В сегодняшней статье я освещу практику цифровой трансформации систем мониторинга с глубокой диагностикой узлов станков с ЧПУ, которая позволила Техническому центру «ТОиР оборудования с ЧПУ»:
Повышение степени автоматизации и расширение функциональных возможностей станков с ЧПУ значительно усложнило их конструкцию и, как следствие, усложнило и продолжает усложнять их ТОиР, и особенно поиск причин отказов в работе станков с ЧПУ в процессе эксплуатации.
Если в станках с ручным управлением причин отказов, как правило, мало, и они часто известны или легко определяются оператором, то в станках с ЧПУ, включающих в себя взаимодействующие механические, гидравлические, пневматические, электрические и электронные механизмы, устройства, блоки, причин отказов может быть значительно больше, и их нахождение требует часто больших затрат времени и средств. Вследствие возникающих при этом простоев станка снижается производительность работы этого дорогостоящего оборудования. Указанные проблемы усложняются дополнительно в связи с более интенсивной эксплуатацией станков с ЧПУ, работающих в три смены при минимальном количестве обслуживающего персонала. Благодаря применению современных режущих инструментов обработка заготовок проводится на более высоких режимах резания, чем раньше, что увеличивает нагрузки на различные механизмы и устройства станка с ЧПУ.
Как показала практика, причины целого ряда отказов могут быть очень несущественными, легко и быстро устранимыми, но время их поиска часто на порядок больше, чем время для их устранения, даже для высококвалифицированного наладчика или оператора. Поэтому все более широкое применение получают системы технического диагностирования.
Под техническим диагностированием в соответствии с ГОСТ 20911—75 понимают определение технического состояния объекта диагностирования (станка, его отдельных узлов и механизмов, системы управления, ее отдельных блоков и элементов и др.) с определенной точностью. Его результатом является заключение о техническом состоянии данного объекта с указанием, при необходимости, места, вида и причины дефекта. Необходимо отметить, что система технического диагностирования только находит неисправности, но не устраняет их.
Применение систем технического диагностирования позволяет значительно сократить простои станка с ЧПУ благодаря оперативной выдаче информации о месте и характере дефекта, а также дает возможность прогнозировать состояние отдельных элементов станка с ЧПУ, режущих инструментов, оценивать погрешность обрабатываемых заготовок и своевременно выдавать информацию для проведения технического обслуживании и ремонта.
За время своей работы в службе ТОиР оборудования с ЧПУ предприятия на всех должностях я много времени уделял разработке и внедрению систем диагностики технического состояния узлов оборудования с ЧПУ. На моих глазах и с непосредственным моим участием прошла эволюция систем диагностики узлов станков с ЧПУ до интеллектуальных АСУ «Мониторинг с глубокой диагностикой формообразующих узлов многооперационных станков с ЧПУ». Хронология разработки и внедрения проектов диагностики узлов станков с ЧПУ выглядит следующим образом.
Исходя из собственного опыта при разработке или выборе системы технического диагностирования оборудования, советую в первую очередь охватывать те неисправности, которые приводят к наибольшим простоям и наибольшим затратам на устранение их последствий.
При поиске неисправностей различают тестовое диагностирование и функциональное диагностирование. В первом случае на станок с ЧПУ подаются тестовые воздействия (чаще всего на устройство ЧПУ). Во втором случае диагностирование осуществляется во время функционирования станка с ЧПУ и на него поступают только рабочие воздействия. При необходимости могут использоваться оба вида диагностирования.
Для получения диагностической информации мы проводим измерение следующих величин: вибраций, акустических колебаний, деформаций и усилий, производительности, длительности циклов обработки, температуры нагрева, износа режущего инструмента и др.
В последнее время много внимания стали уделять усовершенствованию АСУ «Мониторинг с глубокой диагностикой технического состояния узлов оборудования с ЧПУ» многооперационных станков с ЧПУ, за счет внедрения инновационных технологий ТОиР, превращая ее в интеллектуальную систему.
На нерасположенном рисунке показана блок-схема классификации интеллектуальных АСУ «Мониторинг с глубокой диагностикой технического состояния узлов станков с ЧПУ».
- оптимизировать работу сотрудников;
- снизить нагрузку на сотрудников;
- повысить эффективность работы сотрудников;
- повысить эффективность работы оборудования с ЧПУ.
Повышение степени автоматизации и расширение функциональных возможностей станков с ЧПУ значительно усложнило их конструкцию и, как следствие, усложнило и продолжает усложнять их ТОиР, и особенно поиск причин отказов в работе станков с ЧПУ в процессе эксплуатации.
Если в станках с ручным управлением причин отказов, как правило, мало, и они часто известны или легко определяются оператором, то в станках с ЧПУ, включающих в себя взаимодействующие механические, гидравлические, пневматические, электрические и электронные механизмы, устройства, блоки, причин отказов может быть значительно больше, и их нахождение требует часто больших затрат времени и средств. Вследствие возникающих при этом простоев станка снижается производительность работы этого дорогостоящего оборудования. Указанные проблемы усложняются дополнительно в связи с более интенсивной эксплуатацией станков с ЧПУ, работающих в три смены при минимальном количестве обслуживающего персонала. Благодаря применению современных режущих инструментов обработка заготовок проводится на более высоких режимах резания, чем раньше, что увеличивает нагрузки на различные механизмы и устройства станка с ЧПУ.
Как показала практика, причины целого ряда отказов могут быть очень несущественными, легко и быстро устранимыми, но время их поиска часто на порядок больше, чем время для их устранения, даже для высококвалифицированного наладчика или оператора. Поэтому все более широкое применение получают системы технического диагностирования.
Под техническим диагностированием в соответствии с ГОСТ 20911—75 понимают определение технического состояния объекта диагностирования (станка, его отдельных узлов и механизмов, системы управления, ее отдельных блоков и элементов и др.) с определенной точностью. Его результатом является заключение о техническом состоянии данного объекта с указанием, при необходимости, места, вида и причины дефекта. Необходимо отметить, что система технического диагностирования только находит неисправности, но не устраняет их.
Применение систем технического диагностирования позволяет значительно сократить простои станка с ЧПУ благодаря оперативной выдаче информации о месте и характере дефекта, а также дает возможность прогнозировать состояние отдельных элементов станка с ЧПУ, режущих инструментов, оценивать погрешность обрабатываемых заготовок и своевременно выдавать информацию для проведения технического обслуживании и ремонта.
За время своей работы в службе ТОиР оборудования с ЧПУ предприятия на всех должностях я много времени уделял разработке и внедрению систем диагностики технического состояния узлов оборудования с ЧПУ. На моих глазах и с непосредственным моим участием прошла эволюция систем диагностики узлов станков с ЧПУ до интеллектуальных АСУ «Мониторинг с глубокой диагностикой формообразующих узлов многооперационных станков с ЧПУ». Хронология разработки и внедрения проектов диагностики узлов станков с ЧПУ выглядит следующим образом.
- 1984 год: разработка и внедрение АСУ «Управление формой обрабатываемых деталей на многооперационных станках модели ИР 500 ПМФ4, ИР 800 ПМФ4, ИР 1250 ПМФ4 используя данные диагностики шпинделя».
- 1985 год: разработка и внедрение системы удаленной диагностики технического состояния шпинделей многооперационных станков с ЧПУ модели ИР 500ПМФ4 - 5 единиц и MS 3-200 - 3 единицы, входящих в гибкую автоматизированную линию по производству корпусных деталей. Диагностика шпинделей станков модели ИР 500 ПМФ4 осуществлялась методом вибродиагностики, а станков модели MS 3-200 методом определения силы, действующей в осевом направлении на передний тензор-подшипник шпинделя, с помощью диагностического прибора производства фирмы Marposs.
- 1986 год: совместная с Куйбышевским авиационным институтом разработка и внедрение АСУ «Диагностики металлических примесей в масле от износа трущихся деталей».
- 1988 год: разработка системы диагностики технического состояния привода главного движения многооперационного станка модели ИР 500 ПМФ4.
- 1998 год: разработка и внедрение АСУ «Мониторинг технического состояния узлов станка».
- 2002 год: разработка и внедрение АСУ «Мониторинг с глубокой диагностикой технического состояния узлов станков».
- 2004 год: внедрение инновационной системы контроля геометрической точности станков с ЧПУ модели QC 10, QC 20 ballbar (Renishaw).
- 2008 год: внедрение лазерной системы контроля геометрических параметров станков модели XL 80.
- 2010 год: совместно с ООО «Станкосервис» внедрили АИС «Диспетчер», интегрировав ее в АСУ «ТОиР» и в АСУ «Мониторинг».
- 2011 год: внедрение и эксплуатация гибридной АСУ прогнозирования остаточного ресурса работоспособности узлов станков с ЧПУ и комплексной диагностики неисправностей металлорежущих станков с ЧПУ, на базе АСУ «Мониторинг с глубокой диагностикой технического состояния узлов станков» и АИС «Диспетчер». В настоящее время АИС «Диспетчер» является одной из самых распространенных систем мониторинга и диспетчеризации. Эта система представляет из себя комплекс запатентованных аппаратных и программных средств для непрерывного мониторинга и контроля оборудования в реальном времени и обработки результатов. Внедрение АИС «Диспетчер» не требует больших капиталовложений, но при этом она дает возможность точно и качественно оценить загрузку и производительность как современного, так и устаревшего оборудования и подсказать о необходимости принятия своевременного и правильного решения по оптимизации и обновлению производства.Система посредством объединения полученных данных и расчета первостепенных показателей производительности (KPI) увеличивает эффективность работы оборудования, повышает производительность труда, дает возможность принимать верные управленческие решения и исследовать экономический эффект от их применения.
- 2014 год: разработка и внедрение интеллектуальной АСУ «Удаленный мониторинг с глубокой диагностикой технического состояния узлов станков с ЧПУ», используя АРМ диагноста, оснащенного УЧПУ типа Sinumeric-840 D sl и диагностическим комплектом производства фирмы ARTIS.
- 2015 год: внедрили систему против столкновения модели Montronix.
- 2016 год: внедрение лазерной системы измерения объемной геометрической точности многогабаритных многооперационных станков с ЧПУ модели Easy Laser 940.
- 2017 год: внедрение лазерной системы измерения объемной геометрической точности многогабаритных многооперационных станков с ЧПУ c последующей автоматической компенсацией погрешностей модели ETALON - LASER TRACER NG.
- 2024 год: внедрение лазерной системы контроля геометрических параметров станков с ЧПУ модели ХК 10.
Исходя из собственного опыта при разработке или выборе системы технического диагностирования оборудования, советую в первую очередь охватывать те неисправности, которые приводят к наибольшим простоям и наибольшим затратам на устранение их последствий.
При поиске неисправностей различают тестовое диагностирование и функциональное диагностирование. В первом случае на станок с ЧПУ подаются тестовые воздействия (чаще всего на устройство ЧПУ). Во втором случае диагностирование осуществляется во время функционирования станка с ЧПУ и на него поступают только рабочие воздействия. При необходимости могут использоваться оба вида диагностирования.
Для получения диагностической информации мы проводим измерение следующих величин: вибраций, акустических колебаний, деформаций и усилий, производительности, длительности циклов обработки, температуры нагрева, износа режущего инструмента и др.
В последнее время много внимания стали уделять усовершенствованию АСУ «Мониторинг с глубокой диагностикой технического состояния узлов оборудования с ЧПУ» многооперационных станков с ЧПУ, за счет внедрения инновационных технологий ТОиР, превращая ее в интеллектуальную систему.
На нерасположенном рисунке показана блок-схема классификации интеллектуальных АСУ «Мониторинг с глубокой диагностикой технического состояния узлов станков с ЧПУ».
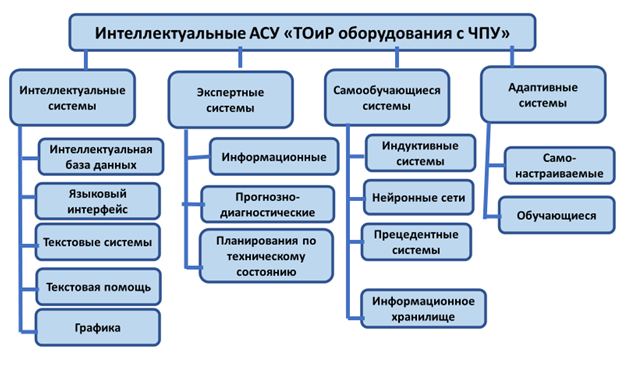
На нижерасположенном рисунке представлена блок-схема Интеллектуального мониторинга с глубокой диагностикой узлов станков с ЧПУ.
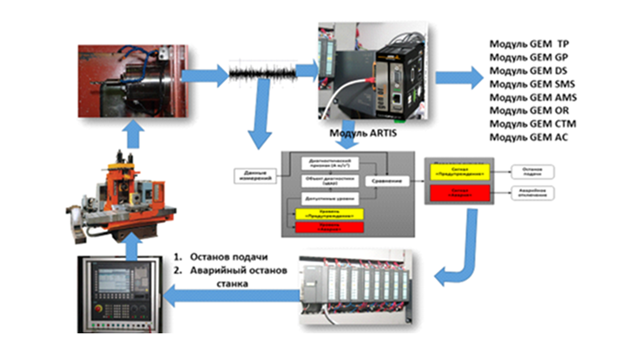
В техническом центре была разработана и внедрена в эксплуатацию интеллектуальная АСУ «Мониторинг с глубокой диагностикой технического состояния формообразующих узлов станков с ЧПУ», охватывающая пять направлений:
На нижерасположенном рисунке показана структурная схема информационных связей АСУ «ТОиР оборудования с ЧПУ», АСУ «Мониторинг с глубокой диагностикой узлов станков с ЧПУ» и АИС «Диспетчер», действующих в Техническом центре.
- контроль готовности станка и системы ЧПУ к работе;
- оперативное цикловое диагностирование;
- оперативное узловое диагностирование;
- специальное диагностирование;
- диагностирование по результатам обработки заготовок.
На нижерасположенном рисунке показана структурная схема информационных связей АСУ «ТОиР оборудования с ЧПУ», АСУ «Мониторинг с глубокой диагностикой узлов станков с ЧПУ» и АИС «Диспетчер», действующих в Техническом центре.
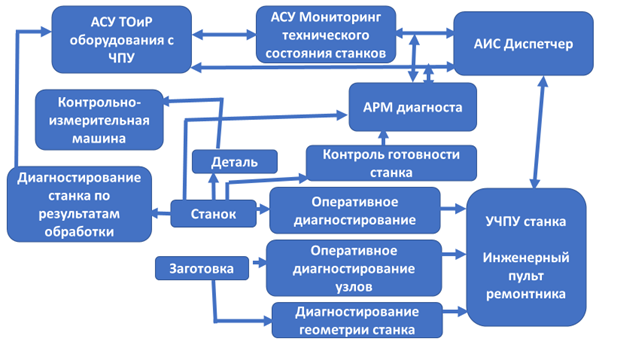
Для контроля готовности станка с ЧПУ к работе мы используем следующие средства контроля:
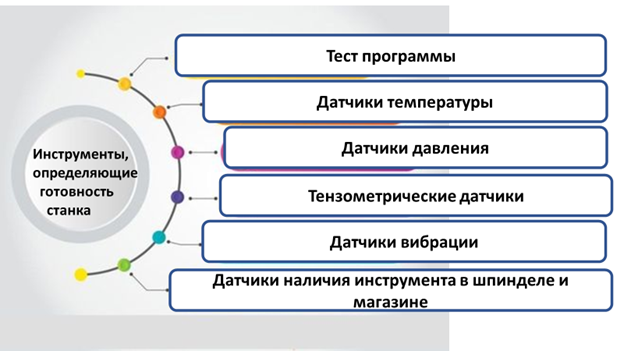
По разработанному алгоритму в автоматическом режиме проверяется:
При оперативном цикловом диагностировании используются:
По разработанному алгоритму в автоматическом режиме:
При оперативном узловом диагностирование мы проводим проверку работоспособности:
Результаты выводятся на экран дисплея УЧПУ и на АРМ диагноста.
При проведении специального диагностирования мы проводим проверку параметров геометрической и кинематической точности, наличия зазоров, упругих деформаций, износа направляющих и др.
Для этого применяется следующие инновационные приборы и системы, оснащенные функциями автоматической записи, обработкой, полученных данных и передачи их в АСУ «Мониторинг» и на АРМ диагноста.
- наличие и правильность зажима заготовки на станке;
- наличие режущего инструмента в шпинделе и магазине инструментов;
- требуемая величина давления в гидросистеме;
- наличие и объем СОЖ;
- наличие необходимого объема масла в баке и др.
При оперативном цикловом диагностировании используются:
- конечные выключатели;
- реле;
- датчики обратной связи;
- датчики вибрации;
- датчики давления;
- датчики температуры.
По разработанному алгоритму в автоматическом режиме:
- проверяется фактическая длительность суммарного времени цикла работы поворота руки смены инструмента, поворот стола, и др.;
- проводится анализ отличия времени — заданного и фактического — и дается прогноз на необходимость регулирования или ремонта механизма.
При оперативном узловом диагностирование мы проводим проверку работоспособности:
- приводов главного движения и подач;
- электроавтоматики станка, блоков УЧПУ и др.
Результаты выводятся на экран дисплея УЧПУ и на АРМ диагноста.
При проведении специального диагностирования мы проводим проверку параметров геометрической и кинематической точности, наличия зазоров, упругих деформаций, износа направляющих и др.
Для этого применяется следующие инновационные приборы и системы, оснащенные функциями автоматической записи, обработкой, полученных данных и передачи их в АСУ «Мониторинг» и на АРМ диагноста.
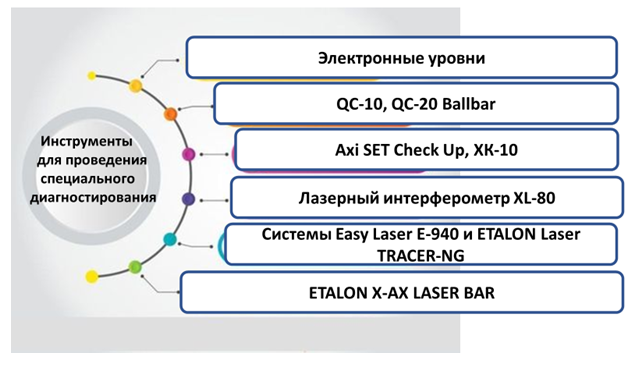
По результатам измерений проводится анализ состояния станка с ЧПУ, сравнение с нормативными требованиями. На основе этого оценивается и прогнозируется техническое состояние станка с ЧПУ, необходимость его ремонта.
Диагностирование может проводиться также по результатам измерения обрабатываемой заготовки, а также измерения готовой детали на контрольно-измерительной машине.
Диагностику состояния узлов станка по изготовленной детали мы проводим с помощью следующих методов:
На основании информации, полученной от датчиков, определяем частотный спектр, который отражает колебания инструмента и заготовки по нормали к обрабатываемой поверхности детали, вызванный наличием дефектов в формообразующих узлах станка. Затем текущий геометрический образ сравниваем с эталонным и по отклонению от него определяем наличие и место дефектов в узле станка.
На основании требований к металлорежущему станку составляем спектр, соответствующий допускаемым отклонениям формы и шероховатости поверхности детали при соблюдении конкретных условий технологического процесса обработки заготовки.
Расчетный спектр составляем с помощью моделирования колебаний инструмента и обрабатываемой детали с учётом технических условий на точность изготовления детали и технического состояния узлов станка и самого станка в целом.
По расчётному спектру выделяем характерные частоты, на которых проявляются погрешности изготовления узлов станка.
Для диагностики используют автоматизированные системы, в которых состояние каждого показателя измеряется с помощью специальных датчиков. На основе анализа показаний составляем заключение о техническом состоянии и работоспособности как узла, так и станка в целом.
Для примера, рассмотрим методы оценки технического состояния шпинделя многооперационного станка, основанные на анализе вибрационного сигнала:
Вибрационный сигнал анализируется узкополосным спектральным анализатором, и по частотному составу спектра мы идентифицируем возникновение и развитие дефектов подшипников шпинделя.
На нижерасположенном рисунке представлена форма вибрационного сигнала с амплитудными всплесками, полученного с помощью датчиков вибрации, установленных на корпусе шпинделя.
Диагностирование может проводиться также по результатам измерения обрабатываемой заготовки, а также измерения готовой детали на контрольно-измерительной машине.
Диагностику состояния узлов станка по изготовленной детали мы проводим с помощью следующих методов:
- Определение геометрического образа поверхности обработанной детали.
На основании информации, полученной от датчиков, определяем частотный спектр, который отражает колебания инструмента и заготовки по нормали к обрабатываемой поверхности детали, вызванный наличием дефектов в формообразующих узлах станка. Затем текущий геометрический образ сравниваем с эталонным и по отклонению от него определяем наличие и место дефектов в узле станка.
- Составление обобщённого (эталонного) спектра.
На основании требований к металлорежущему станку составляем спектр, соответствующий допускаемым отклонениям формы и шероховатости поверхности детали при соблюдении конкретных условий технологического процесса обработки заготовки.
- Определение расчётного спектра.
Расчетный спектр составляем с помощью моделирования колебаний инструмента и обрабатываемой детали с учётом технических условий на точность изготовления детали и технического состояния узлов станка и самого станка в целом.
- Выделение характерных частот.
По расчётному спектру выделяем характерные частоты, на которых проявляются погрешности изготовления узлов станка.
Для диагностики используют автоматизированные системы, в которых состояние каждого показателя измеряется с помощью специальных датчиков. На основе анализа показаний составляем заключение о техническом состоянии и работоспособности как узла, так и станка в целом.
Для примера, рассмотрим методы оценки технического состояния шпинделя многооперационного станка, основанные на анализе вибрационного сигнала:
Метод анализа вибрационного сигнала с точки зрения периодичности появления амплитудных всплесков
Вибрационный сигнал анализируется узкополосным спектральным анализатором, и по частотному составу спектра мы идентифицируем возникновение и развитие дефектов подшипников шпинделя.
На нижерасположенном рисунке представлена форма вибрационного сигнала с амплитудными всплесками, полученного с помощью датчиков вибрации, установленных на корпусе шпинделя.
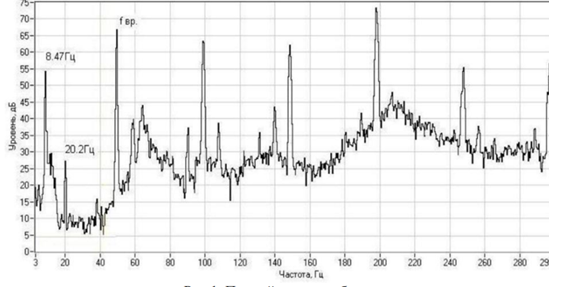
Как видно из рисунка, амплитудные всплески в вибросигнале следуют с определённой частотой. Причём дефекту на каждом из элементов подшипника (тела качения, дорожки или сепаратора) соответствуют свои частоты, которые однозначно просчитываются в зависимости от кинематики подшипника и скорости его вращения. Наличие той или иной дискретной составляющей в спектре сигнала говорит о возникновении соответствующего дефекта подшипника, а амплитуда этой составляющей говорит о глубине дефекта. Это несколько упрощённый подход, поскольку многие дефекты в спектре проявляются в виде не одной частотной составляющей, а нескольких.
Метод по спектру огибающей вибросигнала
Известно, что высокочастотная шумовая часть вибросигнала меняет свою амплитуду во времени, то есть она модулируется более низкочастотным сигналом. Именно в этом моделирующем сигнале и содержится информация о состоянии подшипника. Выделение и обработка полученной информации в виде вибросигнала и составляют основу этого метода. При этом для получения более достоверных результатов необходимо анализировать модуляцию не широкополосного сигнала, получаемого от датчика вибрации, а с предварительно отфильтрованного вибросигнала в диапазоне от 4 до 20 кГц.
Для этого отфильтрованный сигнал выделяется в модулирующий, который и подается на узкополосный спектр анализатора, и мы получаем спектр огибающей.
Система диагностики станков с ЧПУ по параметрам точности изготавливаемой детали содержит:
Бесконтактный датчик перемещения установлен на резцедержательной головке суппорта или корпусе шпинделя. После записи показаний на компьютере предусмотрена обработка экспериментальных данных с использованием методов математической статистики. Построенный геометрический образ поверхности в трехмерном пространстве позволяет определить все необходимые показатели точности детали до ее окончательной обработки. Способ направлен на прогнозирование параметров точности и качества изготавливаемых деталей.
Близким к вышеописанному способу являются способ диагностики шпиндельного узла. Этот способ предусматривает приложение внешней нагрузки к оправке, установленной в шпинделе, и измерение расстояния от поверхности оправки до датчиков перемещения, расположенных в двух поперечных сечениях оправки на заданном расстоянии между сечениями. Оправку обрабатываем резцом, в качестве датчиков перемещения используем бесконтактные датчики, по сигналам которых определяются поперечные сечения оправки в местах установки датчиков перемещения. По поперечным сечениям определяем геометрический образ оправки в трехмерном пространстве. После обработки оправки резцом, для полученной геометрической точности детали мы оцениваем погрешность радиального размера, геометрической формы, суммарную погрешность:
По результатам оценки геометрической точности полученной детали определяем параметрическую надежность шпиндельного узла.
Поставленная задача решается, а технический результат достигается тем, что в предлагаемом способе оперативной диагностики технического состояния формообразующих узлов металлообрабатывающих станков на основании информации, поступающей от датчиков, определяем геометрический образ поверхности обработанной детали, который представляем в виде частотного спектра, отражающего колебания инструмента и заготовки по нормали к обрабатываемой поверхности, вызванных наличием дефектов в узлах станка. Сравнивая текущий геометрический образ с эталонным, мы по отклонению его от эталонного определяем наличие и место дефектов.
Формирование эталонного геометрического образа осуществляется путем фиксации виброметрической информации в ходе обработки металлорежущими станками и применения накопленной информации для обучения нейросетевых моделей, представляющих собой апроксимацию нелинейных характеристик. В качестве архитектуры нейронной сети, реализующей эталонные модели, применяются рекуррентные нейронные сети с долгой краткосрочной памятью.
Поиск дефекта и причины отказа проводится в определенном диапазоне частот путем идентификации частоты возмущения с доминирующей частотой, вызывающей работу дефектного узла в данном частотном диапазоне. Вычисляется несоответствие между эталонной нейросетевой моделью и текущими характеристиками процесса, по величине и динамике изменения которого определяется характер дефекта посредством использования второй нейросетевой модели классификатора.
На основании требований к металлорежущему станку составляется обобщенный (эталонный) спектр, соответствующий допускаемым отклонениям формы (волнистости) и шероховатости поверхности детали при соблюдении конкретных условий обработки.
Расчетный спектр определяется с помощью моделирования колебаний инструмента и обрабатываемой детали с учетом технических условий на точность изготовления и сборки модулей металлообрабатывающего станка.
При использовании эталонного спектра в процессе диагностики технического состояния модулей станка по расчетному спектру выделяют характерные частоты, в которых проявляются погрешности изготовления модулей металлообрабатывающего станка.
При эксплуатации станка постоянно выполняется фиксация спектра в виде амплитудно-частотных характеристик. При возникновении новых видов дефектов, ранее неопределяемых, выполняется дообучение нейронной сети-классификатора по новым данным.
Как было показано, задачи технического диагностирования могут быть различными, поэтому различаются частота и моменты времени, когда получают данные различных измерений.
Диагностирование может проводиться непрерывно в процессе всего времени работы станка с ЧПУ и обработки заготовок, например контролируется температура в шкафу УЧПУ или температура масла в гидросистеме станка и др.
Ряд параметров, например система централизованного смазывания, контроль зажима каждой заготовки и точность изготовления каждого изделия и др., должны контролироваться периодически, но с большой частотой. Часть контрольных операций проводится с меньшей частотой, например один раз в смену или после каждой изготовленной партии деталей. Такие параметры станка, как точность, жесткость и др., должны контролироваться через длительные промежутки времени с очень малой частотой, поскольку эти параметры изменяются очень медленно и для их измерения требуются значительные затраты времени и средств. В отдельных случаях диагностирование может проводиться оператором в зависимости от конкретных требований и условий.
В настоящее время наиболее передовые фирмы — изготовители станков с ЧПУ предлагают новый вид сервиса, который получил название «телефонная диагностика». Ее принцип состоит в том, что диагностирование проводится на предприятии — изготовителе станка с ЧПУ. Естественно, что предприятие, эксплуатирующее станки с ЧПУ, может находиться в другом городе или даже в другой стране. Связь между этими предприятиями осуществляется по телефону. В случае возникновения у потребителя проблемы с диагностированием отказа станка он обращается к фирме-изготовителю и по телефону перекачивает информацию со своего компьютера в компьютер фирмы-изготовителя. Последняя имеет мощную диагностическую систему, которая не только обслуживает потребителей, но и в основном работает по совершенствованию выпускаемого оборудования, а также по доводке опытных образцов новых станков с ЧПУ. Фирма-изготовитель также имеет в своем распоряжении обширный пакет диагностических программ, базу данных и пакет расчетных моделей. Переданная по телефону информация в виде протокола измерений поступает в базу данных и служит исходной информацией для реализации расчетных моделей. Выполнение расчетов и анализ информации, имеющейся в базе данных, позволяют определить причину дефекта.
Контроль и диагностика систем числового программного управления в основном проводятся с помощью контрольных тестов, которые служат для выявления ошибок программ и неисправностей в системе ЧПУ. Основу тестовой диагностики устройства с ЧПУ составляет набор программных модулей, каждый из которых обеспечивает контроль работоспособности и локализацию места неисправности определенного блока устройства ЧПУ.
Станки с ЧПУ содержат две разнородные взаимодействующие системы: электронную систему ЧПУ, механические рабочие органы и вспомогательные механизмы. Для последних характерны параметрические отказы, когда происходит постепенное ухудшение их параметров. В этом случае перед системами технического диагностирования ставятся не только задачи распознавания и установления вида и места дефекта, но и задача прогнозирования состояния узлов станка с возможным учетом ухудшения параметров в процессе дальнейшей работы. Сложность задач технического диагностирования станка заключается также и в необходимости их решения в эксплуатационных условиях при ограниченном объеме контролирующей аппаратуры.
Контроль и диагностирование режущего инструмента является важной задачей при работе станков с ЧПУ, учитывая относительно небольшую стойкость инструментов (40—60 мин), недопущение его критического износа и поломки.
Первой задачей является контроль возможной поломки осевого режущего инструмента для предотвращения получения бракованных деталей и возможной поломки узлов станка. Данный контроль основан на контактном ощупывании инструмента после обработки различными способами.
Второй важной задачей является контроль и диагностирование инструмента с целью своевременного определения его максимально допустимого износа, недопущения его поломки с последующей заменой его дублирующим инструментом, установленным в револьверной головке или в магазине. Система технического диагностирования может также выдавать сигнал оператору для замены износившегося инструмента вручную.
Применяются два способа диагностирования режущего инструмента:
При первом способе, зная время стойкости инструмента, его устанавливают на счетчике. По истечении этого времени инструмент заменяется.
Недостатком данного способа является то, что неизвестно точное время стойкости инструмента. Поэтому его могут заменить раньше времени (недоиспользуют его возможности) или, наоборот, слишком поздно, когда наступит его критический износ или вообще поломка.
При втором способе износ режущего инструмента и время его замены определяются косвенно через измерение крутящего момента или осевой силы на шпинделе станка. Аналогично может определяться осевая сила на ходовом винте.
На токарных станках с ЧПУ может определяться сила, действующая на резец и на револьверную головку, установленную на измерительной плите. Недостатком этих способов является косвенный способ определения износа инструмента.
В составе программного обеспечения АСУ «Мониторинг с глубокой диагностикой технического состояния узлов станков с ЧПУ» функционирует полноценная экспертная система автоматизированной поузловой диагностики формообразующих узлов станков, реализованная в виде дополнительного модуля. Данная система относится к системам смешанного типа и наряду с готовым набором адаптированных правил для диагностики отдельных узлов станков, содержит гибкий инструментарий формирования новых пользовательских правил. Для эффективной работы в условиях различной неполноты данных (отсутствия информации о режимах эксплуатации, конструктивных параметрах отдельных узлов, номерах подшипников и т.д.) в экспертной системе реализованы специальные программы и методики.
Программированная интеллектуальная АСУ «Мониторинг с глубокой диагностикой технического состояния узлов станков с ЧПУ» обеспечивает:
Программное обеспечение АСУ «Мониторинг» имеет весь необходимый функционал для построения общезаводской системы контроля технического состояния всего парка оборудования с ЧПУ, с целью повышения надежности его эксплуатации и организации эффективной стратегии ТОиР. Программный пакет АСУ «Мониторинг» позволил организовать единую интеллектуальную платформу для сбора, хранения, отображения и анализа всей необходимой информации в виде централизованной диагностической базы, а также обеспечить взаимодействие базы с внешними информационными системами. Успешное решение данной задачи позволило нам существенно повысить эффективность эксплуатации всего парка оборудования с ЧПУ и произвести оправданную оптимизацию расходов на его ТОиР.
В настоящее время Технический центр использует гибридную интеллектуальную АСУ «Мониторинг с глубокой диагностикой технического состояния узлов оборудования с ЧПУ», блок-схема которой представлена на нижерасположенном рисунке.
Метод по спектру огибающей вибросигнала
Известно, что высокочастотная шумовая часть вибросигнала меняет свою амплитуду во времени, то есть она модулируется более низкочастотным сигналом. Именно в этом моделирующем сигнале и содержится информация о состоянии подшипника. Выделение и обработка полученной информации в виде вибросигнала и составляют основу этого метода. При этом для получения более достоверных результатов необходимо анализировать модуляцию не широкополосного сигнала, получаемого от датчика вибрации, а с предварительно отфильтрованного вибросигнала в диапазоне от 4 до 20 кГц.
Для этого отфильтрованный сигнал выделяется в модулирующий, который и подается на узкополосный спектр анализатора, и мы получаем спектр огибающей.
Система диагностики станков с ЧПУ по параметрам точности изготавливаемой детали содержит:
- датчик угла поворота шпинделя;
- бесконтактный датчик перемещения, служащий для измерения перемещений вершины резца в плоскости, проходящей через вершину резца и ось шпинделя;
- компьютер.
Бесконтактный датчик перемещения установлен на резцедержательной головке суппорта или корпусе шпинделя. После записи показаний на компьютере предусмотрена обработка экспериментальных данных с использованием методов математической статистики. Построенный геометрический образ поверхности в трехмерном пространстве позволяет определить все необходимые показатели точности детали до ее окончательной обработки. Способ направлен на прогнозирование параметров точности и качества изготавливаемых деталей.
Близким к вышеописанному способу являются способ диагностики шпиндельного узла. Этот способ предусматривает приложение внешней нагрузки к оправке, установленной в шпинделе, и измерение расстояния от поверхности оправки до датчиков перемещения, расположенных в двух поперечных сечениях оправки на заданном расстоянии между сечениями. Оправку обрабатываем резцом, в качестве датчиков перемещения используем бесконтактные датчики, по сигналам которых определяются поперечные сечения оправки в местах установки датчиков перемещения. По поперечным сечениям определяем геометрический образ оправки в трехмерном пространстве. После обработки оправки резцом, для полученной геометрической точности детали мы оцениваем погрешность радиального размера, геометрической формы, суммарную погрешность:
- формы;
- относительного расположения поверхностей в радиальном и торцевом направлениях;
- отклонения от цилиндричности.
По результатам оценки геометрической точности полученной детали определяем параметрическую надежность шпиндельного узла.
Поставленная задача решается, а технический результат достигается тем, что в предлагаемом способе оперативной диагностики технического состояния формообразующих узлов металлообрабатывающих станков на основании информации, поступающей от датчиков, определяем геометрический образ поверхности обработанной детали, который представляем в виде частотного спектра, отражающего колебания инструмента и заготовки по нормали к обрабатываемой поверхности, вызванных наличием дефектов в узлах станка. Сравнивая текущий геометрический образ с эталонным, мы по отклонению его от эталонного определяем наличие и место дефектов.
Формирование эталонного геометрического образа осуществляется путем фиксации виброметрической информации в ходе обработки металлорежущими станками и применения накопленной информации для обучения нейросетевых моделей, представляющих собой апроксимацию нелинейных характеристик. В качестве архитектуры нейронной сети, реализующей эталонные модели, применяются рекуррентные нейронные сети с долгой краткосрочной памятью.
Поиск дефекта и причины отказа проводится в определенном диапазоне частот путем идентификации частоты возмущения с доминирующей частотой, вызывающей работу дефектного узла в данном частотном диапазоне. Вычисляется несоответствие между эталонной нейросетевой моделью и текущими характеристиками процесса, по величине и динамике изменения которого определяется характер дефекта посредством использования второй нейросетевой модели классификатора.
На основании требований к металлорежущему станку составляется обобщенный (эталонный) спектр, соответствующий допускаемым отклонениям формы (волнистости) и шероховатости поверхности детали при соблюдении конкретных условий обработки.
Расчетный спектр определяется с помощью моделирования колебаний инструмента и обрабатываемой детали с учетом технических условий на точность изготовления и сборки модулей металлообрабатывающего станка.
При использовании эталонного спектра в процессе диагностики технического состояния модулей станка по расчетному спектру выделяют характерные частоты, в которых проявляются погрешности изготовления модулей металлообрабатывающего станка.
При эксплуатации станка постоянно выполняется фиксация спектра в виде амплитудно-частотных характеристик. При возникновении новых видов дефектов, ранее неопределяемых, выполняется дообучение нейронной сети-классификатора по новым данным.
Как было показано, задачи технического диагностирования могут быть различными, поэтому различаются частота и моменты времени, когда получают данные различных измерений.
Диагностирование может проводиться непрерывно в процессе всего времени работы станка с ЧПУ и обработки заготовок, например контролируется температура в шкафу УЧПУ или температура масла в гидросистеме станка и др.
Ряд параметров, например система централизованного смазывания, контроль зажима каждой заготовки и точность изготовления каждого изделия и др., должны контролироваться периодически, но с большой частотой. Часть контрольных операций проводится с меньшей частотой, например один раз в смену или после каждой изготовленной партии деталей. Такие параметры станка, как точность, жесткость и др., должны контролироваться через длительные промежутки времени с очень малой частотой, поскольку эти параметры изменяются очень медленно и для их измерения требуются значительные затраты времени и средств. В отдельных случаях диагностирование может проводиться оператором в зависимости от конкретных требований и условий.
В настоящее время наиболее передовые фирмы — изготовители станков с ЧПУ предлагают новый вид сервиса, который получил название «телефонная диагностика». Ее принцип состоит в том, что диагностирование проводится на предприятии — изготовителе станка с ЧПУ. Естественно, что предприятие, эксплуатирующее станки с ЧПУ, может находиться в другом городе или даже в другой стране. Связь между этими предприятиями осуществляется по телефону. В случае возникновения у потребителя проблемы с диагностированием отказа станка он обращается к фирме-изготовителю и по телефону перекачивает информацию со своего компьютера в компьютер фирмы-изготовителя. Последняя имеет мощную диагностическую систему, которая не только обслуживает потребителей, но и в основном работает по совершенствованию выпускаемого оборудования, а также по доводке опытных образцов новых станков с ЧПУ. Фирма-изготовитель также имеет в своем распоряжении обширный пакет диагностических программ, базу данных и пакет расчетных моделей. Переданная по телефону информация в виде протокола измерений поступает в базу данных и служит исходной информацией для реализации расчетных моделей. Выполнение расчетов и анализ информации, имеющейся в базе данных, позволяют определить причину дефекта.
Контроль и диагностика систем числового программного управления в основном проводятся с помощью контрольных тестов, которые служат для выявления ошибок программ и неисправностей в системе ЧПУ. Основу тестовой диагностики устройства с ЧПУ составляет набор программных модулей, каждый из которых обеспечивает контроль работоспособности и локализацию места неисправности определенного блока устройства ЧПУ.
Станки с ЧПУ содержат две разнородные взаимодействующие системы: электронную систему ЧПУ, механические рабочие органы и вспомогательные механизмы. Для последних характерны параметрические отказы, когда происходит постепенное ухудшение их параметров. В этом случае перед системами технического диагностирования ставятся не только задачи распознавания и установления вида и места дефекта, но и задача прогнозирования состояния узлов станка с возможным учетом ухудшения параметров в процессе дальнейшей работы. Сложность задач технического диагностирования станка заключается также и в необходимости их решения в эксплуатационных условиях при ограниченном объеме контролирующей аппаратуры.
Контроль и диагностирование режущего инструмента является важной задачей при работе станков с ЧПУ, учитывая относительно небольшую стойкость инструментов (40—60 мин), недопущение его критического износа и поломки.
Первой задачей является контроль возможной поломки осевого режущего инструмента для предотвращения получения бракованных деталей и возможной поломки узлов станка. Данный контроль основан на контактном ощупывании инструмента после обработки различными способами.
Второй важной задачей является контроль и диагностирование инструмента с целью своевременного определения его максимально допустимого износа, недопущения его поломки с последующей заменой его дублирующим инструментом, установленным в револьверной головке или в магазине. Система технического диагностирования может также выдавать сигнал оператору для замены износившегося инструмента вручную.
Применяются два способа диагностирования режущего инструмента:
- пассивный, когда просто учитывается время работы инструмента специальным счетчиком;
- активный, когда постоянно измеряется крутящий момент или сила резания и по их значениям определяется степень износа режущего инструмента.
При первом способе, зная время стойкости инструмента, его устанавливают на счетчике. По истечении этого времени инструмент заменяется.
Недостатком данного способа является то, что неизвестно точное время стойкости инструмента. Поэтому его могут заменить раньше времени (недоиспользуют его возможности) или, наоборот, слишком поздно, когда наступит его критический износ или вообще поломка.
При втором способе износ режущего инструмента и время его замены определяются косвенно через измерение крутящего момента или осевой силы на шпинделе станка. Аналогично может определяться осевая сила на ходовом винте.
На токарных станках с ЧПУ может определяться сила, действующая на резец и на револьверную головку, установленную на измерительной плите. Недостатком этих способов является косвенный способ определения износа инструмента.
В составе программного обеспечения АСУ «Мониторинг с глубокой диагностикой технического состояния узлов станков с ЧПУ» функционирует полноценная экспертная система автоматизированной поузловой диагностики формообразующих узлов станков, реализованная в виде дополнительного модуля. Данная система относится к системам смешанного типа и наряду с готовым набором адаптированных правил для диагностики отдельных узлов станков, содержит гибкий инструментарий формирования новых пользовательских правил. Для эффективной работы в условиях различной неполноты данных (отсутствия информации о режимах эксплуатации, конструктивных параметрах отдельных узлов, номерах подшипников и т.д.) в экспертной системе реализованы специальные программы и методики.
Программированная интеллектуальная АСУ «Мониторинг с глубокой диагностикой технического состояния узлов станков с ЧПУ» обеспечивает:
- сбор, обработку и запись в единую базу данных результатов измерений, полученных с использованием различных аппаратных средств;
- импорт дополнительных сведений о режимах эксплуатации оборудования, сроках и объемах технических обслуживаний и ремонтных воздействий, включая балансировку и центровку;
- структурированное хранение результатов измерений в сетевой базе данных с возможностью удаленного многопользовательского доступа;
- гибкий инструментарий просмотра и расширенного анализа результатов измерений;
- автоматическое поузловое диагностирование оборудования с использованием встроенных и дополнительных экспертных правил;
- формирование различных видов протоколов и отчетных документо;
- автоматическое создание маршрутов для организации ежедневного мониторинга состояния оборудования;
- двухстороннюю связь с заводскими системами АСУ ТП;
- экспорт информации о состоянии оборудования во внешние информационные системы.
Программное обеспечение АСУ «Мониторинг» имеет весь необходимый функционал для построения общезаводской системы контроля технического состояния всего парка оборудования с ЧПУ, с целью повышения надежности его эксплуатации и организации эффективной стратегии ТОиР. Программный пакет АСУ «Мониторинг» позволил организовать единую интеллектуальную платформу для сбора, хранения, отображения и анализа всей необходимой информации в виде централизованной диагностической базы, а также обеспечить взаимодействие базы с внешними информационными системами. Успешное решение данной задачи позволило нам существенно повысить эффективность эксплуатации всего парка оборудования с ЧПУ и произвести оправданную оптимизацию расходов на его ТОиР.
В настоящее время Технический центр использует гибридную интеллектуальную АСУ «Мониторинг с глубокой диагностикой технического состояния узлов оборудования с ЧПУ», блок-схема которой представлена на нижерасположенном рисунке.
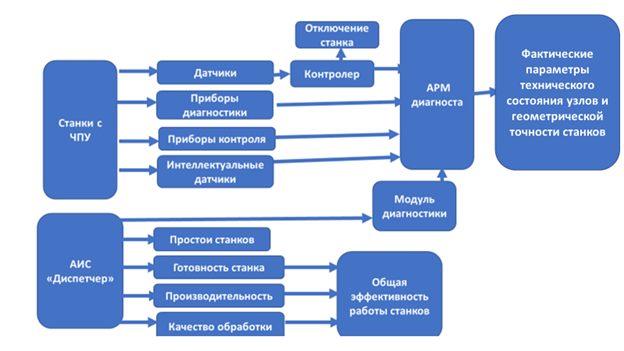
Интеллектуальная гибридная АСУ «Мониторинг с глубокой диагностикой технического состояния узлов оборудования с ЧПУ и диспетчеризации», формируется из нескольких уровней:
В своей практике по характеру управления и контроля мы использовали два типа АСУ:
На этом я заканчиваю данную статью.
При написании данной статьи я использовал следующие материалы:
1. Материалы, опубликованные в открытой печати в интернете.
2. Материалы собственных опубликованных статей.
3. Материалы собственных докладов на научно-технических конференциях.
4. Способ диагностики шпиндельного узла (патент RU2124966 МПК G01M 99/00, опубл. 20.01.99
- нижний уровень – это приборы, которые необходимы для измерения, снятия данных непосредственно с узлов станка (датчики температуры, тока, влажности, давления, контрольно-измерительные инструменты и приборы);
- средний уровень – это модули ввода, модемы, контроллеры, средства передачи данных;
- высокий уровень – это программное обеспечение, программируемые контроллеры, АРМы ремонтника и диагноста.
В своей практике по характеру управления и контроля мы использовали два типа АСУ:
- локальную, которая представляет из себя совокупность оборудования, которое используется для местного управления, защиты, контроля, мониторинга, сбора и передачи технологических данных оборудования. Эти системы автономны и могут работать по заданному циклу без контакта с системами высокого уровня. Данные передаются с технической системы прямиком на пульт оператора станка и АРМы ремонтника и диагноста;
- удаленную, которая представляет из себя комплекс программных и аппаратных средств, предназначенных для централизованного контроля за техническим состоянием узлов оборудования и технологическими процессами и эффективностью работы оборудования. Данная система помогает руководству Технического центра и производства контролировать состояние оборудования, которое расположено на удалении от центра диагностики, ремонтной базы и диспетчерских пунктов цехов и производства, в котором ведется онлайн-мониторинг, контроль процессов и технического состояния оборудования. Происходит передача данных с удаленного оборудования на центральную станцию диспетчеризации с помощью каналов передачи данных.
На этом я заканчиваю данную статью.
При написании данной статьи я использовал следующие материалы:
1. Материалы, опубликованные в открытой печати в интернете.
2. Материалы собственных опубликованных статей.
3. Материалы собственных докладов на научно-технических конференциях.
4. Способ диагностики шпиндельного узла (патент RU2124966 МПК G01M 99/00, опубл. 20.01.99