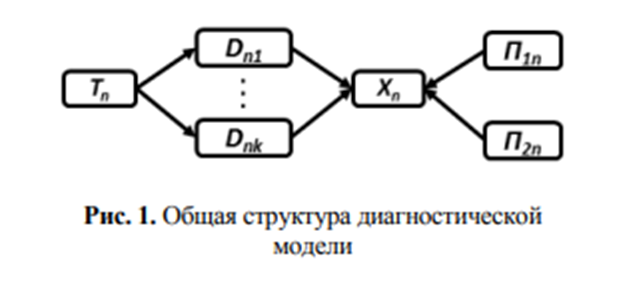
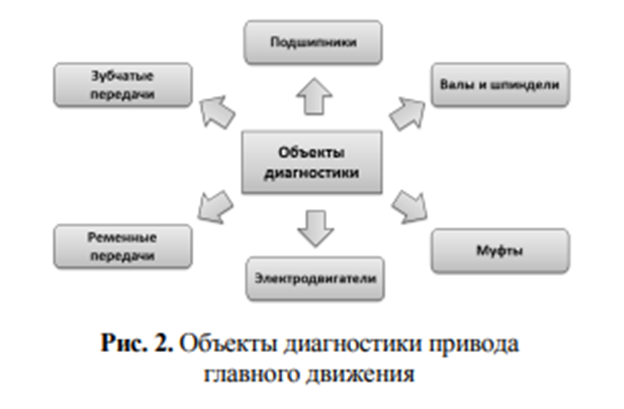
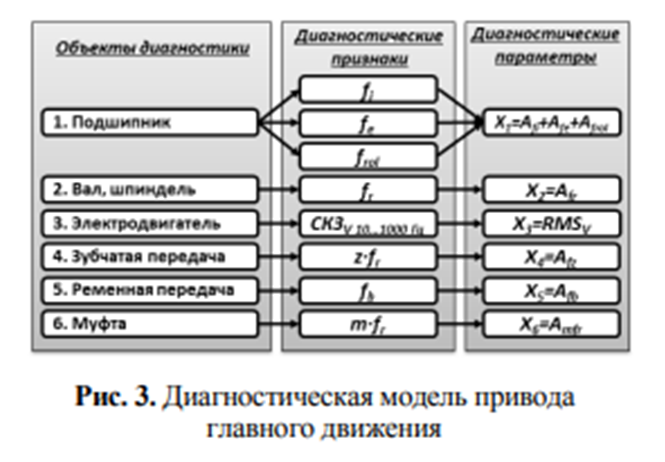
При невозможности выбора одного диагностического признака для объекта диагностики, однозначно определяющего его техническое состояние (например, для подшипников качения), измеряемый диагностический параметр должен представлять собой суммарную величину – сумму, среднее значение или среднее квадратичное значение. В общем случае, при построении системы мониторинга на базе метода виброакустической диагностики, диагностические признаки представляют собой определенные частоты в спектре вибросигнала, а диагностические параметры представляют собой численное значение, полученное путем математических операций со значениями амплитуд в спектре вибросигнала. Рис. 3. Диагностическая модель привода главного движения. При построении САМ на базе метода виброакустической диагностики необходимо организовать вычисление как прямого спектра вибросигнала, так и спектра огибающей вибросигнала. Дальнейшая математическая обработка строится на работе с амплитудами спектров вибросигнала. Диагностический параметр для выявления дефектов подшипников качения (X1) целесообразно представлять как сумму величины амплитуд на основных дефектных частотах в спектре огибающей вибросигнала (рис. 4а). В качестве основных дефектных частот подшипников качения выбраны частота перекатывания по внутреннему кольцу fi , частота перекатывания по наружному кольцу fe и частота вращения тел качения frol , определяемые соответственно по следующим общеизвестным формулам: Известия Самарского научного центра Российской академии наук, том 17, №2(4), 2015, где fr – частота вращения внутреннего кольца подшипника, Гц, z – количество тел качения подшипника в ряду, DW – диаметр тел качения подшипника, мм, Dср – средний диаметр подшипника, мм, α – угол контакта.
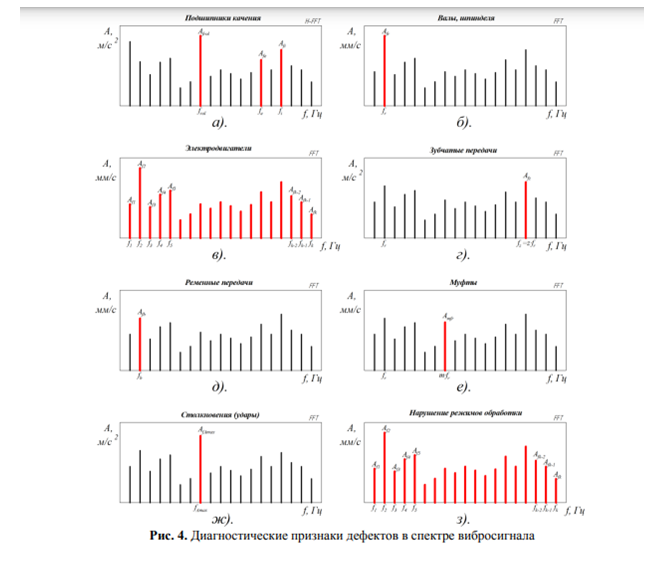
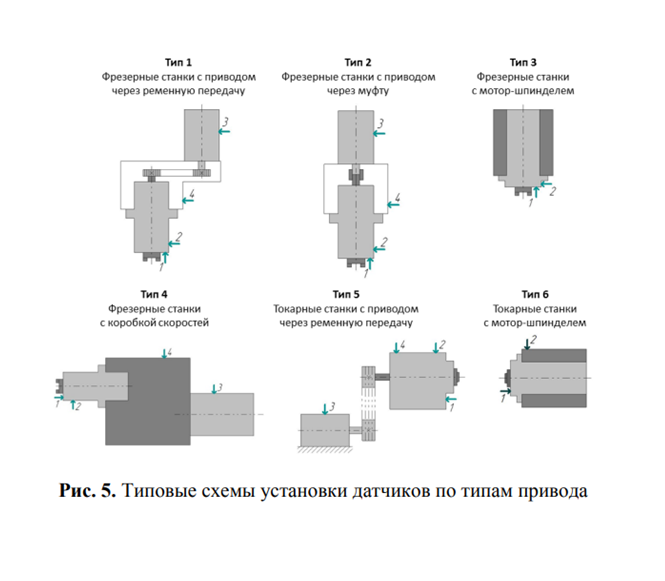
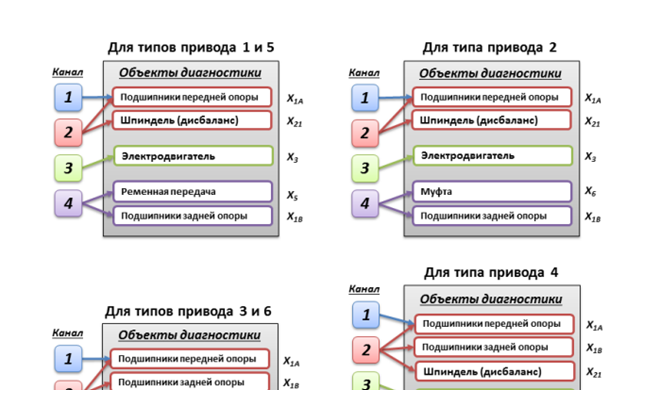
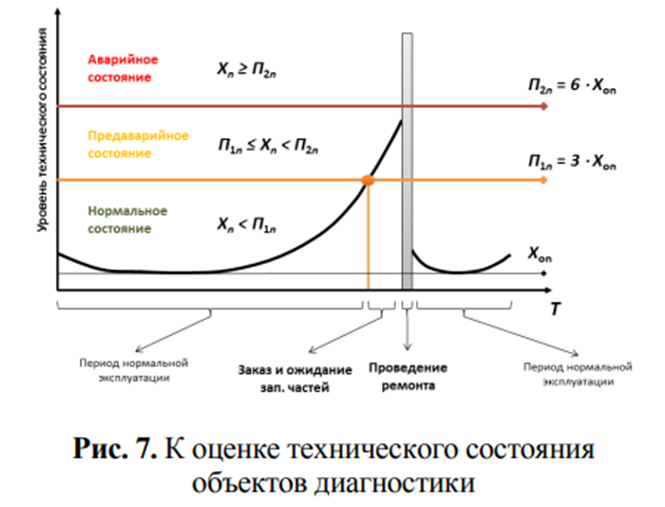
Допустимые значения определяются относительно базового значения диагностического параметра Xоn, характеризующего нормальное состояние объекта диагностики в период его начальной эксплуатации. Базовое значение диагностического параметра определяется по формуле: k XXX X k X nn n k k i o n n i 2 2 2 2 1 1 2 1 ...+++ = å = = , где Xn1, Xn2, … , Xnk – измеренные значения диагностического параметра, k – количество измерений. Изначально рекомендуется устанавливать значение допустимого уровня «Предупреждение» в 3 раза больше базового значения диагностического параметра (П1n = 3×Xоn), а значение допустимого уровня «Авария» в 6 раз больше базового значения диагностического параметра (П2n = 6×Xоn). Однако в процессе эксплуатации стационарной системы диагностики значения допустимых уровней «Предупреждение» и «Авария» необходимо корректировать с учетом мониторинга фактического состояния объектов диагностики. Рис. 7. К оценке технического состояния объектов диагностики Работа САМ технического состояния ПГД металлообрабатывающих станков с ЧПУ иллюстрируется блок-схемой, представленной на рис. 8. При каждом включении станка в блоке 1 автоматически происходит включение заданной ступени переключаемой коробки скоростей при ее наличии. Далее в блоке 2 происходит включение заданного числа оборотов электродвигателя главного движения. В блоке 3 с выхода контроллера УЧПУ на вход регистратора подается сигнал (24 В) на начало измерений заданных диагностических параметров конструкционных объектов диагностики при холостом ходе станка. В VII Всероссийская конференция «Актуальные проблемы машиностроения», 25-27.03.2015 729 процессе проведения измерений в блоке 4 в УЧПУ производится отсчет заданного времени измерения. По окончании времени измерений в блоке 5 сигнал (24 В) с выхода контроллера УЧПУ снимается. Далее, если в приводе присутствуют другие ступени коробки скоростей, то происходит включение следующей ступени и действия 1-5 повторяются. Процессы, происходящие в блоках 1-5, полностью автоматизированы средствами УЧПУ и прописываются в программе электроавтоматики станка при установке системы мониторинга. После окончания измерений диагностических параметров X1 … X6 объектов диагностики, полученные значения записываются во внутреннюю циклическую память регистратора и могут удаленно передаваться по сети для дальнейшего анализа. Кроме этого, происходит сравнение измеренных значений диагностических параметров с допустимыми значениями и при их превышении на панели оператора СЧПУ выводится предупреждающее сообщение о нарушении технического состояния того или иного объекта диагностики. Рис. 8. Блок-схема работы системы мониторинга технического состояния ПГД Параллельно, после окончания измерений диагностических параметров X1 … X6, в блоке 6 начинается мониторинг столкновений подвижных узлов станка и нарушений режимов обработки заготовки. Процесс измерения в блоке 6 осуществляется автоматически при отсутствии сигнала (24 В) на входе регистратора. Измеряемые в блоке 6 значения диагностических параметров, характеризующих столкновения подвижных узлов станка и нарушения режимов обработки, сравниваются с допустимыми значениями постоянно в режиме реального времени, а записываются во внутреннюю память регистратора, как через заданные равные промежутки времени, так и при превышении допустимых значений. При превышении значений диагностических параметров допустимого уровня «Предупреждение» на панели оператора СЧПУ выводится предупреждающее сообщение о нарушении режимов обработки заготовки, а при превышении допустимого уровня «Авария» происходит аварийное отключение станка. В настоящее время в на предприятии внедрены САМ технического состояния ПГД на особо ответственном оборудовании с ЧПУ (около 120 единиц). Комплекс мероприятий по внедрению САМ включает в себя: монтаж аппаратной части системы; настройку программного обеспечения для сбора, обработки и удаленной передачи измеряемых значений диагностических параметров для объектов диагностики; разработку и настройку системы визуализации технического состояния объектов диагностики не базе SCADA-системы. Данная САМ технического состояния ПГД интегрирована в автоматизированную систему управления техническим обслуживанием и ремонтом (АСУ ТОиР) оборудования с ЧПУ для автоматизации планирования ремонтов по фактическому состоянию с прогнозированием остаточного ресурса и оценкой риска выхода из строя. В ходе внедрения САМ на предприятии на данный момент решены следующие задачи: - проведен анализ значений параметров вибрации объектов диагностики, представленных на рис. 2, на более чем 100 единицах оборудования с ЧПУ в течение трех лет и выявлено влияние уровней вибрации на фактическое техническое состояние ПГД; - предварительно определены допустимые уровни диагностических параметров, которые могут корректироваться в процессе эксплуатации системы автоматизированного мониторинга; - разработаны методика измерений диагностических параметров включая унифицированные схемы установки датчиков; - разработано программное обеспечение, отображающее техническое состояние объектов диагностики в виде трендов изменения значений диагностических параметров во времени в сравнении с допустимыми уровнями как для конкретной единицы оборудования с ЧПУ, так и для группы станков одной модели (рис. 9). Тренды изменений значений диагностического параметра, характеризующего техническое состояние подшипников передней опоры шпинделя для группы станков одной модели Выводы: внедрение САМ технического состояния ПГД оборудования с ЧПУ позволяет: получать оперативную информацию в режиме реального времени как о техническом состоянии механических узлов ПГД станка, так и о состоянии технологического процесса обработки заготовок; снижать последствия столкновений подвижных узлов станка путем его оперативного отключения при авариях; предотвращать износовые отказы механических узлов особо ответственного и дорогостоящего оборудования с ЧПУ за счет своевременного планирования работ по техническому обслуживанию и ремонту; осуществлять прогнозирование остаточного ресурса механических узлов ПГД станка; производить оценку рисков выхода из строя узлов станка.
Автор статьи: Владимир Иванович Писарев