по событию» отказаться не удалось и по сей день. Безусловно, от возникновения непредвиденных отказов технологического оборудования уйти все еще не удается, однако в настоящее время уже существуют программные решения (исполнительные производственные системы — MES, Manufacturing Execution Systems), позволяющие оперативно реагировать на такие события — переназначать некоторые операции на исправные взаимозаменяемые станки, корректируя при этом общее производственное расписание.
Используя эффективные эвристические оптимизационные алгоритмы, АСУ ТОиР оборудования с ЧПУ» формирует сменно-суточные задания на выполнение работ по ТОиР оборудования, с учетом текущего состояния оборудования и производства. Одновременно составляется график материально технического оснащения оборудования, график проведения работ, связанных с планово предупредительным ремонтом оборудования, который показан на нижерасположенном рисунке.
В своих статьях я делюсь с Вами своим опытом и накопленными сокровенными знаниями в области организации ТОиР оборудования с ЧПУ на крупном машиностроительном предприятии.
В начале своей деятельности Технический центр ТОиР оборудования с ЧПУ столкнулся с рядом нижеследующих проблем:
- низкий уровень фактически проводимых ППР,
- недостоверная отчётность о проводимых работах,
- недостоверные данные о техническом состоянии оборудования.
Причины:
- отсутствие возможности проверить, что конкретно сделал сотрудник в месте проведения работ;
- отчёты о ППР,о состоянии оборудования и его параметрах со слов сотрудников на бумажных носителях.
В последнее время на передовых предприятиях машиностроения стала активно внедряться концепция «Умное ТОиР оборудования с ЧПУ», я эту концепцию в своих статьях называл «Интеллектуальное ТОиР оборудования с ЧПУ».
Поговорим немного о Концепциях ТОиР оборудования и современных тенденциях в управлении ТОиР оборудования.
В настоящее время существуют четыре концепции для построения системы ТОиР оборудования:
- Концепция всеобщего производственного обслуживания оборудования (Total productivity maintenance — TPM);
- Концепция обеспечения надежности оборудования (Reliability centered maintenance — RCM);
- Концепция, направленная на нормирование и регламентацию последовательного применения нижеперечисленных четырех ключевых процедур:
3.2. планово-предупредительные ремонты оборудования;
3.3 капитальные ремонты с глубокой модернизацией;
3.4. замена изношенного оборудования на новое;
4. Концепция развивающихся систем ТОиР.
Дальше я поясню, что представляет из себя каждая концепция ТОиР оборудования в отдельности. В этой статье я опишу и оценю вышеупомянутые концепции ТОиР оборудования и покажу, насколько значим был этот подход для Технического центра и будет важен для служб ТОиР оборудования с ЧПУ предприятий ВПК.
Рано или поздно любое оборудование выходит из строя из-за:
- брака, полученного при сборке оборудования на заводе-изготовителе,
- износа поверхностей деталей и узлов оборудования,
- неподходящих условий эксплуатации.
И каждый такой отказ влечёт за собой колоссальные расходы, причём ремонт, запчасти и расходные материалы — далеко не самые крупные их статьи. К примеру, поломка конвейера на заводе может привести к полной остановке производства. Производственная линия, которая в обычные дни выпускает продукцию на миллионы рублей каждый час, простаивает, пока проблема не будет устранена. В результате компания упускает выгоду и рискует своей репутацией из-за срыва поставок.
Поэтому очень важно выявлять дефекты и проблемы на оборудовании задолго до того, как они станут причиной аварий и простоев. В этом современным предприятиям помогают системы предиктивной аналитики, интегрированные в АСУ «ТОиР оборудования».
Прогнозный подход к ТОиР и как он работает
Долгие годы машиностроительные предприятия использовали одну из двух стратегий технического обслуживания и ремонта (ТОиР) оборудования:
• «реактивную», то есть меняли детали уже после того, как они вышли из строя;
• или «превентивную», когда проводили плановые ремонты и регулярно обновляли технику.
В первом случае компании сталкивались с немалыми издержками на простоях оборудования.
Во втором случае предприятия тратили огромные средства на обслуживание оборудования, которое в этом не нуждалось.
Развитие Индустрии 4.0 и, в частности, концепции интернета умных вещей, позволило Техническому центру в 2017 году перейти к более современной стратегии (методике) ТОиР — предиктивному обслуживанию оборудования. Её основная идея заключается в том, чтобы за счёт использования передовых технологий предсказывать дефекты и поломки узлов оборудования до того, как они произойдут.
Для оптимизации расходов на ТОиР оборудования в 2014 году Технический центр ТОиР оборудования перешел на концепцию всеобщего производственного обслуживания оборудования (TPM).
Концепция TPM основана на предотвращении появления поломок путем отслеживания и изучения всех причин сбоев оборудования с привлечением персонала, который на нем работает и выполняет работы по межремонтному и техническому обслуживанию.
В основе концепции TPM заложены восемь принципов:
- Автономное обслуживание. Оператор оборудования должен самостоятельно проводить осмотр, работы по чистке, а также незначительные работы по техническому обслуживанию.
- Целенаправленное улучшение. Нацелено на предотвращение семи видов потерь.
- Плановое техническое обслуживание. Обеспечение полной готовности оборудования, а также проведение мероприятий в области технического обслуживания.
- Управление качеством. Реализация цели «нулевых дефектов в качестве» в изделиях и оборудовании.
- Раннее управление оборудованием. Реализация запуска новых процессов.
- Образование и обучение персонала. Сотрудники должны быть обучены в соответствии с требованиями по улучшению квалификации для эксплуатации и технического ухода за оборудованием.
- Административный и офисный TPM. Потери устраняются в непрямых производственных подразделениях.
- Безопасность труда, окружающая среда и здравоохранение. Преобразование аварий на предприятии в «ноль дефектов».
По концепции TPM считается, что идеально работающее оборудование — то, которое чинится еще до того, как оно сломалось. Однако поломки могут случаться по разным причинам, в том числе непредвиденным обстоятельствам или воздействиям. В некоторых отраслях промышленности требуется предусмотреть даже случайные сбои, в связи с чем появилась следующая концепция.
Концепция обеспечения надежности оборудования (RCM)
Концепция RCM зародилась в конце 1970-х годов в области авиации при создании самолетов нового поколения. С 1980-х годов данная концепция стала применяться в других отраслях промышленности и особенно в службах ТОиР оборудования. Главной идеей концепции обеспечения надежности (RCM) является планирование технического обслуживания и ремонтов оборудования на основе инженерного анализа возможных отказов оборудования и вариантов уменьшения последствий этих отказов.
Концепция обеспечение надежности работы оборудования (RCM) обеспечивает:
- построение локализованных моделей отказов для ключевых компонентов оборудования;
- применение различных типов обслуживания к различным частям оборудования;
- минимизацию влияния отказа на производственный процесс в условиях, когда невозможно предсказать или предотвратить отказ;
- детальную проработку и планирование восстановления оборудования после отказа.
Концепция четырех ключевых процедур
Концепция 4 ключевых процедур традиционна для российских предприятий. Данная концепция основывается на принципах планово-предупредительного обслуживания оборудования, которые предусматривают плановый вывод оборудования из эксплуатации в соответствии с ремонтным циклом.
Ремонтный цикл предполагает определенное чередование следующих видов процедур:
- Межремонтное техническое обслуживание и периодические операции — периодическое проведение работ по уходу, регулировке, смазке, очистке, оперативной замене сменного оборудования и т. п.
- Текущие (плановые) ремонты — работы по устранению дефектов в работе оборудования, замене, восстановлению отдельных узлов, деталей и т. п.
- Плановые капитальные ремонты — работы по полному восстановлению оборудования с заменой или восстановлением его частей. Объем и сроки капитального ремонта формируются на основе информации о техническом состоянии оборудования по результатам проведенных текущих ремонтов.
- Замена изношенного оборудования — предусматривает закупку и установку нового оборудования, когда затраты на ремонт сопоставимы с затратами на закупку и установку нового оборудования или превышают их.
Концепция развивающихся систем ТОиР
И, наконец, мы добрались до четвертой концепции учета ремонтов оборудования – концепции развивающихся систем. Практика применения вышеперечисленных концепций: TPM, RCM и концепции четырех процедур - показывает, что универсальных решений для построения систем ТОиР нет, так как каждая отрасль промышленности имеет свои особенности производственного процесса. Как правило, в условиях реального предприятия учет ТОиР строится не на одной концепции, а на основании всех трех.
В то же время концепция развивающихся систем ТОиР предполагает построение опорной модели, состоящей из компонентов: «как есть», «как можно» и «как нужно». Компонент «как есть» регулярно корректируется, исходя из возможностей компонента «как можно», целевых требований компонента «как нужно».
Для создания индивидуального решения по организации ТОиР оборудования необходимо:
- описать ключевые компоненты системы ТОиР предприятия «как есть»;
- проанализировать потенциальные возможности компонента «как можно»;
- сформировать политику компонента «как нужно» в плановом периоде:
- описать целевые требования компонента «как нужно»;
- описать изменения учета ТОиР, необходимых для перевода в состояние «как нужно».
Важно понимать, что самая даже продуманная и грамотно внедренная система учета ТОиР не будет эффективна при использовании на предприятии устаревшего и изношенного оборудования, которое само по себе служит источником низкой производительности предприятия и высокой себестоимости производимой продукции. Система ТОиР как раз будет указывать на необходимость произвести замену устаревшего оборудования, так как задача этой системы – обеспечивать ресурс для качественного производства.
Для этого на формообразующие узлы оборудования мы устанавливали датчики, которые непрерывно отслеживали различные параметры работы узлов и их технического состояния.
Информация, собранная с датчиков, отправляется в АСУ «Мониторинг», где система, используя алгоритмы машинного обучения, сравнивает полученную информацию о фактическом техническом состоянии узла с нормальными (базовыми) показателями, записанными при запуске оборудования в эксплуатацию и прогнозирует, что в ближайшее время те или иные детали могут выйти из строя.
К примеру, система предиктивной аналитики может определить, что при текущем уровне шума, нагрузке и вибрации, росте температуры, росте тренда развития дефекта, электродвигатель привода главного движения может выйти из строя через 40 дней. Благодаря такому подходу инженеры по ремонту могут заблаговременно просчитывать риски и предпринимать меры по приобретению запчастей и спланировать сроки начала ТОиР оборудования. Причём именно там, где это действительно требуется.
Как известно, задача управления техобслуживанием и ремонтом оборудования возникает на разных уровнях управления промышленным предприятием. В последнее время для распределения работ, связанных с проведением технического обслуживания и ремонта (ТОиР), используются исполнительные производственные системы MES (Manufacturing Execution Systems).
В контуре управления предприятием также бывают задействованы системы класса APS (Advanced Planning Systems).
Это программное обеспечение включает в состав своей функциональности задачу «Управление техобслуживанием и ремонтом». Эта же задача сформулирована в блоке 10 модели стандарта ГОСТ Р МЭК 62264–1-2014 и рассматривается также на уровне ERP-систем. Правила проведения технического обслуживания и ремонта оборудования (ТОиР) регламентируются также международными стандартами серии ISO 55000:2014 и национальными стандартами ГОСТ 18322–2016 и ГОСТ 57329–2016 «Система технического обслуживания и ремонта техники».
В состав АСУ «ТОиР оборудования с ЧПУ» входит современное программное обеспечение для формирования графиков ТОиР.
Для формирования графиков проведения ТОиР мы использовали специализированное программное обеспечение, предназначенное для информационной поддержки процедур технического обслуживания и ремонта.
При выборе программных решений в области ТОиР оборудования с ЧПУ мы рассмотрели три класса программных решений, различающихся по функциональным возможностям и полноте предоставляемого сервиса:
- Системы CММS (Computerized Maintenance Management Systems) — простые компьютерные системы управления ремонтами. Такие системы чаще всего привязаны к определенной отрасли и предназначены для небольших предприятий. Как правило, они не обладают глубокой функциональностью в области управления ТОиР.
- Информационные системы управления основными фондами EAM (Enterprise Asset Management) — специально разработанный класс систем, позволяющий эффективно управлять в том числе техническим обслуживанием и ремонтом оборудования. Системы имеют глубокую функциональность в области ТОиР, но не всегда обладают требуемой полнотой в области горизонтальной интеграции с другими системами, касающимися иных сфер деятельности предприятия.
- Модули ТОиР в ERP-системах (Enterprise Resource Planning). В таких системах функционал по моделированию сложного технологического оборудования, его ремонтам, техническому и сервисному обслуживанию представлен в меньшем по сравнению с ЕАМ-системами объеме, но, что очень важно для средних и крупных промышленных предприятий, этот функционал интегрирован со всеми модулями ERP-системы.
Классификация ТОиР, проблемы, условия применения
Работы по техническому обслуживанию и ремонту (ТОиР) включают в себя:
- Техническое обслуживание «по событию» (Run-to-Failure — RTF) — комплекс процедур по поддержанию работоспособности и исправности оборудования при его эксплуатации при возникновении непредвиденных ремонтов.
Уже в 30 е годы прошлого столетия возникло понимание того, что работы ТОиР по принципу RFT, т. е. «сломается — починим», может привести предприятие к значительным убыткам как в результате возникновения брака, так и нарушения обязательств перед заказчиками. В эти годы стала интенсивно развиваться концепция планово предупредительного ремонта как на Западе, так и в СССР.
Окончательно же новые методы планирования предупредительных ремонтов сформировались в послевоенные годы. Но от обслуживания станков «по событию» отказаться не удалось и по сей день. Безусловно, от возникновения непредвиденных отказов технологического оборудования уйти все еще не удается, однако в настоящее время уже существуют программные решения (исполнительные производственные системы — MES, Manufacturing Execution Systems), позволяющие оперативно реагировать на такие события — переназначать некоторые операции на исправные взаимозаменяемые станки, корректируя при этом общее производственное расписание.
Используя эффективные эвристические оптимизационные алгоритмы, АСУ ТОиР оборудования с ЧПУ» формирует сменно-суточные задания на выполнение работ по ТОиР оборудования, с учетом текущего состояния оборудования и производства. Одновременно составляется график материально технического оснащения оборудования, график проведения работ, связанных с планово предупредительным ремонтом оборудования, который показан на нижерасположенном рисунке.
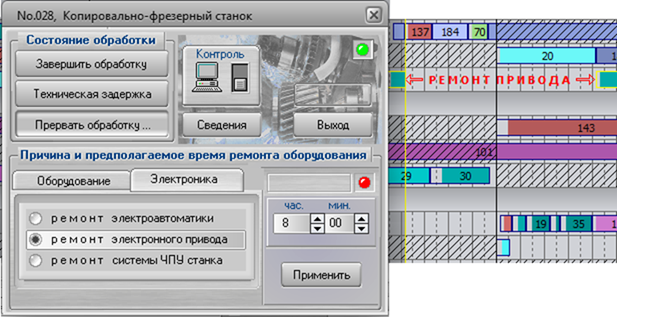
2. Плановые ремонты по графику (Time-Based Maintenance — TBM) — регламентное техническое обслуживание и ремонты, выполняемые по графику для обеспечения или восстановления работоспособности оборудования. Планово предупредительные ремонты (ППР) выполняются в соответствии с установленным ремонтным циклом; обычно указывается месяц, в течение которого должен быть выполнен такой ремонт. Суть этого подхода состоит в том, чтобы провести ремонт до наступления отказа.
Эксплуатируемое технологическое оборудование имеет паспорт производителя, в котором указано, в каком режиме и какое техническое обслуживание необходимо провести для того, чтобы данное оборудование продолжало находиться в работоспособном состоянии. Этот вид обслуживания самый дорогой, хотя и дает самый высокий процент готовности оборудования.
Однако график ППР, формируемый на межцеховом уровне, не учитывает реальную загрузку останавливаемого на профилактику оборудования в текущий момент времени. Последнее обстоятельство нередко сказывается на фактической скорости исполнения производственных заказов, поскольку нередко работы ППР назначаются именно на тот на период, когда соответствующим станкам следовало бы интенсивно работать.
Проблема решается на уровне MES в подсистеме оптимизации работ ППР на цеховом уровне. Рассматриваются две категории планово профилактических ремонтов:
Каждому виду ППР назначается нормативное время его выполнения, индивидуальный приоритет и указываются сроки, начиная с которых работы должны быть запланированы (включены в текущее производственное расписание) для их исполнения, — формируется оперативный график ППР, форма которого показана на нижерасположенном рисунке.
Эксплуатируемое технологическое оборудование имеет паспорт производителя, в котором указано, в каком режиме и какое техническое обслуживание необходимо провести для того, чтобы данное оборудование продолжало находиться в работоспособном состоянии. Этот вид обслуживания самый дорогой, хотя и дает самый высокий процент готовности оборудования.
Однако график ППР, формируемый на межцеховом уровне, не учитывает реальную загрузку останавливаемого на профилактику оборудования в текущий момент времени. Последнее обстоятельство нередко сказывается на фактической скорости исполнения производственных заказов, поскольку нередко работы ППР назначаются именно на тот на период, когда соответствующим станкам следовало бы интенсивно работать.
Проблема решается на уровне MES в подсистеме оптимизации работ ППР на цеховом уровне. Рассматриваются две категории планово профилактических ремонтов:
- работы, выполняемые параллельно (когда бригада ремонтников может проводить ППР сразу для нескольких станков одновременно);
- работы, выполняемые последовательно (когда один ремонтник может остановить только один станок на ППР).
Каждому виду ППР назначается нормативное время его выполнения, индивидуальный приоритет и указываются сроки, начиная с которых работы должны быть запланированы (включены в текущее производственное расписание) для их исполнения, — формируется оперативный график ППР, форма которого показана на нижерасположенном рисунке.

Оптимизация работ по ТОиР оборудования производится таким образом, чтобы работы ППР размещались в той части исходного графика загрузки оборудования, где последнее было наименее загружено. Полученный при этом оперативный график проведения ППР минимизирует негативное влияние остановки ремонтируемого оборудования на общую скорость исполнения производственных заказов.
3. Ремонты по техническому состоянию оборудования (Condition-Based Maintenance — CBM) выполняются с учетом состояния отдельных систем и частей оборудования. Дата таких ремонтов прогнозируется, но точно ее можно определить лишь по показанием специальных датчиков, контролирующих текущее состояние оборудования (MDC- систем). На основании показания датчиков делается прогноз о времени вывода данного оборудования в ремонт. Положительные стороны этого типа обслуживания в том, что себестоимость меньше, а готовность оборудования к выполнению производственных программ достаточно высока.
Однако опыт эксплуатации АСУ «ТОиР оборудования» и АСУ «Мониторинг» Техническим центром, привел к неожиданным результатам. Оказалось, что только 23-34% отказов соответствуют представлению о том, что их интенсивность растет с наработкой оборудования. Эти отказы свойственны относительно простому оборудованию. Напротив, для технически сложного оборудования ( многоцелевые станки с ЧПУ) было замечено, что между вероятностью их отказа и сроком эксплуатации нет или почти нет взаимосвязи т. е. величина наработки или метод учета остаточного ресурса (метод CBM) не позволяет достоверно прогнозировать приближение отказа.
Подсистема имитационного моделирования материальных потоков в MES в диспетчерском режиме автоматически отслеживает исполнение текущего производственного расписания и, следовательно, фиксирует фактически отработанное время по каждой единице оборудования. Система визуализирует, в частности, текущее значение остаточного ресурса, что дает возможность инженеру по ремонту Технического центра принимать оперативные решения относительно проведения работ по ТОиР, исходя из текущего состояния оборудования. Схема планирования ППР исходя их фактического технического состояния оборудования приведена на нижерасположенном рисунке.
3. Ремонты по техническому состоянию оборудования (Condition-Based Maintenance — CBM) выполняются с учетом состояния отдельных систем и частей оборудования. Дата таких ремонтов прогнозируется, но точно ее можно определить лишь по показанием специальных датчиков, контролирующих текущее состояние оборудования (MDC- систем). На основании показания датчиков делается прогноз о времени вывода данного оборудования в ремонт. Положительные стороны этого типа обслуживания в том, что себестоимость меньше, а готовность оборудования к выполнению производственных программ достаточно высока.
Однако опыт эксплуатации АСУ «ТОиР оборудования» и АСУ «Мониторинг» Техническим центром, привел к неожиданным результатам. Оказалось, что только 23-34% отказов соответствуют представлению о том, что их интенсивность растет с наработкой оборудования. Эти отказы свойственны относительно простому оборудованию. Напротив, для технически сложного оборудования ( многоцелевые станки с ЧПУ) было замечено, что между вероятностью их отказа и сроком эксплуатации нет или почти нет взаимосвязи т. е. величина наработки или метод учета остаточного ресурса (метод CBM) не позволяет достоверно прогнозировать приближение отказа.
Подсистема имитационного моделирования материальных потоков в MES в диспетчерском режиме автоматически отслеживает исполнение текущего производственного расписания и, следовательно, фиксирует фактически отработанное время по каждой единице оборудования. Система визуализирует, в частности, текущее значение остаточного ресурса, что дает возможность инженеру по ремонту Технического центра принимать оперативные решения относительно проведения работ по ТОиР, исходя из текущего состояния оборудования. Схема планирования ППР исходя их фактического технического состояния оборудования приведена на нижерасположенном рисунке.
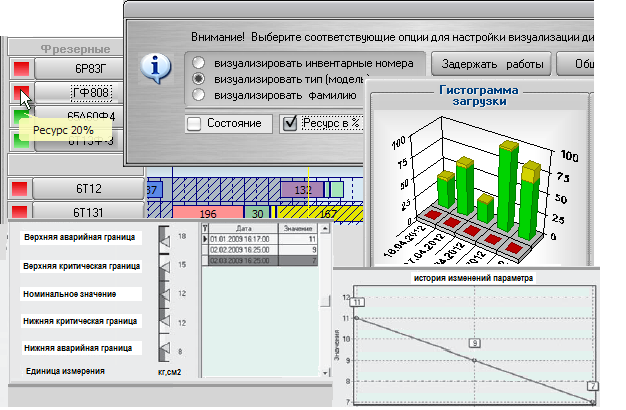
4. ТОиР, ориентированное на надежность (Reliability-Centered Maintenance — RCM) — метод, при котором в первую очередь обслуживается наиболее важное (критичное) оборудование, отказ которого может привести к серьезным последствиям по отношению ко всему производственному процессу с учетом реализуемых технологий, состояния отдельных систем и узлов оборудования. Таким образом, акцент в проведении ТОиР смещается от прогноза возможного возникновения отказа по методу CBM на его негативные последствия на весь ход технологического процесса. технологически сопрягаемых поверхностей.
Реализация метода RCM начинается с анализа пропускной способности станочной системы относительно внутрицехового материального потока, связанного с выполняемым плановым заданием.
Эффективно эту задачу можно решить лишь при наличии:
В состав АСУ «ТОиР оборудования» входит подсистема «многокритериальная оптимизация», которая осуществляет следующие виды анализа :
• Определение функций каждой единицы и групп оборудования в технологическом процессе вместе с требованием к качеству выполнения этих функций.
• Определение перечня функциональных отказов как неспособности выполнять функции в соответствии с установленными требованиями.
• Определение перечня критического оборудования (цепочку станков, лежащих на «критическом пути», включая ресурс, ограничивающий производительность системы, станки, задействованные в обработке деталей и сборочных единиц).
Вычисление индекса «критичности» оборудования
К оборудованию, не являющемуся критичным, ТОиР осуществляется по «событию» методом RFT, т. е. ремонт проводится по факту возникновения отказа.
По отношению к оборудованию с высоким индексом критичности применяется предупредительные практики ППР: как TBM, так и CBM.
Отметим, что во всех четырех методиках ТОиР правила назначения ремонтно-профилактических работ — время их начала и последовательность проведения — на современных машиностроительных предприятиях сегодня строго рассчитываются при их совместной многокритериальной оптимизации производственного графика и графика выполнения ППР.
И в заключении четвертой части статьи «АСУ «ТОиР оборудования с ЧПУ», хочется сказать, что современные АСУ «ТОиР оборудования» рассчитывают оптимальное время начала и окончания проведения работ по ТОиР по каждой единице оборудования. При этом правила назначения работ по ТОиР оборудования должны формироваться с учетом фактической загруженности станочной системы, технического состояния оборудования, обеспечения материально-техническими ресурсами.
Распределение работ, связанных с методами ППР (TBM и CBM), должно осуществляться таким образом, чтобы их проведение, связанное с остановкой оборудования было менее затратно для производства , — это серьезная организационная проблема. Реальный способ ее решения — применение АСУ«ТОиР оборудования».
На этом я заканчиваю четвертую часть статьи из цикла на тему «АСУ «ТОиР оборудования с ЧПУ». Ожидайте продолжение.
Реализация метода RCM начинается с анализа пропускной способности станочной системы относительно внутрицехового материального потока, связанного с выполняемым плановым заданием.
Эффективно эту задачу можно решить лишь при наличии:
- текущего производственного графика работ, составленного средствами MES-системы.
- текущего плана ТОиР оборудования.
- оценок фактического технического состояния оборудования.
В состав АСУ «ТОиР оборудования» входит подсистема «многокритериальная оптимизация», которая осуществляет следующие виды анализа :
• Определение функций каждой единицы и групп оборудования в технологическом процессе вместе с требованием к качеству выполнения этих функций.
• Определение перечня функциональных отказов как неспособности выполнять функции в соответствии с установленными требованиями.
• Определение перечня критического оборудования (цепочку станков, лежащих на «критическом пути», включая ресурс, ограничивающий производительность системы, станки, задействованные в обработке деталей и сборочных единиц).
Вычисление индекса «критичности» оборудования
К оборудованию, не являющемуся критичным, ТОиР осуществляется по «событию» методом RFT, т. е. ремонт проводится по факту возникновения отказа.
По отношению к оборудованию с высоким индексом критичности применяется предупредительные практики ППР: как TBM, так и CBM.
Отметим, что во всех четырех методиках ТОиР правила назначения ремонтно-профилактических работ — время их начала и последовательность проведения — на современных машиностроительных предприятиях сегодня строго рассчитываются при их совместной многокритериальной оптимизации производственного графика и графика выполнения ППР.
И в заключении четвертой части статьи «АСУ «ТОиР оборудования с ЧПУ», хочется сказать, что современные АСУ «ТОиР оборудования» рассчитывают оптимальное время начала и окончания проведения работ по ТОиР по каждой единице оборудования. При этом правила назначения работ по ТОиР оборудования должны формироваться с учетом фактической загруженности станочной системы, технического состояния оборудования, обеспечения материально-техническими ресурсами.
Распределение работ, связанных с методами ППР (TBM и CBM), должно осуществляться таким образом, чтобы их проведение, связанное с остановкой оборудования было менее затратно для производства , — это серьезная организационная проблема. Реальный способ ее решения — применение АСУ«ТОиР оборудования».
На этом я заканчиваю четвертую часть статьи из цикла на тему «АСУ «ТОиР оборудования с ЧПУ». Ожидайте продолжение.